Daramic Thailand towards World Class Maintenance
Daramic Thailand’s Prachinburi plant
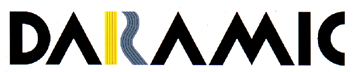
For over 85 years, Daramic has led the way in developing new and innovative technology for the lead acid battery market. With headquarters in Charlotte, North Carolina, USA, Daramic today supplies nearly 50% of the world’s demand for high performance polyethylene battery separators to the lead acid battery industry. Daramic Thailand operates the largest and most advanced polyethylene separator manufacturing plant in Asia, located in Prachinburi. The plant opened in 2000 (first production line), with machinery transferred from older plants, and additional lines were added over the years.
In order to meet the company’s business objective, Daramic Thailand initiated a World Class Maintenance project during 2015. The company had been facing challenges with aging equipment, very high workload in the maintenance department and shutdowns leading to costly production losses. Traditional maintenance tools and previous IT-driven initiatives had proven powerless. The company initially hired Siveco to conduct a maintenance assessment and help define a robust improvement plan.
The maintenance assessment
In November 2015, two Siveco experts conducted a week-long maintenance assessment onsite in Prachinburi. The assessment confirmed Daramic Thailand’s improvement potential and defined a multiphase program based on the ISO 55000 Asset Management standard, with support from a cloud-based CMMS and maintenance coaching services. Aimed at achieving significant financial gains with a 97% uptime target by 2018, the project was launched in March 2016, after approval of the company’s top management in the US.
Coswin 8i in the Cloud
Daramic Thailand chose the flexibility of Coswin 8i in the Cloud: the system is leased on a yearly subscription basis and hosted by Siveco. Siveco guarantees internet connectivity, availability, regular backup and maintenance. No investment was needed in hardware or other IT resources. All the functionalities of Coswin 8i required to support the improvement project were used, with a focus on building the asset database, organizing preventive and corrective maintenance, inventory management include repairable items and KPIs & Reports to close the improvement loop. However, Siveco did not just provide the CMMS, but rather a total solution to meet Daramic’s improvement needs. All services were provided by Siveco Shanghai’s international team of maintenance and CMMS experts.
Rebuilding the asset database
The first step of the project was to establish a structured equipment database with a consistent coding system. This had proven to be an insurmountable obstacle in the company’s previous CMMS initiatives. Siveco made clear recommendations to prioritize data preparation tasks: thanks to Maintenance team’s extra work hours, and with the help of Coswin’s flexible data migration tool, the database was ready and Coswin 8i went “Live” well within 3 months, a first major key success factor for the project.
Reversing the PM/CM ratio
A key project goal, in order to achieve the plant uptime goal, was to increase the Preventive Maintenance (PM) to Corrective Maintenance (CM) ratio. PM guidelines were defined, as part of the continuing data preparation. Coswin 8i automatically generates Preventive Maintenance plans for the upcoming month effort and their execution carefully managed in the system. As a result, the amount of PM work orders has been drastically increased within 6 months, from a few hundred per year to around 4,500. One year after “Go Live”, the improved PM/CM ratio resulted in a significant increase in plant uptime.
Backlog management
Unbalanced workload was the key problem faced with Daramic’s plant management team. Prior to the maintenance improvement project, tasks were assigned daily during the morning meeting. The huge amount of corrective maintenance work made planning very difficult, not to mention optimization. Once the PM/CM ratio was put under control, more detailed work management in Coswin 8i became possible. One type of work that more particularly benefited from the usage of Coswin is Preventive Maintenance Shutdown planning: shutdown activities are now available and easy to export to Excel for detailed planning with the various parties involved (technical teams, suppliers).
