Don’t settle for services, demand results from Condition Based Maintenance!
This article was contributed by Areva 01dB-Metravib. See the Press Release announcing the partnership with Siveco China.
Case study in a paper mill
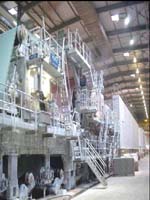
This article is based on the experience of a paper mill located in the South of France. The company aimed at increasing its production output without adding capacity, though a simultaneous increase in production speed and machine availability. At the same time, direct maintenance cost was to be cut down, primarily by decreasing bearing replacements and reducing oil consumption. An extensive audit assessed the feasibility of the project and a performance-based contract was established, covering the implementation of systems and the necessary follow-up services.
The partners
With 25 years of experience in Condition-Based Monitoring (CBM) 01dB-Metravib, a subsidiary of energy giant Areva, is an established partner for the setting up and enhancement of predictive maintenance programs in the process industry. With a comprehensive portfolio of vibration collectors and analyzers, sensors, onsite services and remote services, 01dB-Metravib reduces the overall maintenance cost and increases production uptime.
Siveco Group, on the other hand, boasts another 25 years history as the largest vendor of Computerized Maintenance Management Systems (CMMS) in Europe and a leading maintenance consultancy with presence – either direct or through consulting partners – all over the world.
The integration of 01dB-Metravib’s OneProd system with Siveco’s CMMS Coswin into a common web-based platform allows the centralization of all maintenance-related data, thus optimizing the expert resources needed. In perfect complement of 01dB-Metravib’s specialist tools, Coswin provides an overall plant management tool, a shared know-how database across all disciplines, ensuring the follow up of improvement actions. For both customer’s maintenance personnel and 01dB-Metravib or Siveco specialists, all the necessary maintenance information is just one click away… and from anywhere in the world.
A joint, result-oriented and pragmatic service approach has been developed, making use of the two partners’ complementary skills and capabilities. Return on investment (ROI) has proven to be in most cases just a few months, explaining why companies of any size are adopting CBM whatever their culture or the cost of the local manpower.
A practical application
A practical application is shown below for a centrifugal pump monitored on a periodic basis. An identical installed spare is ready to take the load may the main pump fail or be stopped. Data collection, analysis and their integration in the overall maintenance knowledge base are performed using the OneProd-Coswin platform.
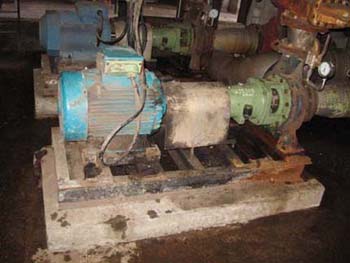
Fig. 1: The pump in our example
During a regular check, the operator observes an abnormal increase of vibration on the pump. He immediately launches a more detailed analysis, which reveals several key points:
–
Trend analysis shows a sudden increase of vibration level on the two bearing cases (see fig. 2).
–
A time-plot of the signal reveals regular shocks (fig. 3). Such shocks are characteristics of wear and tear of the inner ring of 6411 ball bearings, as shown by the spectral analysis (fig. 4).
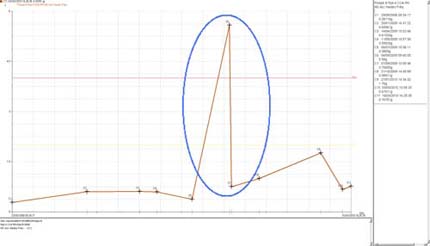
Fig. 2: vibration level on one of the bearings (high frequencies 2,000-20,000 Hz)

Fig. 3: Time signal showing periodical shocks on bearing 4 (opposite to coupling)
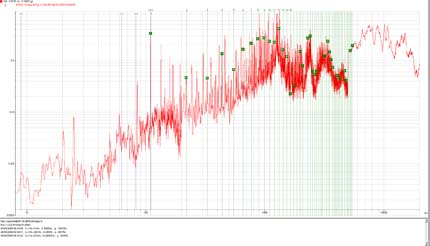
Fig. 4: harmonic phenomenon characteristic of inner ring failure
After careful review of the result, the maintenance team decided to dismantle the bearings as soon a possible. The operation was planned to avoid impacting production and the backup pump was put into operation.
Figure 5 shows the damage of the dismantled inner bearing, on the opposite side of coupling, which confirms the diagnosis resulting from vibration analysis. A degradation of the pump seal is also seen.
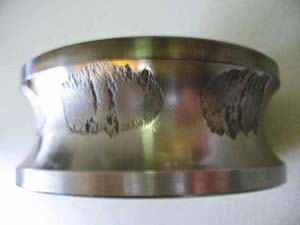
Fig. 5: inner ring of 6411 bearing
For this pump, we concluded the deterioration of the bearings happened further to water leaking into the bearings. This type of failure is typical of pumps, subject to permanent risk related to water tightness.
Overall result
This specific case detailed above proved the capability of the OneProd System to provide accurate diagnosis before repairs. It also shows the benefit of early detection (before failure) that well-implemented condition-based maintenance provides: in this case, the maintenance operation was planned and carried out at the best possible time without any production loss.
The chart below shows the paper mill’s improvement in production output and unscheduled downtime over a four year period.
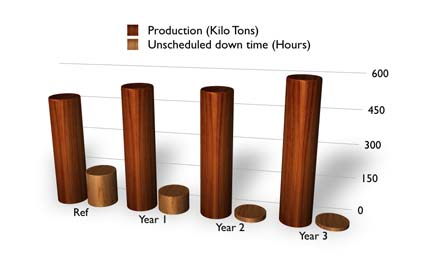
Experience in the paper industry
Both partners boast extensive experience in the pulp & paper industry all over the world. Customers include global papermakers such as Norske Skog, International Paper, ArjoWiggins, Mondi Packaging, SCA, UPM, etc. as well as many local players.