Storage terminal takes risk & asset management to world-class level with bluebee® cloud
LBC Shanghai Shipping Terminal
LBC Shanghai Shipping Terminal is a joint-venture between LBC Tank Terminals (Belgium) and China COSCO Shipping Group. The company operates a 74,200 m³ bulk liquid chemicals and petroleum products storage terminal in Shanghai’s Waigaoqiao area.
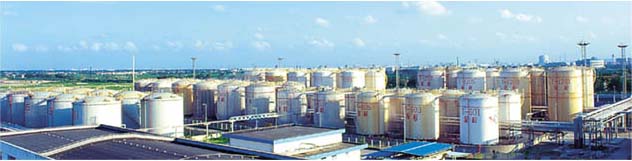
The terminal facilities include 62 tanks from 650 to 3,000 m³ capacity for the storage of chemicals, mineral and vegetable oils. Tanks are equipped with heating, cooling, blanketing and vapor recovery. Infrastructures include ten trucking loading bays, five drum filling stations, two 60MT weighbridges, 120MT per day waste water treatment unit, nitrogen system, steam, radar tank gauge, third-party laboratory etc.
In terms of safety, the terminal and tanks are all equipped with foam line and water sprinkler system, all fully automated. Two diesel fire pumps each almost 800 m³/hour taking in fresh water from the Changjiang River. Security is 24/7 with two technicians on duty at the central control room to monitor product temperature, alarm system etc.
Project background
In recent years, due to various accidents in storage terminals, local authorities have strengthened regulations and stepped up law enforcement. Accidents can often be traced to human management and operation problems. At the end of 2016, In order to improve the safety of operation as well as the standard management of facilities and equipment, the top management of LBC Shanghai Shipping Terminal decided to further enhance the terminal’s risk management processes.
The company selected Siveco China and its bluebee® solution after an evaluation process including technical discussions, system demonstrations and customers visits. Siveco China, founded in 2004, is the country’s largest maintenance consultancy and a pioneer in the development of Maintenance 4.0 technologies, with a focus on mobile solutions “for the worker of tomorrow”. Based on long experience of “maintenance with Chinese characteristics”, Siveco has developed a unique approach to combining maintenance consulting and software tools, particularly well-suited to the needs of LBC Shanghai Shipping.
Siveco had previous experience working for storage facilities in China, such as Tianjin Shell Petroleum Storage & Distribution, a 200,000 cubic meters oil storage facility located in the Nangang Industry Zone. Siveco clients also include Hanas New Energy (LNG), Baosteel Gases and Baida Air (industrial gas supply) and numerous utilities (waste, water and energy), an experience which LBC Shanghai Shipping Terminal considered highly relevant.
A Software-as-a-Service (SaaS) approach to risk prevention
The project was designed to take the company through all the steps of implementing a sustainable risk prevention management system, in compliance with the ISO 55000 Asset Management and ISO 31000 Risk Management standards, with support from Siveco’s bluebee® solution.
The terminal’s technical personnel would use the bluebee® mobile app on explosion-proof ATEX-certified Android phones, also provided by Siveco, and connect to the central management platform bluebee® cloud, operated by Siveco. The solution is provided on a SaaS (Software-as-a-Service) basis, letting the project team focus on critical business processes rather than IT.
As of January 2017, over 1,000 sites are using bluebee® cloud in China, mostly large multisite facility operators.

Staff is using an explosion-proof mobile with bluebee® Android app installed
Project phases
The kick-off meeting held on January 25, 2017. The system was officially “live” on April 26, 2017, meaning that it is used on a daily basis by the terminal staff. This initial project phase is followed by an ongoing continuous improvement phase.
Firstly, the needs of various stakeholders were analyzed, with a focus on HSE and technical management, in order to identify priorities and to establish a “Core Model” based on which bluebee® cloud was setup by the Siveco project team. The Core Model was designed in compliance with the ISO 55000 Asset Management standard (and its Chinese equivalent GB/T 33172).
Followed a data preparation phase, during which the joint project team systematically identified critical equipment, inspections points and tasks, and preventive maintenance plans. QR-coded tags were affixed to equipment, to be scanned by technicians using the bluebee® app.
Finally the system was put into daily use, providing strong guidelines for day-to-day and allowing, thanks to systematic reporting from mobile users, to continuously improve technical risk management and demonstrate progress to the various stakeholders.
The terminal is currently under Enhanced Maintenance Support by Siveco, meaning that Siveco not only operates the bluebee® cloud platform, but also ensures regular visits by maintenance consultants to ensure ongoing improvement.
