Oil storage achieves continuous maintenance improvement with Siveco
Project Background
Royal Dutch Shell, one of the world’s leading international energy companies, operates in more than 70 countries and regions. In 2018, Shell’s revenue was around $388.4 billion, ranking fifth in Fortune 500. Shell Huabei Group is a joint venture of Shell and local partner Tianjin Food Group, operating a first-phase 60,000 cubic meter product oil storage in Tianjing Nangang Industrial Park, with an annual turnover of 680,000 tons of oil products. After the completion of the second phase, the annual turnover of oil products will reach 3 million tons, and the total project investment will be around 550 million yuan.
Tianjin Shell Oil Storage and Transportation Co., Ltd. is a wholly-owned subsidiary of Shell Huabei Group. Nangang petroleum storage terminals are facilities where petrol and diesel is received, stored and distributed. The stored oil is flammable and explosive: in case an accident such as a fire or an explosion occurs, the impact will be huge, with potentially disastrous outcomes, including loss of life, asset damage, environmental releases, or financial losses. During the construction phase, the top management teams of Shell China and of the Nangang terminal realized the need to implement a system to help build-up the site’s maintenance capability and to manage its assets after operations formally start. Thanks to its management team strong experience on-the-ground in China, Shell experts realized the need for a solution more agile than its large corporate systems, with strong local support and a supplier able to input practical maintenance know-how into the project.
A selection process was initiated, identifying Siveco as a potential supplier, for its rich experience implementing O&M solution for large-scale chemical plants, and more particularly its capability to help clients deploy a CMMS during the construction and commissioning period of a project. Nangang petroleum storage contacted Siveco and both sides conducted a comprehensive discussion on the scope of the project with operational safety as the top priority. In December 2014, Siveco team conducted an initial study on the construction site at Nangang petroleum storage. Very early in the process, the Siveco team made practical recommendations for Nangang petroleum storage to start collect basic equipment data and to ensure the completeness, accuracy, and adequate structuring of this data. This data preparation process would be the first step in establishing a CMMS to support future equipment maintenance and inspection work. The formal selection and tendering process finally led to the selection of Siveco as supplier, after several successful reference visits to other Siveco clients in Tianjin.
Implementation
Once Nangang petroleum storage formally selected Siveco to implement the CMMS, the facilities were under commissioning phase. Siveco immediately mobilized a project team, focused on delivering the CMMS by relying on mature management tools (Coswin 8i) and integrating international standards and advanced management concepts. During this project, Siveco helped Nangang to establish a comprehensive O&M platform, which involved the following activities by the joint project team:
●
Establish the plant technical database and technical documents management system
●
Set up maintenance standards and safe operations system
●
Build up a maintenance historical knowledge database for technical analysis and diagnosis
●
Define and implement preventive maintenance for the entire facility
From the onset, both teams expressed great concern about the importance of data collection in the O&M system implementation. Indeed, the traditional IT vendors’ data collection method consists only in providing standard data collection templates (Excel forms) and let end-users collect data by themselves. This ultimately leads to heavy additional workload for an already busy maintenance team before start-up, delays in data preparation and too often useless data, as the end-users had never experienced such process before and did not realize how the data would be used in the CMMS. Instead, Siveco brought maintenance management coaching services, established a detailed data collection plan for Nangang and guided site engineers throughout the process.
How to scientifically rate the criticality of equipment was a major challenge for the Nangang petroleum storage team. Siveco proposed to determine the criticality of the equipment through three aspects. The first is the impact on safety and environment, the second on production and the third is the probability of equipment failures. In addition to this classification based on criticality, the structural relationships between areas, processes, equipment, components, etc. was established. Nangang team divided the facilities in 16 system areas according to Siveco’s recommendations, such as: gasoline tank area, gasoline pump area, additive area, emergency generator room, etc.
In order for repair personnel to find faulty equipment quickly, Siveco recommended Nangang petroleum storage to use graphical navigation in the CMMS to locate the equipment intuitively, and then review the equipment’s historical problems, check past preventive work records, and analyze the equipment’s symptoms. All key equipment preventive work guidelines were prepared by the maintenance planner and supervisors and imported to the system, so that work orders are released automatically when the conditions are met. The work of all personnel is clearly reflected in the dashboard on the front page of the system, such as: unassigned work orders, delayed and unfinished preventive maintenance work, etc.
