Save a forest with Siveco bluebee® solution!
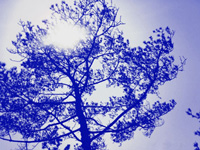
A green justification and funding for your maintenance improvement projects?
This article is based on studies conducted by our project team for customers already using a CMMS (COSWIN, Maximo or SAP PM), with a focus on replacing the paper-based process typically used: printing of work orders for dispatch to technicians, notes taken on paper and final input by a “CMMS secretary” or equivalent. bluebee® proves to be the ideal tool, more particularly for inspection and lubrication rounds. The studies demonstrate quick returns in more ways than one, with the opportunity to contribute to the “green” efforts of the company – and to benefit from such efforts to fund maintenance improvement projects.
Using bluebee®: focus on inspection and lubrication rounds
When bluebee® is installed, inspection and greasing personnel carry a mobile PDA device with them during their patrols. The device is already loaded with all the tasks to be performed during the day:
For the greaser, all the lubrication points are included, with a clear picture indicating their location and accessibility. The system also displays the type and quantity of lubricant required, as well as tools needed to perform the job (grease gun, brush, wipes, screwdriver and wrench if the greasing point is not directly accessible…). It is also possible to include safety instructions (“Do’s and Don’t’s”) and other recommendations.
For the inspector, all the inspections points to be checked during the day are loaded, together with the corresponding control methods or procedures, as well as the tools needed. bluebee® will also display all inspections to be performed during the week: if their planning interval is over one month and no specific day is defined, the technician can chose to do it anytime during the week. To assist diagnosis, pictures of “normal” and “abnormal” states (i.e. when a corrective action is required) can be also included.
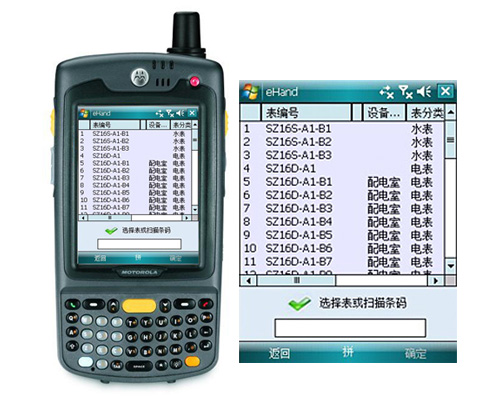
Inspection point in bluebee®
For more on the usage of bluebee® Inspector, see our case study [A catalyst for maintenance improvement at leading chemical group].
The benefits of bluebee®: immediate ROI
Automatically loading work instructions in bluebee® eliminates the entire process of managing and printing work orders (WOs) usually performed by Planners.
Inputting feedback onsite into bluebee® eliminates the process of manual data entry and closing of WOs by Planners.
These two processes, typical of the utilization of a CMMS, bring no value added. On the other hand, they are extremely time-consuming for your Planners (highly skilled workers) and can be easily integrated in inspection and greasing rounds without adding to the workload of field technicians: they simply do in bluebee® what they used to do on paper.
It is also possible for inspectors to create condition-based WOs directly with bluebee®, with attached photo taken with the PDA. bluebee® allows direct access to all the technical information available in the central database (Coswin or other CMMS – e.g. SAP PM or Maximo). For example, when reporting a temperature measurement: once the value is reported in bluebee®, a alert is displayed if the value is outside its normal range. The technican is then immediately aware that the situation is abnormal.
bluebee® allows for a more accurate follow-up of inspection and lubrication activities: a WO can be created for each equipment, without having to be concerned by the total number of WO generated by the system, since the admin process has been eliminated (in a traditional CMMS implementation, strategies should be defined to reduce the number of WOs to be printed, resulting less accurate reporting e.g. by equipment group). This is the ideal solution from an equipment management point-of-view.
The use of barcodes (one per equipment or per measurement/inspection point) – or RFID tags – to be scanned before feedback, helps ensure that the technician has actually been on the spot. This reduces the risk of work not done: it becomes almost impossible for the employee to report without having carried out the task (because the lubrication point is hard to access, due to lack of time or motivation). Such control is not possible with a paper process.
