Siveco assists Arkema Changshu in CMMS data collection best practices
Arkema Changshu: the group’s largest industrial platform worldwide
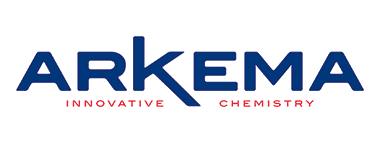
Arkema (www.arkema.com.cn), aiming at becoming a world leading player for specialty chemicals, attaches great importance to the China market. Arkema initially entered China in 1984. A diversified chemicals manufacturer covering three business segments (high performance materials, industrial specialties, coating solutions), Arkema employs over 2900 people in China in 8 manufacturing locations and 2 research and development centers. Arkema China’s research and development teams combine the best science, technology and innovation spirit, to bring solutions to our customers.
Established in 1998, covering an area of 430,000 m² in the Advanced Material Industrial Park of the city of Changshu (Jiangsu Province), Arkema Changshu has been keeping growing since its establishment and has now 5 different manufacturing plants and one R&D center, includes: Arkema (Changshu) Fluorochemical Co., Ltd., Arkema Daikin Advanced Fluorochemicals (Changshu) Co., Ltd., Arkema (Changshu) Chemicals Co., Ltd., Changshu Coatex Additives Co., Ltd. and Arkema coating resins plant. Arkema Changshu is now the biggest industrial platform of Arkema worldwide, employing around 800 people.
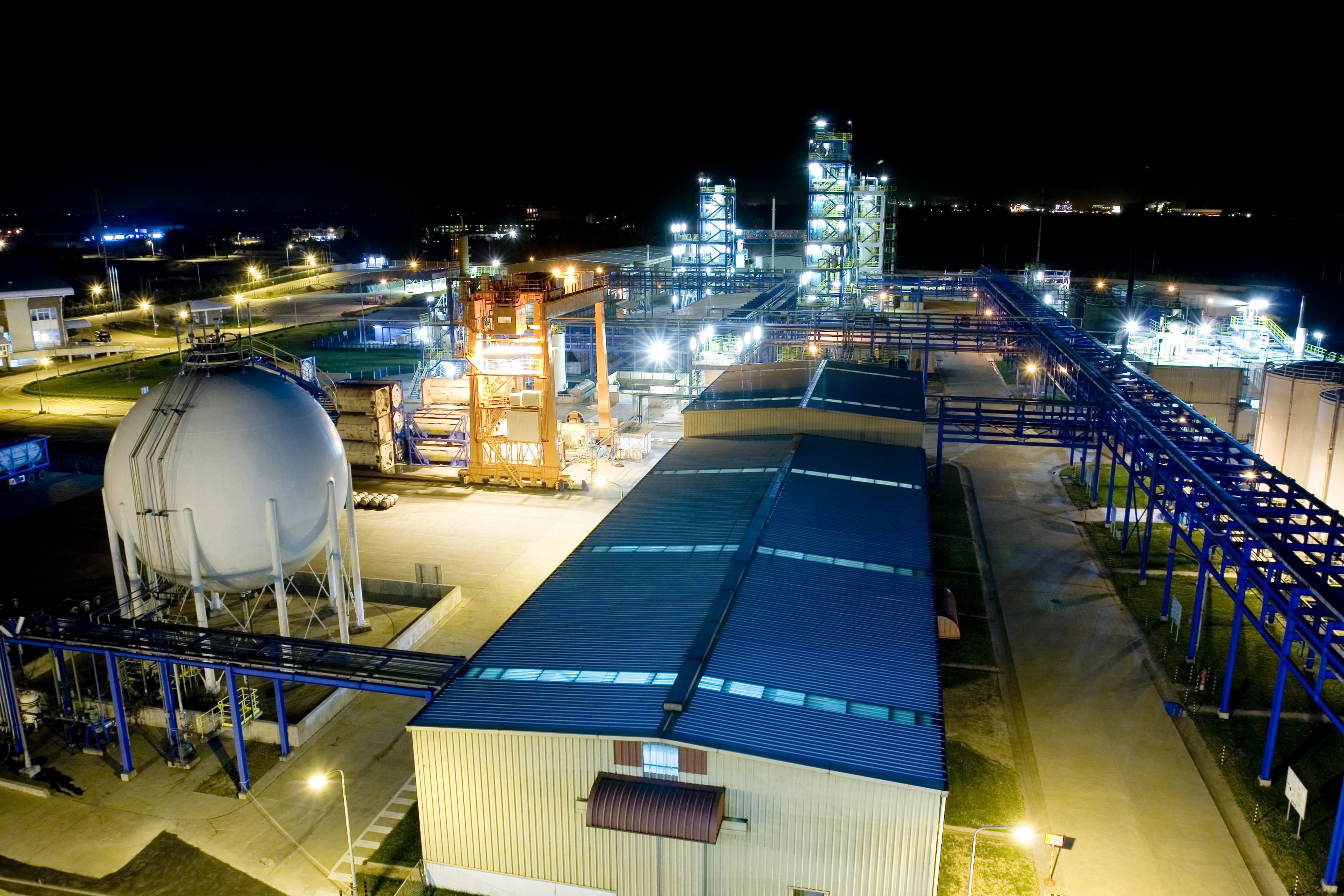
Arkema (Changshu) Fluorochemical Co., Ltd.
