Getting the most out of SAP PM
Introduction
Many large-scale multinationals have chosen to implement SAP across all locations and business processes. This is particularly true in the petrochemical industry, with virtually all majors using SAP. Somewhere down the line, these companies are then faced with the need to implement the SAP Plant Maintenance module (“SAP PM”) to support their Chinese operations.
While deploying SAP PM anywhere in the world involves challenges, most notably the high cost of implementation and ongoing support and the usability of the system for plant workers, these challenges become especially acute in China, where the specificities of the local maintenance market come into play.
SAP decisions are made at board-level and suffer no discussion afterwards. Throughout this article, we assume there is no alternative to SAP: replacing SAP is out of the question. On the contrary, the question is how to get the most ROI out of it, in the specific context of maintenance in China.
Some characteristics of SAP PM projects in China
Due to the very nature of SAP, projects are driven by finance and IT departments. This, although sometimes frustrating from a plant management point of view, is unavoidable. It is in fact a necessity, considering the complexity of the system.
With IT running the show, the customer is requested to provide its knowledge of operations, first of all to help design and validate the “blueprint” defining how the system should be implemented. While IT suppliers in other countries may have a significant industrial experience and, conversely, plant managers may also be well-versed in IT, this is far from true in China where such versatile resources, especially in the area of plant maintenance, are almost impossible to find. Not to mention the acute shortage of SAP PM consultants: all of them with IT background, often recently recycled from “more difficult” SAP modules like MM (understand: “maintenance is simple”), not familiar (and often unwilling to learn) about real-life maintenance. Most are anyway already engaged in giant projects such as those of State Grid and Sinopec, leaving smaller customers (“smaller” as in below the 100 million RMB project range) to fend for themselves… Such is the market we find ourselves in!
As a direct consequence, customers are faced with IT consultants who are barely able to communicate with their maintenance team: SAP is often implemented based on a standard blueprint, taken from elsewhere (in the best case, from corporate back home) or written entirely from a finance or IT perspective, hence focused on administration and cost control, without relation to actual maintenance improvement needs (where the true ROI potential lies). More often than not, the customer’s maintenance team has very limited ability to influence this blueprint, as they lack similar experience.
This typically results in never-ending projects, spanning multiple fiscal years (in practice leading to unlimited budgets, as the implementation is spread across as many budget years as needed). The initial objectives of the project (when there was one, other than “we must deploy SAP”) have long been forgotten. The whole chain of SAP consultants is then offered a free ride: in-house consultants, implementation companies, contractors and freelancers (sometimes moonlighting from another project or company), none of them being able to take responsibility for the project. Industrial managers on the customer’s side are left to deal with this extremely frustrating experience.
In the end, failure is blamed on the customer “lacking maturity”. We have seen the failure of a 100-million RMB rollout blamed on the company being disorganized (probably true, but not at all unexpected for a large Chinese asset-intensive enterprise with no previous exposure to such projects): in the end, the customer agreed to spend a few additional tens of millions RMB and has been doing so on a yearly basis ever since. This is the true miracle of SAP! To reformulate the question that we think plant managers should ask themselves: how to use this miracle to fulfill our own improvement objectives?
What to do?
First of all, if that is your company policy, acknowledge that SAP PM is the only tool at your disposal. Do not fight: the heavy politics involved may drain your energy (although in one case we have seen a reluctant plant manager getting promoted to a nicely paid SAP project manager position!). Realize at the same time that it is a very good tool, fully functional: corporate knew what they were doing, although neither plant management nor China was their priority.
Second, understand that the role of the various SAP consultants will be limited to IT – setting up, configuring the system, guiding you through its intricacies, making it work in the IT sense. This is necessary, considering how complex the whole thing is. Let them enjoy the unlimited budget provided by corporate to make the tool work, as you are going to need it! Do not, however, expect more than that from the consultants.
Based on a long experience dealing with maintenance projects in China, Siveco has developed two angles of approach to ensure the SAP implementation can achieve its objectives, on time, and to obtain ROI just like any other engineering project. Those two angles are summarized below.
Add a usability layer to SAP
Depending on the situation, this consists in adding another layer of software, designed for maintenance engineers by maintenance engineers, acting as a “user interface”. Solutions designed by Siveco include the smartphone-based bluebee® and the tablet PC-based Mtv, both running seamlessly on a SAP platform.
