The potential for improvement in FM
Throughout the article, we will illustrate our points with real-life stories from a large, unnamed, retailer operating in the Chinese market. This retailer is rather typical of large multi-site facility owners in China and similar situations can also be found in smaller companies. |
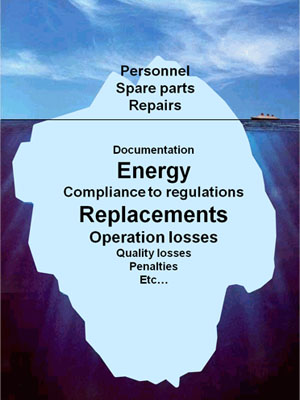
Fig. 1 – Typical “iceberg” of maintenance costs
Our large retailer experienced an incident that raised awareness of maintenance among the management team, composed mostly of experienced China managers: one of the stores had to close for the day, because of an electrical failure with the main transformer. The backup diesel generator did not start (it had never been tested). Losses: one full day of business, all the food in the refrigerated areas, not to mention the company’s image. This added up to four times the store’s annual maintenance budget… The failure was later traced back to a small electrical component that had been replaced with a cheaper locally-made part – a saving of a few hundred RMB. Audits conducted at other stores also revealed poorly maintained HVAC (very dirty coils and filters) were the norm, in spite of up-to-date maintenance records. Clogged filters could add 10-20% to the HVAC electricity bill, which represents close to 40% of the total (see Siveco Partner article in this newsletter). The resulting losses were estimated at two thirds of the annual maintenance cost. A more in-depth facility assessment was conducted in another location, revealing abnormally fast aging of the facilities, with a need to replace a number of major equipment and to launch preventive maintenance routines. The company decided instead to run the store “to failure” and to refurbish the entire facility as part of a coming expansion project. In effect, the indirect cost of poor maintenance (early replacements) was hidden in construction budgets, a very common phenomenon in China, where companies have historically experienced fast growth. |
Our retailer’s early response to maintenance issue was to look for good facility managers at store level and to appoint someone at headquarter to coordinate activities. Recruiting such profiles proved to be impossible… and the best resources ended up working instead on new construction projects, to support the group’s rapid expansion. A third-party engineering company was appointed to design preventive maintenance procedures for one of the stores, with a paper-based maintenance system to record completed tasks. Maintenance plans remained in their folders and were never put into use. Another project was then conducted on three pilot stores, still under construction. The facilities were entirely documented in a centralized maintenance management system setup at headquarter. Using existing know-how from technical teams and equipment suppliers, the system helped train the stores technical teams before opening. From day one, failures were recorded and analyzed on a regular basis, a seemingly simple task that delivered quick results: in one of the stores, after only 4 weeks of operation, analysis showed that most problems were related to lifts and were the responsibility of the supplier (poor installation, bad quality of parts used). The pilot project raised awareness of maintenance across the entire organization, to store managers, financial managers and the top management team and was considered a first success. Based on this first achievement, vendors of sophisticated monitoring systems and equipments convinced our retailer to stuff their new-built stores with sensors and to rely on an external control center. While the initial improvement project was designed to increase the know-how of maintenance personnel and to support better management decisions, with the help of a simple technological tool, this new project focused on reducing dependence on “incompetent technical staff”. By relying on technology suppliers, the fundamentals of maintenance had unfortunately been overlooked. The high-tech sensors suffered high failure rates: without in-house skills for such repair, the retailer tied themselves to a specific supplier for years to come. The external control team, involved in all procurement decisions, faces risks to become a new “corruption central”. A vendor’s dream come true, but a true maintenance nightmare for our retailer! Our partner article also touches on this subject: the intelligent building vs. the intelligent owner. |
Time will tell how the situation evolves for our retailer. Our advice is to go back to the basics, to focus on helping in-house managers raise their skill level, rather than rely on third-parties with their own agenda. Decisions to automate stores should be gradual, based on careful analysis of their impact (positive and negative). What is your iceberg of FM costs? Contact us for an audit! |