Wake-up from the dream of IoT & AI-enabled predictive maintenance: reality is even better!
The article authored by Siveco China consultants was published simultaneously in Vogel’s Chemical Industry Website and in Digital Business Times.
The broken promise
Long-time participants in the industrial maintenance market know that predictive maintenance has been a hot topic since at least the 1980s. In recent years, a variety of new players has claimed to revolutionize predictive maintenance using IoT and AI. As a result, the subject of maintenance, previously considered tedious, complex and… unprofitable as a business, has become hot!
At the World Manufacturing Convention in Hefei mid-2018, global luminaries waxed lyrical about predictive maintenance being the “low-hanging fruit of Smart Manufacturing”. Most notable however was the fact than none of the speakers was able to provide any concrete example of such a project. Not one. Instead, the usual media stories of robots, artificial intelligence and smart glasses.
As of early 2020, the big overhype wave appears to be receding. Many revolutionary startups have disappeared. Many proof-of-concept projects have failed. A depressing state of affairs after so many promises? Not so! It is time for technology innovators to make use of the wisdom and experience accumulated by maintenance practitioners. It is time for the maintenance man, long hidden in his dirty workshop, to take center stage!
Seeking truth from facts
At the Intelligent Process Manufacturing Summit in Hangzhou last summer, a German automation vendor showcased a predictive maintenance case study, conveniently without naming the client and without presenting any data: the pilot had been completed, but the question as to whether or not to deploy the system was yet unanswered. Someone in the audience asked why. The answer: “Because we have realized that the client’s business processes were not digitalized enough”. Running a pilot with state-of-the-art technology must have been a very expensive way to find out this simple truth… Here we encounter a very common phenomenon: big technology and consulting firms blame failure on their clients’ lack of maturity.
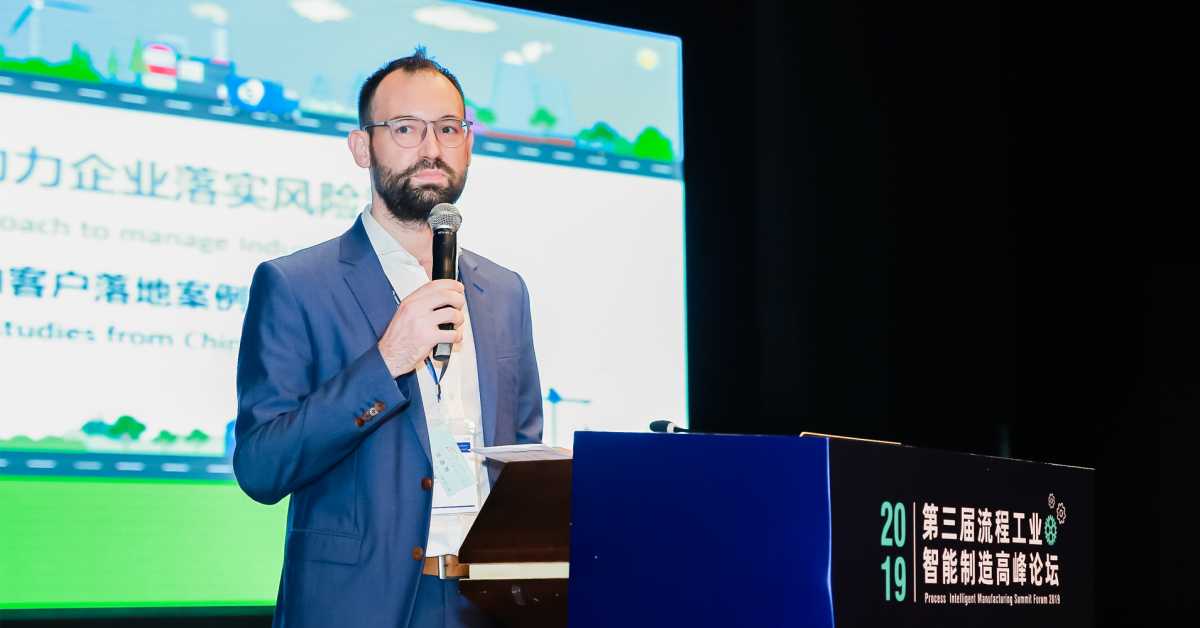
Siveco COO Guillaume Gimonet sharing on practical maintenance improvement experience at the Process Intelligent Manufacturing Summit 2019
A fundamental truth emerges: no technological shift towards predictive maintenance will be possible without a minimum of digitalization of business processes. A simple, yet well-structured, database of assets, maintenance plans, maintenance workflows, key performance metrics to support decisions. In most organizations, and in the anonymous client’s story above, this information is either absent or scattered across databases, Excel sheets and papers, across departments.
To achieve this takes experience and expert knowledge, not quasi-magical apps and fancy tech. In particular to determine what is “right”, what is “useful”, what to computerize as a priority and how to do it efficiently. For predictive maintenance, “right data” is indeed better than “big data”. What data is “right” and “useful” has to be viewed from the perspective of the company’s maintenance strategy.
The theoretical magic weapon
“Without revolutionary theory there can be no revolutionary movement” said Lenin. The theoretical basis is the maintenance strategy! Innovative technologies must serve the strategic maintenance needs, such as reducing downtime in a manufacturing process, preventing safety risks, etc. This is best done by people already equipped with the necessary theory and practice, people who can help formulate the maintenance strategy.
The ISO 55000 Asset Management (known in China as GB/T 33172), provide a robust theoretical framework. A “Core Model” will describes how to digitize asset data and related work processes to support the strategy.
Maintenance is indeed a “low hanging” fruit of industrial improvement in China, as it was seldom a priority before. By benchmarking against ISO 55000 and optimizing management decisions, industrial plants can obtain considerable performance improvement. Cutting edge technology is the cherry on the cake!
Yet, in the 4.0 era, the motivating factor of Smart Technologies should not be underestimated! In most company, funds are available for such initiatives (we call it “Smart Money”!) which would never be available for traditional maintenance improvement projects. Maintenance professionals: you should not be shy to tap into this opportunity to improve your company’s performance, to improve your own skills and to advance your career! It is time for the maintenance man to shine, in a world where robotized, automated production lines need him more than ever before! The maintenance man, long underestimated, can save the day in the era of Industry 4.0!