Hazardous waste incineration plant optimizes plant inspections with bluebee® mobile solution
The case study was nominated for the 2015 Suez Innovation Trophies.
SCIP SITA Waste Services (“SCIP SITA”), a subsidiary of SITA Waste Services, operates a Hazardous Waste Incineration Plant (“HWIP”) in Shanghai Chemical Industrial Park (“SCIP”) since 2006. It has a successful record of treating a wide range of hazardous waste, in full compliance with applicable Chinese regulation. The current facility consists of two incinerators with a total capacity of 60,000 tons per year. The plant is becoming one of the largest HWIP in the world with the extension of a third line.
Ensuring and optimizing the high availability of equipment is critical for the continuing success of the plant and its coming extension. The main way to ensure it is through an excellent preventive maintenance by checking and measuring frequently the critical equipment and also doing appropriate replacement on some parts, based on scientific and on-site knowledge.
Since start-up, the Maintenance department uses a Computerized Maintenance Management System (CMMS) to record and create all maintenance work, including preventive maintenance and overhauls. Inspections however were set by each engineer using a paper-based process which didn’t allow analysis or consistent tracking of findings and measurements. Inspection quality was impossible to measure or review.
The bluebee® project
The bluebee® project aim was to improve the quality of maintenance by standardizing the inspection content (such as routine and daily inspection) and increasing the reliability of data coming from the field. The use of bluebee® was to eliminate the traditional paper work orders from the CMMS system and help establishing a real inspection database for diagnosis and performance analysis.
The pilot project started in March 2013 and went through several optimization phases. Due to the plant hazardous working environment, explosion-proof ATEX Zone 2 mobiles were selected, supplied by Bartec, a Siveco Value Added Partner.

Picture of bluebee® PDA, with a QR code tag
The inspection process
The plant operation condition is constantly monitored online by the plant supervision and control system. Another level of monitoring is performed through onsite inspections by the operation and maintenance team. Many rely on the five human senses: vision, hearing, touch, smell… only taste is limited to the company canteen and is not used to detect problems. Other inspections rely on using specific tools or instruments, including more complex vibration measurement, X-ray test or material analysis. This sometimes inconsistent and hard to optimize paper process was replaced by bluebee® mobile, integrated with the existing CMMS.
A total of 102 inspection were defined initially. The frequency of inspections vary, from daily or weekly routine, to less frequent schedules, according to the criticality of the equipment and the probability of degradation or failure.
Each equipment is labelled with a unique QR code, with its name and code: as part of the project, a total 1,116 QR codes have been installed in the plant (159 for mechanical, 145 for electrical and 812 for instruments).
Inspection workload is automatically balanced by the system, optimizing the daily schedules of all technicians. Each morning, each technician downloads his work orders of the day and prepares for his inspection route accordingly. There is no need to bring any paper on site. After scanning the equipment QR code with his mobile, the user inputs related data. The action of scanning a QR code makes the process more reliable in many aspects: no loss of information as with paper notes, true information collected at the source, easy to check the regularity and content of work, etc. When the technician comes back to his office, he only needs to launch the synchronization process (using the office Wifi or USB cable to computer) and can focus on something else. Everyone has direct access to the data, there is no need any more for data input, sending emails, etc. The automatic input make analysis easier, thanks to the back-office reporting system (part of the CMMS).
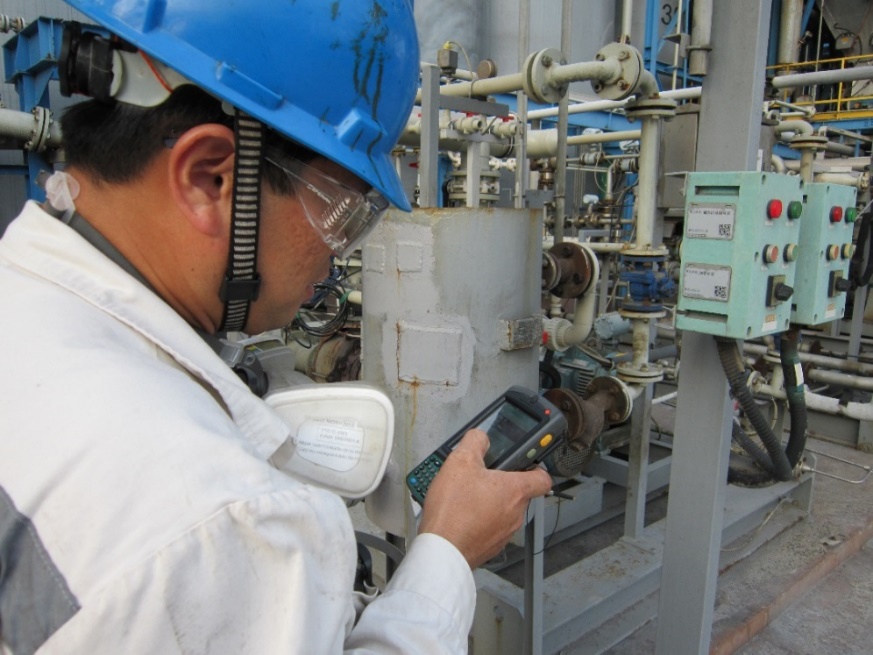
On site utilization
The results obtained
According to Baptiste Garro, Planning Engineer:
“The project makes inspection and preventive maintenance more efficient, reliable and easier. Data from the field (reports, measurements) is now available in the same central database, allowing in-depth analysis and better support on decisions. The technicians benefit from higher motivation in their work, thanks to this technology.
