Preventive maintenance, Risk management and the Middle-class Gentleman
“By my faith! For more than forty years I have been speaking prose without knowing anything about it, and I am much obliged to you for having taught me that.”
The Middle-Class Gentleman (Moliere) Act II, Scene IV
A sense of familiarly
We first started working with Risk Prevention in 2009, in the wake of increasing media coverage of metro accidents, fire hazards and elevators mishaps. The government started to put more efforts on enforcing existing regulations and new rules were put in place, while companies’ managers also became more aware of safety issues.
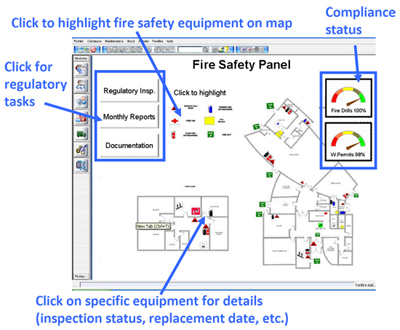
Example of fire safety management system, published in our March 2010 newsletter
It is unfortunate that industrial accidents – very damaging fires, industrial mishaps, sometimes resulting in death, have always been a strong driver to our projects: we may have talked to a prospective customers for several yeas about putting together a preventive program, often based on onsite assessments and clear estimated ROI, decisions always get postponed – too often by corporate headquarters who doesn’t understand why the Chinese operation would require a special treatment. Then one day we get a call, the customer wants to start the project immediately and we quickly found out why: a mechanic died electrocuted because work permit procedures were not clearly defined and implemented, or an equipment outage resulted in enormous losses (sometimes valued at several times the annual maintenance cost), etc.
When they first started to deal with Risk Management executives, our team of maintenance specialists felt strangely familiar with the principles and concepts used. We learnt that Risk Management was often about gathering data in an accurate and structured manner, so that regular reviews could be performed by the managers in charge, key performance indicators calculated, and actions initiated… The preparation of various types of audits or inspections, and their implementation, was the key to this process.
It rang a bell. At Siveco China, a major part of our work had always been to help industrial customers to record failures, events and actions in such a way that meaningful analysis could be done. Based on historical data and more particularly those representing the impact of failures on operations (production, safety, regulatory compliance, etc.), technical managers are then able to make decisions. Decisions may consist in new or modified preventive maintenance actions, design modifications of a machine, training for operators or… simply “doing nothing” (run-to-failure) when the risk associated with a failure is acceptable. Did we just say “risk”?
In true Siveco fashion, we looked up the available international standards, the ISO 31000:2009 – Risk management — Principles and guidelines series of standards and more particularly ISO 31010 on Risk assessment techniques. What we found confirmed our initial impression. This is how risk is defined:
Risk is effect of uncertainty on objectives
Risk is the effect of uncertainty on objectives. This is a very interesting definition, because
1- It covers both “bad” risks and “good” risks, i.e. opportunity (although, most of time “bad” ones are under the spotlight).
2- If there are no objectives, then there is no risk.
2- If there are no objectives, then there is no risk.
Back to the more familiar European standard EN 13306 – Maintenance terminology, our readers will remember that the role of maintenance is “to retain in, or restore to, a state in which the items under maintenance department responsibility can perform the required function”. Typical maintenance objectives include availability, cost reduction, product quality, environment preservation, safety (several of them related to regulatory compliance). Maintenance is meant to reduce the effect of uncertainty on these objectives, mostly by reducing the probability of failure through preventive maintenance.
