Supporting the lifecycle of energy infrastructures with Smart O&M
This article was previously published in the March 2020 issue of APUEA magazine.
In the era of industry 4.0, most energy projects in Asia still enter commercial operation without a maintenance system in place. Instead, the operation and maintenance (O&M) team, already busy with start-up issues, struggles to gather technical documentation, to define paper-based procedures and when time allows, years later, to implement computerized system.
For maintenance, the earlier the better
Experience shows that the earlier maintenance is taken into account, the better results in terms of lifecycle cost. Maintenance should be specifically addressed from the design stage and throughout construction, until the plant is finally handed over to the O&M team. In practice, however, maintenance preparation tends to be overlooked. Construction projects are full of challenges, EPC companies and equipment suppliers lack an overall lifecycle perspective and owner’s construction teams naturally focus on the problems at hand.
The implementation of the supporting IT system (commonly known as Computerized Maintenance Management Systems or CMMS, often referred to as Enterprise Asset Management or EAM in IT parlance) usually come as an afterthought, in spite of its proven value as a tool to handover technical documentation and to structure the maintenance organization. As a result, most plants start up and, sometimes run for years without a structured and modern maintenance system in place. Plants are instead relying on paper forms and Excel sheets where historical records are hard to find and systematic analysis is impossible.
This depressing state of affairs persists in the age of Industry 4.0 and Smart Plants.
