A collaborative approach to asset lifecycle management in gas turbine power plant project
The Ranhill Powertron II (RPII) 190MW Power Plant
Ranhill Berhad (www.ranhill.com.my) is one of Malaysia’s leading engineering and construction company, with asset management and ownership in the environment, infrastructure, power, petroleum and chemical sectors. With more than five decades in the industry, Ranhill has a strong presence in Malaysia and growing overseas operations in China, India, Libya, Saudi Arabia, Sudan and Thailand.
In mid-2009, Ranhill started the construction of a new 190 MW combined-cycle gas turbine power plant (CCGT) in the state of Sabah in East Malaysia, known as Rugading Power Plant in addition to the existing 190 MW Teluk Salut CCGT power plant which is located next to it. The Rugading power plant was built by the Chinese EPC. China National Electric Engineering Company (CNEEC) at a total project cost of 1.74 billion RMB and commissioned in less than 22 months. It comprises two gas turbines of Frame 6FA (Model PG6111+e) units each with a nominal capacity of 65 MW. The first gas turbine unit achieved COD in March 2010 and the second unit COD was on July 2010. The overall Combined Cycle Plant Facility was on Commercial Operations in April 2011, making Ranhill the largest Independent Power Producer in the State of Sabah.
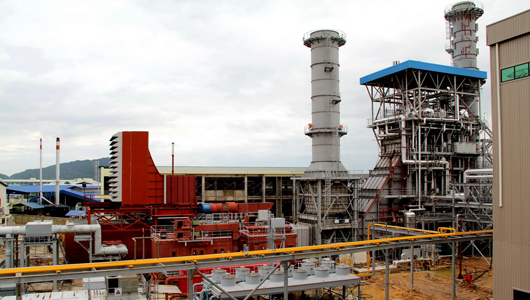
For more information on RPII:
http://www.ranhill.com.my/project-highlights/power/94-ranhill-powertron-ii-190mw-power-plant-sabah
http://www.ranhill.com.my/project-highlights/power/94-ranhill-powertron-ii-190mw-power-plant-sabah
The CMMS implementation: a collaborative project led by Siveco
In 2009, CNEEC selected the partnership of ABB Bailey Beijing Engineering Company and Siveco China to supply DCS and CMMS for the power plant. Based on a long experience of greenfield infrastructure projects all over the world, the Siveco China team had developed a specific expertise to assist EPC companies and their equipment suppliers during the construction phase, ensuring smooth transfer of technical documentation to operation, supporting plant commissioning and start-up with an accurate technical database and enforcing good maintenance practice from day one.
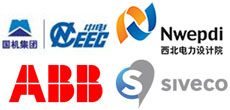
Siveco launched the data collection phase in Beijing on December 2009, working alongside CNEEC, the Northwest Electric Power Design Institute (NWEPDI), equipment suppliers like GE for the turbines and ABB (DCS) to define the data structure, coding rules, based on international standards: IEC61346, IEC PAS 62400 and ISO/TS 16952-10 RDS-PP (the “new KKS”). Data collection priorities were then defined.
In the beginning of 2010, Siveco China engineers set up and configured the CMMS “Coswin” at Siveco Shanghai office. Available data were uploaded into the CMMS by batch using the Clic-Clac tool, ensuring consistency and quality control. The system was shipped to customer site in Sabah, Malaysia towards the end of the year, for final data migration and system acceptance tests, after which Siveco is providing babysitting support onsite to ensure Coswin is effectively put into operation.
Training took place in several stages. An implementation study was conducted with the RPII team at the early stage of the project. Core Team training was performed on the preconfigured system at Siveco Shanghai mid-2010. A few months before “Go Live”, Siveco organized end-users training on site in Sabah, after which the power plant’s operation and maintenance team has started to use the CMMS to manage its daily maintenance job and spare parts inventory.
For more on Siveco’s pioneering approach to implement CMMS from the construction stage:
https://newsletter.bluebeecloud.com/en/reliability/reliability-preparing-maintenance-from-the-construction-stage/
https://newsletter.bluebeecloud.com/en/reliability/reliability-preparing-maintenance-from-the-construction-stage/
Functional scope of the CMMS
The CMMS covers a complete life-cycle asset management scope, as follows:
• Graphical diagram navigation
• Asset management
• Corrective maintenance
• Safety and work permits
• Preventive maintenance
• Stock management
• Repairable spares handling
• Procurement
• Asset management
• Corrective maintenance
• Safety and work permits
• Preventive maintenance
• Stock management
• Repairable spares handling
• Procurement
Results
According to Mr. Muhamad Kamal Ibrahim, Operations Manager at RPII O&M:
“Siveco’s role in the project proved to be critical, considering the very different working practices between Chinese construction firms and overseas power plant operators like us: Siveco’s experience of both ensured that that our expectations were met despite the obvious challenges.”
He added:
“The approach consisting in preparing the CMMS from the early construction stage helped us ensure operation readiness in time, a major business goal for Ranhill being our commitment to reduce construction time and providing the much needed energy for Sabah.”
Ranhill is now considering extending the usage of Coswin to its other units.
Ranhill Powertron II is the first major cooperative project of Siveco and Chinese engineering and construction companies in Asia. Siveco is actively promoting the same concept to Chinese EPC companies building infrastructures all over the world. The concept could also be successfully applied to Chinese power project, as operators’ expectations evolve and get closer to those of international players.