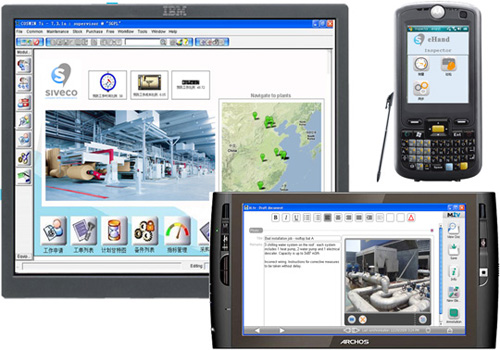
The benefits of this approach are:
- A strong involvement of your maintenance engineers in the project, while they were often not really involved in the SAP implementation, providing an opportunity to work on maintenance improvement.
- A considerably improved usability of the system by technical team, ensuring consistent and high-quality input (failure reports, work completion, etc.) into the SAP database, as well as more usable output (reports, know-how, diagnosis support etc.).
- No conflict with SAP, in the sense that the proposed features (with strong focus on mobility) do not exist in SAP. This is usually proposed as an “inspection management mobile solution”.
This approach should however be introduced with care, as the IT department will have to be involved (software and hardware, interface with SAP PM). We have sometimes experienced strong resistance by IT (which could take the form of a quote for interfacing services worth more than the project itself, immediately killing the deal).
Siveco’s involvement as “owner’s engineer” in the project
Siveco will involve in the SAP PM project in a role usually devolved upon the customer: project management (or assistance to), design of blueprint, data collection, definition of reports and KPIs, coaching and regular audits, and related improvement projects (e.g. the reorganization of spare parts inventory or workshops). Siveco’s engineers are all maintenance specialists, operational from day one without any learning curve. Siveco boast China’s most successful track record of delivering maintenance improvement through implementing maintenance systems. Unlike traditional SAP projects, but in line with normal engineering practice, the scope of work is clearly defined and performed under the responsibility of Siveco, with back-office support in Shanghai (data processing, specific expertise, access to centralized computer system and resources).
The benefits of involving Siveco are:
- A clear definition of your plant maintenance goals and the alignment of the SAP PM implementation with them, from blueprint to implementation and long-term follow-up.
- The streamlining of services offered by the various implementation parties, leading to a direct cost reduction and shorter project time. This is achieved through strong project management, a clear definition of each activity and quality control by experienced engineers familiar with both SAP PM and maintenance.
- High quality and relevance of master data uploaded into SAP PM (functional locations, equipment hierarchy, bill of materials, task lists, etc.) including the codes used (based on international standards) and the data itself.
- A better utilization of the system, through coaching of the users by maintenance experts, more particularly during regular maintenance meetings (planning, analysis).
Allowing customers to achieve excellent ROI, this approach is also easier politically, as the services provided do not encroach on SAP services: this should be seen as a pure engineering project, Siveco engineers will not touch the system itself other than as end-users. The cost of such services is marginal compared to the total SAP implementation cost. For companies already using SAP PM or in the advanced stages of a project, Siveco’s involvement can also take the form of audits (see Arkema case study in this newsletter).
The two angles of approach can obviously be combined depending on actual needs and, mostly, on the political the situation on the ground. Contact Siveco for advice!
Conclusion
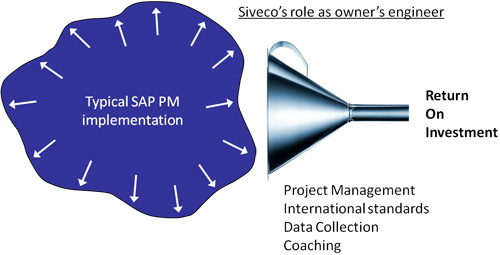
In a market like China where most managers are not familiar with IT projects and IT consultants totally unaware of maintenance realities, the two approaches described in this article can provide tremendously ROI with very little additional cost. In fact, the cost of Siveco’s involvement will most likely be recovered immediately by the resulting reduction in additional services, rework and unexpected support required by the various implementation companies. The cost of additional software layers, if needed, will also be lower than the equivalent SAP user licenses. All it all, this also demonstrates that SAP projects, although miraculous in many respects, can (partly) be managed like engineering projects, with clear goals, deadlines and measurable ROI!