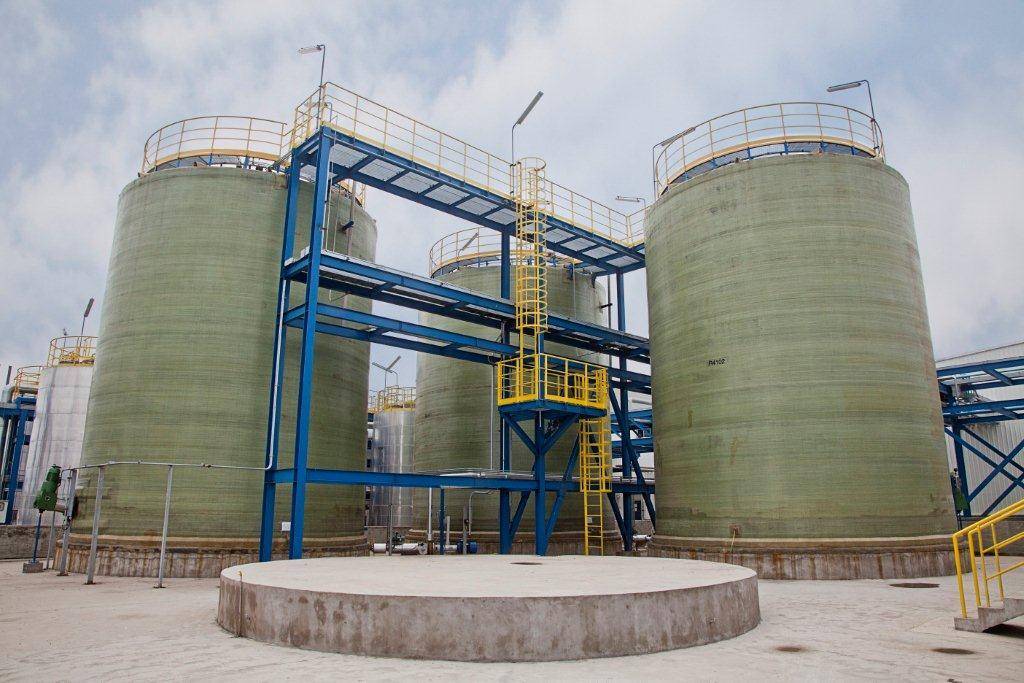
Changshu Coatex Additives Co.
Introduction: Siveco & Arkema
In the petrochemical industry, the choice of IT applications is often dictated by corporate decisions, deployed globally. Arkema had initially selected an American maintenance system in its Shanghai and Changshu plants. As the company was struggling to successfully implement the software, Siveco provided maintenance consulting services. The 2008 project is described in this previous case study. Siveco ran a similar project in Arkema Hydrogen Peroxide plant in Shanghai.
Subsequently, Siveco has worked with Arkema’s Bostik subsidiary sites in Changshu and Guangzhou, which implemented the Coswin plant maintenance solution with great success.
Later, Arkema group initiated a global rollout of SAP, including the SAP Plant Maintenance module. In 2013, Siveco assisted Arkema in SAP PM data preparation for a new petrochemical plant built in Malaysia in cooperation with Korean biochemical producer CJ CheilJedang. The project scope included the build-up of functional and equipment structures for the plant’s SAP Plant Maintenance system. The project was completed in 2013, ensuring technical data readiness well before plant start-up. A short project summary was published here.
