How Smart O&M assists the wastewater division of Jiangsu Sino French Water in the implementation of O&M best practices
This article was honored among the “Selected Cases of Waste Water Treatment Industry” by E20 Environment Platform and E20 Institute of Environment Industry.
The wastewater division of Jiangsu Sino French Water
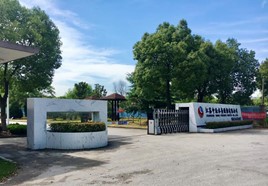
The wastewater division of Jiangsu Sino-French Water comprises multiple wastewater treatment subsidiaries (together referred to as the “wastewater company”). With the support of the parent company Jiangsu Sino-French Water, after years of dedicated work, it now serves over 1 million inhabitants and operates 9 sewage treatment plants, with a daily processing capacity of 165,000 cubic meters.
The company’s core business includes: sewage sludge treatment and management; development and utilization of recycled water; sewage sludge treatment project planning; construction of water supply and drainage projects; engineering installation and operation of water supply and drainage projects; maintenance and management of sewage collection systems; sales of water supply and drainage treatment equipment, pipe fittings and materials.
Project introduction
A well-known water public institution in Jiangsu Province, the wastewater company serves 10 towns and districts in Changshu City, with over 1 million domestic, industrial and commercial clients. In recent years, infrastructure projects such as water and power supply have been increasingly included in the development of Smart Cities, with higher requirements placed on sewage treatment.
On the premise of ensuring production quality and safety, how to keep pace with the times by investing in digitalization to improve management and service quality has become one of the company’s major goals in 2019. After a comprehensive assessment, the digitization of wastewater treatment plant operations and assets maintenance was put on the agenda, aiming to provide a more comprehensive guarantee for the production of the wastewater treatment plant and reducing costs and increasing efficiency. The company investigated the practicality of this project from multiple perspectives, such as operation management and technical feasibility.
For this reason, the wastewater company selected Siveco China, a company that already provided O&M management solutions for Jiangsu Sino-French Water. It is expected that the implementation of project would combine advanced management concepts and smart technology.
O&M needs
Since the establishment of the wastewater company many years ago, relying on the leading technology and scientific management experience of Jiangsu Sino-French Water and the its shareholder Suez Group in the environmental protection market, the company had developed professional and refined equipment operation and maintenance concepts and systems. However, these systems often could not be fully integrated with the actual work. For example, technical data collected on on-site was not complete, equipment information, codes and identification, and inspection procedures were not fully standardized. The company manages 9 treatment plants, 56 pumping stations, distributed in different towns. In addition, the maintenance and inspection personnel headcount is limited, while the workload is heavy, and its management difficult. When maintenance and inspection work is managed on paper, efficiency and accuracy remains low, traceability is impossible. The lack of accurate data also makes it difficult to provide effective analysis reports. These were the typical problems faced by the management team, which needed to be resolved urgently.
Smart technology support
In order to solve the above-mentioned management problems, the wastewater company looked for solutions in many ways, initially using a computerized equipment management system. However, due to a lack of understanding of the water industry and of users actual needs, this system ultimately failed to meet the company’s business requirements.
For wastewater companies, systems are indeed important, but it is preferable to cooperate with suppliers who already understand the water industry, its management and have dedicated technology to help sort out project objectives, inspection procedures and to implement them. Siveco was selected to provide O&M management consulting and system implementation services for this project based on past experience.
In this project, the wastewater company adopted the latest technology of Siveco’s Smart O&M solutions including the mobile app for maintenance management. All technical data, work orders, work instructions and reports, etc. are stored in the back-office system. The system generates work tasks or work orders from predefined strategy, plans and frequencies. The work orders will be displayed on the user’s PC dashboard, according to the specified date, which is very intuitive. Work orders are assigned automatically to the mobile phones of engineers and operators, connected through WiFi or 4G, which, unlike the usual paper-based process, is now fast and convenient. Mobile phone user conduct their tasks under the guidance of predefined work instructions. If a fault or problem is found onsite, it can be directly reported for corrective action in a timely manner. In the end, the work completed on the mobile phone is automatically transferred back to the central system, with multimedia recording (such as voice, text and small video as needed), ensuring a true record of the work done. Thanks to this closed-loop approach, the company’s O&M and inspection work can be completely managed, with full traceability of the work, and convenient query and analysis.
