Prepare early: turn risk into opportunity
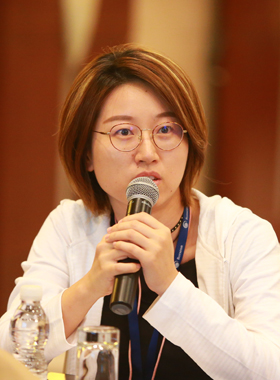
This Reliability article was contributed by Shirley Xuan, Siveco’s Environmental Protection Industry Director. It was previously published in Hazardous Waste Frontline (危废前沿), an official WeChat account aimed at creating the first technology and operational exchange platform for China’s hazardous waste industry. The English version was translated from the original Chinese.
Characteristics and maintenance status of China’s environmental protection industry
The current environmental protection industry presents such characteristics as: massive investments, rapid construction, difficult commissioning and lack of skilled personnel. The industry as a whole looks flourishing. Environmentalists’ social media posts of are full of signing ceremonies for all sorts of new contracts, public-private cooperation gatherings and handsome poses traveling around the world. However, no matter how long the free flow of capital continues, the huge amounts of investment and construction come with the same conundrum that all asset-intensive industries have to face: how do group companies control the operational risks of so many subordinate plants? How can individual plants manage their maintenance better?
Unlike ordinary industrial enterprises, the environmental protection industry is closely related to people’s livelihood. If an accident occurs, it will cause negative social impact. However, safety is seldom associated with daily operation and maintenance and with the foundation of operation and maintenance, which is asset management.
As industry experts, we have inspected many environmental projects. Most of the projects, especially new projects and group companies share these characteristics:
–
The construction period is very short, but the commissioning phase is very long. Some projects will remain continue under semi-commissioning status for a long time after start-up, with many leftover problems, during which maintenance cannot be performed normally.
–
It is very difficult to find experienced technicians for new projects; talents have to be found in other related fields such as the chemical industry. For acquired assets, the original management team tends to be very backwards.
–
Most of the group companies are “small headquarters, large plants”: most of the technical management standards are implemented by each site, beyond the reach of the central technical team. At the end of the year, headquarters realize that improvement costs at the plant have reached ridiculous amounts.
–
Technical management methods are lagging behind those of other industries. Most plants do not have IT tools, most only use paper forms, while the best plants use traditional MIS system (“Management Information System” originating from small capacity power plants) or OA systems (“Office Automation”), lacking specialized management tools.
Stones from Other Hills May Serve to Polish the Jade of This One
As part of the “2017 Maintenance in China survey“, a joint research study conducted by Siveco and academic partners, we identified and analyzed the features of companies with comparatively good management among asset-intensive industries. It is not difficult to see that these enterprises share common traits in specific areas:
–
Having a maintenance strategy aligned with the company’s sustainable development, and raising maintenance to the level of risk management.
–
From the beginning of project construction, paying attention to the definition and collection of basic technical data, preparing for operation and maintenance.
–
Using professional information tools to manage maintenance, holding regular maintenance meetings and conducting multi-angle analysis of historical records during meetings.
–
Paying attention to the skills level of front-line employees and continue to track their growth
–
……
A good start is half of the success: start maintenance preparation during the construction phase of the plant
The environmental protection declaration of “Lucid Waters and Lush Mountains are Invaluable Assets” has led to a proliferation of new players in the environmental market, including solid waste, with a positive scale effect.
Compared with other asset-intensive industries, it has only begun to take maintenance into account after more than ten years of history. Now China’s solid waste industry has an opportunity to create a truly Smart plant supporting the full lifecycle management of the plant from the construction phase.
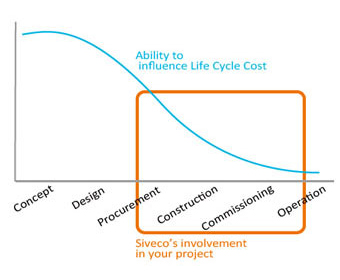
For a new plant, the initial stage of construction is always full of challenges. Maintenance preparations are often overlooked during commissioning and startup. People often feel that maintenance has not yet begun and even the recruitment of maintenance teams is often late. In fact, there may not be much actual maintenance work to be carried out at that time, but there are very critical activities that needs to be coordinated at the global level for the operation and maintenance of the plant, that is, the preparation of maintenance data.
Maintenance data preparation refers to the creation of the plant’s functional location and equipment structure for the owner, including criticality, technical parameters, technical documentation, spare parts, warranty, contracts, preventive maintenance instructions, etc. In the West, “maintenance engineering” is an engineering discipline, of which maintenance data preparation is the key activity. The maintenance team needs to sort out all the data critical for later operation and maintenance, and the contents of the operating manual are translated into a usable technical database to build the operational foundation of the smart factory. In the information age, the implementation of this task is usually carried out with the support of information tools (maintenance management system, also called CMMS), and is gradually advanced during the different stages of plant construction.
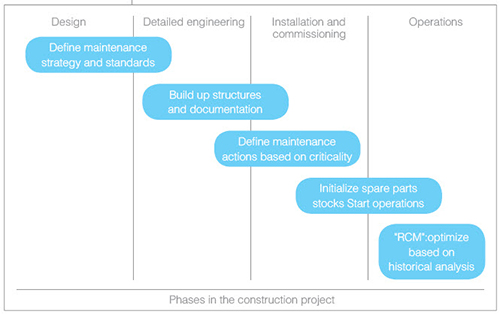
When the maintenance preparation plan can be implemented during the construction phase, it can prevent unwarranted downtime during the operation, greatly reducing maintenance cost, effectively eliminating the repeated occurrence of similar failures, saving the owners millions in annual expenditures. Keeping long-term sustainable development in sight can help accelerate equipment into the service phase, stabilize and extend the life cycle of assets, and continuously optimize the investment of the owners.
Especially for large group companies, once this standard technical data management method has been established, it can quickly be applied to all new projects, with a more impressive effect of scale. By then, the establishment of a standardized technical database in the first few projects can help benchmark equipment performance across sites, provide technical reference for future project design and equipment selection, and in turn can promote standardized work practices during the operation and maintenance phase, gradually forming the maintenance management strategy that can be quickly copied and promoted. At the same time, those tools can be used to cultivate in-house technical talents to finally achieve world-class operation and maintenance management.
As China’s industrial development enters a new stage to achieve the ultimate goal of “China Dream” and “Made in China 2025”, it is necessary to continuously enhance the value of the Chinese manufacturing industry and to transform the traditional extensive management model towards “Automation”, “Intelligence” and “Sustainability”. As mentioned at the beginning of this article, in the Chinese environmental protection industry, we have the opportunity to witness a group of truly Smart factories that carry out the full lifecycle management from the construction phase, with the ability to export this excellent management experience to the “Belt and Road”.
Perhaps this is the reality of the China Dream.