How bluebee® supports Jiangsu Sino French Water Smart O&M in the implementation of best practices
This article is based on a presentation by Jiangsu Sino French Water representatives during this Customer Sharing Event in Changshu.
Project introduction
Since the establishment of the Supply Division of Jiangsu Sino-French Water company many years ago, thanks to the leading environmental technology and scientific management experience of Jiangsu Sino-French Water and the its shareholder Suez Group in the environmental protection market, the company developed specialized and refined equipment operation and maintenance concepts and systems. However, these systems often could not be fully integrated with the actual work. The company manages water plants distributed in different towns. In addition, the maintenance and inspection personnel headcount is limited, while the workload is heavy, and its management difficult. When maintenance and inspection work is managed on paper, efficiency and accuracy remains low, traceability is impossible. The lack of accurate data also makes it difficult to provide effective analysis reports. These were the typical problems faced by the management team, which needed to be resolved urgently.
O&M needs
- Create repair and inspection work orders to achieve paperless management.
- Receive and manage work orders on the mobile devices.
- NFC tags (use NFC tags to ensure presence on-site)
- Trace relevant historical records and customization of technical data.
The implementation and execution of the bluebee® mobile solution
- In this project, water supply company adopted the latest technology of Siveco’s Smart O&M solutions including the mobile app for maintenance management. All technical data, work orders, work instructions and reports, etc. are stored in the back-office system.
- The system generates work tasks or work orders from predefined strategy, plans and frequencies. The work orders will be displayed on the user’s PC dashboard, according to the specified date, which is very intuitive. Work orders are assigned automatically to the mobile phones of engineers and operators, connected through WiFi or 4G, which, unlike the usual paper-based process, is now fast and convenient. Mobile phone user conduct their tasks under the guidance of predefined work instructions.
- If a fault or problem is found onsite, it can be directly reported for corrective action in a timely manner. In the end, the work completed on the mobile phone is automatically transferred back to the central system, with multimedia recording (such as voice, text and small video as needed), ensuring a true record of the work done. Thanks to this closed-loop approach, the company’s O&M and inspection work can be completely managed, with full traceability of the work, and convenient query and analysis.
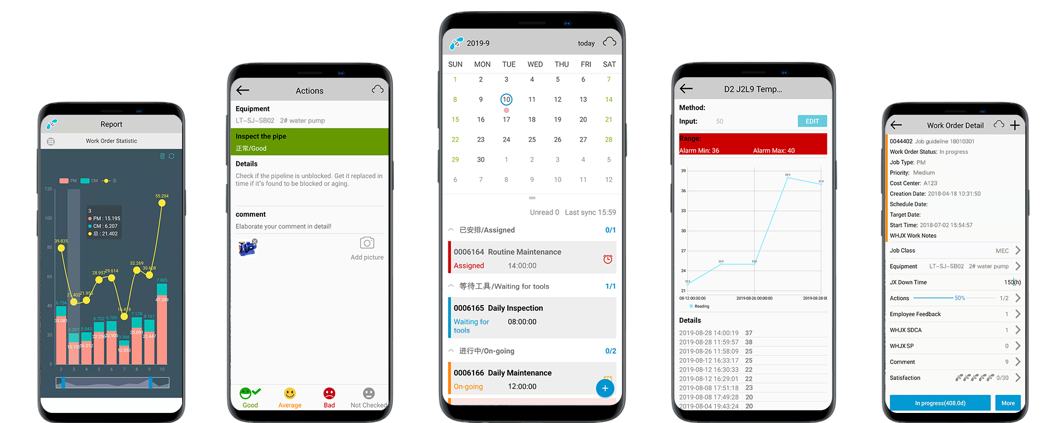
According to the company’s guidelines and Siveco China’s recommendations, standardized equipment asset coding, inspection procedures, work order statuses, and report metrics (KPIs) have been established, bridging the gap between theory and practice.
Smart O&M results
Adopting Siveco’s complete solution based on the concept of Smart Operation and Maintenance, the system mainly consists of two parts:
- The Coswin back-office management system, on a Browser/Server, web-based architecture, and the bluebee® mobile app running on Android smartphones.
