IoT for predictive maintenance and the hidden complexity behind its successful, practical, implementation
IoT, Digital Twins, Industry 4.0 have been hot topic for several years already. Vendors tend to make near-magical promises. “Predictive maintenance” is often called a low hanging fruit for such technologies, usually by people who ignore the fundamentals of maintenance. As a result, as many industrial clients know, such projects tend to deliver much less than promised. Often, the technology is working. Instead, customers get blamed for failure. Because they were not mature enough. In reality, the fundamentals, methodologies, data, and management systems were lacking.
This article authored by Siveco China’s Managing Director Bruno Lhopiteau, will try to explain this phenomenon by going through what it takes to establish a plant-wide predictive maintenance program.
Typical approach: from sensors to maybe solving a problem
“Let’s do IoT and see if it solves a problem” is how the common approach could be described. The focus is on sensors, on technology, not on the problems to solve. This approach is taking everything upside down. As a result, most IoT projects stop at pilot stage or focus only on monitoring energy meters: nothing to do with predictive maintenance.
Maintenance fundamentals
Let’s go back to the fundamentals. There are only two main types of maintenance. Predictive is a subtype of preventive maintenance. You usually would want to avoid breakdowns, which is Correct Maintenance. This means doing more Preventive Maintenance. In practice, it is a question of cost and benefit. In any case, in a plant, you will have all different types of maintenance: breakdowns, regular calendar-based maintenance such as inspections, regulatory checks, and so on. And perhaps predictive maintenance. You need to be able to manage all types and they are closely interconnected. Defining what maintenance types will be performed is called the maintenance strategy.
To define the Maintenance strategy and the Preventive Maintenance plan for a machine, you employ a methodology such as FMECA. Failure Modes, Effects and Criticality analysis. If the machine is complex, this is a time-consuming exercise that requires a mix of technical skills, experience with this machine and methodological knowledge.
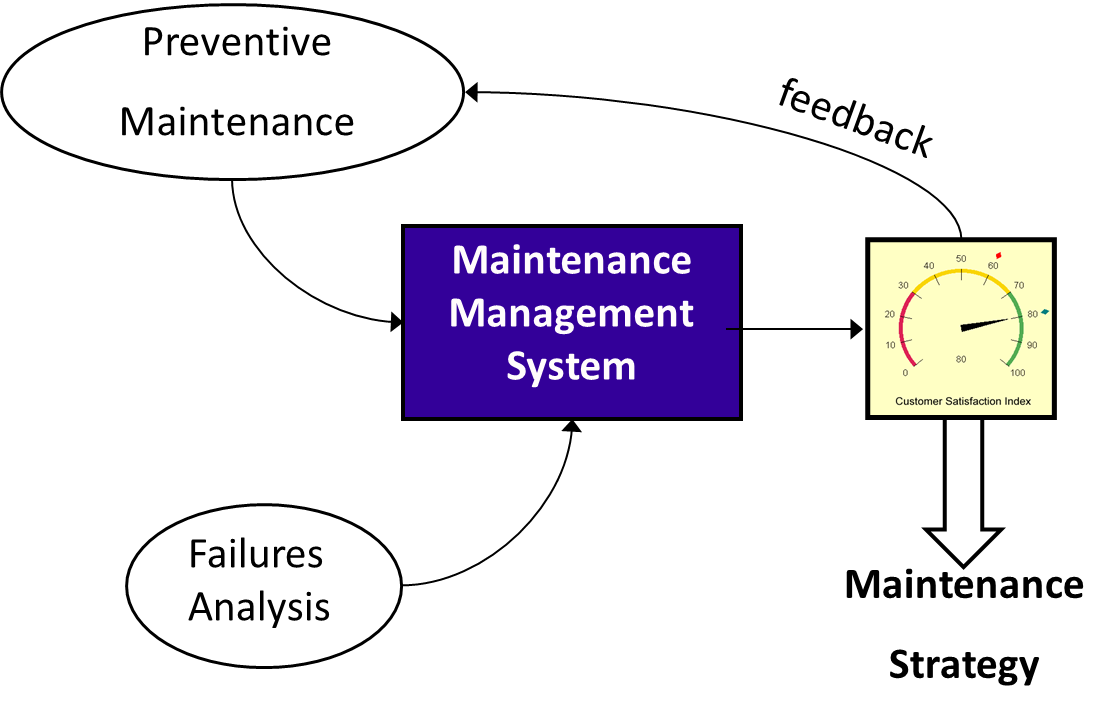
At the plant level, with many machines interconnected in a process, supporting utilities and so on, the process of defining the maintenance strategy is even more challenging. In the manufacturing industry for example, no company can afford to conduct full FMECA on every machines. Instead, a prioritization approach is taken, known as RCM or Reliability Centered Maintenance.
