Measuring OEE in your CMMS/EAM
Overall Equipment Effectiveness (OEE) is one of the key indicators of performance in the manufacturing industry. Originally part of the TPM portfolio, OEE is now commonly used to assess the results of Lean Manufacturing initiatives. The OEE reflects the contribution of all players to the performance of a product line and is easily used for benchmarking not only within an organization but also with other companies.
What is OEE?
OEE and related indicators (in particularly Availability) are officially defined in various standards, to which we invite interested readers to refer. The utilization of standards is the best way to avoid endless discussions and common mistakes. For example, EN 15341, Maintenance, Maintenance Key Performance Indicators offers useful reference (more on this in a future article).
OEE is best explained by a picture:
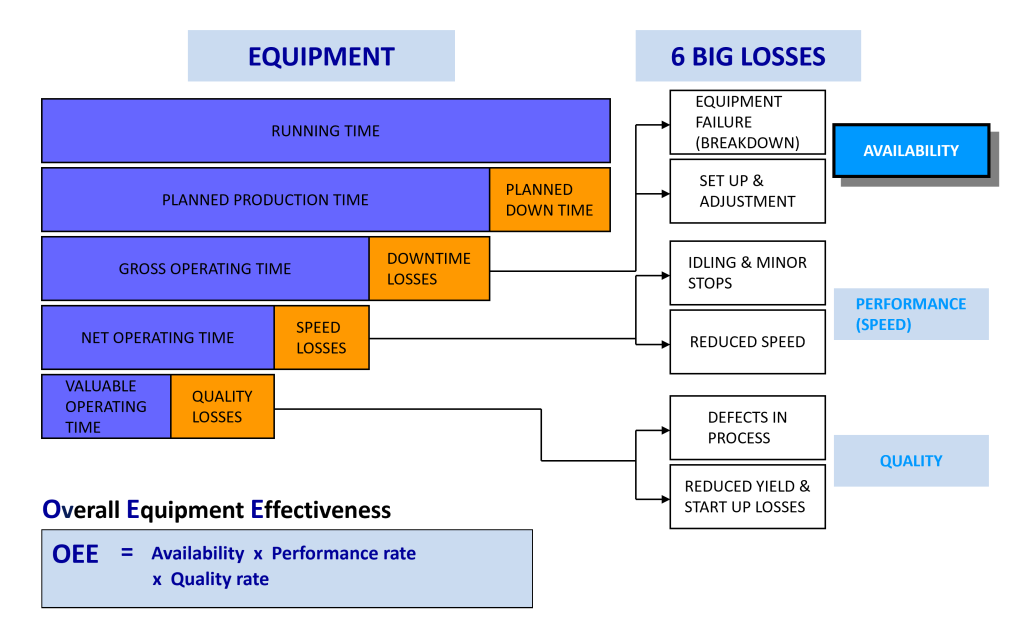
Now that the definition is clear, let us look into key considerations.
OEE is not everything!
A very popular indicator, OEE is often misunderstood.
- OEE does not reflect the link between Performance and Quality. It treats them independently, which is often not true based on the production team’s experience (“We know we can’t run the line over 500 units/min otherwise the scrap ratio will be too high”).
- OEE is penalizes variability amongst its subcomponents (Availability, Performance, Quality). For example: 20% x 80% = 16%, and 50% x 50% = 25% which does not necessarily reflect an industrial reality.
- OEE doesn’t take in account the fact that unscheduled stoppages are much more painful (and costly) than scheduled stoppages. It treats them equally (unless you drill down to the components of OEE).
- We do not recommend following the OEE for the whole plant (except in process plants, where one plant is in fact one large machine). If you really must, it is preferable to take the average OEE of all the production lines.
- OEE cannot be 100%… Even 100% is almost impossible… It would mean perfect quality, all the time, at the fastest possible speed, without downtime… OEE above 100% usually results from calculation mistakes (which may happen and should lead to corrections) and, if presented to management, a misunderstanding of OEE. 85% is considered World Class, 70% average.
- For Availability, discrepancies between production and maintenance records are common. Not necessarily alarming, the degree of discrepancy may reflect the communication gap between production operators and maintenance technicians.
- All in all, the components of OEE, the Availability, Performance and Quality ratio, at the right level in the equipment structure, are much more meaningful than OEE itself.
