Learning from retailers
Introduction
When we started this company in 2004, coming from an infrastructures and utilities background, we would not have imagined applying our know-how and technology to retail stores! After all, a retail store is technically much less complex than a plant, represents a much smaller investment and technical failure certainly has less impact…
It however happened: we first started to work with Auchan, Ikea, B&Q, much later with Carrefour, Sephora and retail property owners. We conducted numerous maintenance audits, ran improvement projects, implemented computerized maintenance systems and later went on to design new solutions for retailers and multi-site facility operators.
More surprising, we found that the innovative technological solutions we designed for retailers could also apply to industrial customers. We learnt many lessons from retailers and now our entire business benefits from our experience in this market segment!
This article will simply look into recent stories featuring our experience with retailers and try to show their relevance to other industries, more particularly to industrial plants.
The Carrefour China experience – advanced modern technology in action
In December 2013, our Risk Prevention Management System (RPMS) project with retailer Carrefour won the prestigious CHaINA Supply Chain Excellence Award. A customer story has been published here: Risk Prevention, key to sustainable retail success at Carrefour China.
The Carrefour China story is a story of using flashy technology, touchscreen panels, tablets, mobile devices, integration with various subsystems, to achieve industrial goals. Comparatively, too many industrial plants still rely on old-style CMMS, with a PC at the office, a printer, a lot of paper work orders and a “CMMS secretary” to use the system… See the movie One Day in the Life of a Maintenance Team for an illustration (this movie even won an award). A CMMS display is often unappealing, with grey menus and tables… The touchscreens used in Carrefour are the opposite of that, they are lively, user-friendly and modern – and our customers like to show them to everyone! We often hear industrial clients telling us their technicians will not be able to use a mobile solution – perhaps they are “too old”, “not open to technology” or “less educated”… If so, how come retail workers can use them?
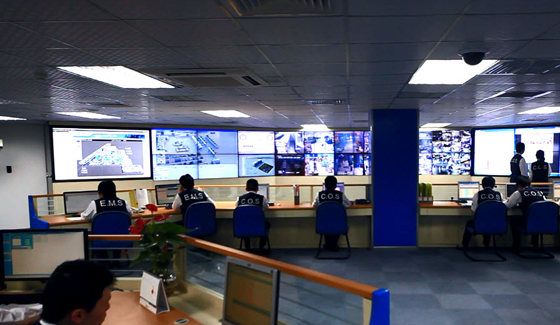

Integrating POS (or shop floor users) as part of the bluebee® suite
A POS (Point of Sale) is the software used by the cashier in a retailer store. The integration allows such users to create Job Requests and monitor their handling by the maintenance team. The same approach could be used to integrate other types of terminals and software tools with bluebee®, for example in a manufacturing plant to integrate operators’ terminals to create and monitor production problems.
Integrating shop floor users into the CMMS has long been a topic of discussion in the manufacturing industry. As Lean Manufacturing became popular, this topic has become again popular. Is it however seldom done in practice: most production teams interact with maintenance using paper work orders or sometimes from an old PC installed in the production area, even when the most advanced computerized CNC machines are used. Why is it so, when technology is available? The Siveco experience with POS integration retail proves that it can be done.
The bluebee® solution for multisite operators
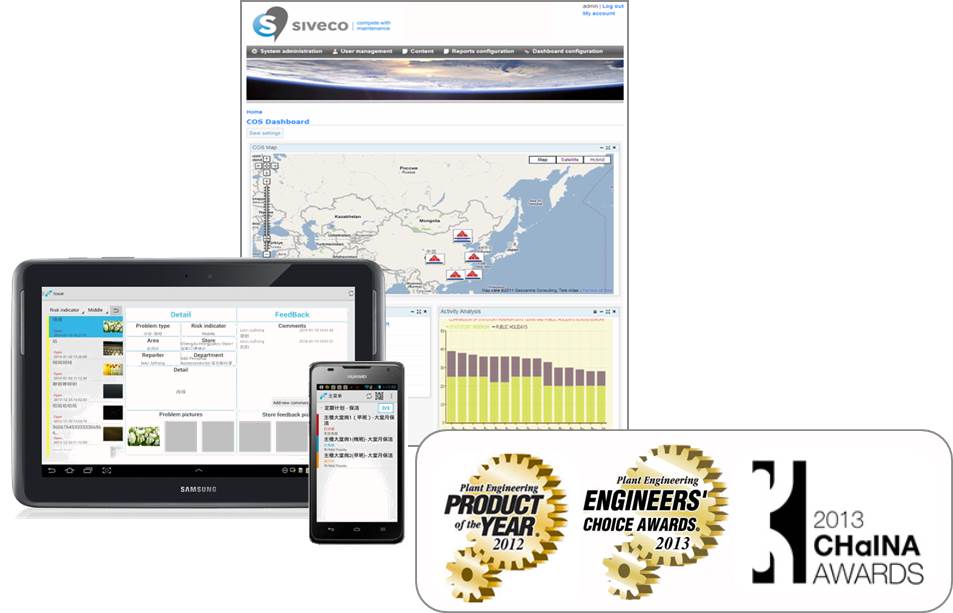
Siveco retail and facility management customers use the bluebee® technology to deploy and enforce their best practices in Facilities Management and Risk Prevention over a very large number of sites all over China. The solution is described in this Tips & Tricks article.
This approach is now well proven, with references including Carrefour China but also Chinese property management companies such as Changcheng Property Group (see the movie here) or Green Property Management, as well as industrial service provides such as Cofely Gient Energy Services.
We believe the same approach could be applied to large multi-site manufacturers (central deployment of the best practice embedded in the system to all the sites). It will prove much more cost effective that traditional site-by-site CMMS/EAM projects and technology, mobiles and tablets, will be a strong motivating factor for users.
Conclusion – the future of CMMS/EAM in manufacturing
At Siveco, we believe that out-of-date technologies and approaches, the so-called “EAM” commonly used in the manufacturing industry, is bound to disappear. We explained our views before in the infamous “EAM is dead” article. This change has not occurred yet, but the example of retailers could prove a powerful one: if retail stores can make use of advanced technologies for their maintenance, why are comparatively more sophisticated industrial plants still using systems invented in the 1980s?