- RCM is a methodology to define your maintenance strategy
- It is a step-by-step approach
- It is based on priorities
- It is based on continuous improvement, meaning once you have defined your maintenance program, you implement it for a while, you collect data on the results and then you loop back to improve it and perhaps move to the second priorities.
This process is very data intensive. It must also be clearly structured. This is why a Computerized Maintenance Management System is needed, essentially a database software designed for this purpose, to manage all aspects of maintenance management. This is Siveco China’s core business of course.
Now you have seen that for FMECA and RCM you need to be able to analyze past failures, their impact, their causes, across all your machines. This means you need to manage your corrective maintenance in the system. Corrective maintenance is not something bad you can ignore while pretending to focus on predictive or even preventive only. It is part of the same puzzle, in fact the most important part, without which there is no RCM even!
Failure analysis is a topic in itself. We won’t really get into it in this article, only to say there are many KPIs. Failures are defined from different angles, which require structured, complex data. This process also requires methodologies, knowledge of the methodology. The IT system to manage such data cannot be improvised.
The ISO 55000 standards give a good overall framework for such a project
To manage the entire system of maintenance management, there is a standard called ISO 55000 Asset Management that gives a good overall framework for such a project. This is of course how Siveco China structures all its projects.
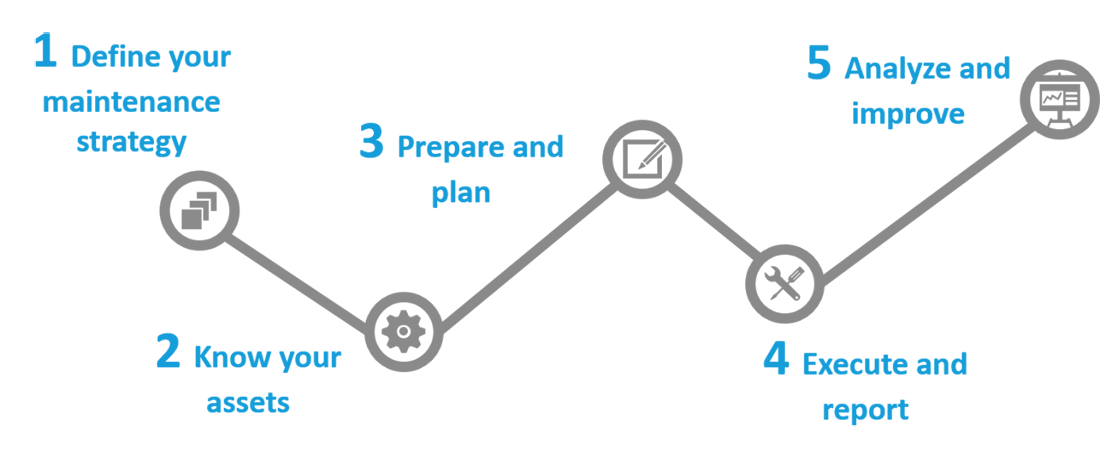
The hidden complexity of Predictive Maintenance is in the underlying system
If you go into the system, the database, templates are very complex animals, not just a list of things to do with a triggering criteria. They also need to be planned and scheduled, a very complex process in itself. To translate that into a management system is a very specialized job, which is why there are so few successful global CMMS suppliers… It is a very narrow field, you cannot improvise yourself as CMMS supplier: our company has been working on this for over 35 years, over 18 of which in China.
The point is: be aware of the hidden complexity behind making predictive maintenance successful.
