Semiconductor gas producer controls plant maintenance risks with bluebee®
Yangzhou Taiyo Nippon Sanso Semiconductor Gases (YTNS)
Taiyo Nippon Sanso Corporation is Japan’s largest industrial gas producer and among top five industrial gas suppliers in the world. The company is part of Mitsubishi Chemical Holdings. In June 2017, Taiyo Nippon Sanso’s Chinese subsidiary Yangzhou Taiyo Nippon Sanso Semiconductor Gases (YTNS) started the construction of a new electronics gas manufacturing plant at Yangzhou Chemical Industry Park in Jiangsu province, in order to support increasing demand for electronics gases in Asia and especially in China. YTNS uses advanced production equipment and adopts Taiyo Nippon Sanso’s strict quality management system to manufacture high-purity gas used in the manufacturing of semiconductors, TFT-LCD, LED, solar cells etc. The plant started production in April 2019.
Identifying maintenance challenges
At the end 2018, during the late construction phase, YTNS’ management team expressed the need for a robust and user-friendly management system to ensure technical best practices in line with its business requirements. YTNS contacted Siveco, which then conducted an onsite assessment.
Specific challenges where identified during this assessment:
●
As a producer of specialty gases with stringent quality requirements, YTNS operates high-precision equipment relying on professional maintenance, with a focus on anticipating work execution through careful planning and scheduling.
●
Furthermore, the plant will operate under strict health, safety and regulatory oversight by the authorities (fire prevention, high voltage, etc.), demanding full traceability of O&M actions and documented compliance.
●
However, it would be difficult for the plant team to find time to build its management system, technical database, O&M procedures, etc. before startup, as most resources are tied up with construction activities.
●
Finally, spare part management, in particular establishing safety stock levels and ensuring early notice for purchase, was identified as critical for the future plant operation.
After several rounds of evaluation and reviewing Siveco’s successful references with other industrial gas plants in China, YTNS selected Siveco to implement its innovative bluebee® solution, with consulting services aimed at tackling the challenges already identified. The contract was signed in March 2019.
ISO 55000 as methodological framework for the project
To achieve the project objectives, Siveco proposed a coordinated five-step methodology based on the ISO 55000 Asset Management standard.
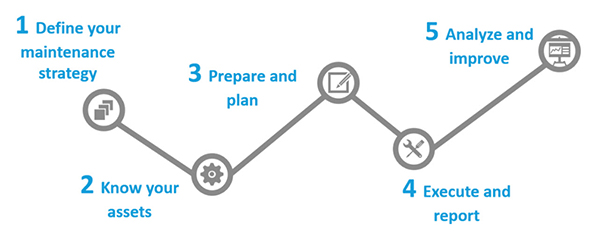
The joint Siveco and YTNS team went through all the steps of the project:
1.
Formulating a maintenance strategy, based on Taiyo Nippon Sanso’s in-depth domain knowledge, existing documentation and a fact-base evaluation of the gaps between the current situation and the plant’s objectives in terms of efficiency, compliance, and safety.
2.
Building a structured asset database for the plant (code, type, function, technical specs, spare parts and other information) to achieve a strong statistical analysis capability. In particular, equipment criticality was formally defined according to its impact on plant operations and regulatory compliance.
3.
Designing a practical maintenance plan, corresponding to the maintenance strategy and YTNS’ risk profile, consistent with the site’s operational constraints and regulatory requirements.
4.
Setting up a framework for systematic recording of work feedback consisting of fault codes, spare parts consumption, labor costs, etc. covering all maintenance activities such as inspection, regular preventive maintenance, corrective maintenance, etc.
5.
Leveraging the structured asset database and work feedback for analysis and performance monitoring, to support continuous improvement and management supervision through data visualization and reports.
To each step corresponds activities in the deployment of the bluebee® solution. All assets were identified and tagged using QR-codes. Technical data, standard operating procedures (SOPs), maintenance plans, spare parts, employee information, etc. were loaded in the database, which was configured based on the management rules defined with YTNS.
The supporting mobile solution bluebee®
bluebee® is a worker-centric Smart O&M solution designed “for the worker of tomorrow”. The back-office system bluebee® cloud is an Industry 4.0 platform that enables Risk Prevention decisions based on true data from Mobile Users and Connected Objects. By enforcing systematic recording of failures, inspections and work done, the integrated bluebee® solution provides a technical knowledge base to support technical teams’ daily work and to facilitate management decisions. Essentially, bluebee® allows YTNS to “close the ISO55000 feedback loop”.
