Smart O&M’s role in the energy transition: optimizing O&M from the construction phase in new energy projects
A significant untapped potential in the ongoing energy transition
Experience in the energy industry has shown that paying attention reliability and maintainability earlier in the project helps reduce future Operation & Maintenance costs.
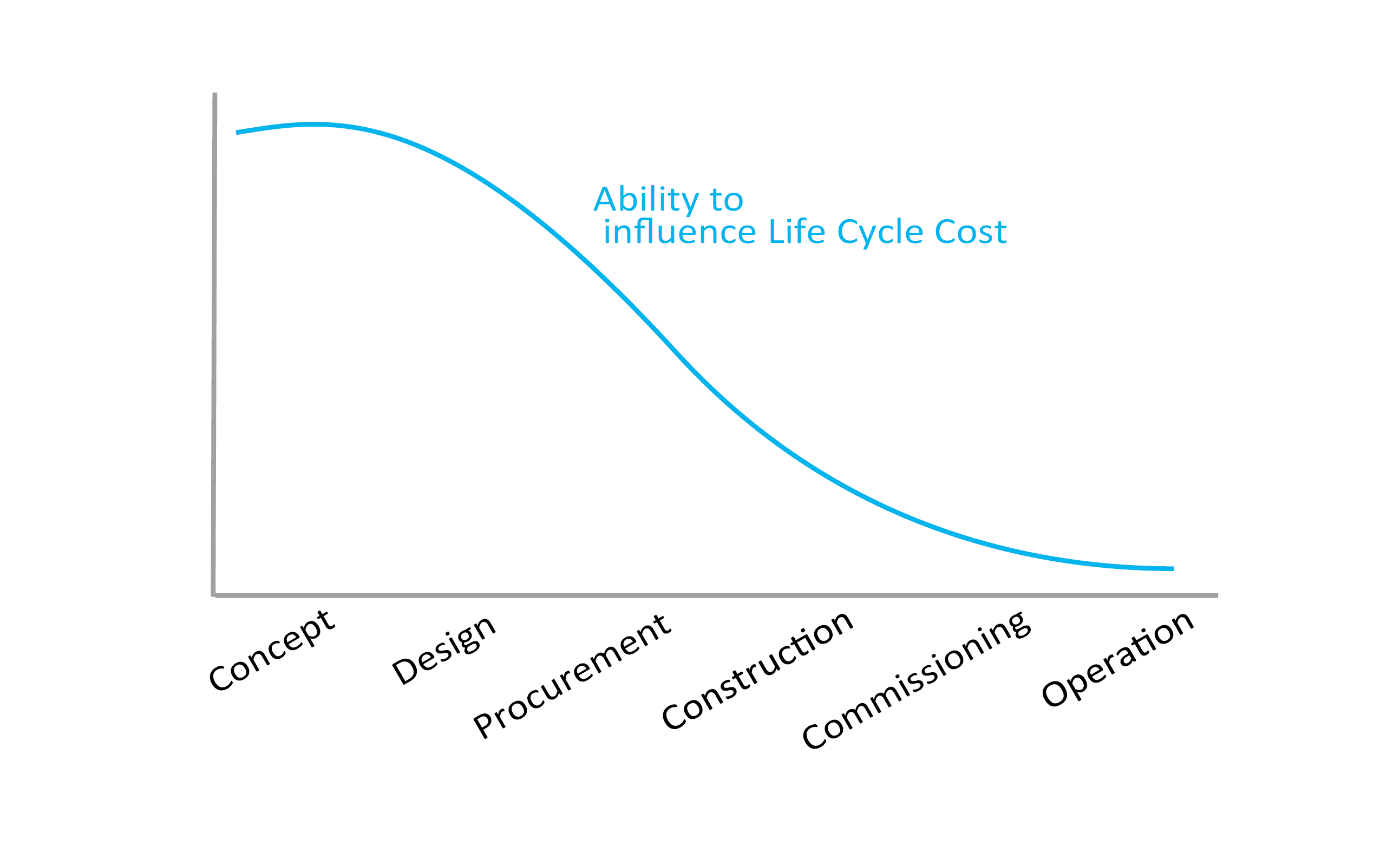
Yet, complex business realities put priority on immediate commercial, technological and construction matters. EPC companies also tend to lack the overall lifecycle perspective. Focus on cost control and an “agile” as-you-go construction approach contribute to future O&M problems: poor as-built documentation, lack of established maintenance plans, etc. Even in projects that have invested heavily in sophisticated BIM software, useful O&M data is often scattered between Excel and paper documents or simply missing. Design or installation problems that should have been identified during commissioning may go undetected: quick fixes were applied, problems went unreported, no analysis was carried out, resulting in early replacements, reliability problems and spiraling cost during operations.