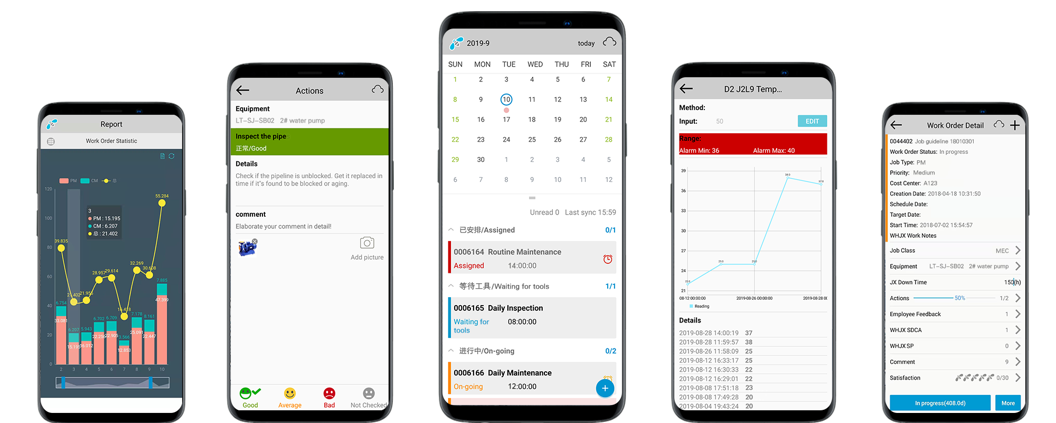
In addition, based on Siveco’s recommendations, the wastewater company has defined new standardized equipment asset codes, inspection procedures, work order status and Key Performance Indicators (KPI), so that theory and practice are no longer disconnected.
At the same time, the wastewater company deployed NFC tags for equipment or asset labels and inspection points. Compared to traditional QR code, NFC tags offer better security, they cannot be copied, while they can be reused and are well suited for in-field usage.
Benefits
Both sides had in-depth discussions on this Smart O&M project. Through repeated communication all the way to final approval, Siveco finally implemented a complete Smart O&M solution to meet the needs of the wastewater company. The project helped to establish and obtain the following benefits:
- Based on ISO 55000 asset management consulting services, the Core Model for the Smart O&M and inspection system was established. This model will be applicable to future acquisitions of new-built wastewater plants of the company, and has a wide range of practical applications;
- Established a standardized equipment and asset technical database, covering coding rules, naming rules, asset identification, equipment and spare parts data, failure information, preventive maintenance plans, etc.;
- Using the combination of the back-end management system and the mobile devices to organically integrate Operation and Maintenance data, daily work, analysis reports, etc., to basically realize a paperless and high-efficiency working mechanism;
- Through the implementation of mobile solutions, an effective work execution and feedback mechanism has been established, from which work done is accurately reported, providing a strong basis for decision support;
- Decision support: definition and display of Key Performance Indicators for O&M management. The report display is very friendly and can also be displayed on a larger BI platform.
On October 22, 2019, both sides formally held a project kick-off meeting and on December 20 of the same year, the system was officially put online.
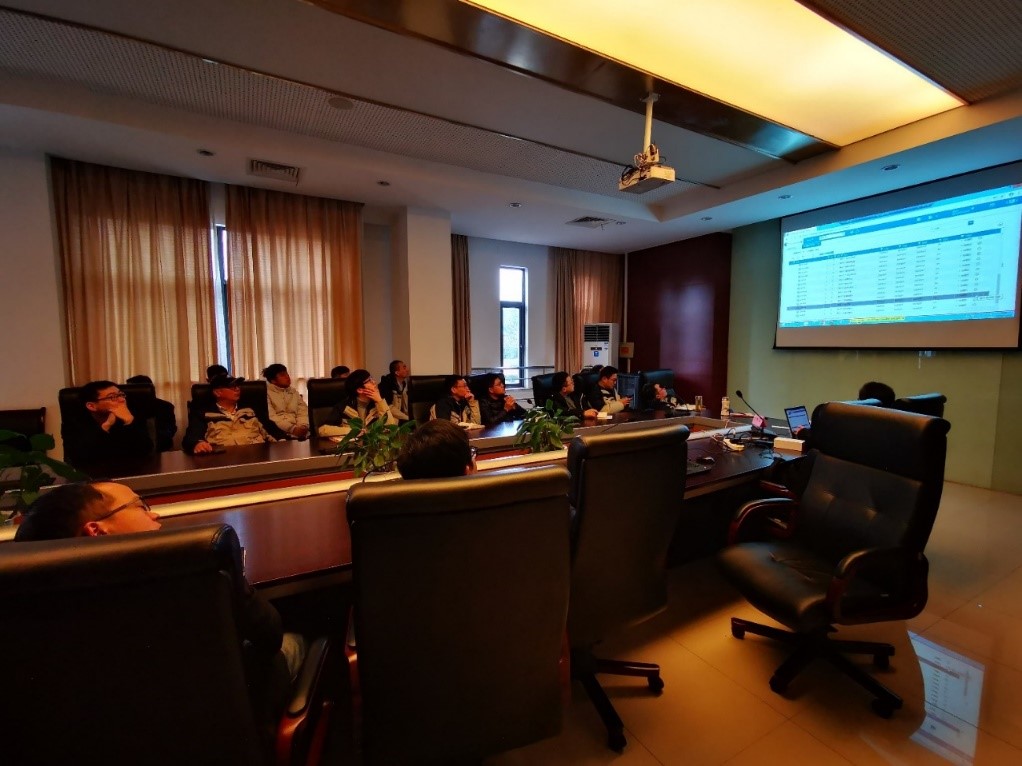
Smart O&M results
Adopting Siveco’s complete solution based on the concept of Smart Operation and Maintenance, the system mainly consists of two parts: the Coswin back-office management system, on a Browser/Server, web-based architecture, and the bluebee® mobile app running on Android smartphones. Through a dedicated dashboard on the system’s homepage, users can track the current status of all work orders and manage them; by establishing a databased for the plants, the system helps the equipment department and the water treatment plants’ personnel to manage their equipment, making it easy to create, repair, and maintain equipment. In addition, after establishing a preventive maintenance plan, the system helps schedule work orders and track their execution.
