CMMS/EAM系统中的设备综合效率(OEE)指标
源于TPM概念的设备综合效率(Overall Equipment Effectiveness,下文称“OEE”),是制造业中主要的绩效指标之一,常用于评估精益制造措施的实施结果。OEE反应了生产线上所有人员对生产线绩效的促进作用,不仅可用来在组织内部进行标杆管理,也可以用来与其他公司的生产绩效进行比较。
何为OEE?
各种国际指标对OEE及其相关指标都进行了官方定义,为避免无尽争论和常见错误,使用国际标准是最佳方式。有兴趣的读者可以查阅相关资料,如:EN 15341-维护关键绩效指标等,都提供了重要参考,在未来的文章中我们也将带来更多相关内容。
OEE的含义如下图所示:
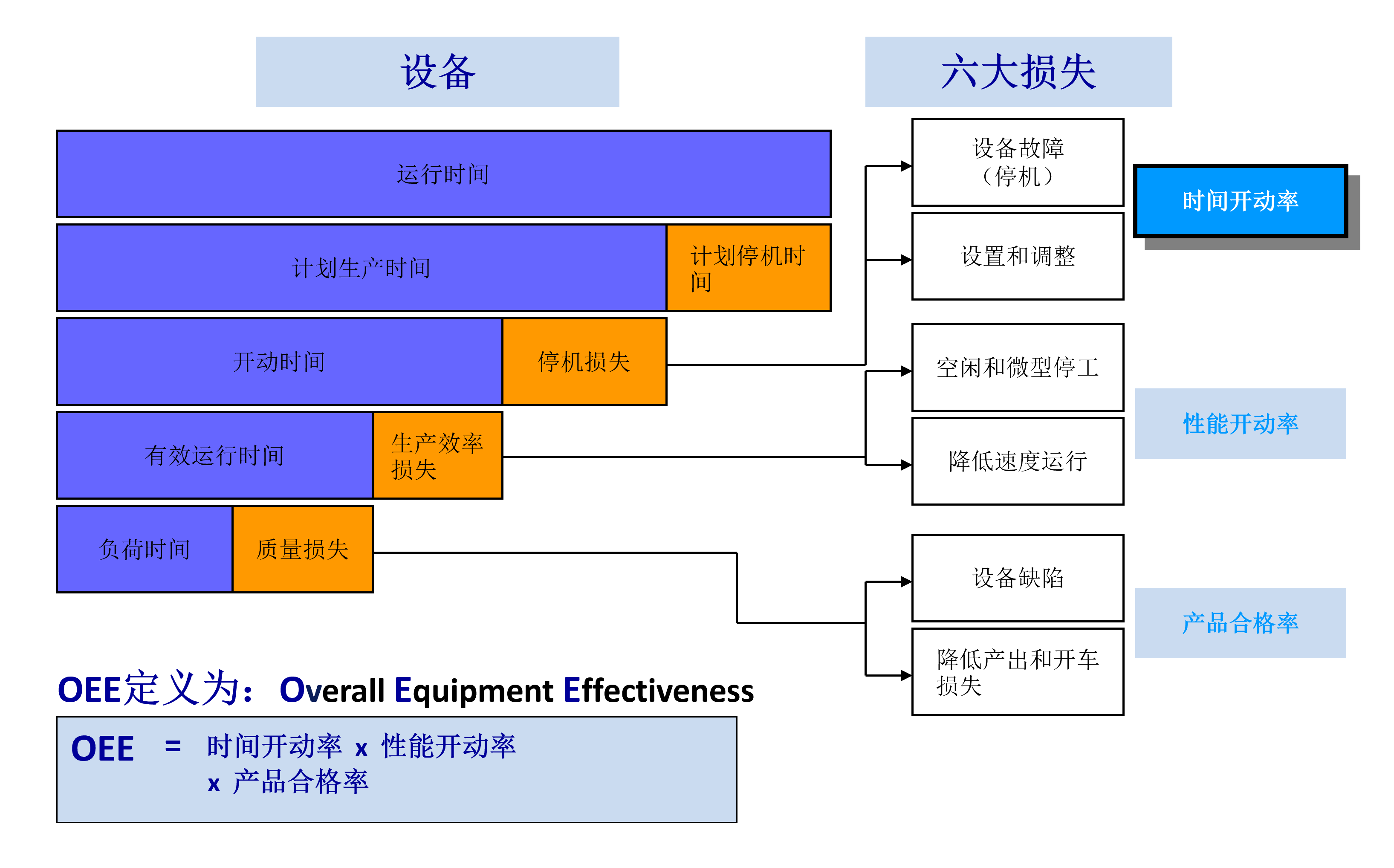
现在,我们已经理清了OEE的定义,接下来将深入探索OEE的关键考虑因素。
OEE并不代表一切!