In New Energy projects, new technologies, a higher degree automation, sometimes overconfidence in modern control system, IoT platforms and the likes, and the relative lack of O&M experience, exacerbate the challenge. O&M preparation represents a significant untapped potential in the ongoing energy transition.
Learning from experience
Siveco China, established in 2004, have in the past 20 years developed specific expertise working alongside plant owners and EPC contractors from the early stage of the project, ensuring smooth transfer of technical documentation from construction to operation, ensuring maintenance readiness before start-up using Smart O&M solutions.
Smart O&M is a modernized take on the traditional Computerized Maintenance Management Systems or CMMS, encompassing modern BIM and IoT technologies and a wider scope covering HSE and ESG. The solution is ideal for greenfield plants, supporting data preparation, commissioning and start-up with an accurate technical database and enforcing good maintenance practice from day one.
In Asia more than anywhere else, the Smart O&M solution turns out to be the ideal tool to bring concrete structure to the O&M preparation process often perceived as abstract (“Prepare for maintenance? But the equipment has not yet been delivered! The maintenance team hasn’t been hired!”). The high-tech factor becomes a key motivator for engineers involved in the project.
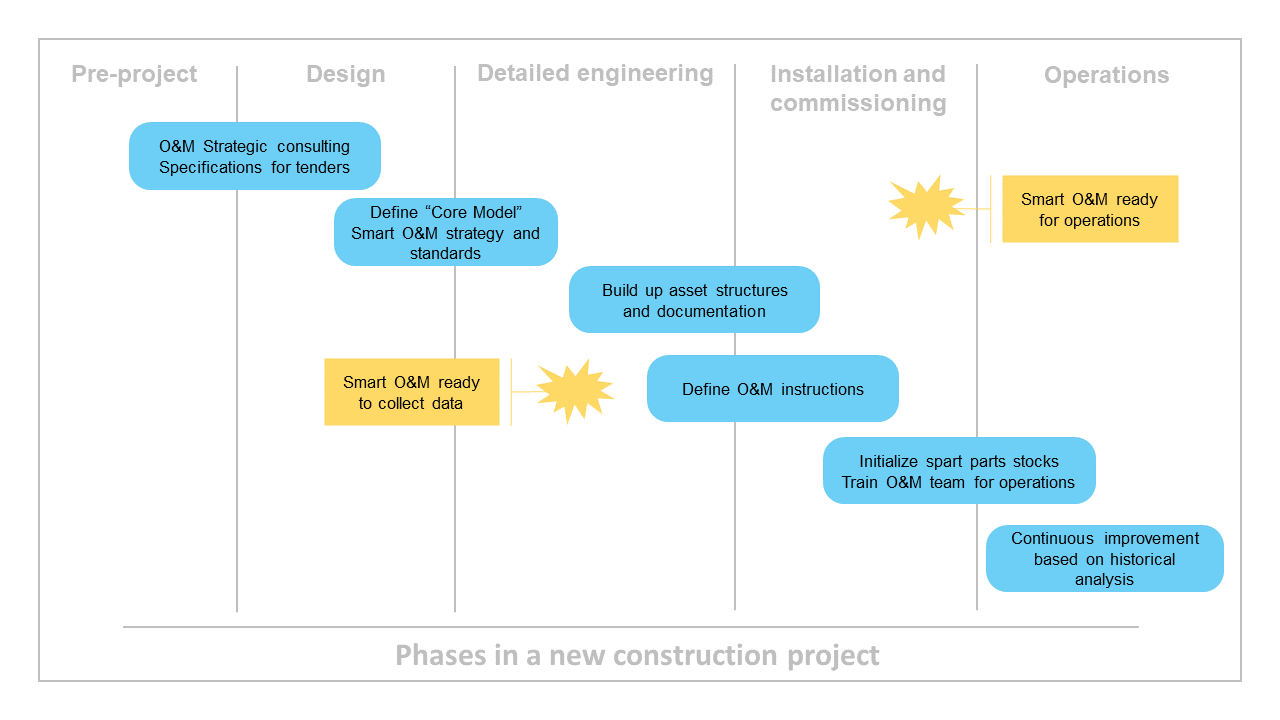
Main benefits