- Through a dedicated dashboard on the system’s homepage, users can track the current status of all work orders and manage them; by establishing a databased for the plants, the system helps the equipment department and the water treatment plants’ personnel to manage their equipment, making it easy to create, repair, and maintain equipment. In addition, after establishing a preventive maintenance plan, the system helps schedule work orders and track their execution.
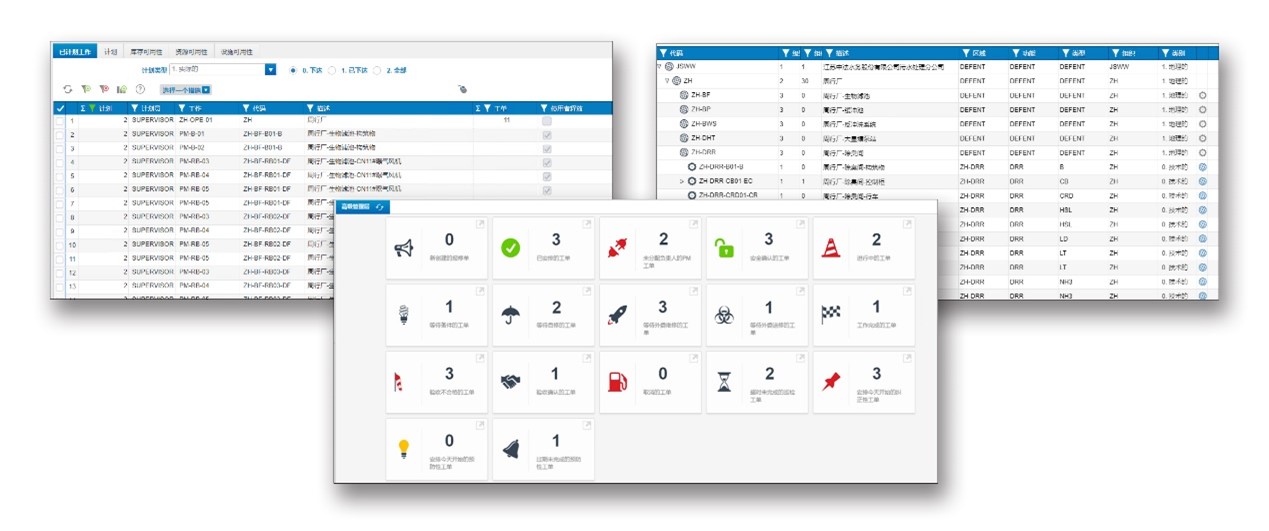
bluebee® is a unique tool designed “for the worker of tomorrow” to capture information from the field and to enforce best practices.
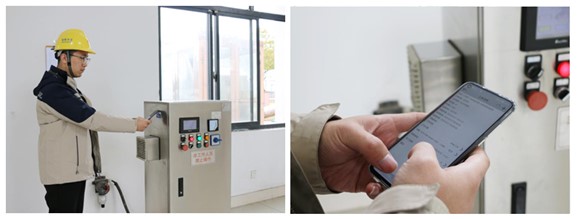
- According to the planned inspection tasks and workers shifts, the system will automatically generate inspection work orders every day, the mobile app will receive the work orders, with a reminder message pushed to the inspectors’ mobile phones.
- Through the paperless work model and clear work processes, on-site work efficiency has been greatly improved. Data is synchronized to the database in time to ensure backup and data analysis. On-site scanning of equipment NFC tags ensures that employees are actually there and have completed their work orders, which also plays an effective supervisory role.