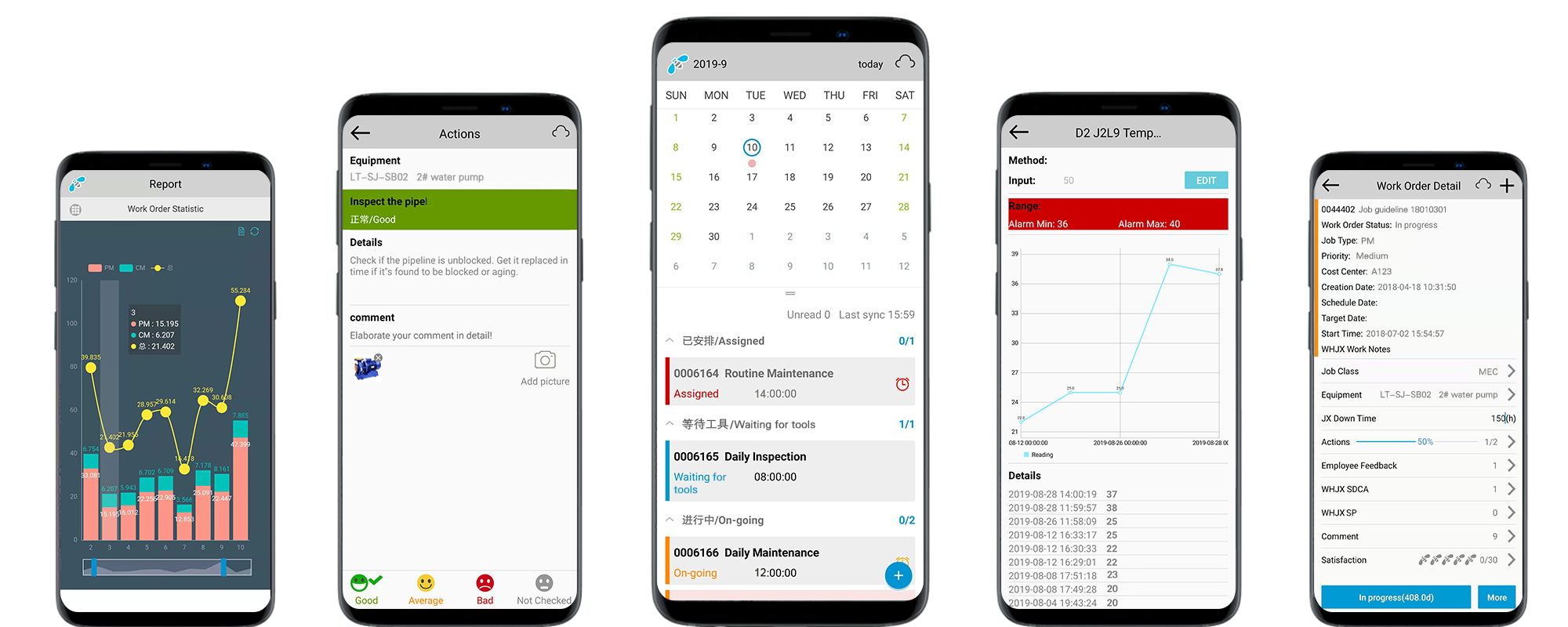
Since August 2019, after 4 months of implementation, YTNS technicians started to use bluebee® to perform their daily work. The app runs on industrial Android phones certified for hazardous environments (Class I, Division 2). Planned activities including preventive maintenance, inspections and planned corrective maintenance appear in the app, allowing technicians to access all necessary information from the central database. Problems can be reported directly by scanning the faulty equipment QR code which facilitates cross-department management and work coordination. The mobile tool has proven very user-friendly and efficient in supporting frontline teams in adhering to the strict regulatory framework effectively in an auditable way.
