bluebee® functional components
In this month’s bluebee® tips & tricks, we provide an overview of the main functional components of our mobile solution “for the worker of tomorrow”. Previously published articles in this series include “What is bluebee®?” and “bluebee® system architecture and components“.
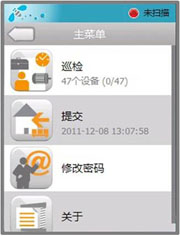
Example of main menu (PDA version)
Screenshots in this article illustrate how the standard bluebee® can be configured to meet the demands of specific industries or customers, on both smartphone/PDA and tablet devices. The entire app is available in both Chinese and English.
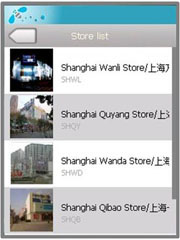
Direct access to all facilities information
Facilities & equipment
Displays all facilities and equipment information, synchronized with the central database based on each mobile user’s profile and current task, including equipment tags (from RFID/barcode reading), technical specifications, drawings, pictures and associated files. All related records are directly accessible, for example meter readings, work history, inspection plans etc.
Benefits:
– Ensures immediate access to all related technical data from the central database, directly from the technician’s mobile with a few finger clicks.
– Build-up of a well-structured historical database for analysis and improvement, since all bluebee® records (job requests, work orders, inspection reports etc.) are linked to a specific facility or equipment.
– In Surveyor mode, direct creation of equipment data by technician during onsite visits: tag number, equipment type and model, photo, equipment condition with possibility to record defects or non-conformities directly in the mobile with a simple wizard.
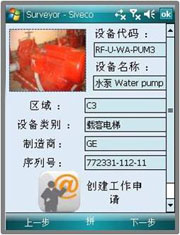
Technical asset data (after scanning asset tag – RFID or barcode)
Work Order
The Work Order is the main vehicle for know-how in bluebee®, a highly configurable tool, designed to support a vast range of work processes: predefined or ad-hoc, planned or unplanned, technical (maintenance, operations) and non-technical (audits, cleaning) etc.
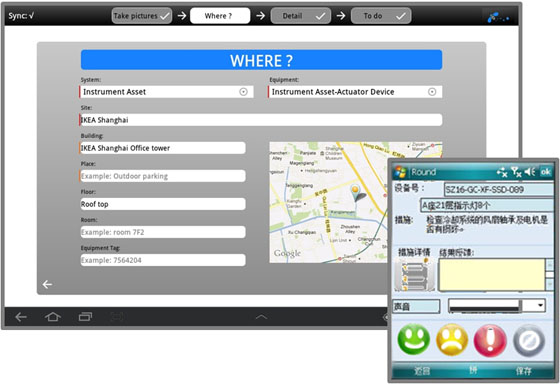
Examples of work orders, with easy input using color codes and map localization (PDA and tablet)
Benefits:
– Eliminates the inefficient and error-prone process of managing paper Work Orders, writing down feedback by workers and manual input by secretary.
– Technicians obtain immediate assistance to complete their job according to standard company practice, the system even providing troubleshooting assistance in case of problems. Ensures job safety and compliance with regulations through clear guidelines provided on-the-job to workers through the mobile.
– Data collected from the field is immediately made available centrally, for analysis and action.
– Technicians obtain immediate assistance to complete their job according to standard company practice, the system even providing troubleshooting assistance in case of problems. Ensures job safety and compliance with regulations through clear guidelines provided on-the-job to workers through the mobile.
– Data collected from the field is immediately made available centrally, for analysis and action.

Reporting measurements (after scanning measurement point on PDA)
Measures & meters
Measurement points and meters are managed in relation to the equipment and facilities they belong to. All corresponding processes, such as regular readings (with warning for abnormal reading, triggering and tracking of follow-up actions), calibration, maintenance and meter replacement, are supported in bluebee®. Points are tagged with RFID chips or barcodes for quick identification by scanning.
Benefits:
– Ensuring the technician has actually been onsite to complete the job, by mandatory identification of measurement point or meter through RFID or barcode scanning.
– Eliminating risk of error thanks to display of related measurement point or meter information, including clear layout and picture, reading instructions if needed.
– Provide assistance in case of abnormal readings, through warning and access to historical readings from the central database.
– Complete integration with back-office system (bluebee® cloud or existing solution) for trending and analysis.
– Ensures that manual readings, that often fall in the gaps and as a result can be critical compared to automated online readings, are performed efficiently.
