Driving improvement with Siveco’s Enhanced Maintenance services
Siveco China has for many years already established a professional Customer Support Organization: putting customers as the center, providing efficient customer support focused on improving maintenance management, with high customer satisfaction results. As of today, around 450 sites are enjoying Siveco China’s Support services, under two formulas: Standard Support or Enhanced Maintenance Service. Most of our customers chose the “Enhanced Maintenance Service” option, as it helps them to improve their maintenance practices on a daily basis, using the system as a framework… and it works! This offer packages two previously available services (annual maintenance assessments and traditional software support contracts) into one annual contract. The objective of the contract is to provide a measurable improvement in the utilization of the system, on a year-to-year basis. This improvement is guaranteed by Siveco and measured jointly with customer at the end of the year.
It principle is simple: Siveco experts will visit customers’ site at least once during the year for a system assessment. This assessment will be followed by clear recommendation and improvement proposals by Siveco, with measurable objectives to be obtained. Based on this, Siveco team will work out the next year’s plan to make sure that actions are implemented effectively. During the following year, Siveco will remotely monitor progress and coach customers. In this article we would like to review some of the results obtained by customers’ in recent years.
Nanchang Shuanggang Water Supply Company
On Dec 22, 2016, Siveco team came to the Nanchang Shuanggang Water Supply Company to conduct the first annual assessment (one year after the system was put in operation). The assessment proved that the initial project objectives have been achieved: 1) Set up advanced maintenance management concepts and methods in line with the ISO 55000 Asset Management Standard. 2) Establish as-built asset technical database as a basis for the company’ maintenance management system. 3) Use bluebee® mobule to perform inspection work. 4) Ensure that all the maintenance tasks are totally recorded and used for analysis and improvement. Based on the bluebee® mobile app, Nanchang Shuanggang Water Supply Company has realized the paperless maintenance management model. The Siveco experts gave improvement advice to help the customers improve gradually towards maintenance excellence: Nanchang Shuanggang Water is well on its way to achieve it!
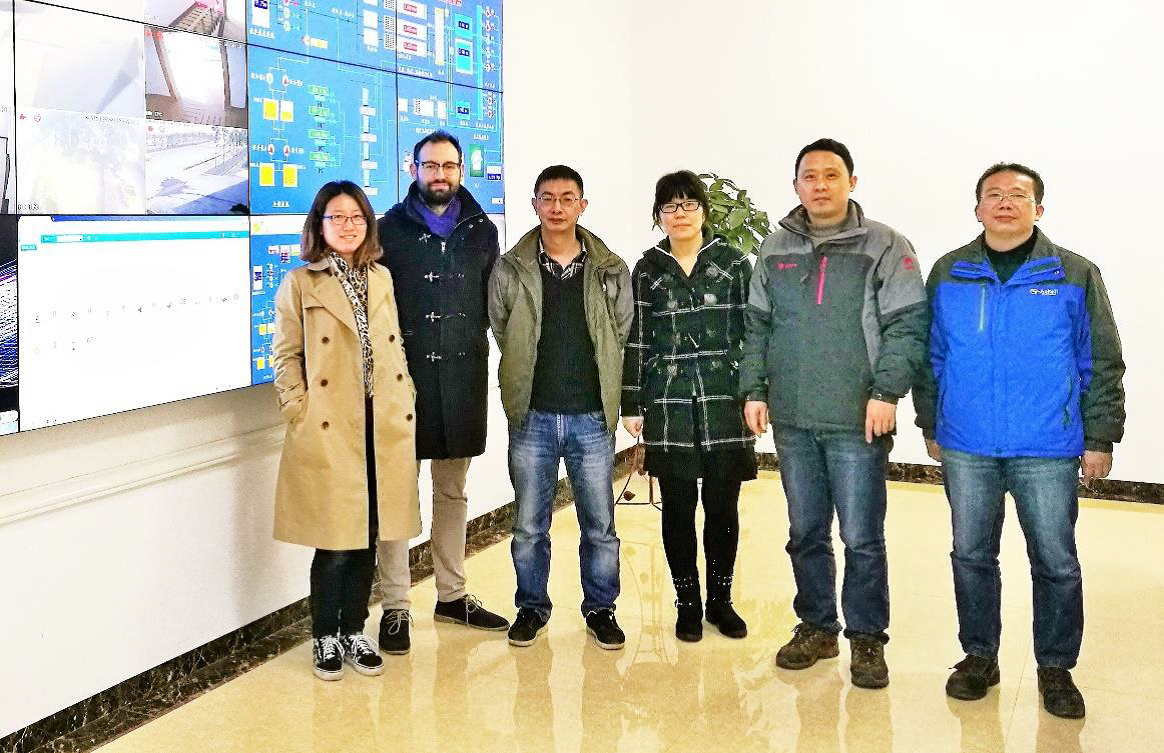
Suez Nantong waste-to-energy plant
On Dec 27, Siveco experts conducted the annual assessment for the Suez Nantong waste-to-energy plant, mainly focused on whether the plant’s maintenance management conformed to their group company’s Minimum Operating Standard (MOS) 7 steps, as defined by SITA Group. Finally, the two companies engaged in an in-depth discussion on how to perform effective data analysis. Siveco advised on the EU standard EN 15341 – Maintenance key performance indicators, also drawing on other Siveco customers’ successful experience. After the assessment, Siveco engineers improved the Suez Nantong’s monthly analysis reports accordingly, which were then used for the monthly follow-up.
