The 3 reasons maintenance managers enjoyed upgrading to Coswin 8i
The main reason to upgrade from Coswin 7i to Coswin 8i is to further improve maintenance performance – at every level. As part of our 2015 Summer Roadshow, we have talked with many customers already using Coswin 8i and asked them what they liked in the new version, and why was it worth upgrading. Here is their feedback, from the point of view of maintenance managers. Recognizing that different people have different needs and views, we are preparing similar articles from the perspective of IT managers and top managers. New customers considering to implement Coswin 8i to support a maintenance improvement project may also find this useful.
1 – Improve your performance through value-added activities
Improved support for specific analysis and management decisions
Reports, already available in Coswin 7i are very useful: they provide a strong framework for failure analysis, monthly reporting, team performance analysis, etc… But this is not enough.
Sometimes maintenance engineers or maintenance managers might want to check a specific problem – for example during a kaizen session or a RCA workshop, or answer a specific question from their boss. Furthermore, they would like to justify their point (for example an investment request) with meaningful data, properly formatted in graphics.
The new Coswin 8i support direct extract to Excel: directly looking at the relevant Coswin screen, users can rearrange columns as desired (drag-and-drop), filter data based on any criteria (equipment category, production line, department, fault type, etc.), and click on the export button. Then the end-user can endlessly aggregate and adjust the data in Excel until they get the result they expect. Ready for the RCA or the investment request!
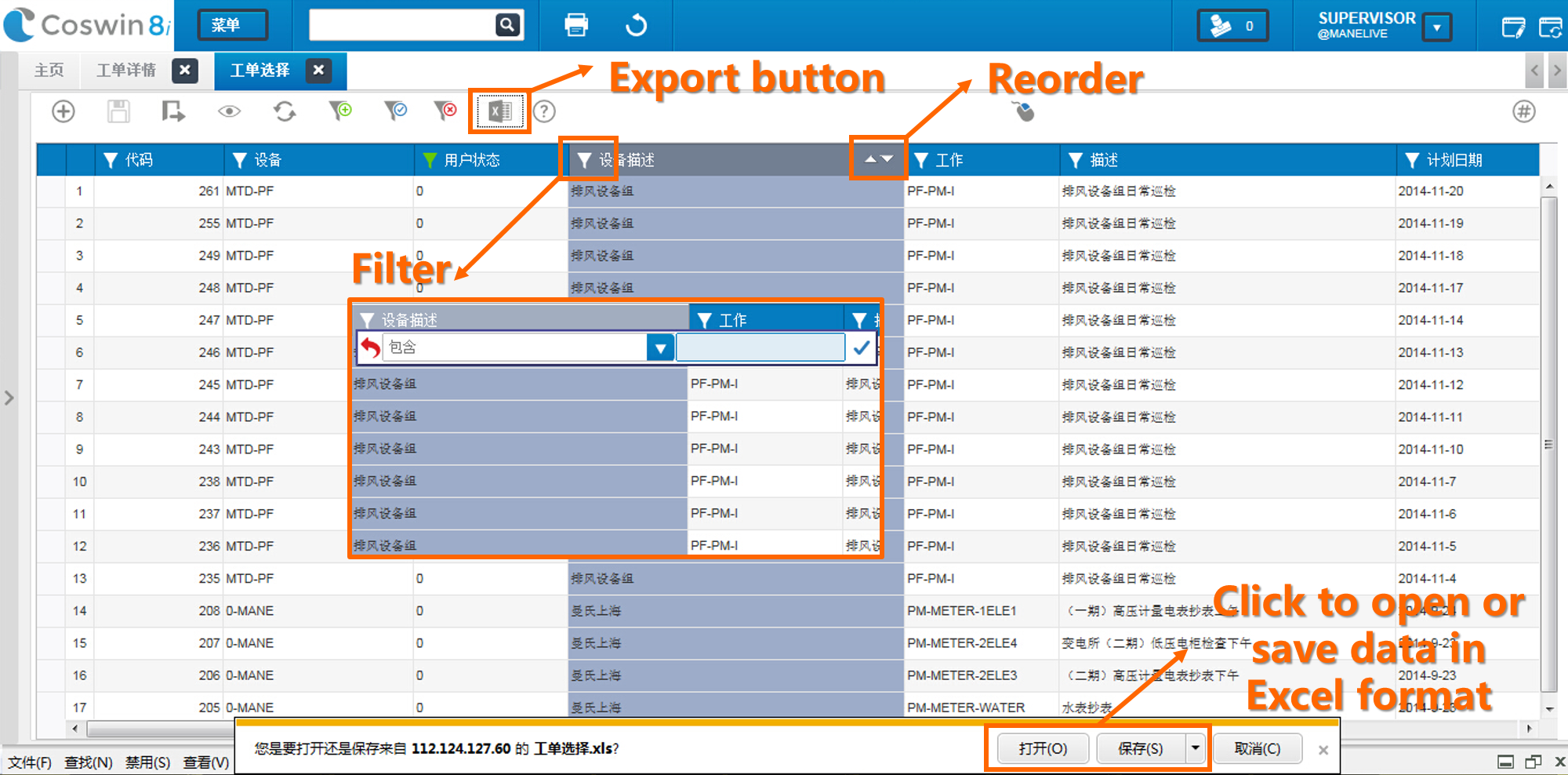
Improved communication with departments served by maintenance
Coswin 8i now comes with a comprehensive set of Helpdesk functionalities. Exchanges between maintenance department and their internal or external “customers” are better documented. Requests can be organized more accurately and their progress is tracked more accurately.
Complex requests requiring several Work Orders (WO) can be treated easily and remain linked together so that the requester can understand what’s going on, even if he is not familiar with maintenance activities.
Comments on status changes have even be added so that both parts can communicate in a very transparent manner.