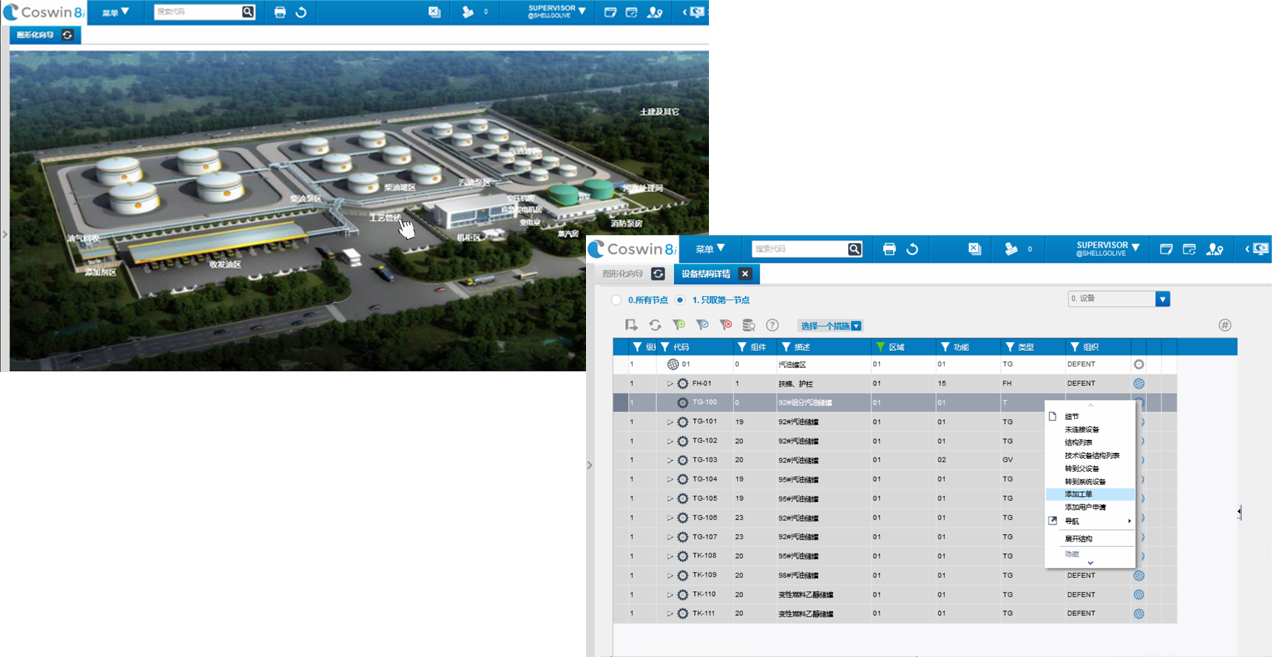
Nangang’s main CMMS dashboard featuring graphical navigation, a concept available in all Siveco products. More than a beautiful image, the diagrams allows users to drill-down to selected facilities, open related screens, execute actions, directly from the diagram
Finally, Nangang petroleum storage team input all spare parts into the system and set up the safety stock levels. If the actual inventory of spare parts goes below the safety level, the system will alert the warehouse administrator to purchase. Moreover, maintenance supervisors can also use the reporting tool to compare the forecasted consumption of spare parts in the coming month with the current inventory and decide whether to purchase spare parts in advance.
Benefits
The Smart O&M project implemented by Siveco for Nangang petroleum storage has entered its fifth year of operation. Making full use of the maintenance management system put in place before startup, the maintenance team of Nangang terminal insists on the maintenance summary meeting at the end of each month and analyzes the work situation of the month by using the standard report defined by Siveco. Multiple data indicators, including: work order completion