How to measure the success of a CMMS implementation
It is often said that maintenance digitalization projects have a very low success rate. Often managed by IT, most CMMS or EAM projects result in systems that maybe work from a technical standpoint (users can login and access the various functions) but cannot be used in practice (data not accurate, no useful reports, inconvenient user interfaces). Obviously such system does not help the company achieve any industrial improvement.
This has been a recurring theme in previous Siveco articles: in-depth audits of companies having implemented IT solutions for maintenance or asset management consistently show major gaps between their strategic needs (as per ISO 55000) and the actual coverage achieved by the system. Indeed, virtually all EAM projects are driven by IT departments and conducted by IT vendors with limited understanding of O&M, hence this focus on non-strategic “administrative” aspects of the projects.
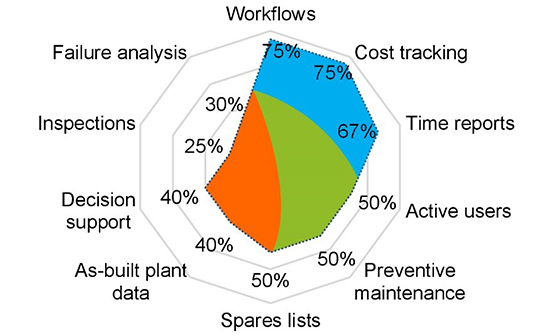
Typical coverage of “EAM” systems (achieved / goal in %)
The results of our Maintenance in China survey (last edition in 2017) give insights into what best-in-class companies (those with the best performance) have done to obtain such performance, as summarized in this previous article “Improvement from CMMS: what do best-in-class companies do“.
As far as Siveco is concerned, our yearly customer satisfaction survey (part of our ISO 9001:2015 quality management process certified by Bureau Veritas) specifically inquire about our customers’ user experience and improvement or benefits obtained from working with Siveco.
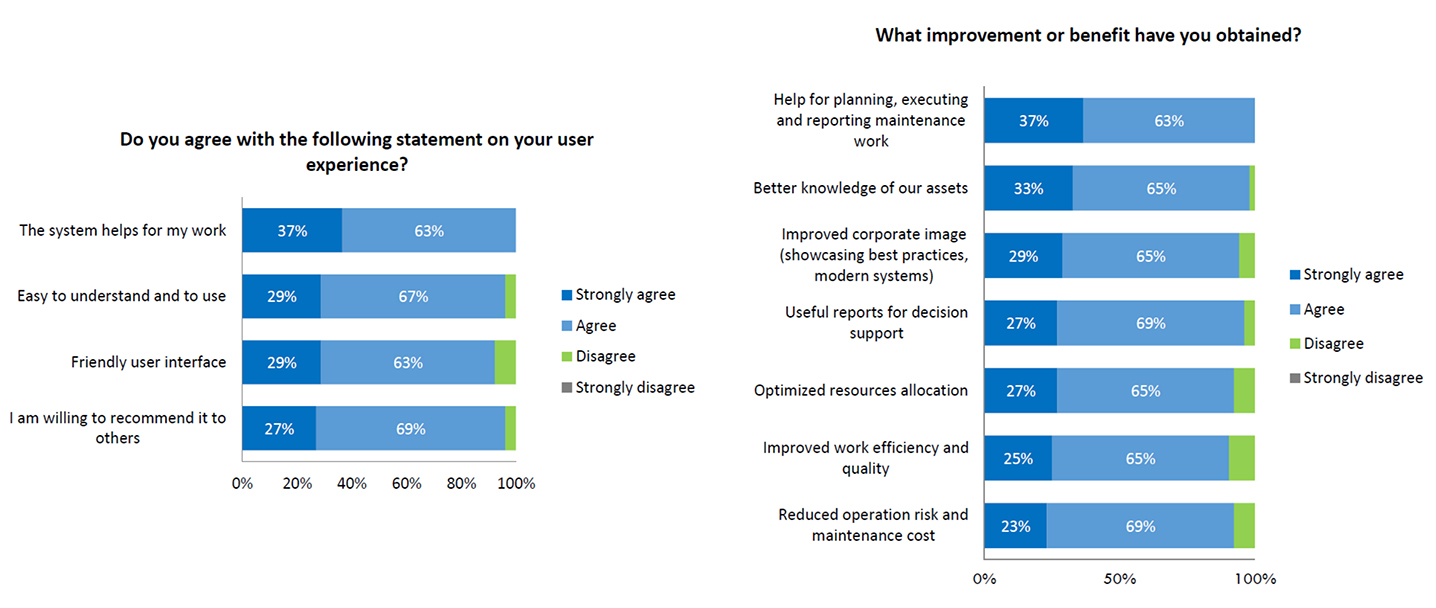
Results from Siveco China’s 2019 customer satisfaction survey (audited)
In conclusion, we believe CMMS success must be measured by direct feedback from users and the industrial improvement achieved, not by whether or not the IT department thinks the system is technically working. Experience shows that our approach consistently delivers results and year-to-year continuous improvement, which is the only goal of maintenance digitalization.