2 – Improve your performance by managing maintenance knowledge better and faster
As we value strongly the experience of our users, making the system even more user-friendly has been the first objective of this new version. This has been achieved through a large numbers of “small improvements” – kaizen style!-, which will make the Coswin usage faster & more reliable.
Working faster
Many shortcuts and contextual menus has been added everywhere, but the innovation with the strongest impact is the ability to work directly from the list (no need to open records one by one like before). Additionally, the position of buttons and menus have been harmonized, so user can get familiar very fast with Coswin operation.
Here are the examples for some of the new features:
–
Fast access to workflow validation from the header
–
Contextual menu in WO, equipment, items, so the user can right click and access immediately to the relevant history, technical details, etc… directly from the list
–
Improved horizontal navigation
–
All modules accessible from the main menu in one click only
–
Files attached directly available in WO, maintenance guidelines, etc.. (no need to open a folder)
Working better through a more reliable operation of the system
Many sources of misoperations have been identified and eliminated in Coswin 8i! The users will do less mistakes, and will not waste time correcting them …or calling support for trivial issues. We are always pleased to receive phone call from our customers and to help them the best we could. But just like them, we strongly believe than “preventing an issue is better than solving it”: according to our statistics, such mistakes can make up to 70% of the call received for certain customers. Coswin 8i will save a lot of time on this, which can be reallocated to higher-value work (both on customer and Siveco side)!
Here below the examples for some of the new features:
–
Users can now be guided when they input information in the system based on their own profile or information already available on the screen
–
Status circuits can be configured based on user group or job type
–
Wrongly formatted inputs are highlighted in red, masks force the user to input data according to the expected format (AA-99-BB for instance)
–
Plan jobs & WO are displayed on the same screen when releasing, allowing the user to clearly manage its plan – jobs don’t “disappear” anymore.
–
There is an official “Cancel” status for WO, so the plan is left undisturbed when a cancellation is done, while the information is kept in the database.