A more in-depth look into “EAM” projects
When the IT system is finally online a few years later, its usage seldom meets expectations. Paper and Excel processes usually remain with the new system adding another layer of mandatory administration. Technology vendors are prompt to blame clients for their lack of maturity: the software was good, but the team is not ready for it! The objective for the project (the need to improve) becomes the excuse for its failure.
Siveco’s in-depth audits of Asia utilities having implemented CMMS/EAM solutions, consistently show that the areas most essential for maintenance improvement (as per the ISO 55000 Asset Management standard) are gravely lacking. Instead, projects cover administrative needs of little value for industrial improvement, such as time and cost tracking and approval workflows, as illustrated in the radar chart below. This is understandable, as virtually all EAM projects are driven by IT departments and IT vendors with limited understanding of maintenance.
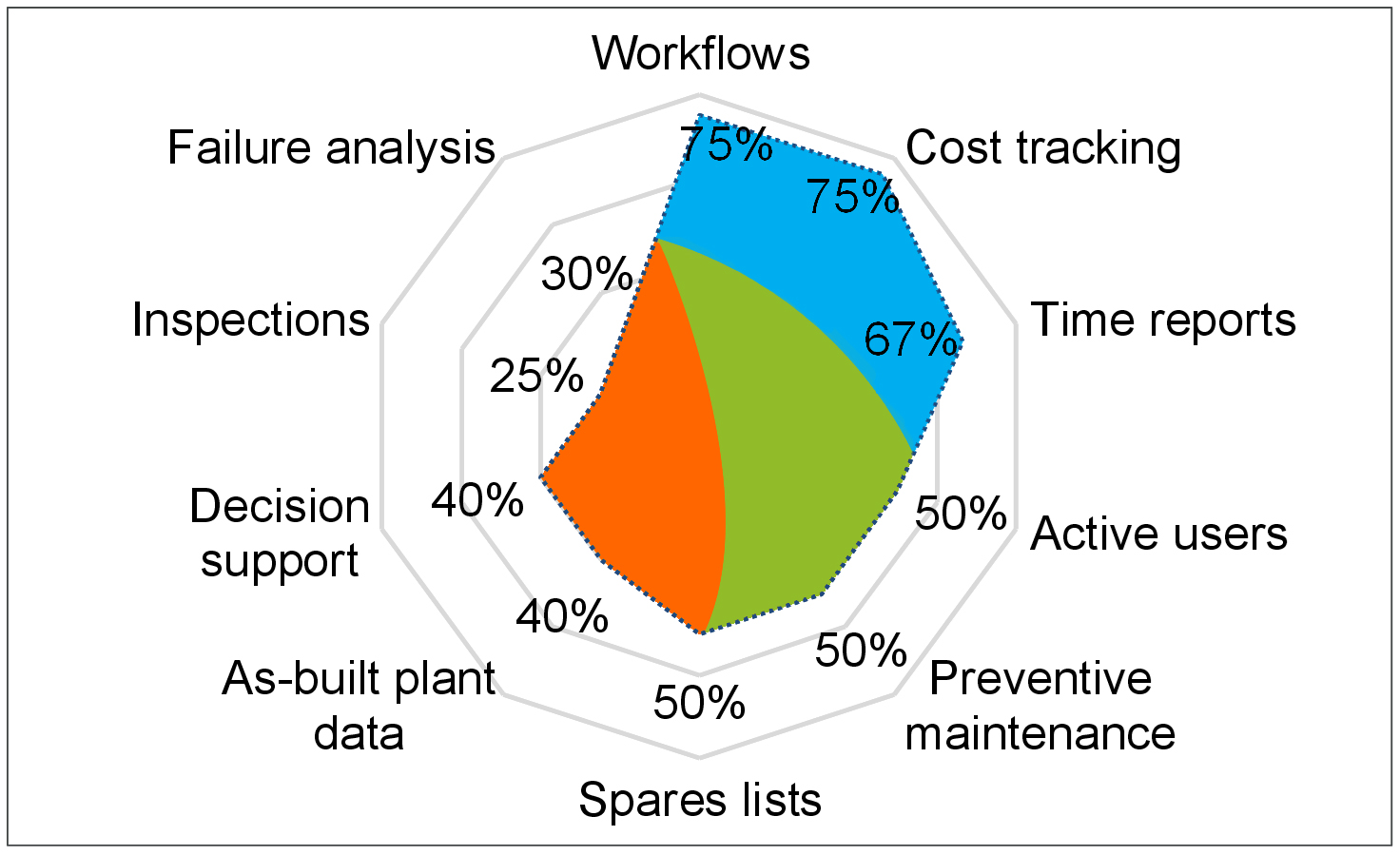
Typical coverage of “EAM” systems (achieved vs. objective in %)
The example of failure analysis provides a good illustration: it is essential for optimizing maintenance (for example through RCM) to collect failure information in a structured manner for systematic analysis. Studies show that 88% of the failures reported in EAM systems do not include a failure code (either no code at all or a generic code such as “miscellaneous”), thus rendering the entire system almost useless.
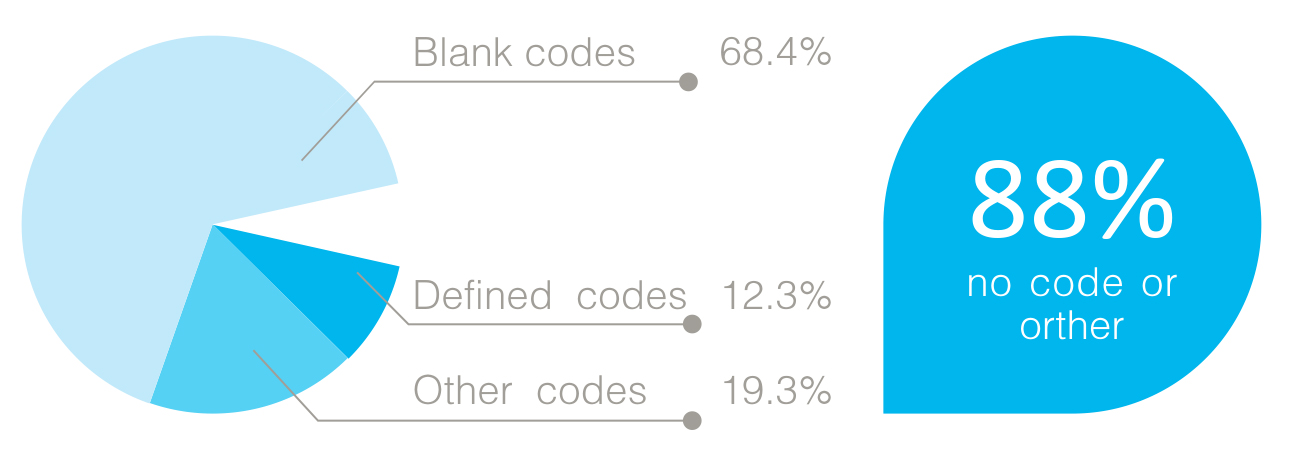
Study of Maximo data over a 3-year period
Finally, most EAM solutions still rely on printed papers, manual inputs by a junior technician or system clerk, just like in the 1980.