Overview of bluebee® usage at LBC Shanghai Shipping Terminal
All departments can create incident reports or work requests using explosion-proof mobile devices. Requests must be then be approved by department managers. The system reduces approval time delay and helps establish work priorities for the Engineering or Project departments.
Based on inspections and preventive action guidelines, pre-defined as per regulations, equipment suppliers’ recommendations or the terminal’s own risk analysis, the bluebee® cloud planning engine automatically creates working plans.
Both corrective and preventive work orders are assigned to relevant personnel and sent to their mobiles, thus highly improving technical staff working efficiency: no more paper forms. QR code scanning, voice records and detailed task reporting in bluebee® handheld devices provide strong evidences that the work is done.
Overall, bluebee® ensures efficient communication between operation, HSE, maintenance departments and top management. It assists in the implementation of daily work and work management.
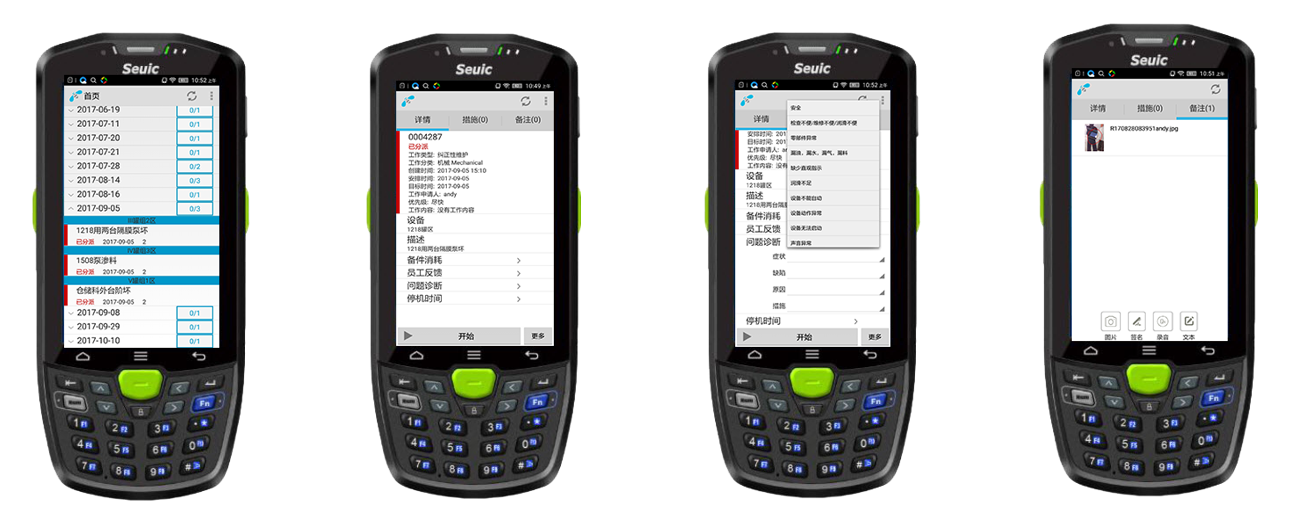
Based on work feedback, accurately obtained in real-time from mobile users, bluebee® cloud automatically creates monthly management report and performance appraisals. LBC Shanghai Shipping Terminal teams can analyze reports and performance by equipment type, incident type and cause, and other classifications.
Results obtained
The terminal is now actively using bluebee® to optimize its assets management. All technical work is managed in the system, significantly improving the working efficiency of the technical team. Fault diagnosis information is now recorded systematically, allowing for scientific analysis and improvement. Getting rid of the old paper-and-Excel based system meant that the corresponding administrative time could be reallocated to preventive activities. Overall inter-departmental collaboration has been optimized with a beneficial impact on safety.
According to LBC Shanghai Shipping Terminal’s General Manager Yuan Xiaolin:
“bluebee® is helping managers to monitor the condition of facilities and equipment, to identify risks and to track improvement actions. Non-compliance and risk areas are instantaneously reported on mobiles. Data records allow us to demonstrate compliance with the strictest standards and to systematically analyze and improve.”
Both Siveco and LBC Shanghai Shipping hope that this project, showing tangible improvement in terminal risk management, using technological tools and good management practices, will help promote further improvement in the industry as a whole. We welcome experience-sharing with other terminals.
bluebee® cloud itself is highly scalable, from one to many sites, allowing sharing and benchmarking between terminals within the same group or even between different companies, while ensuring data security and confidentiality. Some siveco clients already operate several hundreds of sites with bluebee® cloud.