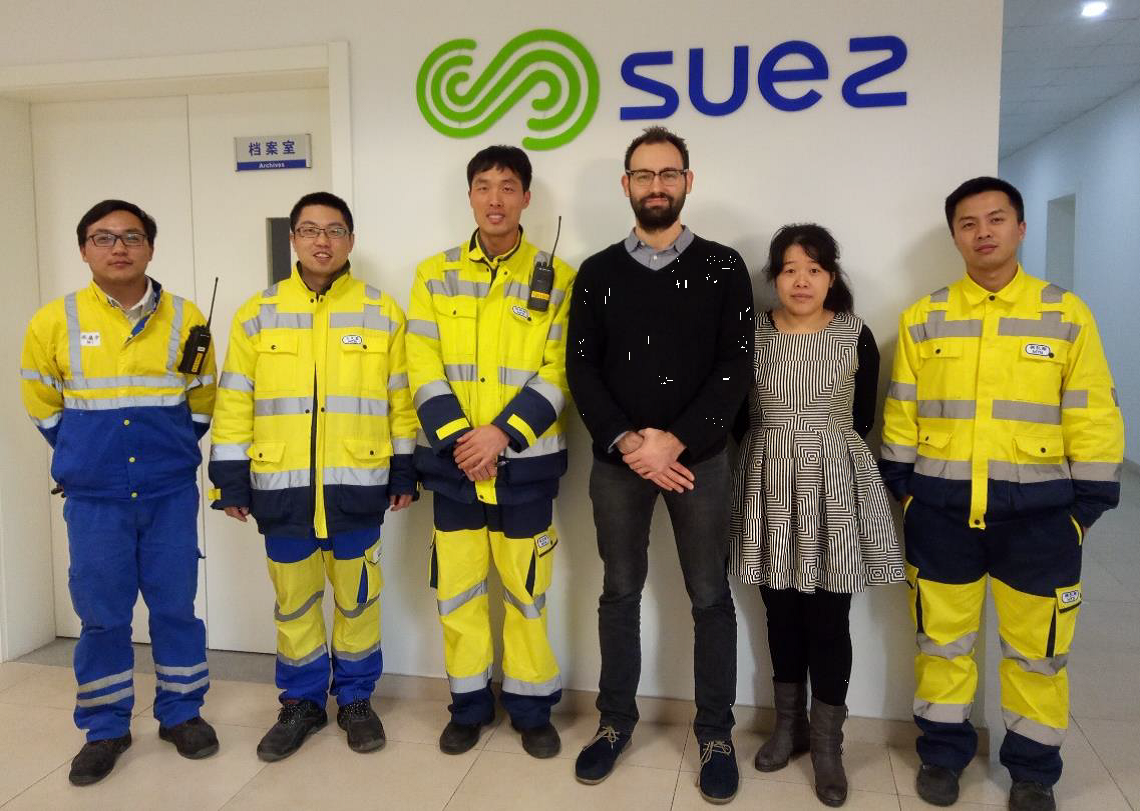
Saint-Gobain PAM (pipelines) China
To meet the development needs, the Saint-Gobain PAM (pipelines) China’s maintenance management organization has recently been centralized. Initially each factory of this large industrial complex had its own maintenance unit. The centralized management approach aims to unified management and scheduling of the maintenance activities and save costs. On Apr 27, 2017, Siveco team was invited to the Saint-Gobain PAM (pipelines) Xuzhou plant to review the organizational structure change and advice on its impact, then discussed how Coswin and bluebee® will support this change.
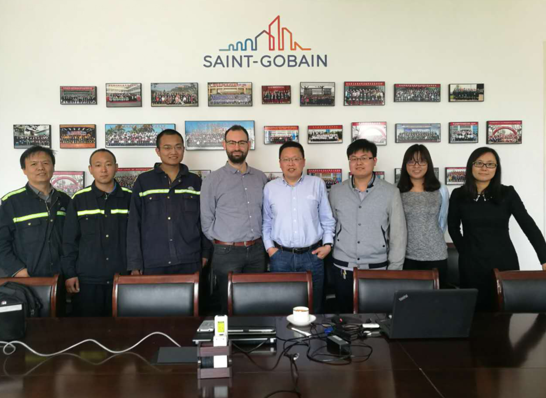
Daramic Battery Separators (Thailand)
In this month’s Customer Story, we feature Daramic Battery Separators, a large plant located in Thailand, also under Enhanced Support. In the first year, thanks to hard work by all involved onsite, based on clear management objectives and monthly follow-up, the company has reached its 97% uptime target. Daramic is now ready to continue for another year of support. More in the Customer Story.
Other services
In addition to the annual assessments and monthly coaching, Siveco organizes regular training for customers under Enhanced Maintenance Support. In 2016, the program covered New Coswin 8i features, Training on optimizing preventive maintenance plan, Training on optimizing Coswin usage, etc. The Siveco training not only provides system’s usage skills, but also offers a platform for different clients to communicate and share their maintenance management experience: many clients were very satisfied with the training.
Although satisfaction is good, we know that there are always new improvements opportunities ahead and we are more than willing to seize them! To help us provide the best possible support services in China and Asia, please send us your suggestions or questions to contact support@sivecochina.com!
Finally, we would like to take the opportunity of this newsletter to thank all our customers and customers-to-be for their constant trust in our services and products, for their hard work in joint improvement efforts and for all the fun time spent together!