Detailed, accurate and easily accessible plant documentation
The Smart O&M platform helps coordinate suppliers to build up a detailed and accurate technical documentation (specifications, contracts, spare-parts lists, etc.), in line with O&M standards (rather than construction habits) and immediately usable by the O&M team.
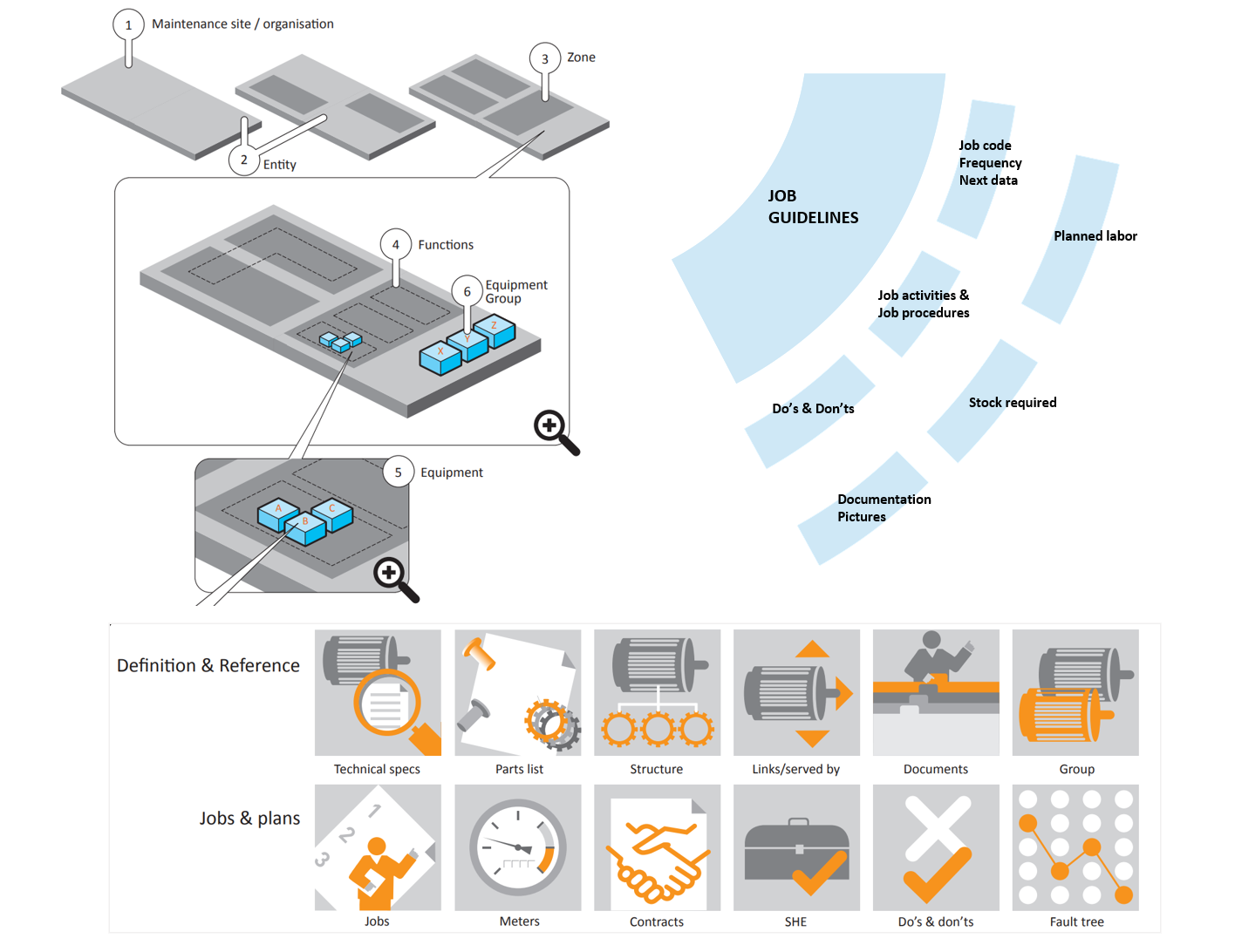
Traceability of commissioning problems
Commissioning engineers record problems onsite in their Smart O&M mobile app, ensuring proper follow-up by construction company and suppliers. Faults occurring in the early phases of operation are accurately documented, with root cause analysis, remedial action plans, in the O&M historical database.
Support ESG goals in the O&M system
As ESG is gaining traction, it is often managed separately from O&M. More than just monitoring emissions, energy consumption and showing beautiful KPIs, ESG relies on the systematic analysis of problems, tracking improvement actions, based on proven data from sensors and people. ESG is best tackled as part of the Smart O&M build-up, to ensure ESG and O&M strategies are fully aligned.
Integration with automation systems
Construction is the best time to integrate data from automation systems (DCS, SCADA, IoT in general) in the Smart O&M as this is when the O&M strategy, in particular the role played by predictive maintenance, is defined. Joint systems design ensures more meaningful data transfer (traditional DCS-CMMS interfaces often send alarms and measurements indiscriminately) and full HMI integration (operators can access technical documentation directly from their supervision HMI).
Integration with BIM
Similarly, an early integrated Smart O&M design allows the smooth buildup of completely integrated “BIM for O&M” solutions, with user interface integration allowing users to view the model (usually in Revit format) inside their O&M environment and to access all data from O&M to BIM, from BIM to O&M.
Optimized plant lifecycle
In greenfield energy projects, ROI from the Smart O&M approach can be achieved as early as startup time, thanks to direct savings during the construction to maintenance handover, with lower manpower (in-house teams and maintenance consultants), as well as lower IT and systems integration costs. In projects involving ambitious BIM plans, savings may be achieved by lower BIM consulting fees alone. More importantly during the O&M phase, this approach can easily save millions of dollars in risk reduction through the enforcement of better HSE standards, avoided losses (downtime, delayed repairs, recurring problems etc.), and ensuring regulatory compliance.
Global projects highlights
Sunzil, a JV of Total and EDF, operates over 750 solar PV plants in the French overseas territories, islands scattered all over the world, presenting enormous O&M challenges. Rationalized work procedures in the centralized system (Coswin 8i) resulted in improved service levels (response time divided by 2 to 3), better safety and a more secured supply of spare parts.
