Integrating FMECA in your Maintenance System
Introduction of FMECA
Most companies have a Preventive Maintenance plan in place, which incorporates regulatory demands (such as mandatory checks), suppliers’ recommendations (from the equipment O&M manuals) and best practices accumulated in the organization (similar plants in the group, experience of the maintenance teams).
Developing a Preventive Maintenance Plan from scratch or optimizing the existing Preventive Maintenance Plan is a challenging task, which requires identifying potential problems, estimating their impact and designing actions to prevent their occurrence. A systematic approach is required, the best-known approach being “Failure Modes, Effects and Criticality Analysis” (or FMECA) or sometimes simply FMEA.
The FMECA is a tool used to systematically analyze potential component failures, identify their causes and effects, so as to define the necessary preventive actions to improve the reliability of facilities, the quality of outputs, the safety of operations, etc.
This article will show, through a practical example of a client project, how FMECA can and should be integrated into the overall maintenance system and its supporting IT system (the CMMS or Asset Management System).
Implementation steps
In this article we take the FMECA management module built into the Baosteel Gases EMM system (Coswin 8i) as an example to introduce the application of FMECA in the actual enterprise quality management system in detail. The FMECA module is fully integrated in Coswin 8i, making use of all existing functionality of the system, such as equipment structures, technical data, failure history, preventive maintenance plans, etc.
1.
First in the module’s basic data, are defined the severity, probability and degree of detectability of potential failure modes in the system, in order to facilitate the comprehensive analysis and evaluation of failure modes. This is shown below:
Severity SEV:
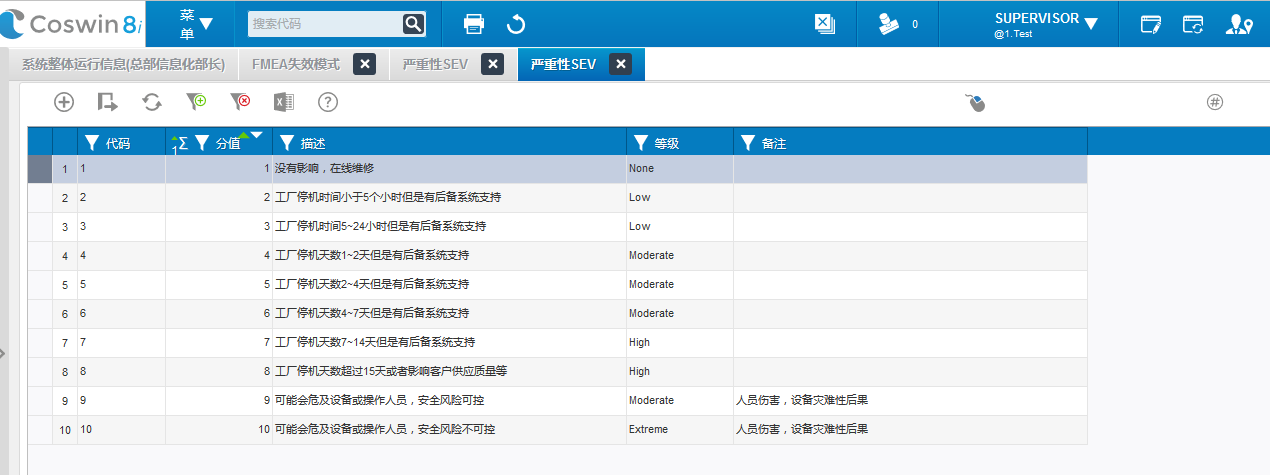
Occurrence probability OCC:
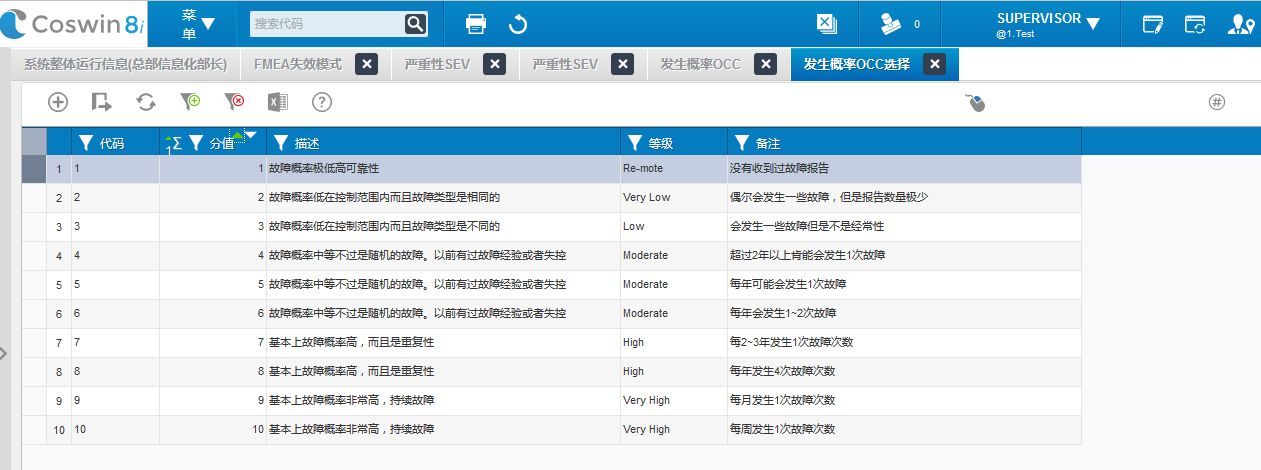
Degree of detectability DET:
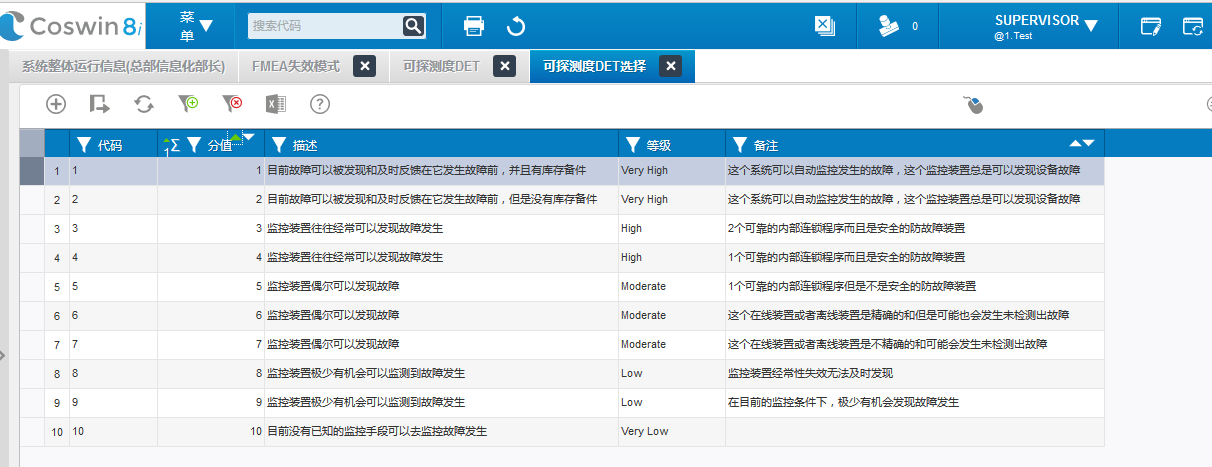
2.
The module then supports the FMECA process, allowing users to list all potential failure modes, consequences and causes of failure for key parts of the equipment, then to determine the severity, occurrence probability and degree of detectability of each failure mode.
