The Siveco maintenance assessment
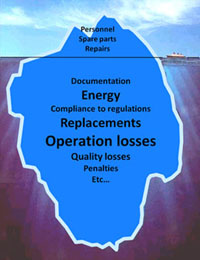
After over 20 years running maintenance assessments worldwide, Siveco has shown that poor maintenance can drag down profits by up to 40%. According to benchmarks in manufacturing, even the world’s very best plants can still deliver up to 11% more in bottom line profits.
Based on a unique experience combining both industrial maintenance expertise and consulting project in China, Siveco has developed a proven maintenance assessment methodology: an approach that has delivered results for many facility owners in China.
Maintenance improvement is often not about cutting budgets, but about improving effectiveness: indeed our studies show that you can save more than 10 times more money by acting on indirect costs and losses, i.e. the impact of maintenance on the business. But: where and how? This is the question we can answer.
The assessments are designed to answer such questions as:
• Where and what are you excess costs and losses?
• How to get more ROI from your CMMS/EAM without new investment?
• Identify maintenance improvements and how to deliver them!
• How to get more ROI from your CMMS/EAM without new investment?
• Identify maintenance improvements and how to deliver them!
The Siveco assessment
Principles
Our assessments are always tailor-made to each customer’s specific case. We can however distinguish three types of assessments:
• Maintenance organization assessment – focus on the organization and its processes
• Maintenance system (CMMS/EAM) assessment – focus on your systems and their utilization
• Condition assessment – focus on the equipment itself and its condition
• Maintenance system (CMMS/EAM) assessment – focus on your systems and their utilization
• Condition assessment – focus on the equipment itself and its condition
Often our assessments combine components from all three types above to answer the key questions:
1. Where do you stand?
• What is your situation now?
• What are you getting for each RMB you spend on maintenance?
• What are you getting for each RMB you spend on maintenance?
2. What could you gain?
• What direct costs could easily be cut?
• What would performance improvements deliver to the bottom line?
• How much more flexible and “fit” for modern business would you become with world class maintenance?
• What would performance improvements deliver to the bottom line?
• How much more flexible and “fit” for modern business would you become with world class maintenance?
3. How can you achieve your goals?
• We provide action plans
• Knowledge-base of best maintenance practice
• Tools and services for implementing action plans
• Knowledge-base of best maintenance practice
• Tools and services for implementing action plans
Our working approach
Siveco assessments always involve active cooperation between the customer’s and Siveco teams, based on the following working principles:
• Dedicated expert full time on your project
• An on-site action focused on your main requirements, driven by a Siveco project manager, assisted by maintenance engineers
• A partnership approach of our work: we recommend efficient, long-term solutions, and prepare your teams in a self-working organization
• An on-site action focused on your main requirements, driven by a Siveco project manager, assisted by maintenance engineers
• A partnership approach of our work: we recommend efficient, long-term solutions, and prepare your teams in a self-working organization
Confidentiality: Siveco will sign Non-Disclosure Agreements as required by customer.
Safety is non-negotiable: all Siveco employees will wear the necessary personal protection equipment when working on site.
Note that all Siveco projects are offered on a fixed price basis for the scope defined in an agreement.
Methodology
The Siveco assessments are based on a standard assessment methodology that we have used in many projects across China, and on the professional expertise of our team members, always capable to adapt and improvise if needed.
Whenever applicable, European and IEC standards are used (alternatively, customer can request specific standards to be applied).
Assessments always comprise three main phases as shown in the figure:
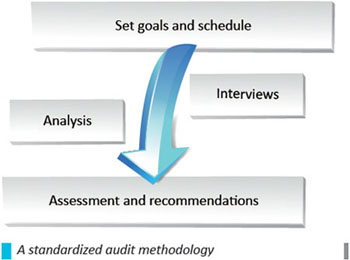
Benchmarking
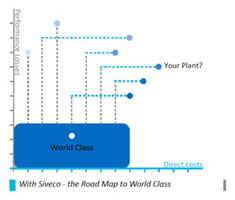
Benchmarking with international standards and other companies plays an important role in all Siveco assessments.
Our growing customers’ database in China and abroad allows us to benchmark your operations to other plants in similar or different industries. We also run multisite assessments with internal benchmarking between your own sites.
A strong basis for our maintenance benchmarking in China has been the annual “Maintenance in China” survey that Siveco has run in association with the Sino-European School of Technology of Shanghai University and the European Chambers of Commerce since 2006, covering over 1,500 multinationals in the country.
Deliverables
The main deliverables for the assessment are:
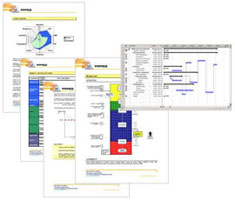
• Detailed assessment report (completed Excel document and analysis report, which would include, depending on the scope of assessment, pictures, work processes maps, etc.)
• Recommendation report with related action plan. Recommendation report could include ROI estimates (if financial data was made available to Siveco).
• Optionally, the above data and action plans in advanced electronic format (CMMS database) with possible follow-up services.
• Recommendation report with related action plan. Recommendation report could include ROI estimates (if financial data was made available to Siveco).
• Optionally, the above data and action plans in advanced electronic format (CMMS database) with possible follow-up services.
The report with our recommendations will be presented to the management team at the end of the project, after which discussions will take place. A final conclusion report will be drafted at the end of the session.
Siveco China has experience conducting assessments in all three target segments: Facility Management (property owners and FM suppliers), Industry (factories in various industry, process or discrete manufacturing) and Infrastructures. Nowadays, in addition to independent assessments, all our projects include a start-up assessment and our “enhanced maintenance contracts” also utilize our assessment practice. The accumulated experience of our team (some of our team members have been active in this field since 1997) is unparalleled in China.