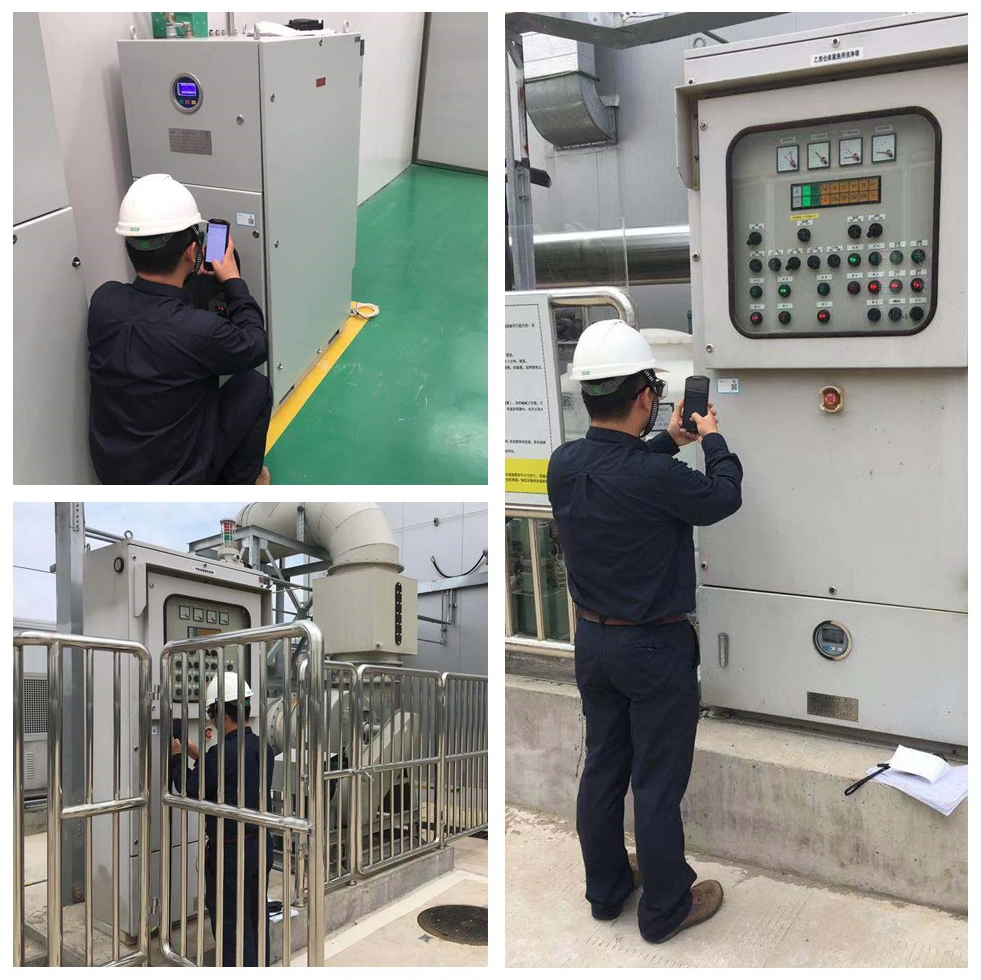
Contextualized and operational dashboards
Through the powerful analysis tool embedded in bluebee® cloud, visual dashboards give the YTNS team a deeper understanding of their activities and the plant’s operational risk profile. This management tool is available securely through the internet for any authorized YTNS user.
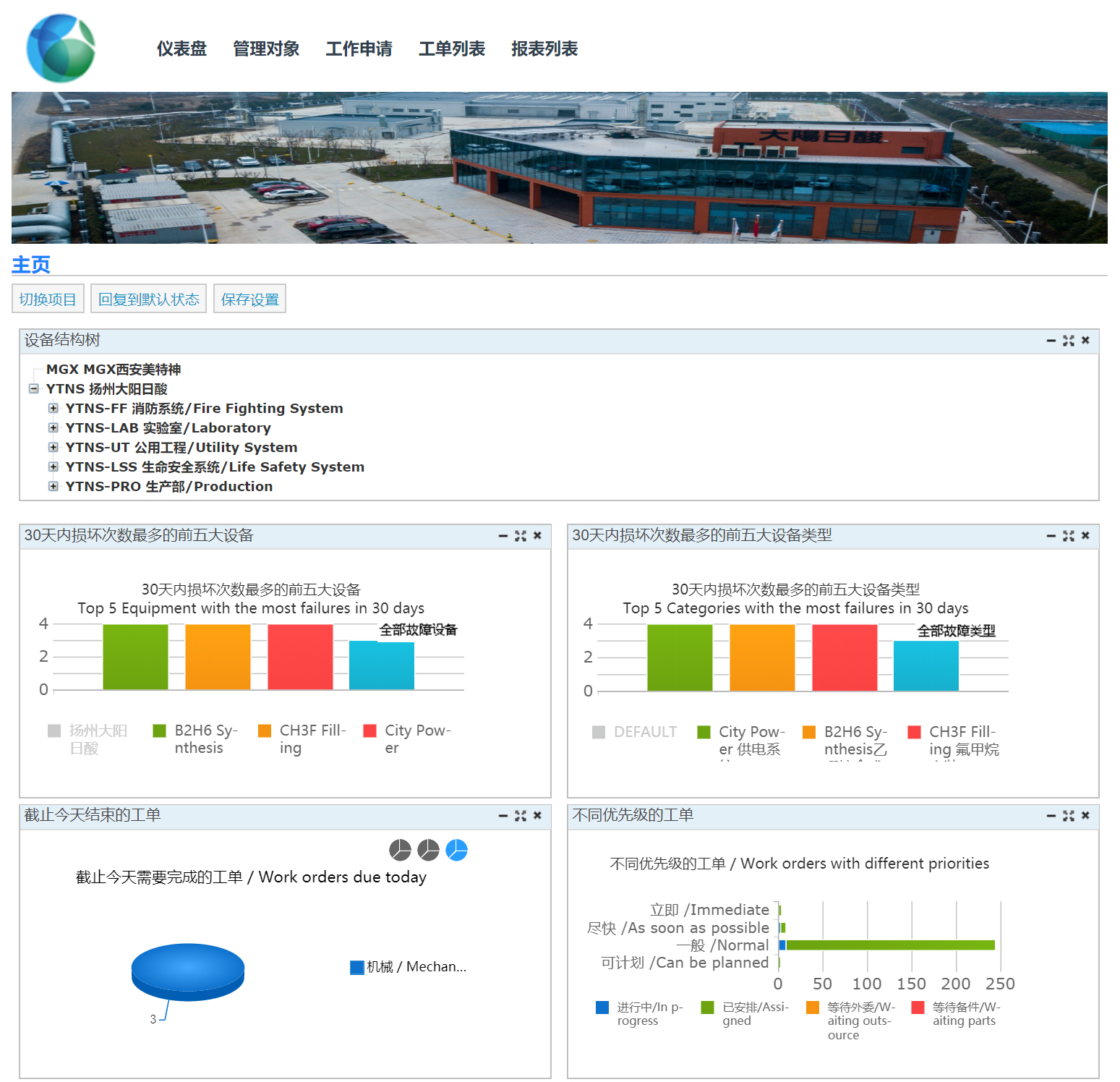
Anticipating upcoming maintenance activities, including spare parts requirements, for high-precision equipment is critical to ensure the reliability and safety of YTNS’s plant. For this reason, the bluebee® implementation at YTNS goes beyond the typical CMMS setup of releasing preventive maintenance work orders or stock and purchase requisitions at predefined intervals.
For example, a visual widget enables the maintenance team to identify how much work will be required in upcoming time periods. Thanks to this tool, the maintenance teams can anticipate, at any point in time, how busy they will be on maintenance activities for critical equipment.
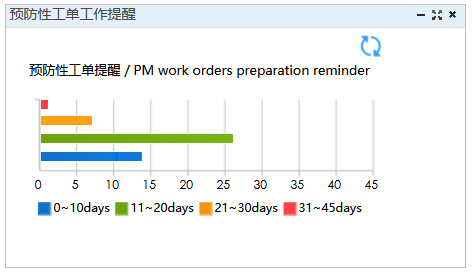
A similar concept has been applied to address the parallel need for anticipation and preparedness in spare part procurement: maintenance team are informed in real time if the quantity of any inventory item goes below the safety level and below 50% of the safety level, showing acute shortage risk. This tool also helps the team adjust safety levels for each part based on the accumulated experience.
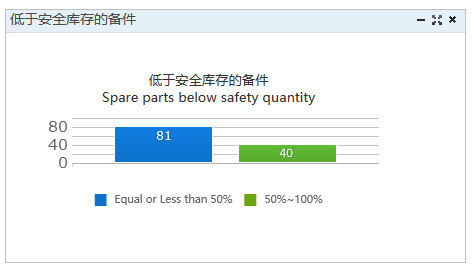