Learning from experience
Based on a long experience all over the world and lessons learnt during the rapid, and massive Chinese infrastructure built-up of the past 20 years, Siveco has developed innovative Smart O&M solutions (a term coined to differentiate from the traditional CMMS/EAM) integrating modern technologies such as mobility, 3D Building Information Models (BIM) and Connected Objects for the benefits of O&M teams. The company has also devised practical guidelines for the design, implementation and long-term stewardship of Smart O&M projects.
•
First of all, Smart O&M requirements must be incorporated in construction budgets, and ideally be included in the EPC tender, in order to pass the data preparation responsibility to the construction team, ensuring smooth transfer of technical documentation from construction to operation and enforcing good maintenance practice from day one. This early-stage approach also allows a smooth integration with control systems (DCS/SCADA).
The figure below summarizes the Siveco approach for maintenance preparation during a construction project based on the utilization of the Smart O&M.
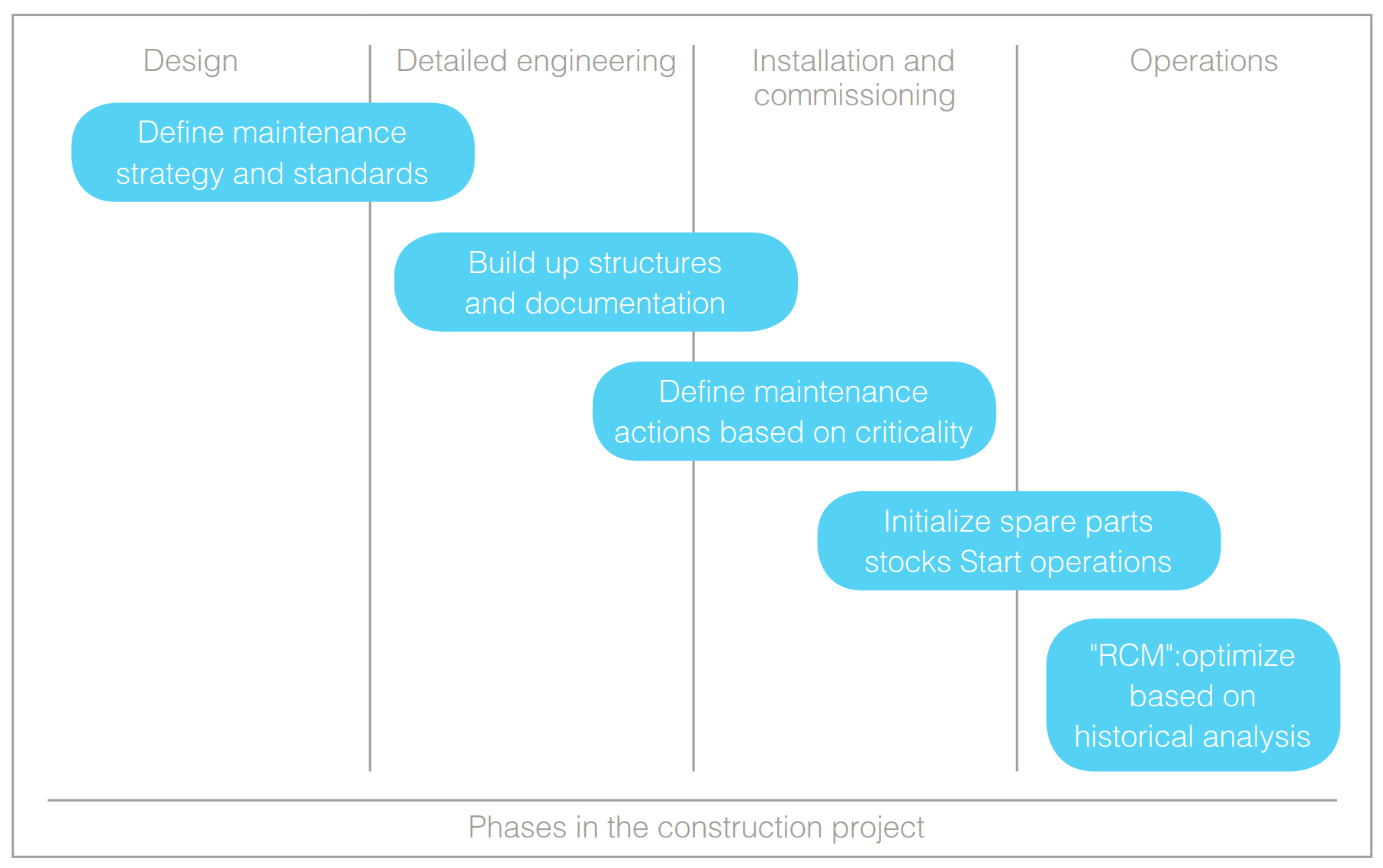
•
For the design of the Smart O&M system itself, focus on the gaps observed in traditional IT/EAM projects using the ISO 55000 Asset Management standard as a frame of reference. Use ISO 55000 to drive the project and avoid the complexification or confusion often seen with IT or administrative projects.
•
Finally, focus on people, technicians, and decision makers, rather than processes or technology. This is easily achieved by using modern user interfaces, such as mobile solutions (eliminating the need for paper and tedious manual inputs) and large touchscreens (making otherwise hidden O&M information highly visible and tangible to decision makers). This cannot be improvised and must be supported by the chosen software.