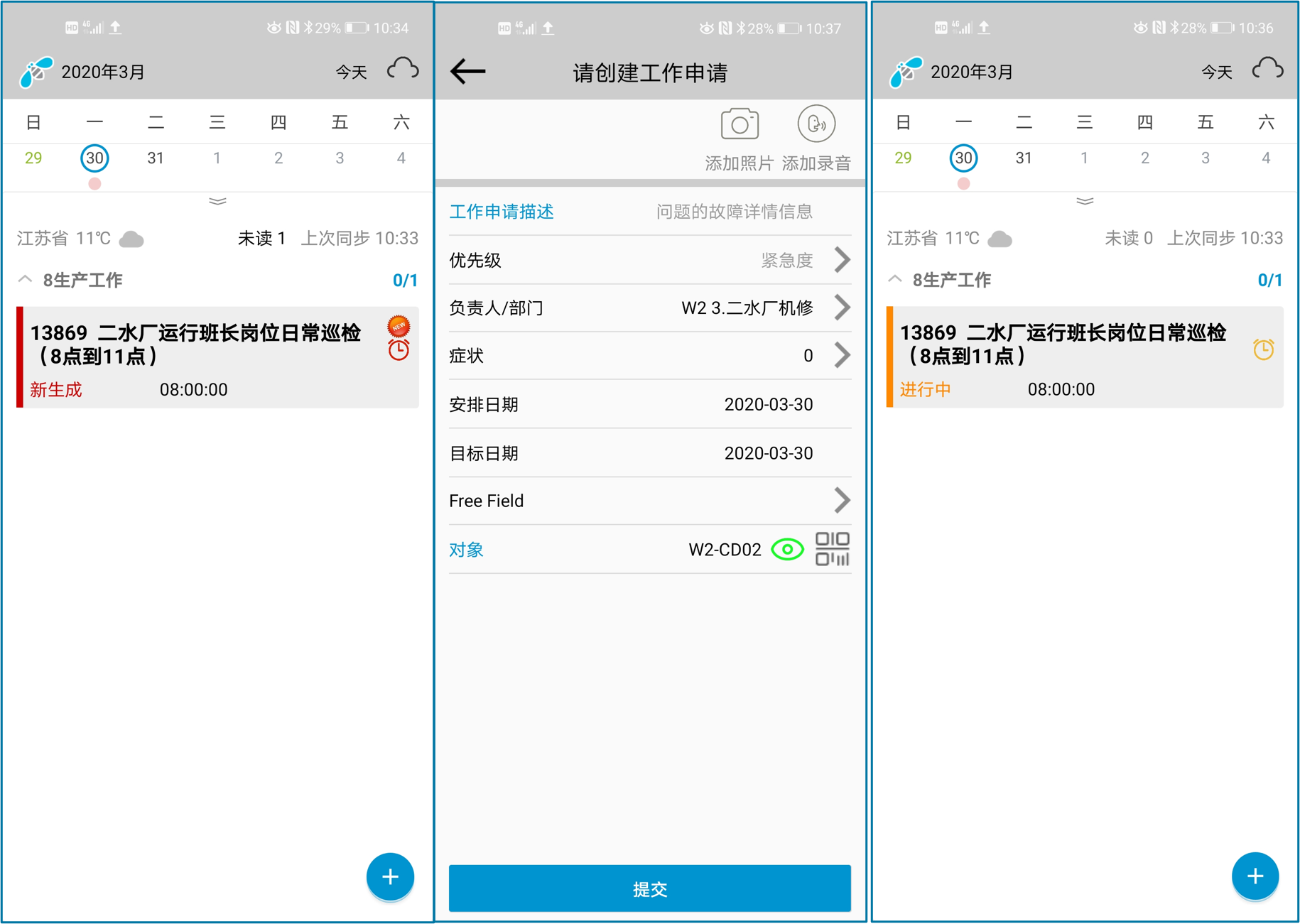
- Relying on the strong support and participation of the company’s management and users, as well as Siveco’s rich experience in water and environmental protection, with mature and stable software products, the Smart O&M project was delivered and put into use in only two months. At present, the various system functions meet the needs of the water supply company and have solved the various problems from technical data acquisition, work execution management and report analysis.
- At present, the water supply company has used the Smart Operation & Maintenance + bluebee® mobile inspection system to carry out their daily maintenance management, effectively integrating data through Information Technology, building a data platform, which will provide a huge boost to the company’s cost-effectiveness.