The following figure shows the analysis for an air filter system with three main parts:
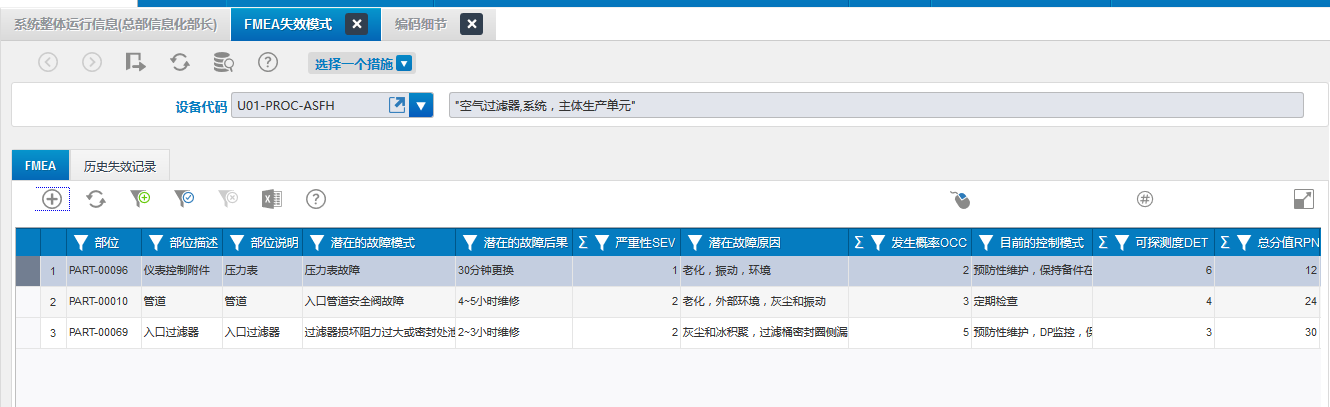
Select a part, double-click to open, you can see the details of this FMECA:
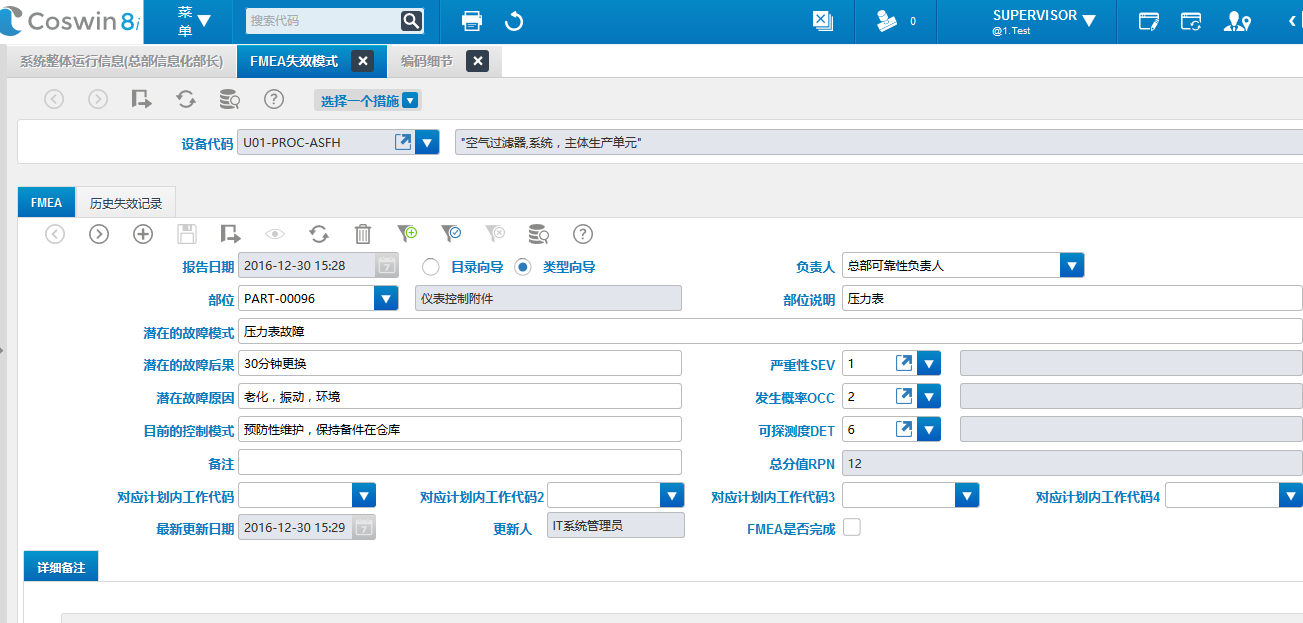
You can also click the “
” button to add a new part in the FMECA for failure mode and consequences analysis:

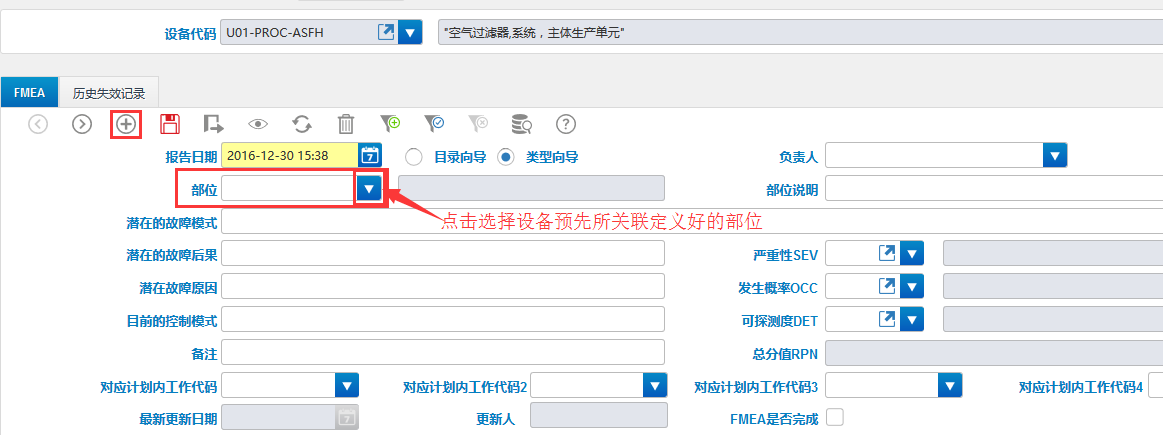