Based on Siveco’s successful track record working for Arkema and Bostik and more generally with large chemical companies such as Bluestar-Adisseo, CEPSA, Evonik, Hanwha etc., the company’s top management hired Siveco to conduct consulting services to assist in CMMS data preparation in all Arkema Changshu plants.
Key Challenges: data preparation and business blueprint
Arkema Changshu had identified two main challenges requiring Siveco’s assistance: data preparation and the definition of standard operating procedures, and noted that one would impact the other.
Data preparation is a key aspect of implementing SAP PM (and more generally of any CMMS project), affecting the usage and usefulness of the system for years or even decades to come. Data preparation covers the establishment of the plant functional locations and equipment structures (in the SAP terminology, a “functional location” represents the system area where an equipment object can be installed), with all related information: criticality, specifications, documentation, as well as spare parts, warranty periods, contracts, preventive maintenance instructions, etc.
Unattended by traditional SAP implementation consultants and IT firms, which lack the necessary maintenance know-how, data preparation is usually left to the customer’s maintenance team, requested to fill-in complex Excel templates, on top of their existing job, with a limited understanding of how it will affect their future use of the system. Arkema China was well aware of this need, thanks to their strong CMMS experience in China and feedback other plants’ SAP PM projects elsewhere in the world.
Arkema Changshu faced specific data preparation challenges, due to the massive scale of the site (5 plants, 11 units, a huge number of equipment items) and data in the previous CMMS that did not match with P&ID drawings. Furthermore the logic employed in the previous CMMS did not match that of SAP PM. Reviewing, correcting, completing existing data and reformatting them for upload to SAP PM was looking like an enormous task, with many unknowns and a tight deadline.
At the same time, Standard Operating Procedures (SOPs) had already been defined, based on which the SAP PM system was to be setup. Sometimes called “Business Blueprint” or “Core Model” depending on the terminology employed by the lead SAP consultants, it is almost inevitably based on SAP system processes rather than the customer’s maintenance strategy. This approach often results in a very admin-driven usage of the system, a disconnection between reality and the system, and ultimately a less useful maintenance system.
Arkema Changshu was well aware of the limitations of their existing blueprint, but also of their lack of professional resources to review and improve it in-house. Existing consulting firms involved in the SAP project did not possess the necessary maintenance expertise, while group support teams had no China experience.
Arkema Changshu turned to Siveco to tackle these two critical success factors for its SAP PM implementation.
The Siveco project: a proven ISO 9001-certified approach
The project was kick-off in July 2017, under the joint responsibility of Arkema Changshu site maintenance manager and a Siveco China project manager. Data preparation started first, considering the large amount of data and Go Live deadlines. SOP reviews started later and were then conducted in parallel.
Siveco offered a strong methodological framework for the project based on international standards, chiefly the ISO 55000 Asset Management standard (also known in China as GB/T 33172), ISO 14224 Petroleum, petrochemical and natural gas industries — Collection and exchange of reliability and maintenance data for equipment and IEC 81346 Industrial systems, installations and equipment and industrial products — Structuring principles and reference designations.
Data preparation
This part of the project started with a review Arkema Global Guidelines, to which Siveco had to ensure strict compliance, followed by an audit of SAP templates and existing data for the five Arkema Changshu plants. The actual data preparation was based on reviewing P&ID, extracting data, checking and correcting existing data templates.
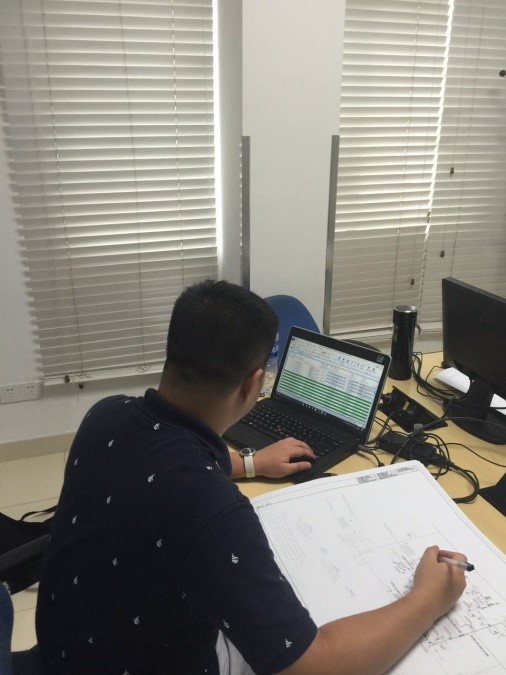
The data preparation covered:
•
Master data
•
Functional locations – around 50,000 in total
•
Technical equipment register
•
Bills of Material (BOM)
•
Planned Maintenance plans
Most of the data preparation work was carried out at the Siveco engineering back-office in Shanghai, under the supervision of a project management team in direct contact with client, via regular face-to-face meetings. Siveco uses specialist IT tools, the bluebee® cloud platform, to ensure quality, accuracy and efficiency of the data preparation work. Siveco working procedures are ISO 9001-2015 certified, ensuring quality, reliability and efficiency essential for such complex data preparation task.
