Making sense of Lean: Mr. Harada’s interview on equipment maintenance and the Toyota Production System (TPS) (Part 2)
This month I am proud to introduce the second part of Tom Harada’s interview on the link between maintenance and lean manufacturing. The first part was published in our December edition 2011 and can be found here. In this month’s interview, Tom Harada provides deeper and more specific insight into the subject, which many of our readers will feel familiar with. Maintenance is at the core of operating a lean production system. It is perhaps even truer in China, where equipment reliability and the supporting maintenance organization tend to be weaker than in the west: more often than not, maintenance is the weakest link in a lean supply chain in China, which unfortunately many manufacturers learn from accidents. This has been a recurrent topic in this newsletter and more generally for Siveco (I have spoken about again on this at an event in Kunshan two weeks ago). I would like to thank Tom Harada and his interviewer Art Smalley for lending their powerful voices to our cause!
Art:
On a different vein what type of maintenance organization is used in Toyota?
On a different vein what type of maintenance organization is used in Toyota?
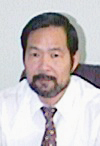
Tom:
It depends. In a vehicle assembly plant we can’t tolerate even a few minutes of down time so the maintenance technicians response time is very critical. However the equipment is less complex and requires fairly straight forward trouble shooting. Tolerances are thought of in millimeters for example. In this type of shop a territory style organization is generally used. The maintenance person would even report to a production manager.
It depends. In a vehicle assembly plant we can’t tolerate even a few minutes of down time so the maintenance technicians response time is very critical. However the equipment is less complex and requires fairly straight forward trouble shooting. Tolerances are thought of in millimeters for example. In this type of shop a territory style organization is generally used. The maintenance person would even report to a production manager.
However, in an engine plant we have more precision machines to maintain. Tolerances by way of comparison are in microns or .001 millimeters. This of course necessitates more time to develop a skilled trades person in terms of electrical knowledge, mechanical knowledge, hydraulics, lubrication, measuring, tooling, etc. The average time to make a repair on a machine tool is also much longer than on an assembly machine. So we employ a central dispatch system and work often in teams of two people. One person diagnoses the situation and the other simultaneously gets the necessary drawing or spare parts, etc. Together they can work faster and also we can level up skills in terms of cross training.
Art:
Is there a difference in terms of ratios for maintenance to production workers between shops that have primary processing (casting, forging, and machining) versus final assembly?
Is there a difference in terms of ratios for maintenance to production workers between shops that have primary processing (casting, forging, and machining) versus final assembly?
Tom:
Of course. It takes more skilled trades people in equipment intensive shops. Maybe two or three times as many comparatively speaking in some instances. I don’t want to quote ratios though since it also depends up where in the life cycle of the equipment the production shop is as well. For example a machine shop in the middle of the bath tub curve will need fewer maintenance resources than a machine shop that is either at the beginning of the life cycle curve or end of the curve. It is not so easy and very dangerous to just quote ratio numbers. We move people around depending upon the specific requirements of the situation.
Of course. It takes more skilled trades people in equipment intensive shops. Maybe two or three times as many comparatively speaking in some instances. I don’t want to quote ratios though since it also depends up where in the life cycle of the equipment the production shop is as well. For example a machine shop in the middle of the bath tub curve will need fewer maintenance resources than a machine shop that is either at the beginning of the life cycle curve or end of the curve. It is not so easy and very dangerous to just quote ratio numbers. We move people around depending upon the specific requirements of the situation.
Art:
What basic types of maintenance practices are employed?
What basic types of maintenance practices are employed?
Tom:
Generally there are five basic categories at least in a machine shop like Kamigo. Everywhere there are slight differences of course. The five general types are breakdown maintenance (BM), preventive maintenance (PM), daily maintenance (DM), corrective maintenance (CM), and maintenance improvement and prevention (MP).
Generally there are five basic categories at least in a machine shop like Kamigo. Everywhere there are slight differences of course. The five general types are breakdown maintenance (BM), preventive maintenance (PM), daily maintenance (DM), corrective maintenance (CM), and maintenance improvement and prevention (MP).