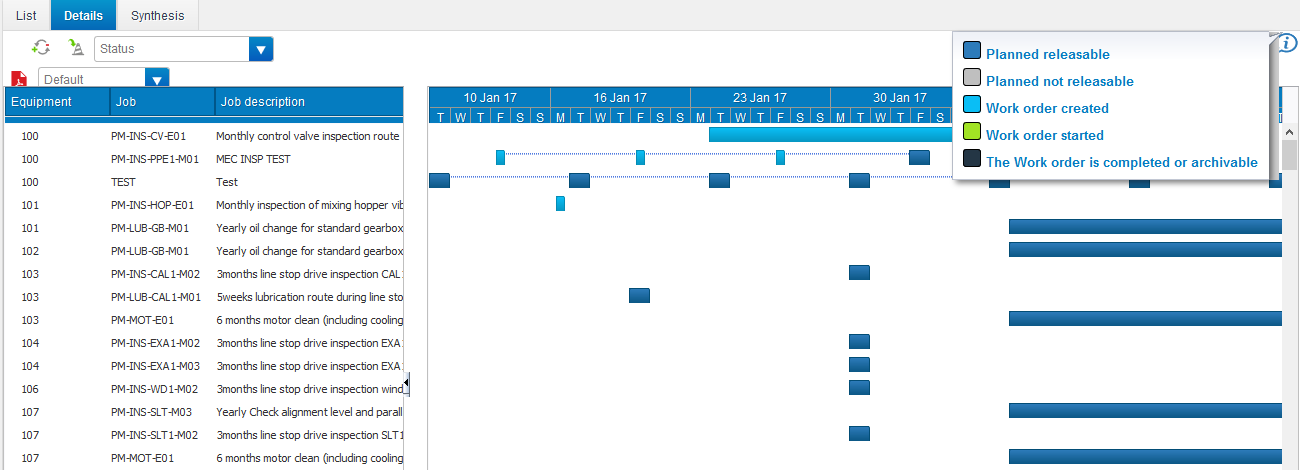
Consumables and repairable items management
Initially not in the Coswin project scope, stock was to be managed in Daramic’s corporate ERP system. However, as new needs appeared, Siveco was able to flexibly integrate it into the project. Today, consumables, repairable items and direct purchases not managed by the ERP software, are managed in Coswin 8i instead. Repairable items move between stock, production lines, the repair workshop or may even be sent to suppliers for repair: they are now managed in Coswin, with serial numbers allowing individual tracking.
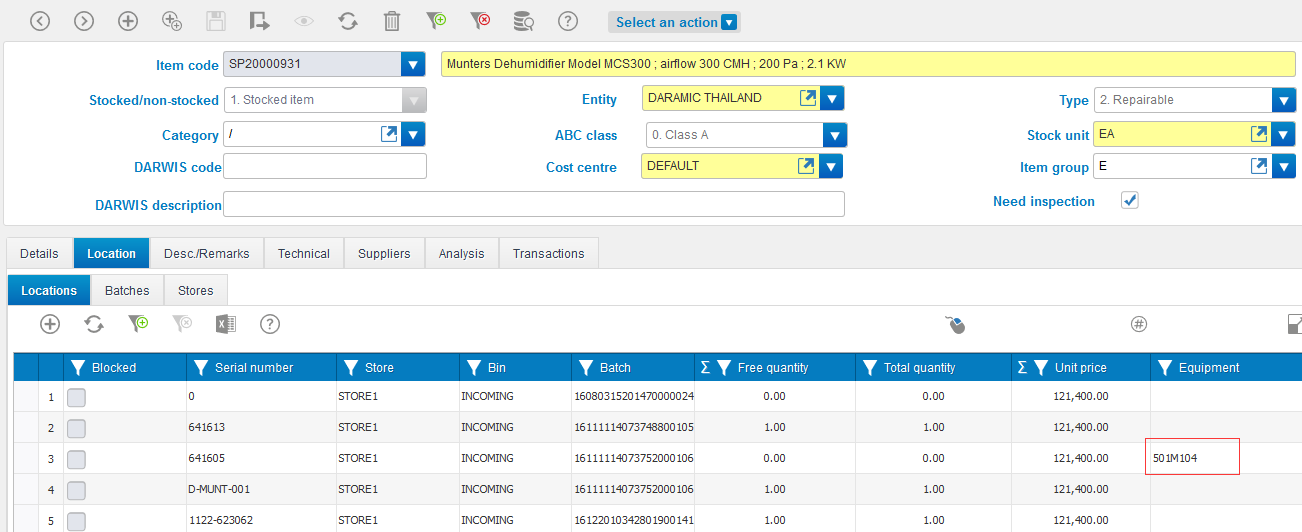
KPIs and reports
Siveco has implemented KPIs and reports for Daramic (primarily based on the EN 15341 Maintenance, Maintenance Key Performance Indicators standard), so that the management team can monitor work-in-progress, summarize equipment problems and systematically improve plant reliability. For the first time in the plant history, a clear link is established between breakdown events (recorded by production team in the ERP) and maintenance work orders (recorded by Maintenance team in Coswin), with all technical explanations, including symptom, defect cause, actions.