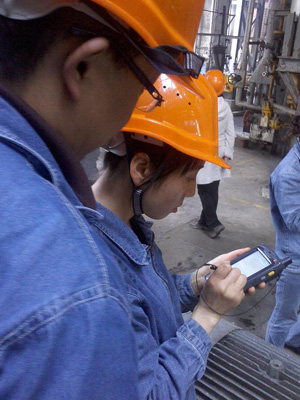
Technicians in action with bluebee®
The amount of information made available to field technicians thanks to bluebee® helps reducing the impact of employee turnover on the quality of inspections. bluebee® informs techicians on where to go, what to do, in such details that any technician, whatever his level of qualification and without prior knowledge of the line, can carry out the necessary tasks.
The longer term perspective: improving skills
As time pass, the current inspectors will become “Master Inspectors” and focus on defining inspection procedures. Those procedures, stored in the CMMS and directly available in bluebee®, will allow less qualified personnel to carry out the inspections. This constitutes an excellent tool to train the team and ensure smooth knowledge transfer.
As inspectors can spend more time building up accurate technical data, another step would be to use fault trees (symptom, defect, cause, action) to provide diagnosis support with bluebee®, for corrective maintenance. The process could be as follows:
1. The technician scans the barcode of the faulty equipment and inputs the symptom (from a predefined list)
2. bluebee® suggest likely causes, based on the equipment fault history, and provides access to previous WOs
The technician is thus guided in his diagnosis. Benefits are immediate: time saving in the diagnosis process and reduction of breakdown time. This can, in a more simple form (normal/abnormal states), be implemented from the early stages of using bluebee®.
Integrating bluebee® in your current CMMS infrastructure
As explained above, traditional CMMS implementations require a compromise to be made between a detailed work feedback (sufficient for analysis pursposes) and the corresponding admin workload (acceptable for the maintenance team).
More often than not, a “CMMS secretary” role is created. This unrewarding job is devolved to a junior staff member. This approach almost always brings problems with the accuracy of data (this person has to read hand written reports and input data into the system, often in a different format, without having any knowledge of the daily maintenance work) and key people (the planners, the maintenance manager and his supervisors) lose their feeling of ownership for the CMMS… this usually results in the system being abandoned or being used in a pure administrative manner (hours worked on work orders).
Over time, the CMMS is supposed to allow for an optimization of preventive maintenance : from the initial setup of tasks, to progressive changes in tasks and their frequencies based on technical-financial analysis. For example, for inspections carried out weekly on a piece of equipment that ultimately fails only every three months, a monthly check may be enough. This optimization work requires a significant amount of historical data in the system, at a good level of accuracy: it is often not the case due to inefficiencies in the reporting process described above (paper printing/input by planner or secretary) – this optimization is seldom done with the CMMS.
Additional work is required for the bluebee® implementation itself:
– Tagging of equipment with barcodes or RFID tags (can be done in-house or by Siveco)
– Setup or improvement of inspection/lubrication methodology (depends on the existing practice, often constrained by the CMMS)
– IT: installation and integration (facilitated by the use of a standard synchronization plaform, with available connectors to COSWIN, Maximo, SAP PM, easily adapted to other CMMS knowing that the data exchanged is always the same, regarless of the CMMS)
– Setup or improvement of inspection/lubrication methodology (depends on the existing practice, often constrained by the CMMS)
– IT: installation and integration (facilitated by the use of a standard synchronization plaform, with available connectors to COSWIN, Maximo, SAP PM, easily adapted to other CMMS knowing that the data exchanged is always the same, regarless of the CMMS)
At the same time, the bluebee® projects allows for a “clean-up” of the existing CMMS data which often prove to be outdated or wrongly structured (especially the equipment hierarchy). A major side benefit of using bluebee® is the rejuvenating effect it has on the CMMS – it “adds value to your CMMS” (see previous article on the subject: Getting the most out of SAP PM).
Save the forest: another way to look at an bluebee® project!
While we at Siveco, and our customers, tend to think in terms of maintenance improvement – and the huge financial returns at stake (ROI within one year being the norm, with often much quicker returns obtained from specific “spot” actions) – this is usually not the case of corporate managers. The elimination of paper work orders, on the other hand, is an incidental aspect of the project, which may prove crucial to get management attention and perhaps even funding! Indeed, most large corporations, multinationals and locals alike, have adopted environmental policies: “Green” has become a corporate best practice (and a huge business in itself).
At one of our customers operating metal-working plants, we have counted 240 printed WOs per week – which add up to one tree per year – for inspections only.
Does your company have a “green” program? Can obtain financing from the “green” budget for your projects? Can you at least get more attention from management?
Do not miss next month’s reliability article: saving the whales with Siveco!