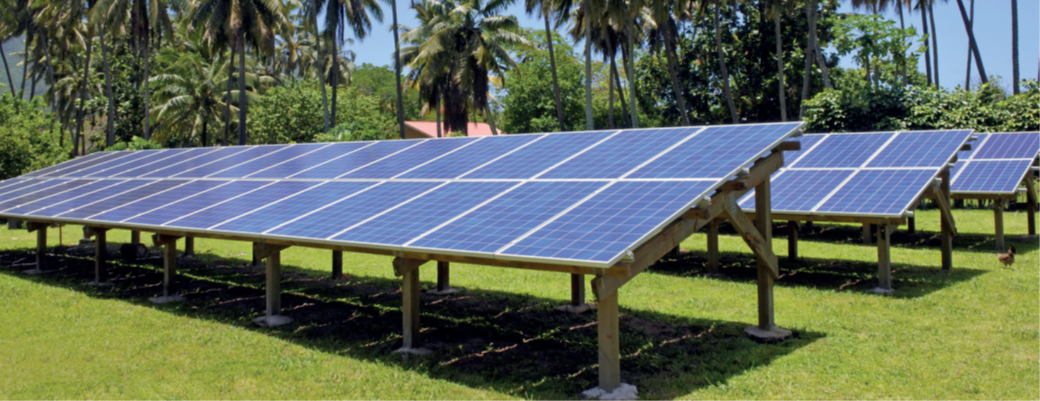
SVA Group owns 30 hydroelectric plants for a total capacity of 906 MW in northern Italy. The company standardized assets management and HSE, ensuring a proactive O&M governance to ultimately extend the useful life of assets. The Coswin 8i-based O&M solution runs on PC (web), mobile (offline and online app) and is interfaced with the corporate SAP.
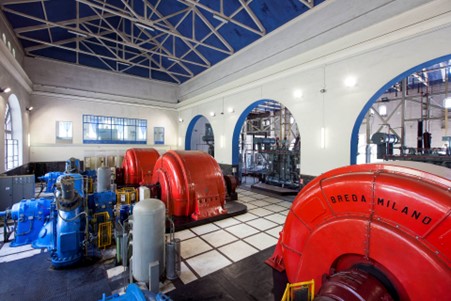
Photo credit C.V.A. S.p.A.
The 230 MW Garadagh Solar PV Plant in Azerbaijan is developed by Masdar, the Abu Dhabi Future Energy Company, and built by Dongfang Electric. The bluebee® solution (web and mobile), integrated with the plant SCADA system, started-up in late 2023, ensuring best O&M practices from day one.
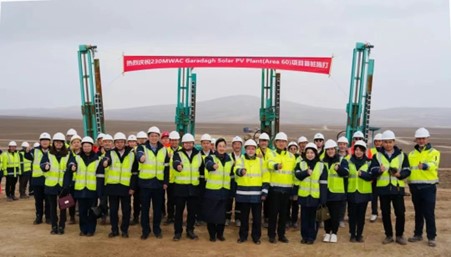
Korean EPC Hanwha Engineering & Construction built the 450MW Biskra Simple Cycle Power Plant in Algeria. Siveco China provided a turnkey O&M solution in time for start-up (2016). Data preparation services and system configuration were performed in Asia, with final system installation and end-user training onsite in Algeria.
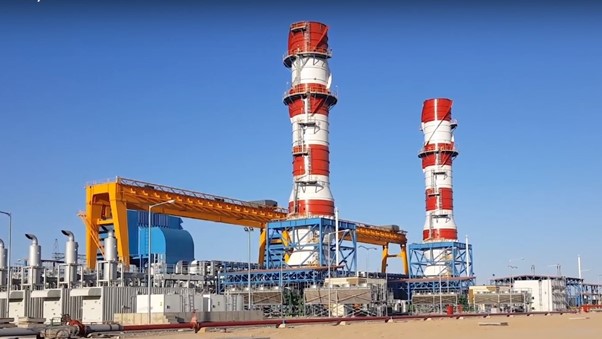
Center One Shopping Plaza in Bangkok, Thailand, launched a project aimed at improving the maintenance of centralized utilities at the 20,000sqm mall. The implementation of bluebee® was conducted by a joint team between Bluebee Technologies, a branch of Siveco China and academic partner Chulalongkorn University’s School of Integrated Innovation.
