The maintenance assessment: a stepping stone for improvement
Maintenance assessments (sometimes called “audit” although we prefer the term “assessment”) represent a growing part of our business in China. This article will explore the principles, practice and benefits of such assessments.
1. Why an assessment?
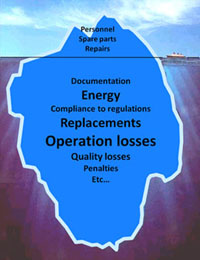
After over 20 years running maintenance assessments worldwide, Siveco has shown that poor maintenance can drag down profits by up to 40%. According to benchmarks in manufacturing, even the world’s very best plants can still deliver up to 11% more in bottom line profits.
Based on a unique experience combining both industrial maintenance expertise and consulting project in China, Siveco has developed a proven maintenance assessment methodology: an approach that has delivered results for many facility owners in China.
Maintenance improvement is often not about cutting budgets, but about improving effectiveness: indeed our studies show that you can save more than 10 times more money by acting on indirect costs and losses, i.e. the impact of maintenance on the business. But: where and how? This is the question we can answer.
The assessments are designed to answer such questions as:
• Where and what are you excess costs and losses?
• How to get more ROI from your CMMS/EAM without new investment?
• Identify maintenance improvements and how to deliver them!
• How to get more ROI from your CMMS/EAM without new investment?
• Identify maintenance improvements and how to deliver them!
2. The Siveco assessment
Principles
Our assessments are always tailor-made to each customer’s specific case. We can however distinguish three types of assessments:
• Maintenance organization assessment – focus on the organization and its processes
• Maintenance system (CMMS/EAM) assessment – focus on your systems and their utilization
• Condition assessment – focus on the equipment itself and its condition
• Maintenance system (CMMS/EAM) assessment – focus on your systems and their utilization
• Condition assessment – focus on the equipment itself and its condition
Often our assessments combine components from all three types above to answer the key questions:
1. Where do you stand?
• What is your situation now?
• What are you getting for each RMB you spend on maintenance?
• What are you getting for each RMB you spend on maintenance?
2. What could you gain?
• What direct costs could easily be cut?
• What would performance improvements deliver to the bottom line?
• How much more flexible and “fit” for modern business would you become with world class maintenance?
• What would performance improvements deliver to the bottom line?
• How much more flexible and “fit” for modern business would you become with world class maintenance?
3. How can you achieve your goals?
• We provide action plans
• Knowledge-base of best maintenance practice
• Tools and services for implementing action plans
• Knowledge-base of best maintenance practice
• Tools and services for implementing action plans
Our working approach
Siveco assessments always involve active cooperation between the customer’s and Siveco teams, based on the following working principles:
• Dedicated expert full time on your project
• An on-site action focused on your main requirements, driven by a Siveco project manager, assisted by maintenance engineers
• A partnership approach of our work: we recommend efficient, long-term solutions, and prepare your teams in a self-working organization
• An on-site action focused on your main requirements, driven by a Siveco project manager, assisted by maintenance engineers
• A partnership approach of our work: we recommend efficient, long-term solutions, and prepare your teams in a self-working organization
Confidentiality: Siveco will sign Non-Disclosure Agreements as required by customer.
Safety is non-negotiable: all Siveco employees will wear the necessary personal protection equipment when working on site.
Note that all Siveco projects are offered on a fixed price basis for the scope defined in an agreement.
Methodology
The Siveco assessments are based on a standard assessment methodology that we have used in many projects across China, and on the professional expertise of our team members, always capable to adapt and improvise if needed.
Whenever applicable, European and IEC standards are used (alternatively, customer can request specific standards to be applied).
Assessments always comprise three main phases as shown in the figure:
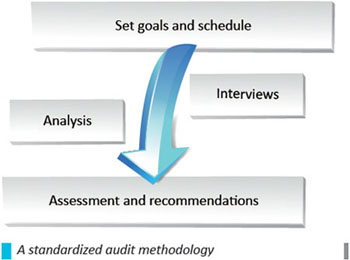
Deliverables
The main deliverables for the assessment are:
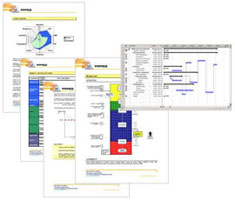
• Detailed assessment report (completed Excel document and analysis report, which would include, depending on the scope of assessment, pictures, work processes maps, etc.)
