Green buildings: the operation and service perspective
This article is based on our presentations at Green Building events held in Beijing and Wuhan during the month of June 2011. Some of the stories and pictures courtesy of Terao Green Building Engineering.
Sustainable Development is often all about design, choice of material, equipment and systems, construction… usually in view of obtaining a green certification for your building. The operation and maintenance aspects remain largely ignored, in spite of their significant impact on operating expenses and the lifetime of the building.
Green labels already point in that direction
Green certifications obtained in the design and construction phase have proven extremely successful with project owners in China, with the main goals to enhance their image (impact on the building rental and resale value) and to reduce future energy consumption (savings). China already has 77 LEED (the US label) and 52 GBDL (its Chinese counterpart) certified buildings, with hundreds more in the process of getting certified: LEED and international labels are naturally popular with international owners and high-end properties, while the slightly less costly and less demanding local standard sees very strong demand from local government projects. The ambitious targets set in China’s 12th five-year plan are certainly going to play a major role in this market.
Designing “green” involves more than engineering calculations; instead they require an Integrated Design Process, taking into account the following key concepts of:
• Defining long term objectives and life-cycle cost
• Anticipating technical issues causing underperformance
• Following a rational decision-making process
• Assessing and monitoring operations
• Anticipating technical issues causing underperformance
• Following a rational decision-making process
• Assessing and monitoring operations
This is why all these different labels have also developed rating systems for the operation of existing buildings.
The (green)tech effect
Technology has a powerful attraction effect, in China perhaps more than anywhere else. Buyers love technology-based solutions, which seem to solve all problems by simply getting the right piece of equipment. This is true of hardware in general, as opposed to services: tangible equipment has always been easier to sell, at a good margin, while services tend to be undervalued and subject to ferocious competition – including that of direct recruits (“with what you charge for a day, I could pay an engineer for one month”). Siveco China has, in a large part, built its business model on this phenomenon, packaging expert services within its technology offering.
Applied to green buildings, this phenomenon has been the driver to many projects, and to the business successes of many equipment suppliers. In terms of actual savings in operation, the effect has however been less than satisfactory. As always in modern China, the rapid growth of the market allows us to obtain quick feedback from operations and many “horror stories”, which can then be analyzed in order to improve the way we work: this is one of the aspects of what we at Siveco have come to refer to as “maintenance with Chinese characteristics”.
Feedback from the field
Actual performance often differs from the initial design projections. Let’s take a look at some of the stories.
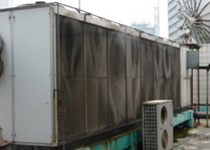
A facility assessment conducted on retrofitted residential buildings revealed sizing problems of the HVAC (a very common problem), compounded by obvious lack of maintenance and cleaning, which going up to the roof for a visual inspection was enough to uncover. The poor condition of the heat pump, adding up to the insufficient air side cooling capacity, resulted in low efficiency and lack of capacity: for the building users it meant comfort issues (29°C in summer, 15°C in winter) and high electricity bills.
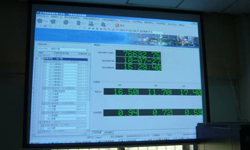
Energy Management Systems have become a typical feature of green buildings. Audit of a commercial facility showed that the system was installed and working, but was not used by the management team to take corrective actions. This was simply due to lack of skills and lack of building operation procedures in that regards. The building itself was modern, not the management team.

A large property operator has equipped all its sites with a very advanced centralized Building Management System. When the project was launched, the operator and its advisors (who should have known better…) were clearly enthralled by the Sci-Fi technology proposed and the huge benefits announced. Audits performed a few years down the line show the full-scope of the BMS was never delivered: instead the system only performed the usual building automation functions, appears to be disconnected at most times and cannot produce any useful energy consumption reports.
A few years ago, we audited a state-of-the-art R&D center, designed by internationally-renowned architects to showcase the deep concern of a multinational for the environment. A picture-perfect facility the day of its opening, the audit two years later revealed the very fast aging of the building and its inefficient HVAC operation. Apart from construction issues the foreign architect did not foresee, the maintenance schedule of the facility had to be totally redesigned.
In general, do LEED-certified buildings save energy? A survey of 100 LEED-certified commercial buildings showed that they consumed on average 18 to 39% less than average similar buildings, but that 30% of them consumed more! We are talking here about facilities that have been awarded the LEED label: they were designed and built to be energy efficient. But a shocking 30% of them, one out of three, are not. This proves there are indeed many things to be done to improve performance at individual building level, through proper operation and maintenance…
The above is not specific to China: similar stories of discrepancies between design and operation can of course be found in other countries. The gap tends however to be bigger in China, where the facility management practice is still largely immature.
