Status of “Enterprise Asset Management” (EAM) in the Chinese market
This article is based on an interview of our GM Bruno Lhopiteau, a leading figure in the Chinese utility maintenance market, by magazine Control Engineering China, in which Bruno shares his experience in the power industry and explains its relevance to other process plants.
Learning from experience
Power plants were among the first to implement computerized maintenance systems in China. Some of us remember the old days of Siemens BFS++, the development of PSDI and Datastream (long before those two historical players got acquired by large IT firms), the quick emergence of IFS (the company that brought me to China for that purpose in 1999), the many unsuccessful attempts by other vendors who never really understood the market, and later the appearance of SAP as a major actor. Local companies have also tried to replicate the success of their foreign counterparts, often targeting smaller plants, sometimes shamelessly copying better-known systems, but usually not going very far.
It is the privilege of pioneers to also be the first to make mistakes and hopefully learn from them. The emergence of SAP as an all-encompassing corporate system provided an opportunity to replace failed “EAM” systems, unfortunately, more often than not, those projects themselves proved disappointing. Most plants did not take the time to reflect on those failures and disappointments. Are “EAM” projects – either as part of local MIS projects, global EAM suppliers or SAP deployments – doomed to fail? Our own experience in other process plants shows that it is not the case. In this article we would like to share some of the lessons we have learnt over the years.
The so-called “EAM”
Acronyms can be powerful tools, especially when nobody truly understands them. Over the years, IT salesmen have become more and more creative in finding new ways to promote their products. The term “EAM” was invented by IT people in the mid-90s and has gained huge popularity in the Chinese power market.
In our opinion as maintenance professionals, we have always preferred to use the timeless industrial term “maintenance management system” (MMS) or “computerized maintenance management system” (CMMS). Without the initial C for computerized, the acronym denotes a broader view of maintenance, including the system itself but, more importantly, its usage.
“EAM” pretended to include stock, purchasing, sometimes project management and more functionalities – making the CMMS a true enterprise-wide solution. This was forgetting that CMMS had always included such modules and that in asset-intensive industries like power generation, maintenance is anyway at the core of the enterprise business.
The same IT salesmen have in the past few years tried to promote new terms EMMS, SAM, eEAM etc… while also using every possible buzzword (RCM, RCM II, SRCM, ERP II and many more) often without even understanding their meaning.
In the end, we at Siveco have taken the position to use a word that maintenance professionals all over the world recognize, regardless of IT fads and salespeople’s tricks. We encourage our customers to keep a clear mind and see the industrial reality behind the fancy words: the truth that CMMS, EAM, EMMS, MMS, etc. are one and the same thing.
Project failures due to “lack of maturity”
Most “EAM” implementations are heavily delayed, often taking several years to be fully operational. The system audits we perform often show a huge gap between the ambitious goals of the initial project and what has actually been achieved after several years. The comment we most often hear is “our organization was not mature”! It is surprising how successful large-scale state-owned companies so readily accept to be blamed for the failure of the projects… There are obviously various reasons for this; we will only discuss “professional” ones.
In our opinion, the relative lack of maturity, when it comes to maintenance methodologies and practices, is a given in the Chinese market. Maintenance consulting firms like us should of course take it into account during projects – in fact, as far as Siveco is concerned, it is the very reason behind our business! There are, on the other hand, many advantages of working in China. Among them, the abundance of new-built plants, for which systems can be designed and implemented from scratch – while in the West we mostly have to deal with existing plants, existing organizations and their working habits. Local technicians are much more open to new technology, they are very willing to accept change in their daily work process: in the West, technology is often seen as a threat, designed to control people’s activities. Finally, in China, it is also much easier to obtain ROI from projects, because maintenance has seldom been optimized. Not only projects do not have to fail in China, but on the contrary they can be much more successful both in terms of the technology deployed and ROI obtained!
“EAM” projects fail mostly because they are IT-focused. “EAM” suppliers in China inevitably have a pure IT background and operate on a Western business model, assuming to get maintenance expertise from the client… This model if fundamentally flawed: in China such projects should be driven by maintenance people.
Plant equipment structures
The most commonly heard problem with “EAM” projects, a few years after “Go Live” (the term IT people use to say the system has been put into use – to be compared with the engineering term of “commissioning”), is that equipment structures are outdated. From this derives a whole series of other problems: if equipment structures are outdated, it is sometimes not possible to record work orders, or they get reported at the wrong place. As a result, the history of work becomes wrong, affecting analysis. Spare parts cannot be ordered based on specifications from the system, so instead the team starts to rely on drawings, Excel records, papers. The usage of the system drops – or, as using work orders and work permits is usually mandatory as part of the power plant operation, the quality of data drops instead, rendering the entire historical database useless after a while.
This phenomenon is further exacerbated by the lack of analytic technical-financial reports in most implemented systems. Reports tend to replicate former paper-based reports: list of work orders, financial reports, compliance and other regulatory reports to the authorities, which were designed with paper systems in mind. Reports needed for decision support and reliability improvement are usually not implemented…
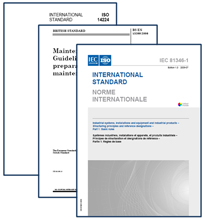
A key reason technical data is not kept updated is it is wrongly designed to start with. Power plant executives in China often talk about KKS coding: this job is sometimes handled by design institutes or specialized firms, which will produce the KKS structure in paper or Excel format. KKS is the German standard for power plant equipment designation, it has however been replaced, several years ago, by other standards more relevant to the needs of the Chinese power industry: we advise clients to be suspicious when vendors still talk about KKS in 2011… Siveco has been working with the latest IEC 61346 Industrial systems, Installations and Equipment and Industrial Products — Structuring Principles and Reference Designations, IEC PAS 62400 Structuring principles for technical products and technical product documentation and ISO/TS 16952-10 RDS-PP Reference Designation System Power Plants (the “new KKS”). We note that China is an active member of IEC (the International Electrotechnical Commission).
In conclusion – time for a new start for power plant and other industrial CMMS in China
In power generation as well as in other industries in China, customers can benefit from nearly 15 years of history with the so-called “EAM” projects. It is time companies draw lessons from past failures and the accumulated experience, which we attempted to summarize in this article. Power plants executives are educated engineers with high responsibilities in the well-being of the nation, they are perfectly capable to see the failings of past projects and to learn from them, even if people will still claim their project is successful to avoid losing face or to help their suppliers develop more business.
Our company Siveco China, the country’s largest maintenance consultancy, has a long experience with power projects all over the world (our first customer was EDF, the French state-owned power utility), vast experience in process plants in China, and has recently displayed its ability in an
export project; with CNEEC in Malaysia. Personally I have, since 1999, involved not only in CMMS but also in engineering systems, condition monitoring and ERP for power utilities.
There are four main ways we can contribute to maintenance projects in power plants (and more generally in process plants):
– Owner’s engineers services, assisting the plant in the implementation of their “EAM” system – typically with SAP PM. This is explained in another article:
Getting the most out of SAP PM.
– Implementing our mobile solution on top of an existing EAM system, as a way to clean up the database and bring it back to life. This was performed for example in the chemical industry, see case study of
Sichuan Lutianhua Chemicals.
– For new plants, implementing a complete CMMS project from scratch, including the maintenance engineering and data collection part of the project, using our own CMMS “COSWIN”. This is featured for example in the
RPII case study.
All in all, in our view, a CMMS project should not be different from any other engineering project. In fact, a CMMS implementation is an engineering project, with clear goals and the ability to measure the results. This is the correct starting point for a project.