Although there are direct efficiency improvements (less time spend reporting on paper, compiling data or looking for missing data), the main benefit will be indirect: less problems, improved thinking on risks and losses, and scientifically taken decisions.
Finally, it directly helps the detection of minor and major malfunctions that can lead to a breakdown. Each day when a breakdown is avoided is a day without safety or environmental issues. It also will save huge direct and indirect costs from avoided breakdown.”
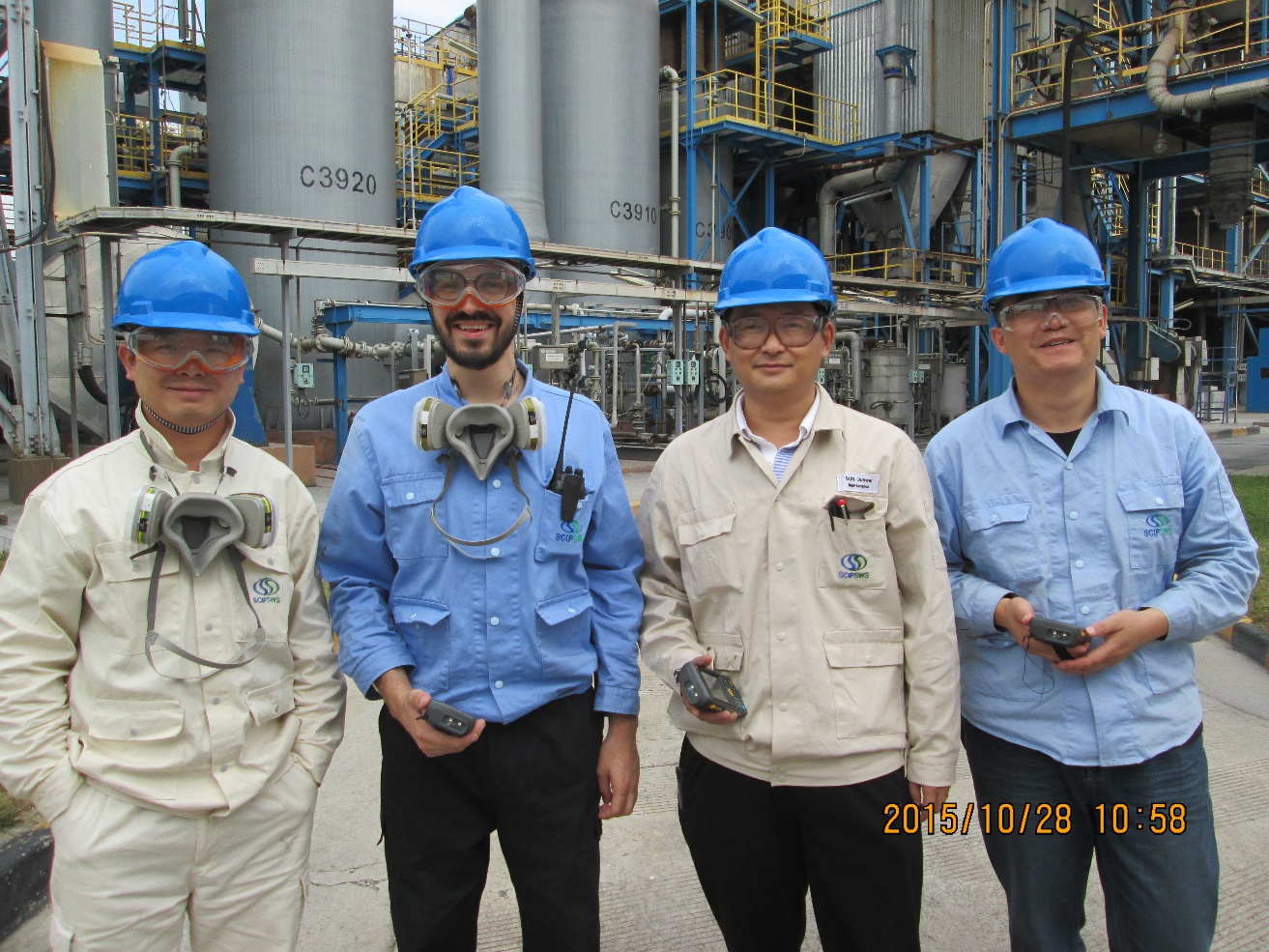
Picture of the bluebee® Team, from left to right: Thomas Tao, Baptiste Garro, Sun Junwei and Xu Yong