The other side of the coin
The positive aspects of this lack of maturity is that seemingly simple operational and maintenance actions can have a great impact in terms of energy savings and sustainability (not only direct Opex savings but also in extending the lifetime of equipment and buildings i.e. impact on Capex). This is yet another aspect of what we call “maintenance with Chinese characteristics”.
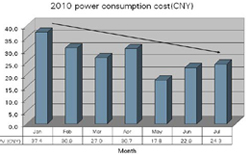
Traditional maintenance improvement projects, in all types of buildings, very often generate ROI through energy savings. A step-by-step preventive maintenance program conducted at an automotive supplier resulted in a progressive reduction of the site’s electricity bill, with ROI in one year. Without any fancy equipment, without any green label, just good operation practice.
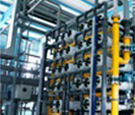
One of our clients was among the top 10 energy users in their industrial zone. Pressed to reduce their consumption, they decided to install meters to track consumption over 6 months, analyze it and prepare an action plan. A technical assessment was conducted and international benchmarks were also used. Most of the actions were no “rocket science” but simple, focused, improvements, inexpensive in terms of investment: changes in automation rules, review of equipment design, changes in equipment connections, linking management bonus to energy savings, etc… which generated close to 20% energy savings, a major part of which were traced back to installation issues (i.e. over 5 years before).
Keeping the design performance alive
How to keep the designed performance “alive” throughout the life-time of your building? The first step is obviously to understand the impact that operation and maintenance is going to have, which is enormous, as shown above.
There are tools too, which can be used, the same tools which were in fact used during the design and construction stage: technology and green labels. As explained, both seem to have a near-magic effect on building owners: this can be used to make operation better.
The magic of labels

Operation and maintenance labels were created after design & construction labels, when it was realized that green buildings turned “brown” if not operated properly. LEED has its Existing Buildings: Operation & Maintenance rating system. The Chinese label GBL also includes operation criteria. Generally, rating criteria cover the various building management aspects: cleaning and maintenance issues (including chemical use), recycling programs, exterior maintenance programs, measurement and monitoring, and systems upgrades. Seeking operation & maintenance certification will help motivate your team with clear goals and further enhance the image of your properties.
The magic of technology
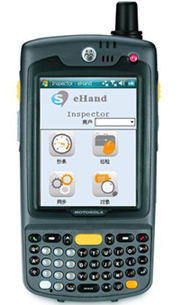
Using high-technology as a driver for operation and maintenance improvement has always been the key to Siveco’s business model. Unfortunately, as shown in our examples and in the many audits we have conducted over the years, most technology/IT projects fail. Those failed projects all have one thing in common: technology for the sake of technology, IT implemented by IT people. Instead, technology should be seen as just a tool, in the hand of operation people, not IT. Furthermore, technology is often used in the hope to run a facility without the maintenance people – on the contrary, we believe it should be used to enhance the ability of the people to maintain their facility. This approach has proven to be very successful especially in China, where hi-tech is a powerful motivator and a relatively easy purchase decision. The latest mobile solutions introduced by Siveco are perhaps the best example, as they ensure preventive maintenance actions are done, assist the technicians in his daily work and enable a constant flow of information from the field to decision makers.
For more information on how mobile technology can be applied to enforce proper management practices, see this month’s case study “Taking maintenance engineering services to new heights with Siveco’s cloud-based” and other article on “Optimizing field service operations with Motorola’s handheld devices”. Interested readers may also want to refer to one of our earlier articles “Intelligent buildings for intelligent owner” (published August 2010 in our newsletter), which goes deeper into some of the topics.
Facility management services: a light at the end of the tunnel
Often thought to solve all problems, outsourcing soft and hard services to a FM company often doesn’t solve anything – apart from perhaps reducing direct cost and headcount. Only cost is outsourced, not risk, which the owner retains. FM service providers in China face exactly the same issues as facility owners, in terms of skills shortages, implementing good practices, lack of preventive maintenance concept etc. Due to intense competition, service suppliers often operate on very low margins that do not allow them to invest in improvement, creating a vicious circle. The emergence of ESCO business is changing the landscape, the service supplier taking a risk in the operation of the property, in exchange of better margins.
A major source of improvement may be coming from large Chinese property developers and their FM divisions. Cash-rich, with a long term vision (that of the owner), access to the best human resource pool, these companies are able and willing to invest in improvement programs, making use of both tools listed above: the green labels and technology. After a period of trial and errors, more and more of those giants are making steps in the right direction. The Chinese government, as the largest of all property owner and the one with the longest-term vision, is also moving in this direction has seen with the 12th five-year plan. China has more green projects in progress than any other country.
The scale of this effort will forever change the industry, in a way no international investor can even dream of. We already see today local FM suppliers at the forefront of innovation (see our customer story published a few months ago: Changcheng Property in 3G times). This is, again, “maintenance with Chinese characteristics”: history in the making in the property management market.