Since the module is fully integrated in Coswin 8i, equipment parts can be directly selected from parts in the equipment database.
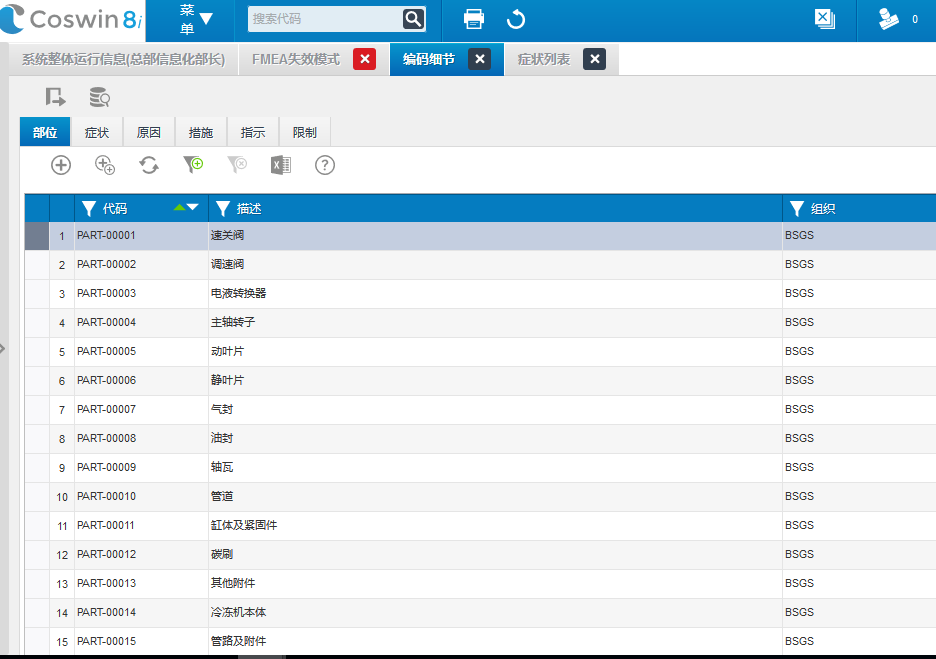
In the FMECA module, information is added pertaining to failure modes, consequences, cause, the current control mode, the severity, occurrence probability and degree of detectability as shown below:
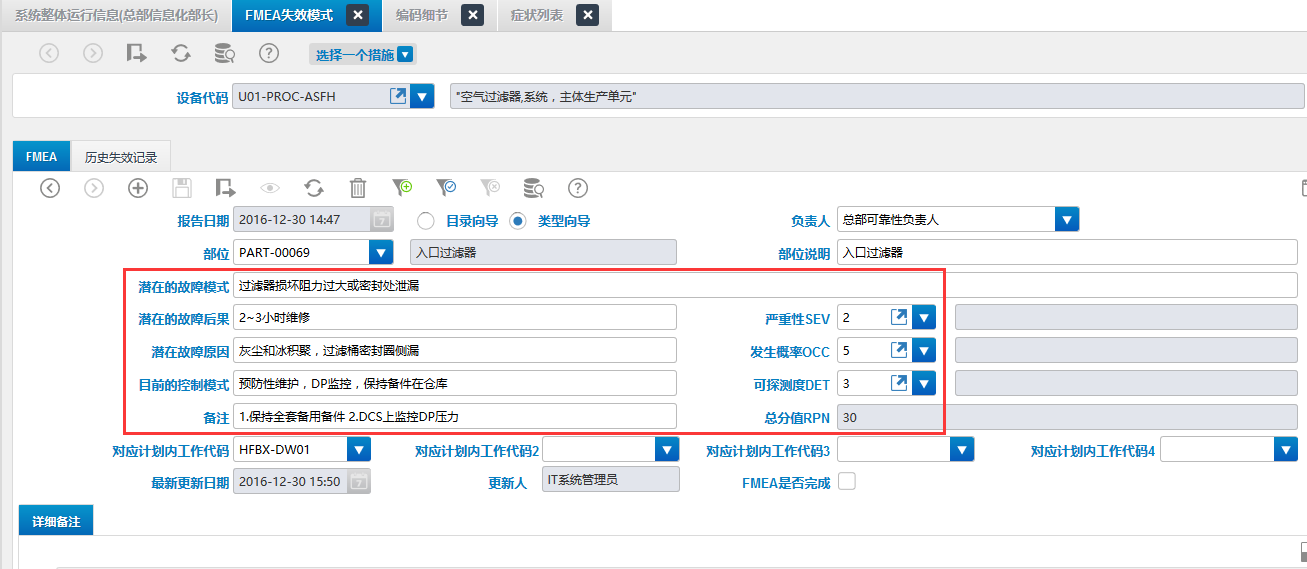
3.
Based on the FMECA analysis, the corresponding preventive maintenance plan can