- Although the definition seems simple enough, the actual calculation of A, P, Q is complex and error prone in practice. Definitions and understanding may vary, the maths can be difficult, raw data hard to obtain. As a result, implementation mistakes are frequent.
- Last but not least, OEE does not take Health, Environment and Safety (or ESG) into account. OEE must always be completed with HSE indicators, with the understanding they may be related (for instance, running the equipment at higher than design speed may result in safety risks).
Which IT system to measure OEE?
Should the OEE be calculated in the maintenance system (CMMS/EAM), in production tracking systems (MES, ERP), in monitoring systems (IoT based, SCADA, PLC, DCS)? Or perhaps in an external system based on data from multiple sources either automatically or manually input? There is no right or wrong answer, it all depends on your current needs, situation, and IT landscape.
Probably the first question to ask: doesn’t the production department already provide all the reports and indicators required? This may be done using an ERP or MES system, or often it is simply in Excel with manual or semi-manual inputs. Most of the data required to complete the OEE come from production anyway. By letting production continue to handle such reports, the maintenance department can instead focus on implementing methodologies to solve technical problems. This is what we observe at most customers’: if a well-functioning production reporting system is already in place, perhaps it is not worth changing it.
On the other hand, ERP or MES usually do not offer analysis at the event level: what was the incident that contributed to the loss, its causes, resulting actions (corrective – immediate fix, equipment modification, etc. and preventive – changed maintenance frequency, new inspection routine, etc.) as most of the information needed would be in the CMMS or EAM system, if correctly implemented. Such ability to drill-down to such detailed data and to run analysis (for example on the effectiveness of action taken, on the causes contributing the biggest losses, etc.) is a major tool for improvement. Simply observing OEE trends won’t help define improvement plans.
All in all, the decision to measure OEE in the CMMS/EAM rather than in whatever system production is using must be taken based on the actual situation on site. It also depends on the level of maturity of the organization – a company struggling with permanent emergencies and no preventive maintenance is well advised to focus on the fundamentals first.
Generally, it makes more sense in the process industry (e.g. pulp and paper, steelmaking, chemicals etc.) than in discrete manufacturing i.e. the closer the maintenance department is to the core operations, the more interesting it becomes to have OEE in your CMMS/EAM. Process plants are also more automated, allowing the CMMS/EAM to collect data directly from the control system.
Can your CMMS handle it?
In most companies, the CMMS or EAM system has not been setup to properly calculate OEE in a useful manner. Large systems controlled by corporate IT are often inflexible or difficult to adjust. Cheaper cloud-based systems often have standard setup that result in wrong OEE values (sometimes above 100%, which makes no sense) or may lack useful, actionable analysis tools.
Calculating the OEE may also require pulling data from multiple systems (ERP, MES, DCS/SCADA etc.) through interfaces, adding complexity to the IT setup. Additional manual input into the CMMS may also be required, adding to the maintenance team’s administrative burden.
All in all, it is often difficult to calculate OEE in the existing CMMS.
Beyond OEE: improving OEE!
Always keep in mind that the OEE is a strategic indicator, reflecting the utilization of invested assets. From the operational point of view, what matters is the evolution of the OEE and the analysis of causes, in order to determine and implement improvement.
This requires not only the total OEE value, but also that of its components A, P and Q at different levels in the plant structure. The ability to drill-down to incidents or events that contributed to losses for systematic analysis based on the symptoms, defects, causes and actions, the impact of the losses (in terms of A, P and Q but also cost and risk – again HSE comes into play, although it is not measured in the OEE). Once improvement action plans have been defined (machine modifications, new maintenance routines, autonomous maintenance actions etc.), how to track their execution and how to measure their effectiveness, their impact on the OEE?
Most software solutions, either in their design (ERP, MES, IoT-based solutions) or in their implementation (CMMS or EAM) totally ignore these aspects. Yet, improving OEE is more important that simply measuring OEE.
How to do it with Coswin 8i and bluebee®?
For users of our CMMS Coswin 8i, see this previous article on how to calculate OEE.
The bluebee® platform on the other hand allows a flexible approach to collect data from existing systems or provides its own data collection mechanism directly from operators and technicians using the mobile app. bluebee® is a Smart Operation & Maintenance platform that natively interacts with Mobile Users and Connected Objects to enable management decisions based on true data from the field. bluebee® is designed to complement, rather than compete with, legacy corporate IT systems such as EAM, CMMS, ERP.
This will be covered in more details in a coming article.