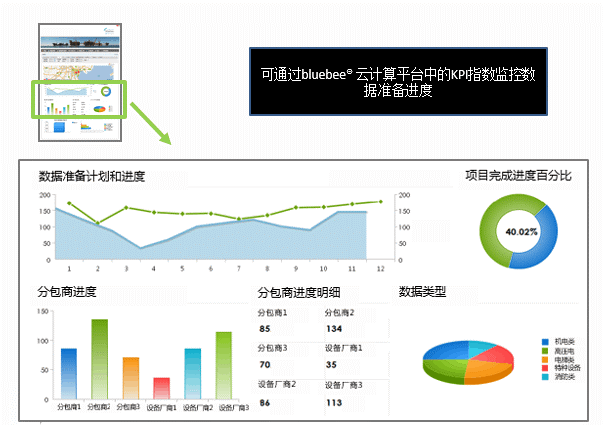
Siveco ensured the as-built technical accuracy of all data supplied and delivered the data is the template format specified by customer, in Excel templates ready for import to SAP PM. The actual data upload, a typical SAP implementation step, was not under Siveco’s responsibility.
Blueprint improvement
For blueprint review and improvement, Siveco also had to ensure consistency with Arkema Global guidelines, through coordination with international Arkema teams. Starting with audit of the existing blueprint, covering all maintenance work processes to be completed in SAP PM, Siveco experts offered various suggestions based on practical experience of maintenance management and of using SAP PM.
The first optimization suggestion was to restructure the SOP documents around Arkema’s maintenance strategy and processes rather than taking SAP as the reference point. Processes should be defined according to Arkema Changshu’s needs and organizational context, based on which the way SAP supports these processes can be described.
The blueprint covered the following main areas:
•
Maintenance strategy: how it is defined and applied in SAP PM
•
Review and necessary support for Reliability Centered Maintenance (RCM), Failure Modes and Effects Analysis (FMEA), Risk Based Inspections (RBI), Root Cause Analysis (RCA)
•
Work management processes, expressively covering Emergency, Regular work, RCA and Management of Change (MOC)
•
Preventive maintenance
•
Maintenance analysis and improvement
•
Functional location and equipment master data management
In addition, Siveco provided training on the topics covered in the SOPs and advised Arkema on the usage of Electronic Document Management Software (EDMS) in connections with the existing software environment (SAP PM and Sharepoint).
Results Obtained
As a result of the project, over 50,000 functional locations and related data were uploaded into SAP PM. Function Location codes were standardized, checked against P&ID drawings, with no leakage, error or repetition. Function Location structures were sorted out, including Pipes, Facilities, Equipment, Instruments etc. ensuring the relationship with P&ID drawing number and superior functional location (parent equipment). Arkema verified the quality of Siveco work through both systematic reviews and automatic checks made upon upload.
The blueprint and SOPs were realigned with Arkema Changshu’s maintenance strategy, in application of ISO 55000 principles. Consequently, all processes defined to be performed in SAP PM match value-added activities in support of this maintenance strategy. Basic data such as Object type, Cost Center, Work center, Planner group and so on were established according to the definitions set in the blueprint.
Arkema Changshu’s Technical Director commented on the work done by Siveco:
“Of course we can still run our software with poor data. But at the end of the day, users will not be satisfied and will gradually lose confidence in the tool. Ultimately, they will reject it and the implementation of SAP PM would not be successful. We think the support Siveco provided for master data preparation is good. With their help, the process has been fast, with minimum back & forth and a maximal utilization of the resources assigned to these tasks.”