Industrial Excellence in China: Lean Manufacturing, a Giant with Feet of Clay
The Importance of Maintenance to Low-Cost Manufacturing
This article was published in Kunshan Connection magazine. Read or download the pdf format (in English only): here.
Maintenance with Chinese characteristics
Maintenance is seldom recognized as a key aspect of plant operations in China – how many articles have you read on the subject? Trendy topics such as Green Technologies or Lean Manufacturing are almost never seen in relation to maintenance, which however plays a critical role in their successful implementation. Not at the top of the corporate agenda, maintenance management is often left to a technical supervisor, reporting to production, or handled by the local JV partner.
At the same time, horror stories of poorly designed and badly maintained facilities abound. Industrial accidents make headlines; less critical incidents provide endless material for discussion between expats. The last edition of the yearly “Maintenance in China” survey, conducted by Shanghai University in 2010, estimated the indirect cost of maintenance, in the form of losses and consequential costs, at around 10 times its direct cost… which indicates that the impact of maintenance on business is far from insignificant!
It is not uncommon for industrial facilities to show signs of early aging, characterized by an increasing number of breakdowns after only a few years of operation. Quick aging is the direct consequence of maintenance not being managed: most organizations still operate on a purely reactive basis (“run-to-failure”), with a short-term view focused on immediate cost cutting. The abnormally low maintenance expenditures typically observed in the early years of a Chinese factory life inevitably lead to high unplanned cost later on. For instance, it is very common, in plants that have run for many years, to find design problems that should have been identified in the early stage of operation.
The situation is further complicated by some of the other aspects of “maintenance with Chinese characteristics”: an acute shortage of experienced managers and skilled technicians (multi-disciplinary knowledge, essential for maintenance management, is particularly lacking), widespread irregularities in procurement (too often willingly ignored by expat managers on the grounds that “this is China”) and the lack of capable service suppliers (facing even toughest labor challenges than manufacturers that can usually offer more attractive conditions and benefit from better-known brand names).
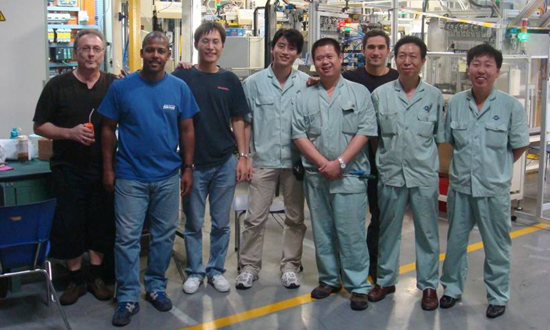
Building a new plant –prepare maintenance early
In China perhaps more than anywhere else, it is essential to take maintenance into account as early as possible, ideally from the design stage. This includes designing your facility and machinery with the constraints of maintenance in China in mind. While engineering firms based outside of China may not be aware of them, many locally-based businesses do not know any better: local Design Institutes and construction companies tend to have very narrow-focused team and won’t have much concern for future operations. Quick-fixes on construction sites are the norm, proper as-built drawings almost impossible to obtain…
Similarly, maintenance plans for utilities and production machines should be defined before start-up. Never assume that newly-recruited technicians will familiar with standard maintenance procedures, as would be the case in the West. Plans should be adapted to the reality of maintenance in China, to the experience, habits and skills of local teams: do not simply copy or translate Western standard operating procedures.
The more complex and automated the plant, the more maintenance preparation is critical – think about Foxconn and their ambition to have “one million robots” in China: who is going to keep them running and how? That is going to require very serious preparation! On a smaller scale, we have seen expensive machines (such as welding robots) left unused as they were too complex to maintain and even entire production lines (automated precision assembly) running on slow speed for the same reasons.
This recommended approach ensures that the required technical documentation, basic organization, well-defined inspection plans and other preventive actions are in place from the start-up stage, in a manner suited to the skills of local staff. It doesn’t ensure, however, that they will be properly implemented over time.
Operating the plant –ensuring best practices
Ideally, the maintenance team should be trained on modern maintenance practices, especially in terms of preventive maintenance, planning and optimization. The management team should also be made aware of the impact maintenance can have on production and the business (production managers often have had little or no previous exposure to such ideas). However, as many expats have already found out, classroom training tends not to work very well in China.
When it comes to maintenance improvement, Western wisdom – which recommends conducting audits, providing training, reorganizing the department and, when everything works well, introducing IT tools (a maintenance management system) to increase efficiency – is at best irrelevant, often counter-productive. More often than not, the audit will upset local teams (loss of face and often inadequate advice if done by a foreign expert without China experience), training will be forgotten as soon as it’s over, the reorganization will prove confusing (new roles not understood as too different from a traditional Chinese organization). At last computerization effort is likely to focus on administration (approvals, replacing paperwork, control of working time, etc.) i.e. on direct cost reduction, bringing no benefits in the area most needed (indirect cost reduction). The same scenario has been observed at dozens of companies all over China.
Experience has shown, however, than high-technology (typically a maintenance management system, albeit one adapted to local needs) is the ideal tool to immediately structure the maintenance team, to build up historical records (what happened, why, what impact did it have) to support improvement decisions based on systematic technical/financial analysis, to train the team on-the-job on the concept and practice of preventive maintenance and ultimately build reusable know-how (critical when turnover is high). The resulting organization will be less reliant on specific persons such as an expat manager soon to leave China or an excellent local technician soon headhunter by competitors.
A contrarian approach, from a Western point-of-view

For years the central government has been promoting “informatization” initiatives that amount to using IT as a shortcut to best practices (although the necessary industrial expertise is often lacking, resulting in computerization for the sake of it). Nowadays, high-tech is very well accepted by Chinese personnel, a generally young workforce, well-equipped in personal computing gadgets. High technology can be a powerful motivator for maintenance teams, which too often – and rightly so – feel undervalued in the factory.
The recommended approach may be counter-intuitive for Western companies. Many are reluctant to equip their Chinese plant and local employees with technology that their more qualified counterparts back home may not even use. It has however proven very effective in projects across China, while the more traditional Western approach usually meets with failure. Typical ROI for a maintenance improvement project making proper use of hi-tech, as a catalyst, can be well within one year, sometimes weeks when design problems are quickly uncovered.