作为一项流行指标,OEE常常被误解
- OEE不能,也几乎不可能达到100%,那意味着完美的质量:在任何时候都以尽可能快的速度完成维护行动、不存在停机时间。OEE超过100%通常是由于计算错误(这是可能发生的,需要被纠正),将错误结果递交给管理层会造成其对OEE的误解。OEE达到85%通常被认为是世界级的,70%则为平均标准。
- 就时间开动率而言,生产报表和维护报表之间的误差是正常的。误差的程度恰恰反映了操作人员和维护技术人员之间的交流缺口。
- 总而言之,OEE的组成(时间开动率、性能开动率、产品合格率)在设备结构中处于恰当的水准,比OEE本身更有意义。
- 虽然定义看起来很简单,但时间开动率、性能开动率、产品合格率的实际计算很复杂,在实践中容易出错。定义和理解可能各不相同,计算起来可能很困难,原始数据难以获得。因此往往就会发生计算错误。
- 最后但同样重要的是,OEE并不包含对健康、环境和安全(或ESG)的考量。因此,OEE必须始终和HSE指标一起去看,并需要正确理解二者可能的相关性(例如:以高于设计速度运行设备可能会导致安全风险)。
使用怎样的IT系统来进行OEE的测量?
OEE应该在维护管理系统(CMMS/EAM)、生产追踪系统 (MES、ERP)、监控系统(基于物联网、SCADA、PLC、DCS)中计算,还是基于多个来源的数据在外部系统中自动或手动输入?其实这没有对错之分,一切都取决于您现下的需求、设备情况和 IT 架构。
也许第一个要问的问题就是:生产部门已经准备好提供所有必须的报表和相关指标吗?要知道,计算OEE的大部分数据其实都来自于生产部门。虽说用Excel来计算也不会太过复杂,但多数数据都可以通过ERP或MES系统来获得。在让生产部门处理这些报表的同时,维护部门就可以专注于解决某些技术问题。这也正是我们在大多数客户那里观察到的:如果您已经拥有一套完善的生产报表系统,那就没有必要对其进行改动。
从另一方面看,ERP 或 MES 通常无法提供事件级别的分析:造成损失的具体事件、其原因、采取的措施(纠正措施——立即修复、设备修改等,以及预防措施——改变维修频率、新的巡检工作等)。如果实施正确,大部分需要的信息都会在 CMMS 或 EAM 系统中,从而作为改进的重要工具来深入到数据细节并进行分析(例如对采取措施的有效性进行分析,对造成最大损失的原因进行分析等),仅仅观察 OEE 趋势是无法帮助制定改进计划的。
总之,选择在CMMS/EAM系统,而非生产部门正在使用的其他系统来测量OEE的这个决策是取决于实际情况而定的。同样这也取决于企业管理层的成熟程度——如对一家长期为各种紧急事件而疲于奔命且没有实施预防性维护的工厂而言,我们会建议其首先着眼于完善并改进现在的基本维护工作。
换言之,对流程制造业(比如:纸浆和造纸、炼钢、化工等)工厂而言,使用OEE指标要比离散型制造企业更有意义。而且,流程型制造工厂的自动化程度也较高,从而CMMS/EAM系统就可以直接从控制系统中采集到所有所需的数据。
您的CMMS能胜任吗?
对大多数公司来说,现有的CMMS或EAM系统并没有作为一种有效的方式来正确计算OEE。由企业IT控制的大型系统往往不够灵活或是难以调整。低廉的基于云的系统通常有标准设置,导致了错误的OEE值(有时超过100%,实际上毫无意义),或者可能缺乏有效的可行性分析工具。
计算OEE可能还需要通过多个系统接口(如ERP、MES、DCS/SCADA等)提取数据,会增加IT设置的复杂性。可能还需要额外手动输入到CMMS系统中,增加了维护团队的管理负担。
总而言之,在现有的CMMS系统中,通常很难计算出OEE。
不止是OEE:提高OEE!
要谨记的是,OEE只是一个反映企业所投资资产使用率的战略指标而已。从生产运营角度看,重要的是通过使用OEE指标和根本原因分析来改进企业现有的生产工作绩效。
这不仅需要总OEE值,还需要其组成部分(时间开动率、性能开动率、产品合格率)在工厂结构中不同层次的OEE值。能够深挖导致损失的事件或活动,以便根据症状、缺陷、原因和行为、损失的影响,从时间开动率、性能开动率、产品合格率以及成本和风险方面进行系统分析(尽管HSE不在OEE中测量,但在这一过程中再次发挥了作用)。一旦制定了改进行动计划(设备修改、新的定期维护、自主维护操作等),又该如何跟踪执行情况、如何衡量改进行动的有效性及其对OEE的影响?
大多数的软件解决方案,无论是在设计(ERP系统、MES系统、基于物联网的解决方案等)还是在实施(CMMS/EAM系统)中,都完全忽略了这些方面。然而,提高OEE比简单地测量OEE更重要。
如何在Coswin 8i 和bluebee®中计算OEE?
对于Coswin 8i CMMS系统的用户,请参阅《如何在Coswin 8i中计算OEE》这篇文章。
另一方面,bluebee®平台支持从现有系统灵活收集数据,或通过移动应用程序由运营和技术人员直接上传提供数据。bluebee®作为一个智慧运维平台,可与移动用户和物联设备进行交互,从而根据来自现场的真实数据支持管理决策。bluebee®旨在补充,而非与传统的企业IT系统(如EAM, CMMS, ERP)竞争。
更多信息将在以后的文章中详细介绍。