How to make meter reading a true value-added process with your CMMS
Most industries rely on meter readings, at the very least to measure the consumption of electricity and water (utility meters) but also to follow-up production (cycles, running hours, quantity produced, and other operation meters). Meter readings are relevant to maintenance in two main cases:
- Upon reaching a certain value (or at a certain interval of value), a preventive maintenance task should be performed. This could for example be a lubrication job every 1,000 cycles or a part replacement based on actual operating hours (as opposed to a fixed time period); electricity meters would also be inspected on a regular basis and replaced over longer intervals.
- The meter value is useful for performance calculations. For example the computation of OEE (Overall Equipment Efficiency), a performance indicator commonly used in the process industry, requires input of production quantities and durations for the various manufacturing processes.
Measurements share similar feature with meters but differ by the nature of their values i.e. measurements can go up and down, while meters only go up until they are reset. Almost all CMMS available on the market today can handle both meters and measurement points, in one way or another. Our CMMS COSWIN provides extensive facilities to manage meters, most notably in terms of using the value not only to trigger a work order (a seemingly useful feature, in fact just a reminder) but, more importantly, to actually forecast the next work order date. This forecasting capability in COSWIN enables a true planning of corresponding resources – such as manpower, parts, tools, workshop space etc. – knowing that, based on industry statistics, planned work is approximately 50% more efficient than unplanned work. As obvious as the above statement may sounds, most other CMMS still use meters to automatically generate work orders when they are due – thus losing all the benefits of planning normally associated with meter-based maintenance…
This article will deal with a specific but critical part of the process: the reporting of meter values or measurements in the CMMS. This is how the process usually goes:
- A technician starts his round, reading meters and recording values with pen and paper (usually in a pre-printed form showing meter tag numbers, with empty space to write down the value and some comments). The pre-requisite is that meters should have been tagged for easy identification – or can be identified by their type and location (“electrical meter in room 12”). The technician may then deal with other issues – technical problem with the meter, other checks and repairs etc.
- When his round is over, he will go back to his base and either input data by himself in the CMMS or hand over this task to someone else (a “CMMS secretary”). This clerical task is often delayed, perhaps done on a weekly basis or sometimes irregularly. On the CMMS side, the input typically consists in entering or selecting the meter number (often in a very long list, which can then be filtered by area/equipment/process), to finally key in the value.
- While it is relatively simple to so do with one meter value, it becomes very tedious when a large number of meter values have to be entered, as is usually the case. In addition to being tedious, this entire process is prone to errors at several points: the taking down of meter value on paper, reading of the written value and the manual input in the CMMS. In COSWIN the input process can be made slightly easier through the use of diagrams.
Note that there is very little value added in this process, hence its delegation to junior engineers or clerks without understanding of the importance and underlying usage of this data. More often than not, the original purpose of the job is forgotten, becoming a purely administrative task. As triggering of work orders from the CMMS is mostly useless (no planning), the only output for this entire process is often limited to: a list of work to be done immediately and a historical record of values available for later study (perhaps with trending).
Knowing the limitation of the manual process described above, automatic meter reading is one of the solutions available, with values read directly into for example a SCADA system, then passed onto the CMMS through an interface. Siveco China has also worked with technology partners providing remote reading capability through the mobile network (for example to collect meter readings and measures in pumping stations over a large are in a water distribution network). This however requires significant investments in hardware and, for large infrastructures, may take several years to implement: it doesn’t solve the problem at hand and manual reading by a technician will continue to be a daily reality.
Apart from the actual meter reading, other – more value-adding – parts of the process have been left out, without support from the CMMS: assessing whether or not the value is normal, conducting further checks if the value if abnormal, diagnosing faults (meter problem or other), reporting work done (reset of meter, replacement of damaged part etc.) or requesting further action (meter replacement etc.).
From Siveco China’s point of view, technology aims at removing complexity and let maintenance people focus on improvement. Siveco China has developed mobile solutions based on very intuitive user interfaces and running on Android mobile phones, as well as in WeChat. The solution, known as bluebee®, is further declined into several role-based applications. With the “Inspector” application, the complex administrative-driven scenario described above is totally transformed:
- The technician starts his round and read the first meter. He inputs meter tags, followed by its value directly in the device (in less than 30 seconds: total 3 clicks and 2 value inputs with the phone numerical keyboard).