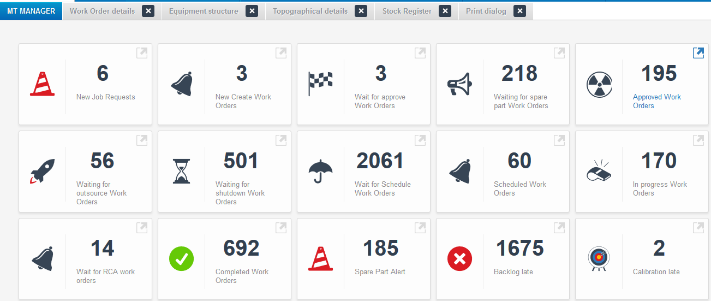
Thai language support
Daramic Thailand users primarily operate Coswin 8i in English but the in-built translation tool was used to create Thai-language screens when required for end-users, such as for Job Requests or Work Orders.
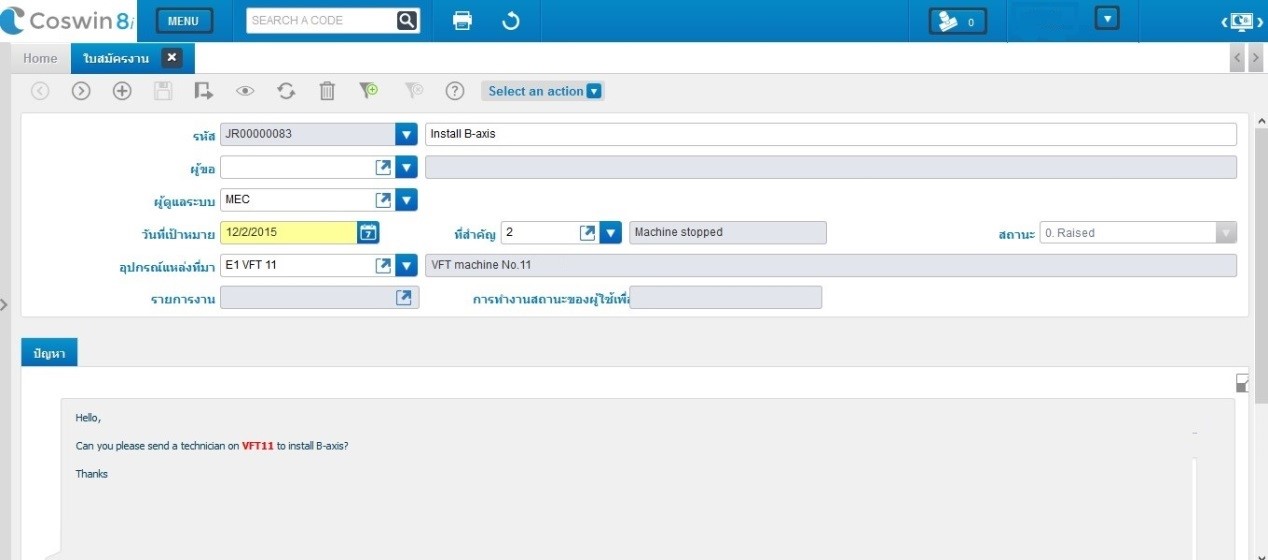
Benefits obtained
Coswin 8i was operational in the plant in May 2016, meaning that the new maintenance processes were defined, team members trained and the CMMS itself fully in place. Throughout the project, Daramic Thailand’s plant manager, technical manager and maintenance manager provided strong leadership, involving in key meetings and decisions, shaping the CMMS to meet the corporate goals. Over the following months, the maintenance team went through multiple improvement loops, showing good spirit and tenacity in spite of the many technical challenges keeping the plant up-and-running.