With a few clicks, users can immediately contextualize their KPIs with other information and drill-down to more details and specific records. For example, users can compare the remaining inventory quantity of a specific part with the number installed in the plant, thus evaluating at a glance the seriousness of situation. They can quickly operationalize this information, to generate the list of spares to be purchased, in a single click, directly from the dashboard.
With bluebee® and bluebee® cloud, YTNS can continuously optimize its plant maintenance strategy based on actual, verified, real-time data from the field.
Continuous improvement
In terms of IT infrastructure, from the get-go the choice was made of a cloud-based solution. Through its global partnership with Alicloud, Siveco manages high-availability highly-secured cloud servers optimized for bluebee®. This approach eliminates all needs of IT support in the plant, allowing the YTNS team to focus on continuously improving its core business.
According to YTNS’s Maintenance Manager Richard Yang: “After the 4 months implementation phase, the bluebee® system has been running smoothly since August 2019. It has become our main management platform and a tool for continuous improvement. Our team is satisfied with the implementation service and ongoing support provided by Siveco, communication between us is very smooth and feedback always timely.”

YTNS is planning to expand coverage of bluebee® to its other specialty gas plant located in Xian. Siveco will continue to provide better service to YTNS and is planning to organize sharing sessions between its industrial gas customers. Siveco Smart O&M solutions are in use across hundreds of industrial gas plants of Yingde Gas, Baosteel Gases, Baida Air, etc. all over China.