• Recommendation report with related action plan. Recommendation report could include ROI estimates (if financial data was made available to Siveco).
• Optionally, the above data and action plans in advanced electronic format (CMMS database) with possible follow-up services.
• Recommendation report with related action plan. Recommendation report could include ROI estimates (if financial data was made available to Siveco).
• Optionally, the above data and action plans in advanced electronic format (CMMS database) with possible follow-up services.
The report with our recommendations will be presented to the management team at the end of the project, after which discussions will take place. A final conclusion report will be drafted at the end of the session.
3. The supporting tools
Benchmarking
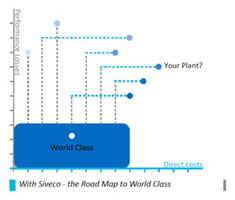
Benchmarking with international standards and other companies plays an important role in all Siveco assessments.
Our growing customers’ database in China and abroad allows us to benchmark your operations to other plants in similar or different industries. We also run multisite assessments with internal benchmarking between your own sites.
A strong basis for our maintenance benchmarking in China has been the annual “Maintenance in China” survey that Siveco has run in association with the Sino-European School of Technology of Shanghai University and the European Chambers of Commerce since 2006, covering over 1,500 multinationals in the country.
IT tools
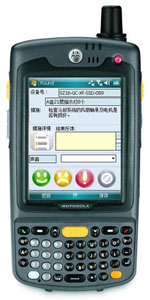
Owing to Siveco’s strong background in using technology to support maintenance improvement, IT tools play an important part in supporting assessment services, depending on the scope and size of the assessments.
The detailed methodology for each types of assessment is pre-established, serving as a guide for Siveco’s engineers during the assessment itself available in various format: either in Excel (suitable for interviews) or on mobile devices used by Siveco (for onsite surveys). Findings are reported directly in the Excel sheet or on the mobile, allowing immediate feedback and analysis.
When conducting site assessments, Siveco engineers are equipped with bluebee Surveyor: a unique tool to capture information from the field, record asset conditions, or even to build a complete facility or plant database by simply walking around and taking pictures. Follow-up actions (job request, preventive job) are automatically created and updated into Siveco’s central server database. Depending on the scope of contract, Siveco can then deliver a complete technical database, including photos, remedial actions to be taken, etc. in CMMS format (by remote access or installed at the customer’s site).
The Siveco back-office
Assessments are conducted by true maintenance experts appointed on the project, under the responsibility of a dedicated project manager:
• Our team members have worked previously as maintenance managers, preventive maintenance engineers, CMMS leaders in facilities, manufacturing and infrastructure projects.
• The Siveco China team comprises both local experts and foreign experts with experience of world-class maintenance.
• Our CMMS experts have working knowledge of various systems available in the Chinese market.
• The Siveco China team comprises both local experts and foreign experts with experience of world-class maintenance.
• Our CMMS experts have working knowledge of various systems available in the Chinese market.
In addition, during the entire project, the assessment team will have access to Siveco Shanghai’s back-office resources, which includes:
• Back-office teams and the Siveco network of experts on specific technologies (e.g. vibration analysis or corrosion), specific facilities or equipment (e.g. HVAC specialists) or methodologies (e.g. IEC standards).
• Centralized IT tools including benchmarking database and CMMS in SaaS model.
• Centralized IT tools including benchmarking database and CMMS in SaaS model.
4. The assessment and its benefits in practice
In practice, for the typical assessment, two Siveco engineers will come to your site for approximately one week. For a CMMS/EAM assessment, one engineer will focus on maintenance management, the other on the utilization of the system itself. For a more organizational assessment or a facility condition assessment, the assessment will involve specific industrial skills as required. Onsite work will be concluded by a presentation workshop, followed by report preparation time, before the final deliverables are handed over to the client.
Siveco China has experience conducting assessments in all three target segments: Facility Management (property owners and FM suppliers), Industry (factories in various industry, process or discrete manufacturing) and Infrastructures. Nowadays, in addition to independent assessments, all our projects include a start-up assessment and our “enhanced maintenance contracts” also utilize our assessment practice. The accumulated experience of our team (some of our team members have been active in this field since 1997) is unparalleled in China.