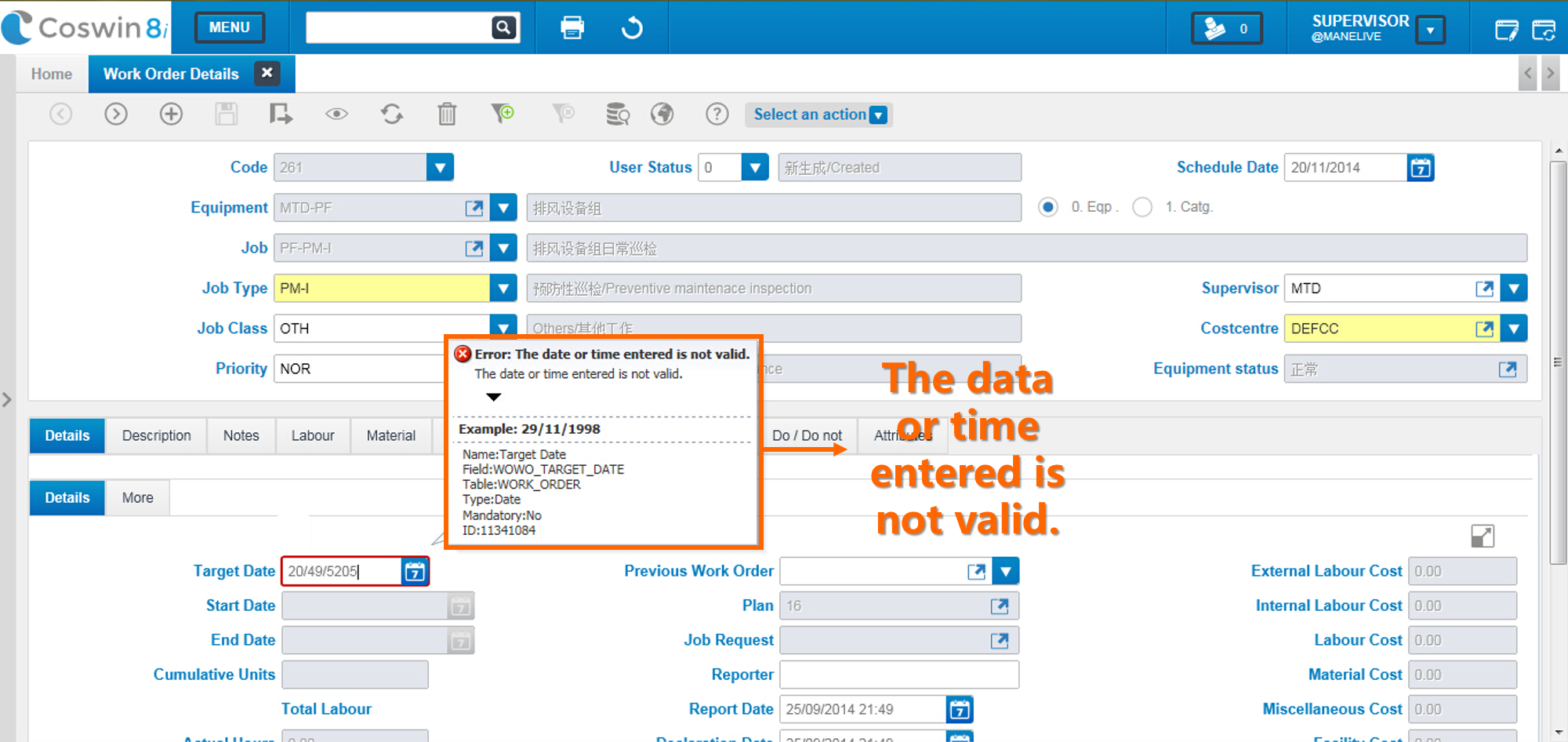
A comfortable work environment
A good, clean work environment also participate in the team’s efficiency. This has also been one of the key concern when designing Coswin 8i. The user can now have access to the information in a more direct and clear way, reducing the time spend and the risk of mistake together.
For example:
–
Ability to add “comments” when changing WO or Job Request status, and to review the history of status changes
–
Ability to “expand” the windows the user is working on, so that it takes the whole screen and all the info is catchable in one look.
–
Text windows are improved and allow formatting (bold, italic, size, color, hyperlink,…) and undo/redo.
–
Thumbnails for Employee, Items, Equipment: the right object can be spotted visually without ambiguity.