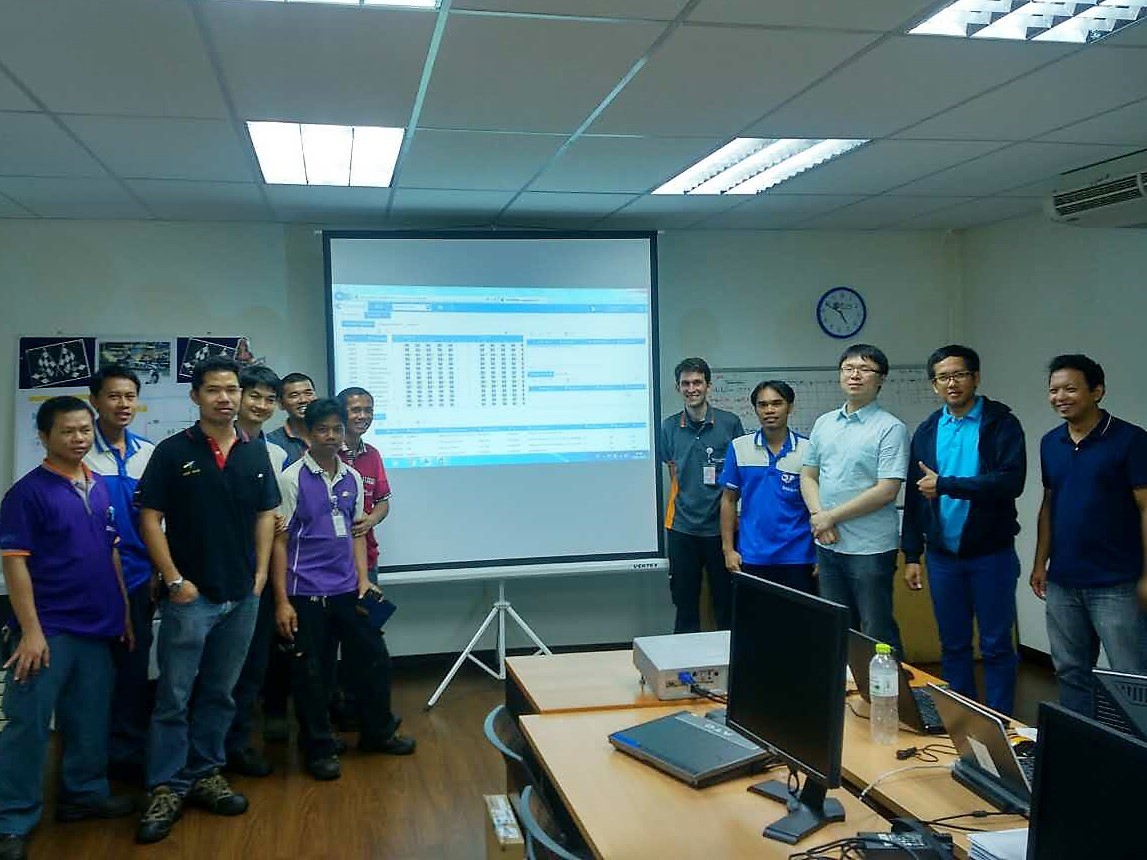
According to Plant Manager JB Lestrade:
“One year later, Daramic Thailand has achieved its first year performance objectives (plant availability). Team overtime has been reduced. For the first time, our work order backlog is under control and we have a much better visibility for further, continuous, improvement.”
According to Maintenance Manager Weerachai Hudakorn:
“The Siveco team perfectly mastered our project, providing technical and strategic advices all along. I also want to thank the Siveco hotline for their great support and reactivity, giving us explanations and advices whenever needed after Go Live.”