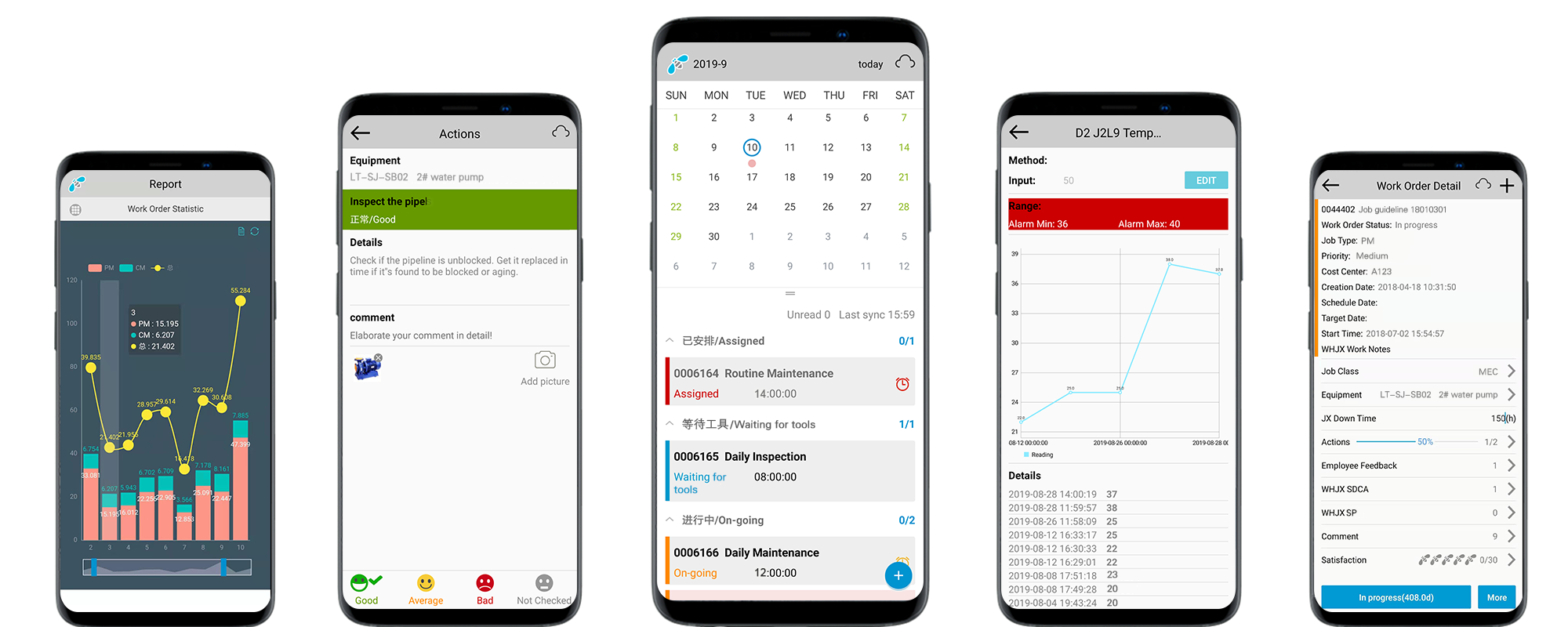
bluebee® is Siveco’s mobile solution “for the worker of tomorrow”
Recent energy projects have benefited from Siveco’s Smart O&M approach in Asia:
Chonburi Clean Energy (Thailand)
Chonburi Clean Energy (CCE), a joint venture of Suez, Glow Energy and WHA Utilities and Power, is the first industrial waste-to-energy facility in Southeast Asia to meet European emission standards. The plant is getting attention in the Thai utility market as a showcase for maintenance preparation during the construction phase, with its Smart O&M system ready before start-up. CCE is the first company to use the bluebee® mobile app in Thai.
Raffles City Chongqing District Cooling Plant (China)
A subsidiary of SP Group, Shirui Energy designed, built, owns and now operates the advanced energy-efficient cooling system of Raffles City Chongqing, an iconic real estate project. Siveco provides cloud-based lifecycle support for the facilities. Technicians used bluebee® mobile for commissioning and for day-to-day maintenance management since start-up.
Hanas New Energy (China)
Hanas New Energy owns and operates the largest LNG plant in China. Siveco has supported the plant with its maintenance needs from the construction stage, working alongside the EPC and contractors. The Smart O&M solution provides support for continuous performance improvement in spite of the LNG plant’s high staff turnover.
Ranhill Powertron II (Malaysia)
The 190 MW combined-cycle power plant was built by China National Electric Engineering Company (CNEEC). Siveco led a collaborative project to ensure maintenance readiness. According to the client, Siveco’s role was “critical, considering the very different working practices between Chinese construction firms and overseas power plant operators like us”.
Algerian Mega-Project (Algeria)