- Meters or measurement points may of course be tagged with QR code, NFC and RFID chips for easier identification by mobile devices equipped with these technologies, thus removing the need to manually input meter tag. The tagging process itself may take time (well managed, it can be finished in one meter reading cycle, i.e. the period required for all meters to be read) but it is inexpensive and doesn’t change the overall process (meter equipped with device-readable tags are scanned, while others have their tag number keyed in manually).
- Upon inputting the value, the technician can view previous records and get immediate feedback on an abnormal reading. He can then either correct a reading mistake (which can always happen) or assess the nature of the problem – meter problem, sensor problem, abnormal value leading to further maintenance action. He can also immediately report other faults (e.g. a broken display cover) with a photo or voice record, access the knowledge base (has a similar fault occurred before, what were its cause and remedial action taken?) and, guess what… he can make a phone call, for example to talk to an expert at headquarters. We, at Siveco China, are firm believers in the use of no-nonsense old-fashioned technologies, in total harmony with the latest gimmicks.
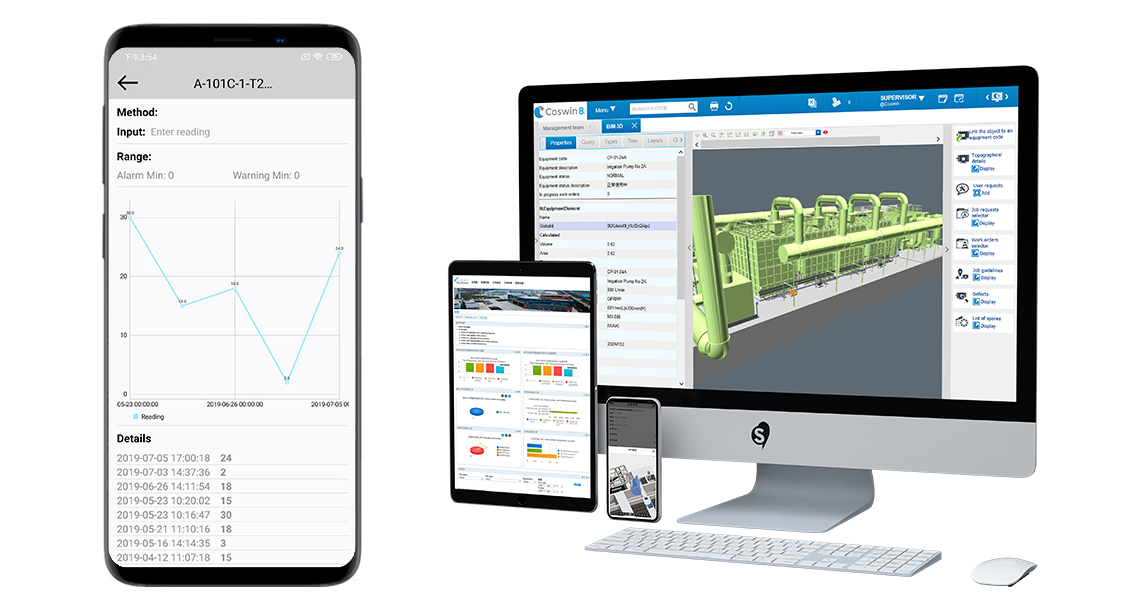
The scenario above is a perfect example of how inexpensive technologies can greatly simplify the utilization of the CMMS and help users focus on value-added improvement processes rather than admin. Immediate ROI are obtained by a reallocating human resources to non-clerical tasks or to other job (the “CMMS secretary” – usually a young engineers who could be better utilized), by reducing the number of errors and their consequences (missed jobs, rework). As in all CMMS applications in China, most ROI however will derive from maintenance improvements (better diagnosis by direct access to the knowledge base from the field).
bluebee® and other Siveco China mobile solutions (see our website for details) are compatible not only with COSWIN but also with other CMMS/EAM or Plant Maintenance module of your ERP, adding tremendous value to the existing system. All development is performed at our Shanghai R&D unit, allowing us to efficiently tailor our application to customers’ specific needs and to provide quick local support. For more details, contact us at info@sivecochina.com.