Leading auto parts maker optimizes maintenance with Coswin 8i
Sogefi (Suzhou) Automotive Parts Co., Ltd.
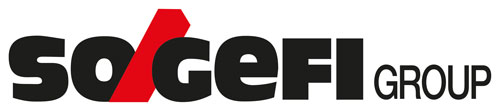
Sogefi (Suzhou) Automotive Parts started operation in 2014. The factory, located in the Wujiang Economic & Technological Development Zone, produces suspension components. It is a subsidiary of Sogefi Group (www.sogefigroup.com), a leading global supplier of original parts for the automotive industry, with over 35 years’ experience. Sogefi designs, develops and produces filtration systems and flexible suspension components as well as air management and engine cooling systems. Sogefi is listed on the Milan Stock Exchange and has a commercial presence in 21 countries on 4 continents, with 42 manufacturing sites and 16 sales offices.

Project background
After the factory was setup, the priority was naturally to ramp up production, not to optimize maintenance. The company’s management team was however well aware of the importance of maintenance and initiated discussions with Siveco as early as 2014 during the startup phase. The topic gradually gained traction and became a priority at the end of 2015, with a clear need to improve maintenance efficiency and to keep costs under control.
Specific challenges met by the maintenance and production teams of the Sogefi Suzhou plant at that time included:
•
Traditional paper- and Excel-based processes started to become overwhelming and time consuming
•
In particular, all preventive maintenance planning was done manually using Excel sheets
•
Spare parts consumption could not be traced to related maintenance work or equipment, making it difficult to optimize.
•
The maintenance of tools and dies needed to be reorganized.
Sogefi Suzhou decided to hire Siveco China to run the maintenance improvement project by implementing the Coswin 8i computerized maintenance management system (CMMS). Siveco had previously completed similar projects for Sogefi Shanghai factory and had extensive experience helping other automotive suppliers optimize their maintenance in China.
Implementation schedule
The Maintenance Improvement project, based on the implementation of Coswin 8i, was kick-off in July 2016. One month later, the “Core Model” defining the maintenance organization and the supporting system was approved. Coswin 8i was then configured and tested on site. Sogefi’s maintenance team received training and on-the-job coaching by Siveco. The system was finally put into production in October 2016, four months after project start.
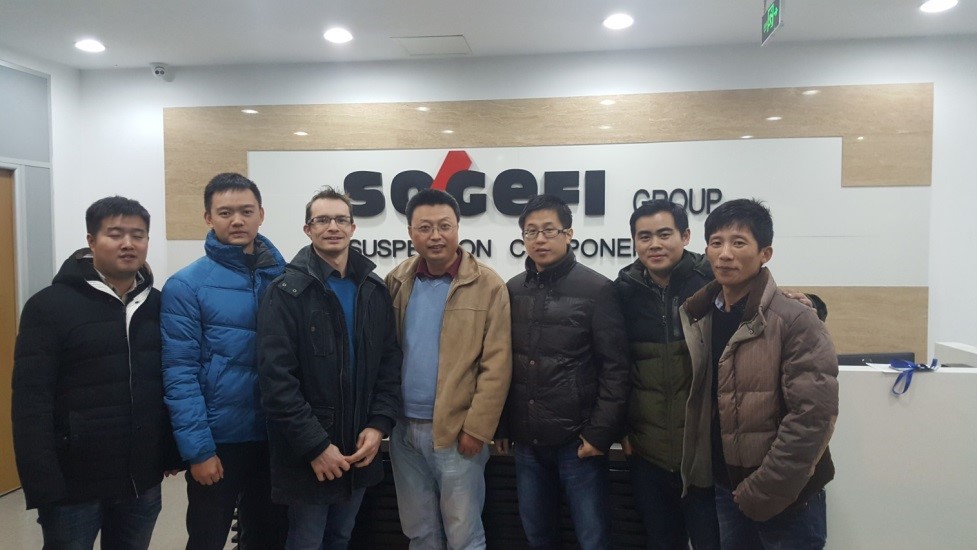
The joint Sogefi-Siveco project team
The CMMS Coswin 8i
Sogefi Suzhou’s maintenance management processes are supported by Coswin 8i. The system, implemented based on a Core Model aligned with the company’s objectives, covers the following main functional areas:
•
Asset management: asset structure, basic information such as criticality, category, technical attributes, spare part list and so on.
•
Fault Reporting: the entire corrective maintenance process, but with a strong emphasis on fault reporting and following up spare parts usage.
•
Preventive Maintenance: definition of job guidelines and planning, for inspections and regular maintenance.
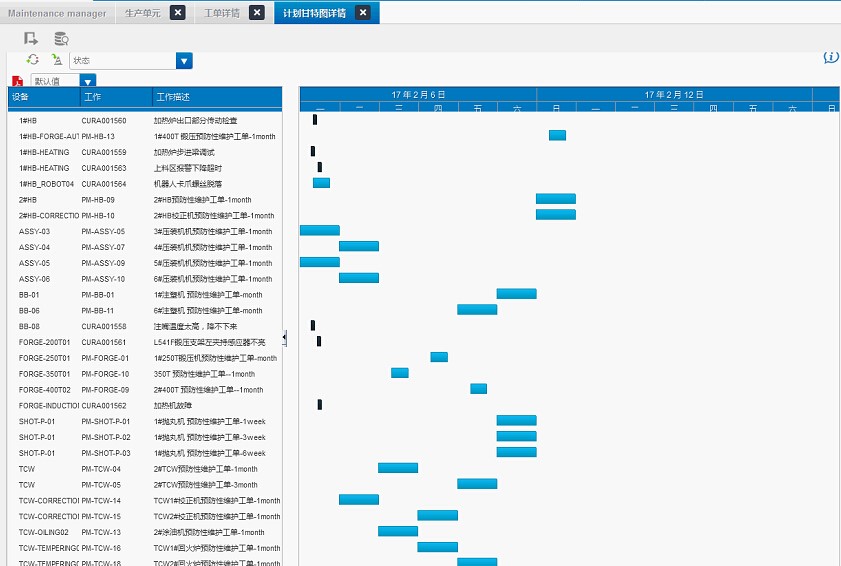
Preventive maintenance planning
•
Tooling management: based on the tool’s production meter value, recorded by production team. Tooling team plans and executes related preventive maintenance work according to the predefined alarm values.