then be formulated. For example, the self-cleaning filter is routinely checked with a frequency of one month:
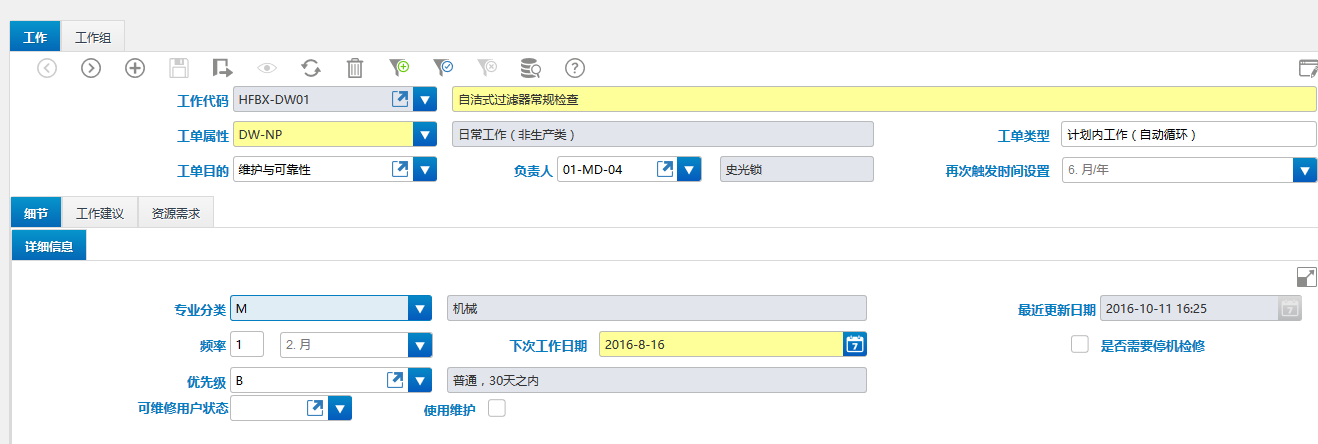
The work code is associated with FMECA to facilitate following up preventive maintenance. Since all data is interlinked in the system, advanced analysis is possible, so as to support a continuous improvement process (RCM or equivalent) based on a FMECA fed by systematic feedback from the field.