– Eliminating risk of error thanks to display of related measurement point or meter information, including clear layout and picture, reading instructions if needed.
– Provide assistance in case of abnormal readings, through warning and access to historical readings from the central database.
– Complete integration with back-office system (bluebee® cloud or existing solution) for trending and analysis.
– Ensures that manual readings, that often fall in the gaps and as a result can be critical compared to automated online readings, are performed efficiently.
Resources
Manages all resources needed to complete the job, both from an organizational point-of view (departments, suppliers, in-house teams and contractors), as well as materials (parts, consumables, tools, whether stocked, purchased or leased). People and their contact details (directly available for phone call, SMS or email) are maintained centrally and synchronized to every device, with all related HR information (availability, skills, certificated, ID photo, responsibilities). Stock transactions can be managed from the mobile, in connection with the back-office inventory system. Purchase requests can be raised.
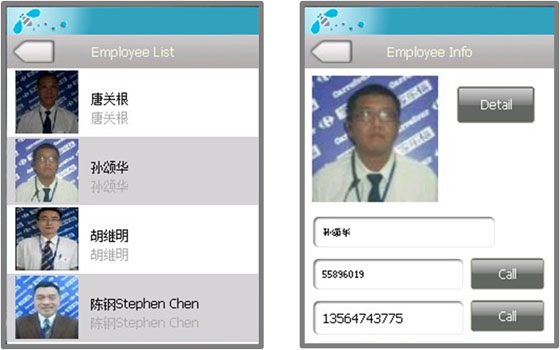
Direct access to employees and skills information
Benefits:
– Quickly find reference person, such as supplier’s contact person for a specific service contract or a piece of equipment, in-house expert for a certain category of assets (e.g. HVAC expert) – and then allowing one-click phone call.
– Improved work safety, by checking adequacy of an employee’s skills and qualifications/ certificates for a specific job, by viewing all related identification information from the central system.
– Increased accuracy of stock data, by allowing mobile workers to scan bins and parts, to perform stock count, to issue and receive parts, at anytime, from anywhere in the warehouse.
– Full integration with the enterprise’s inventory, purchasing and HR systems (for example SAP).
– Improved work safety, by checking adequacy of an employee’s skills and qualifications/ certificates for a specific job, by viewing all related identification information from the central system.
– Increased accuracy of stock data, by allowing mobile workers to scan bins and parts, to perform stock count, to issue and receive parts, at anytime, from anywhere in the warehouse.
– Full integration with the enterprise’s inventory, purchasing and HR systems (for example SAP).
Documents
Ensures all documents stored in the back-office system can be viewed in the mobile, including office documents, drawings, photos and multimedia file – the available bandwidth from your telecom operator being the only limit. Documents can be linked to various objects, typically facilities and equipment, as well as work orders. Tablet devices allow the best usability for viewing documents, with multi-touch zooming capability in large screen format.
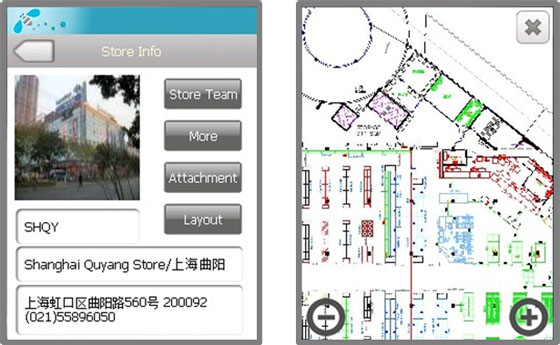
Documents are directly available: facility layout and related information (PDA version)
Benefits:
– Helps workers carry out their daily work, by making all the knowledge accumulated in the company available to them anywhere, anytime.
– Access to drawings and technical documents, especially critical for technical jobs, with direct access from Work Order or Equipment (no need to search in a large document library).
– Ability to create multimedia records, including pictures, movies and voice records, directly onsite, which will then be synchronized with the central database, allowing field technicians to built up a practical know-how base.
– Full security and users rights settings, permitting users to only view documents related to their job and their clearance level.
– Access to drawings and technical documents, especially critical for technical jobs, with direct access from Work Order or Equipment (no need to search in a large document library).
– Ability to create multimedia records, including pictures, movies and voice records, directly onsite, which will then be synchronized with the central database, allowing field technicians to built up a practical know-how base.
– Full security and users rights settings, permitting users to only view documents related to their job and their clearance level.