Art:
Can you say a brief word about each one?
Can you say a brief word about each one?
Tom:
BM is the most obvious. Our goal is to minimize the percentage of time we spend on BM related work since it is costly and reactive. None the less it still occurs and we have to execute it as efficiently as possible. In the past time we studied a breakdown calls and analyzed where the actual time was being spent. The concept of SMED (Single Minute Exchange of Die) for example can be applied to maintenance work too. Every simple breakdown should be done in ten minutes or less – we call this single minute maintenance. We also compile detailed equipment breakdown history records for our data base. A key focus although reactive is to constantly work on improving the top five machines in terms of the frequency and intensity of the breakdown.
BM is the most obvious. Our goal is to minimize the percentage of time we spend on BM related work since it is costly and reactive. None the less it still occurs and we have to execute it as efficiently as possible. In the past time we studied a breakdown calls and analyzed where the actual time was being spent. The concept of SMED (Single Minute Exchange of Die) for example can be applied to maintenance work too. Every simple breakdown should be done in ten minutes or less – we call this single minute maintenance. We also compile detailed equipment breakdown history records for our data base. A key focus although reactive is to constantly work on improving the top five machines in terms of the frequency and intensity of the breakdown.
PM is just the practice of implementing preventive actions before the machine breaks. We have recommended lists from the supplier about basic PM items but we also learn to add our own based upon the actual condition of the machine and the point in the life cycle. We also work on adjusting the frequency of the PM interval as well so we don’t over-maintain the machine. Doing unnecessary PM work is a form of waste like over-production.
DM is the type of daily maintenance work that the operator is tasked with performing and not the skilled trades person. This involves a lot of simple inspection and cleaning work. For example key items always include checking coolant condition, tooling wear, hydraulic oil levels, lube levels, etc. By doing these checks the operator can discover many little things like leaks or damaged hoses, etc. that we can then fix between the shifts and avoid a more costly breakdown later.
CM is the acronym for corrective maintenance. Every machine has a weak spot of some kind and you only find them after years of operation. Where it makes economic sense we modify equipment to improve the basic design while it is still in production if there is a pay back or improvement to quality. Sometimes this is as basic as improving the design of a fixture to hold the part better, or eliminating cutting chip build up. In other cases it is entirely redesigning a mechanism that for some reason just fails every six months for example. This is a form of machine kaizen and we are quite good at it.
The last major category is maintenance prevention (MP). Senior people in the department spend a lot of time up front when we order new equipment studying how we will maintain it properly. Often you only get one chance to fix certain items before the equipment specifications are finalized. We examine equipment and look for ways to maintain things easier or even eliminate the need to maintain it at all if possible. This is high level work though and does not happen often since machine tools are often used for 10-15 years.
Art:
What are key points in maintenance for Toyota?
What are key points in maintenance for Toyota?
Tom:
It is difficult to summarize since there is so much. But here are what I consider the main points of our maintenance system.
It is difficult to summarize since there is so much. But here are what I consider the main points of our maintenance system.
First we recognize the notion of the life cycle curve. We adjust our resources and the nature of our work to reflect this basic fact of equipment life. Our goal is to efficiently use and maintain the production asset at the highest level necessary to support production. We never over maintain or under maintain.
Second we spend a lot of time training and developing skilled trades people in maintenance. Equipment technology is constantly advancing and we need to improve our skill sets in order to keep up. It is not just hard skills sets that we focus on but the soft skills as well also. Maintenance workers are taught how to standardized certain repeat jobs, how to problem solve and get to the root cause of breakdowns, and how to spot machine kaizen opportunities.
Third we are very good at basic data collection and trend analysis. I can easily tap into the equipment history database and see where the most breakdowns are occurring on any line in terms of frequency and intensity. I can sort by machine, by station, by type of fault, or by category and get useful information. This is only because we train people how to input the data correctly and make sure they understand how to use it as well. This is very important.
Fourth we plan and execute maintenance work very efficiently. Production departments will not give us the machine for a long period of time. So we have become very adept at working in things between shifts and on weekends especially for our top problem machines.