•
Spare part management: interface with SAP, spare part list and basic information such as code, description, quantity, price, etc… are imported from SAP automatically through Coswin 8i’s Clic-Clac interface tool.
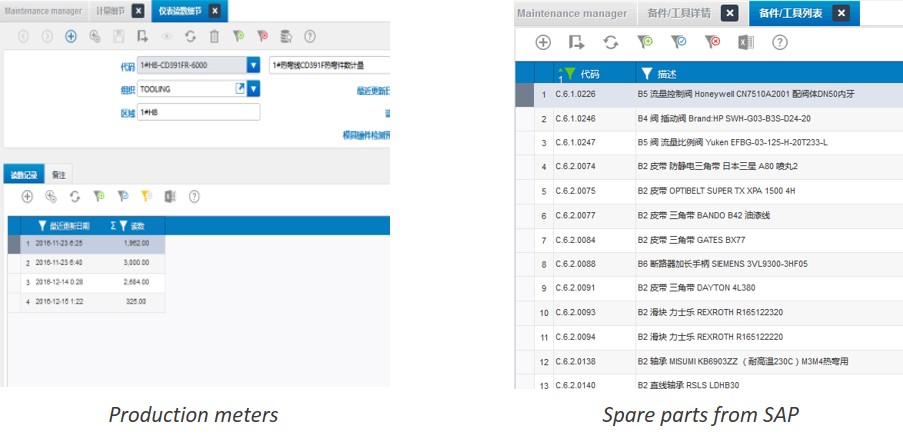
Cockpits and Reports: the system automatically generates KPIs for day-to-day management and analysis reports for decision support.
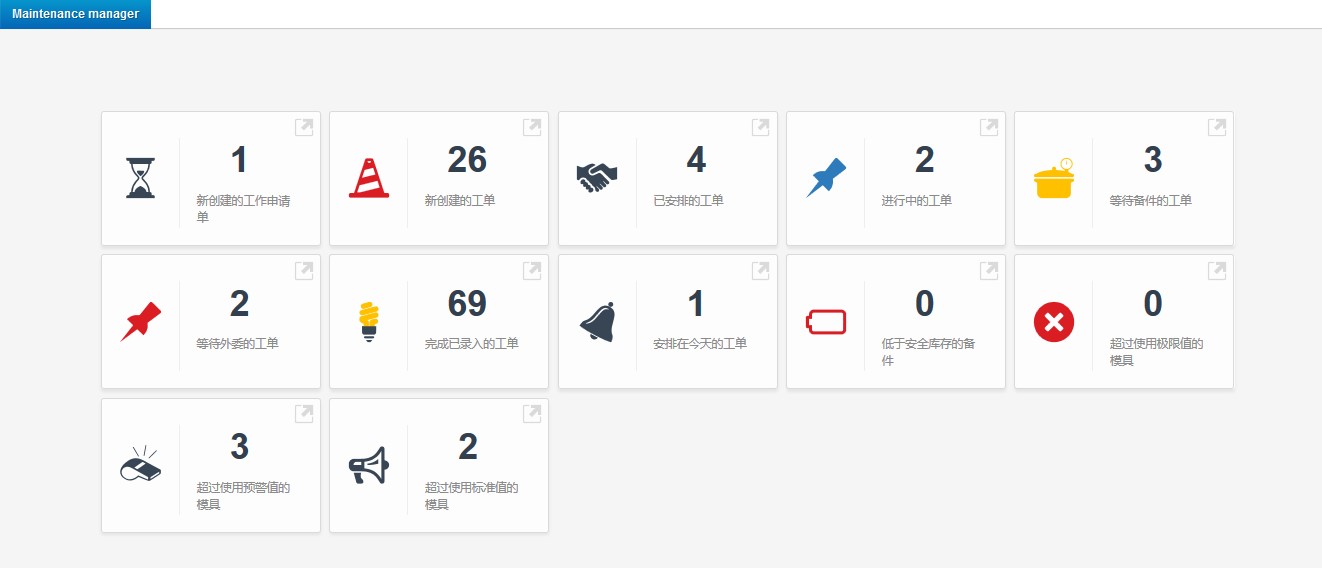
KPIs in the maintenance “Cockpit”
Benefits
The project objectives have been met.
According to Zhou Ronghua, Maintenance Manager at Sogefi (Suzhou) Auto Parts:
“Sogefi Suzhou has successfully got rid of Excel and paper-based maintenance management. Our entire Work Order process is now managed in Coswin: critical data is captured, allowing systematic analysis and improvement initiatives. Work efficiency has greatly improved. Maintenance management is now under control for the first time.”
His manager Emilien Delecluse, Operations Manager, also said:
“I am glad to see our maintenance team is satisfied by the efficient management of preventive and predictive maintenance. Our priority is now to gain benefits from monthly analysis of maintenance activity and performance: our CMMS provides the necessary tool for this.”