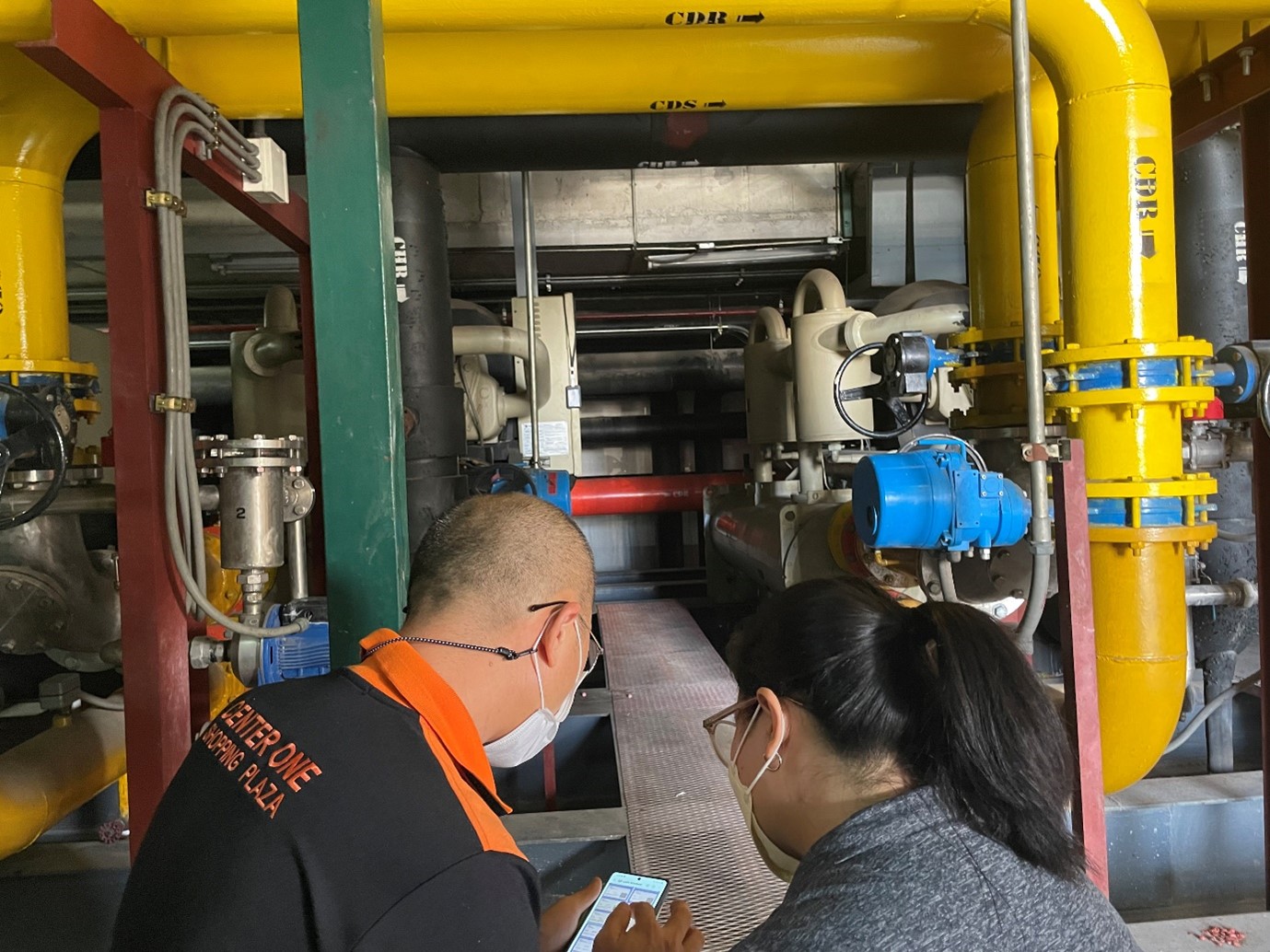