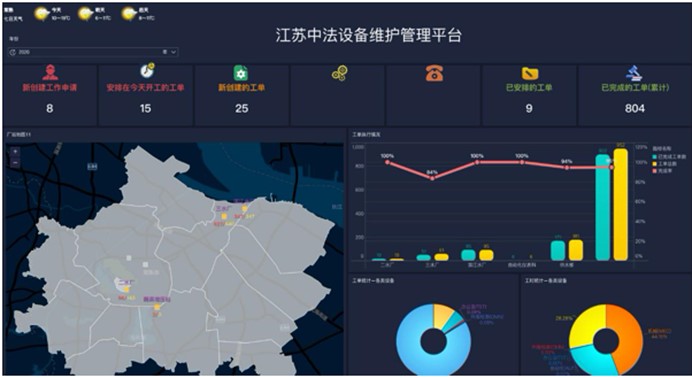
Utilizing the data analysis system, a comprehensive analysis of the data related to inspection work is performed. Through these reports, a visual representation of the execution status of inspection work is obtained, as shown here:
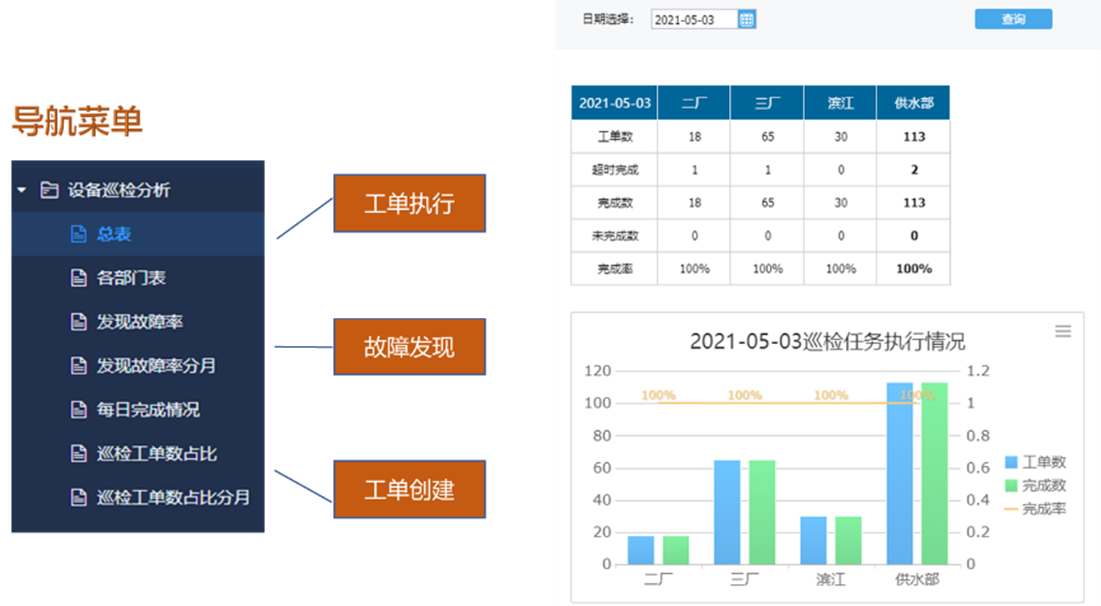
Project summary
Both parties conducted in-depth discussions regarding the Smart Operation and Maintenance project. Through repeated communication all the way to final approval, Siveco China ultimately implemented a complete Smart O&M solution that meets the needs of the water supply company. The project helped establish and achieve the following benefits:
- Based on ISO 55000 asset management consulting services, the Core Model for the Smart O&M and inspection system was established. This model will be applicable to future acquisitions of new-built water plants of the company, and has a wide range of practical applications;
- Established a standardized equipment and asset technical database, covering coding rules, naming rules, asset identification, equipment and spare parts data, failure information, preventive maintenance plans, etc.;
- Using the combination of the back-end management system and the mobile devices to organically integrate Operation and Maintenance data, daily work, analysis reports, etc., to basically realize a paperless and high-efficiency working mechanism;
- Through the implementation of mobile solutions, an effective work execution and feedback mechanism has been established, from which work done is accurately reported, providing a strong basis for decision support;
- Decision support: definition and display of Key Performance Indicators for O&M management. The report display is very friendly and can also be displayed on a larger BI platform.