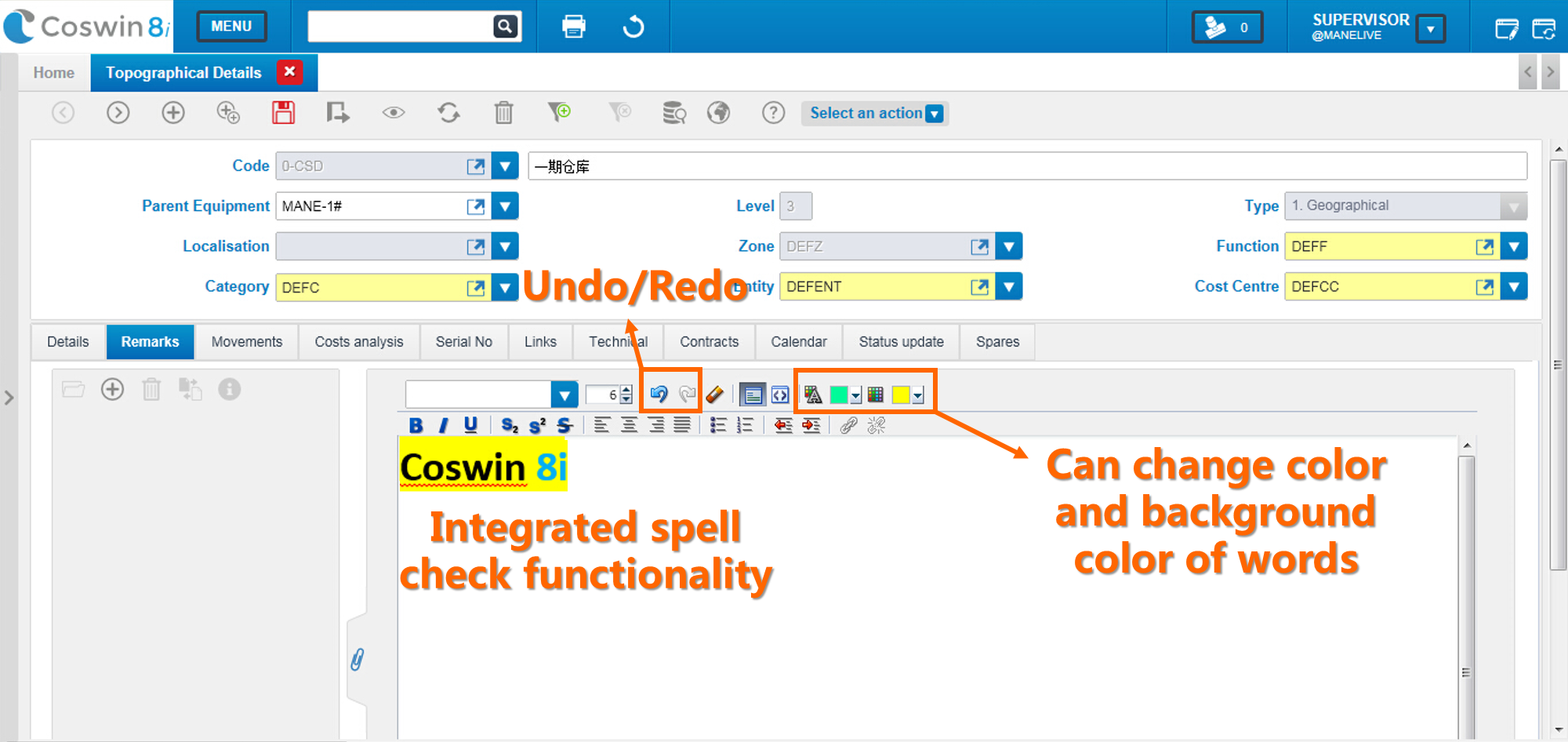
3 – Refresh & improve your maintenance management practices
According to our customers, this is perhaps the best reason to upgrade to Coswin 8i. Paradoxically, it doesn’t require Coswin 8i! How come?
At many customers, upgrading to Coswin 8i have been the opportunity to have a fresh look at the basics of maintenance engineering and to discuss them freely. Many good ideas from the users and expectations from top management have been taken in account during the upgrade so that:
–
Maintenance teams’ practices are more aligned with ISO 55000 requirements, new safety regulations and risk management approaches
–
Processes are streamlined, especially since today’s users grew more mature and shifted their expectations from the system, from pure administrative tool to decision-support system. Work feedback is more accurate and automatized.
–
Most of our customer reported a renewed interest & motivation in getting the job well documented, thanks to the pleasant and modern look of Coswin 8i!
Conclusion
Upgrading to Coswin 8i shows that the management remains committed to give teams a strong tool to manage their maintenance. This tool, like all the aspect of maintenance work, must be improved continuously in order to stay aligned with more and more ambitious objectives: efficiency, exposure to risk, work quality, etc…
In return, improvements in team’s efficiency, technical communication and, ultimately equipment reliability and performance are expected.