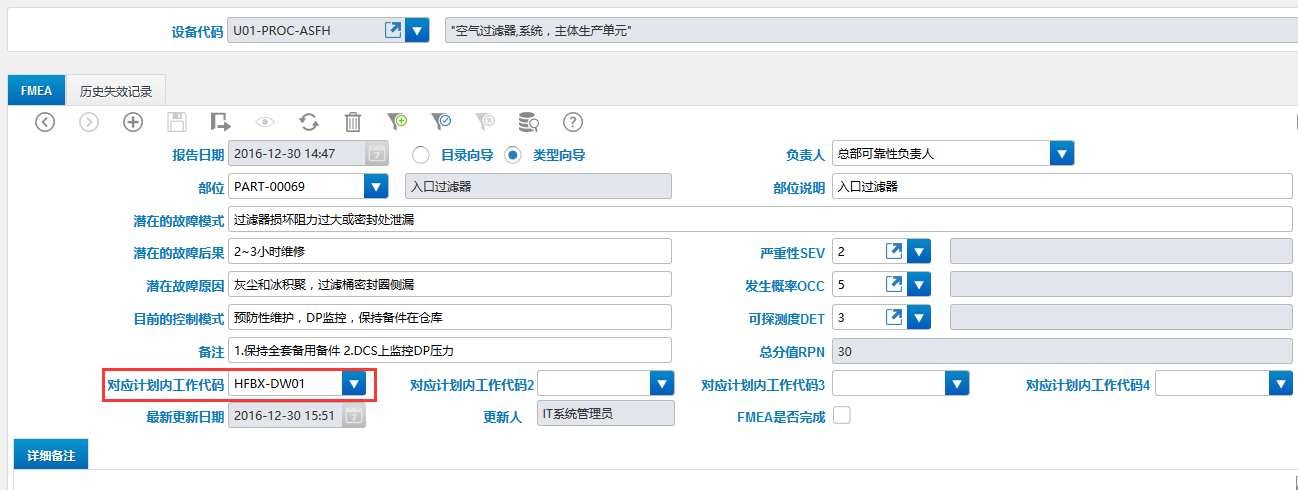
The resulting preventive maintenance plan will automatically trigger the generation of maintenance work orders in the Coswin 8i system, execution is then performed with support from the bluebee® mobile solution, ultimately reducing the occurrence of equipment failure, thus achieving the purpose of preventive maintenance.
Why integrating FMECA inside the Maintenance system?
Quoting from above: “Since all data is interlinked in the system, advanced analysis is possible, so as to support a continuous improvement process (RCM or equivalent) based on a FMECA fed by systematic feedback from the field.”
Indeed, more often than not, companies use Excel sheets or paper forms to support the FMECA process. FMECA however requires a relational database, considering the complexity of inter-related data and the sheer amount of technical data in large plants.
Some companies chose to implement a separate specialized FMECA tool, which often prove too complicated (such tools are designed for aerospace or military applications of FMECA, or for product-FMECA which is a similar yet different process than manufacturers apply to products, not production equipment). They are not integrated with the CMMS or rely of importing history files: there is no proper feedback loop from operation.
Instead, the Siveco approach of an integrated FMECA module described above is compliant with continuous improvement and the feedback loop philosophy of modern management systems (such as ISO 55000 Asset Management – now also a Chinese standard under the name GB/T 33172资产管理综述、原则和术语).
This is made possible by flexible Coswin technology: the FMECA module does not require any software development, it is a standard Coswin 8i “free module” adapted to the specific needs of clients. For more on Coswin flexible configuration, see this article. Another example of application of Coswin free module was for WCM/TPM, as shown in this article.