ratio, top five failure causes, and top five repair measures, etc. have become the main reference for reviewing the maintenance team work, and it has truly helped Nangang team to continuously improve maintenance work.
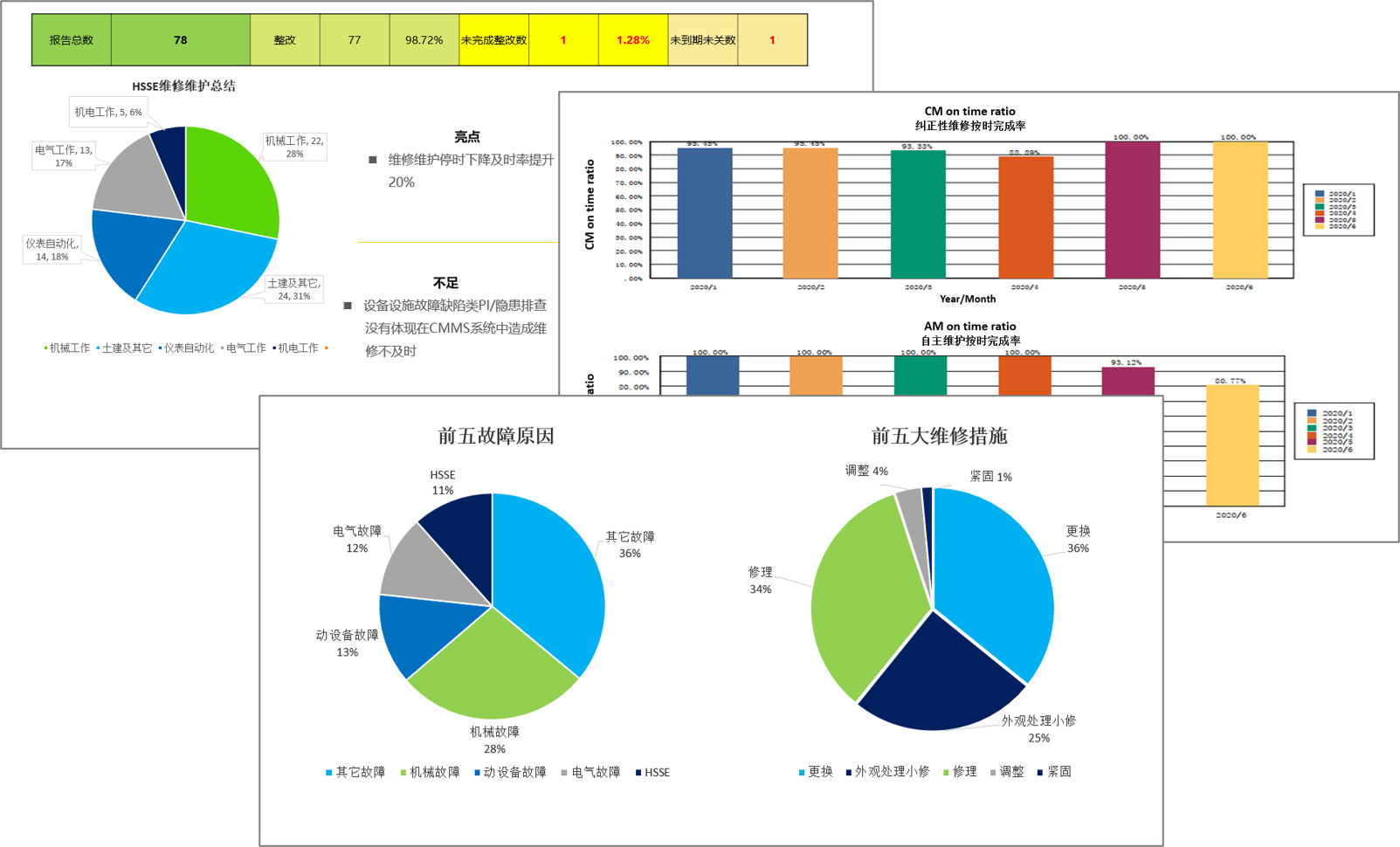
In addition, according to the annual follow-up cumulated downtime tracking, the downtime of Nangang petroleum storage has shown a significant downward trend, proving that the maintenance team strictly follow the defined maintenance strategy, which can effectively reduce the downtime and ensure the normal operation of the enterprise.
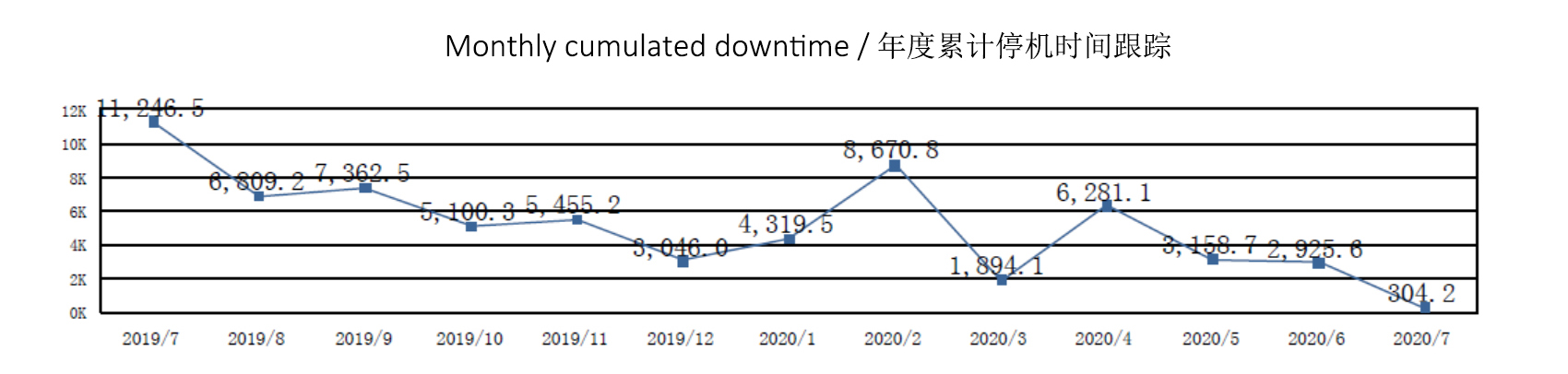
(Note: The graph shows a spike during the COVID-19 crisis, when work orders could not be closed on time, resulting in higher downtime in February)
According to the Production Process Manager of Nangang petroleum storage: “Years of cooperation with Siveco has helped us establish a perfect equipment management system. We have fully applied Coswin to the daily maintenance work. Over the years, we have established a complete technical database and the equipment conditions are clear. With the joint efforts of both sides, the maintenance management of Nangang petroleum storage has been continuously improved.”