To be very clear: this means that if you have implemented a Preventive Maintenance plan, you that have already successfully implemented a Risk Management framework! We can further illustrate the similarity (actually, the equivalence!) between both principles by looking at two diagrams:
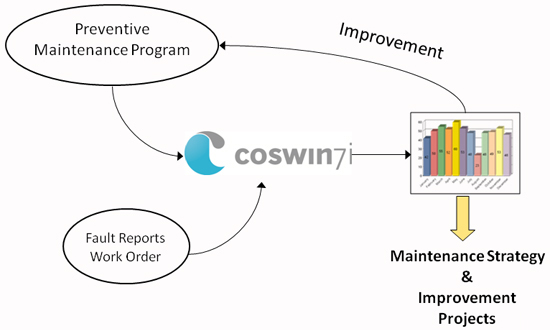
The Siveco Approach
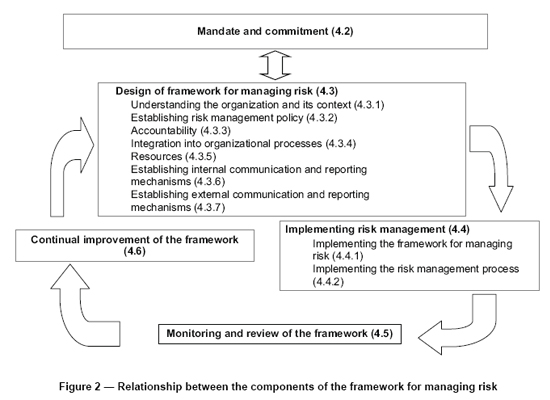
ISO 31000
Just like Monsieur Jourdain in Moliere’s play, we had been implementing Risk Prevention frameworks without knowing it for many years!
The best Risk Management tools are… maintenance management tools
A more detailed study of the ISO 31000 series of Risk Management standards confirmed our earlier “discovery”. For example the risk management process (clause 5) defined in ISO 31000 describes a typical failure analysis process, with all the steps maintenance specialists are familiar with:
Step 1 – Establishing the context (i.e. the scope)
Step 2 – Risk (breakdown) identification
Step 3 – Risk (breakdown root cause) analysis
Step 4 – Risk (breakdown impact) evaluation
Step 5 – Risk (breakdown) treatment
Step 2 – Risk (breakdown) identification
Step 3 – Risk (breakdown root cause) analysis
Step 4 – Risk (breakdown impact) evaluation
Step 5 – Risk (breakdown) treatment
Thanks to our experience in those areas, we are all Risk Managers, with a focus on technical risks. Don’t just take our word for it, ISO 31010 is even more straightforward: it lists a variety of methods and techniques recommended for risk assessment. Techniques are rated as “Strongly Applicable (SA)”, “Applicable (A)” or “Non Applicable (NA)” for the 5 aspects of risk assessment, namely: Risk identification, Consequences, Probability, Level of risk and Risk evaluation). Out of 31 evaluated methods, FMEA (Failure Modes and Effects Analysis) and RCM (Reliability Centred Maintenance) are among the few techniques rated with 5 SAs (Strongly Applicable) ratings!
Our own experience at Siveco China, supported by undisputable international standards, highlights the strong convergence between Maintenance Management and Risk Management. The concepts put into use are strictly the same, which means that Risk Managers can draw on the experience of their maintenance counterparts and the existing tools. Conversely, Maintenance Managers can learn from the more recent risk management practice, especially on how to communicate risk to stakeholders and how to involve them in the process.
On a final note, in China, both disciplines are at similar stage of maturity, which means they are meeting similar challenges:
– The ability to gather data in a systematic and structured way (ISO 31000 emphasizes that “Relevant and up-to-date information is important in identifying risks. This should include appropriate background information where possible.”)
– The ability to utilize and analyze not extensively at a start, but by prioritizing them or giving them a weight
– The ability to set-up and implement on the long run a risk prevention/maintenance strategy including regular checks and actions.
– The ability to utilize and analyze not extensively at a start, but by prioritizing them or giving them a weight
– The ability to set-up and implement on the long run a risk prevention/maintenance strategy including regular checks and actions.
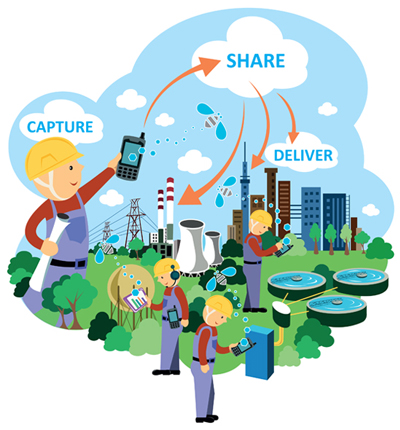
bluebee® – for the worker of tomorrow
Major challenges, even more so for large organizations, in a fast evolving environment, often with a transient workforce… Challenges which Siveco China has made its business to tackle, with a uniquely successful track-record using high-technologies to address what we have called “maintenance with Chinese characteristics”, with customers as varied as chemical plants, automotive factories, real estate owners, retailers etc.