The Algerian government has launched a massive investment program, with around 12 GW of capacity (combined cycle gas turbine power plants) added to the grid between 2015 and 2020. For all projects, Siveco China has delivered the maintenance system, including data preparation services, in cooperation with Turkish and Korean EPC companies, before the plants start-up.
Yingde Gases (China)
Asia’s largest industrial gas producer, Yingde Gases selected Siveco to implement an ISO 55000-compliant Maintenance and Reliability management system unified across 100+ plants of heterogeneous background (older assets, recent acquisitions, modern plants, etc.). All O&M staff carry out their daily work with the mobile app and touchscreens, at plant and group level, make performance improvement visible to all stakeholders.
Other Siveco infrastructure clients in the region include Brunei’s Department of Electrical Services, Beijing Environment, Bukit Asam, Capital Water, CNOOC, COSCO Terminals, Fushun Mining, Engie, Everbright, Hyundai E&C, Samsung C&T, Shell, Suez NWS, etc. Siveco also works with multisite manufacturers such as Arkema, Baosteel, Essilor, Daramic, International Paper, Imerys, Mane, etc. that operate plants across Southeast Asia.
Conclusion
The early-stage Smart O&M approach devised by Siveco to ensure maintenance readiness has a proven track record of over 850 projects in Asia. Ideally funded by construction Capex, the project generates direct savings as early as the O&M handover process (reduced labor, avoided delays and data losses). The solution supports commissioning activities, makes accurate plant documentation accessible by O&M teams and ensures maintenance readiness from day one. Last but not least, the Smart O&M successfully closes the “ISO 55000 feedback loop” between plant technicians and top managers, thanks to the innovative use of mobility and decision-support tools running on large touchscreens.