Fifth we are very diligent about maintaining all the documentation we need for trouble shooting and analysis. We have very standard lists of documentation that we keep for each machine and store it effectively. For example PLC drawings, CNC program, spare parts lists, hydraulic oil and lubrication oil charts, machine assembly drawings, etc. Without this documentation we can not make good repairs.
Lastly as I said we practice kaizen in maintenance organization as well. We problem solve the top five machines every week and every month. In some cases we analyze the repair task from a time study point of view and ask why it took so long. We are constantly asking why certain machines break down and confer with the external vendor. On more difficult maintenance items we think of ways to make it easier in the future. On reliability problems we look for ways to build a better process. Toyota maintains very close cooperative ties to its equipment vendors in Japan. The opportunities are endless if you look at it the right way.
Lastly as I said we practice kaizen in maintenance organization as well. We problem solve the top five machines every week and every month. In some cases we analyze the repair task from a time study point of view and ask why it took so long. We are constantly asking why certain machines break down and confer with the external vendor. On more difficult maintenance items we think of ways to make it easier in the future. On reliability problems we look for ways to build a better process. Toyota maintains very close cooperative ties to its equipment vendors in Japan. The opportunities are endless if you look at it the right way.
Art:
Do you measure OEE?
Do you measure OEE?
Tom:
No it is not a good management metric for us. It is a good spot analysis tool for use some times. OEE has several flaws from a practical point of view. Anytime you measure six things and multiple them together to get a number there is danger. It is better to have the six components understood and tracked individually. Otherwise you can’t tell the difference between 75% OEE and 85% OEE. The former could be better if was due to the production mix and number of changeovers. The latter could have fifteen percentage points of scrap for example and be a total disaster. OEE is also based upon machine cycle time and not production line takt time so driving a higher OEE can lead to over production if you are not careful. Also in a big machine shop like Kamigo with over 5,000 machines you would need a small army to collect all the data required. We occasionally use it as a spot analysis tool but not as a management metric.
No it is not a good management metric for us. It is a good spot analysis tool for use some times. OEE has several flaws from a practical point of view. Anytime you measure six things and multiple them together to get a number there is danger. It is better to have the six components understood and tracked individually. Otherwise you can’t tell the difference between 75% OEE and 85% OEE. The former could be better if was due to the production mix and number of changeovers. The latter could have fifteen percentage points of scrap for example and be a total disaster. OEE is also based upon machine cycle time and not production line takt time so driving a higher OEE can lead to over production if you are not careful. Also in a big machine shop like Kamigo with over 5,000 machines you would need a small army to collect all the data required. We occasionally use it as a spot analysis tool but not as a management metric.
Art:
With all the important things that maintenance does to support TPS why doesn’t it get more attention?
With all the important things that maintenance does to support TPS why doesn’t it get more attention?
Tom:
If you do your job well in maintenance you fly under the radar and production gets the credit for a smooth running line. If you don’t do it well then you get a lot of the blame. It is the nature of the job I guess. No one ever really says thanks to maintenance. Anyway from a pure TPS point of view maintenance is a necessary waste to maintain the process but not a value add to the equation in the eyes of most people. Also as I said earlier no academic or external consultant is going to walk through a plant like Kamigo for a couple hours and see all that I have described. With too much to see or understand they’ll get too overwhelmed and distracted by all the other parts of the system and write about that instead. This is just maintenance’s lot in life and probably a hidden advantage for Toyota.
If you do your job well in maintenance you fly under the radar and production gets the credit for a smooth running line. If you don’t do it well then you get a lot of the blame. It is the nature of the job I guess. No one ever really says thanks to maintenance. Anyway from a pure TPS point of view maintenance is a necessary waste to maintain the process but not a value add to the equation in the eyes of most people. Also as I said earlier no academic or external consultant is going to walk through a plant like Kamigo for a couple hours and see all that I have described. With too much to see or understand they’ll get too overwhelmed and distracted by all the other parts of the system and write about that instead. This is just maintenance’s lot in life and probably a hidden advantage for Toyota.
Art:
Thank you for your time and cooperation.
Thank you for your time and cooperation.