A case study of a CMMS assessment was presented in a past newsletter.
Some of the concrete benefits observed in previous assessments include:
Maintenance organization assessment at a large process plant
The overall conclusion of the assessment showed that the company should focus on improving performance instead of further cost cutting: analysis of financial figures and comparison with benchmarks show that the plant has extra capacity to fund this effort, i.e. it can easily afford the additional cost. This would result in downtime reduction with easily measurable returns: a detailed technical study estimated returns at 1 million RMB within one year on the main machines alone.
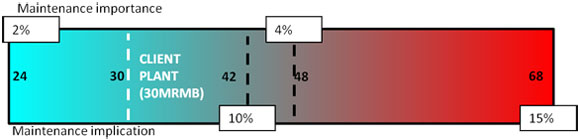
Benchmarking of key metric (figures are in millions RMB).
CMMS assessment (SAP PM and various other systems) at a chemical plant
The in-depth assessment showed that the company underutilizes its SAP infrastructure but has built a practical way to work around it, using various additional systems and well-defined management procedures. Overall the maintenance system is working rather well compared to similar companies in China, whether using SAP or other CMMS tools. This is to the credit of the company’s strong maintenance team members and management.
Weaknesses in analysis and decision support started to affect the capability of the maintenance division to improve its performance, while production put increasing demands on reliability.
Siveco recommended implementing small improvements in SAP Work Orders and to develop better reports (probably using the SAP Business Warehouse tool already in place in other departments). A third-party mobile solution would certainly enhance the inspection process, allowing a full feedback loop to manage preventive maintenance improvement. The costs/benefits of the various options were analysed.
CMMS assessment (Maximo) at automotive plant
The assessment found that the maintenance organization focuses its efforts on basic preventive maintenance: inspection, greasing, etc… as it lacks the necessary tools to eliminate failure through technical analysis. As the maintenance team is understaffed and busy with production-related tasks, and without proper support from the CMMS, they do not have the time to manually process long lists of WO feedbacks, although they do have the technical knowledge to understand their machines and find solutions.
This situation finally leads them to insure themselves against breakdown risk by adding more inspections (i.e. more workload). This is consistent with the pure “workstation approach” of the current failure analysis tool: the inspection plan is based on workstation.
The systems proved to be one of the bottlenecks and no solution was proposed by the IT vendor other that providing resources to develop reports. These problems reflect implementation- rather than software-related weaknesses, resulting in low ROI on the CMMS investment.
Siveco recommended a complete course of action, based on improving technical feedback, with standard pick-lists for downtime, causes, actions etc. The equipment structures should be reorganised to accommodate such reporting (currently not possible). IEC 81346 or ISO 14224 standards were proposed as the basis for this change.
Facility condition assessment at a major retailer
A full facility assessment was conducted in one of the buildings, covering the building itself and all systems (HVAC, water, fire-fighting, lifts, etc). The study also included a review of the FM suppliers’ contracts, the quality of their work and the paper-based reporting systems. Siveco delivered a full assessment report in two formats: office documents (word file with pictures, Excel list of recommended actions, updated maintenance plan in Ms Project format) and in database format, easily up-loadable into a CMMS. For each problem detected, a diagnosis was proposed, together with corrective and future preventive actions, allowing the retailer not only to take immediate measures, but also to prevent reoccurrence of problems. A management solution was proposed in order for the customer to better manage its facilities in the long term.
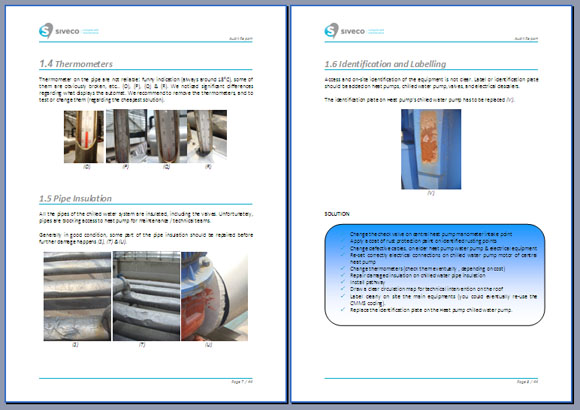
Sample facilities assessment report (also delivered in Excel and CMMS database format)