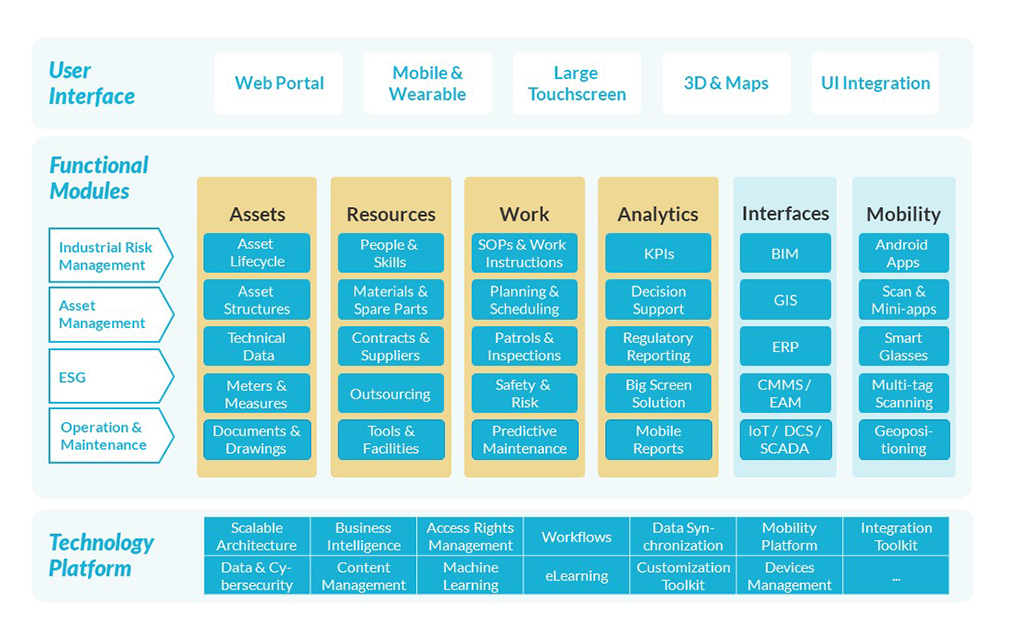
From the management system (CMMS) standpoint, all this industrial know-how needed to tackle this complexity must be taken into account. The system cannot be a custom-made solution just catering to your current needs. Instead, it must be open to allow continuous evolution of the maintenance strategy. This is the very purpose of the system! As new machines, new sensors are installed, as continuous improvement from systematic analysis brings about new maintenance plans (regular tasks with different frequencies, new inspections routines, new monitoring points requiring additional sensors), not to mention the maintenance of the sensors themselves (calibration, preventive maintenance, repairs)!
This is why many IoT projects or “platform development” project fail to achieve the desired benefits.
Read this article to see the application featuring IoT for predictive maintenance with our partner Schaeffler.
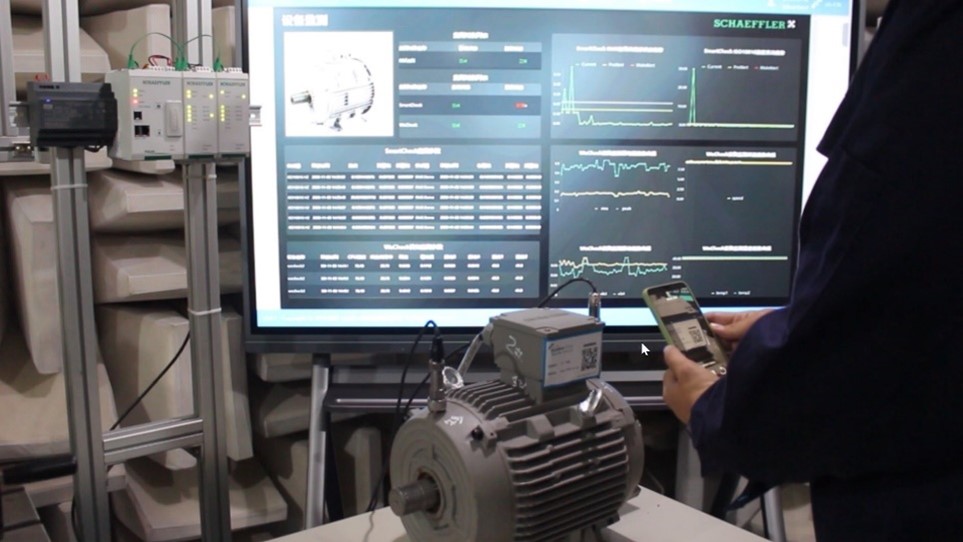
This article talks about the fundamentals and doesn’t go into too much details. Welcome to talk to us if you want to engage into a predictive maintenance program or any maintenance improvement project.
Do not hesitate to reach out to us with questions.