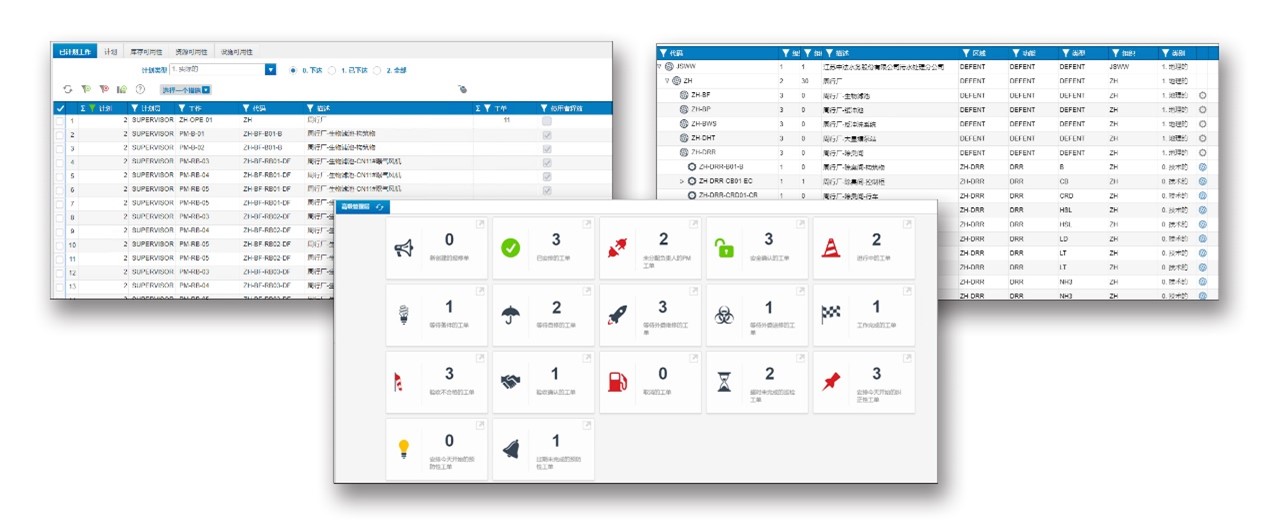
bluebee® is a unique tool designed “for the worker of tomorrow” to capture information from the field and to enforce best practices.
According to the planned inspection tasks and workers shifts, the system will automatically generate inspection work orders every day, the mobile app will receive the work orders, with a reminder message pushed to the inspectors’ mobile phones.
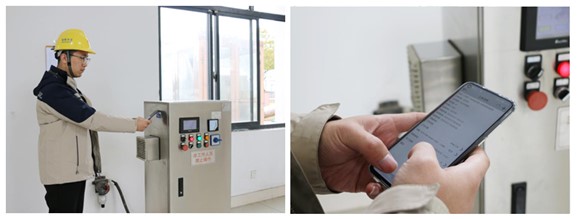
The Maintenance Division is responsible for all the maintenance activities for all wastewater treatment plants. That is, maintenance is managed centrally and each plant’s Operation team needs to report equipment failures to the maintenance department. The Maintenance Division will accept maintenance requests from the various plants and arrange the corresponding maintenance teams in each site for repair operations. The plant personnel must first confirm the safety of the maintenance work, take corresponding safety precautions such as power-off, LOTO, etc., Once the maintenance team has completed the work, the plant personnel will finally accept the work done.
Through the paperless work model and clear work processes, on-site work efficiency has been greatly improved. Data is synchronized to the database in time to ensure backup and data analysis. On-site scanning of equipment NFC tags ensures that employees are actually there and have completed their work orders, which also plays an effective supervisory role.
Relying on the strong support and participation of the company’s management and users, as well as Siveco’s rich experience in water and environmental protection, with mature and stable software products, the Smart O&M project was delivered and put into use in only two months. At present, the various system functions meet the needs of the wastewater company and have solved the various problems from technical data acquisition, work execution management and report analysis.
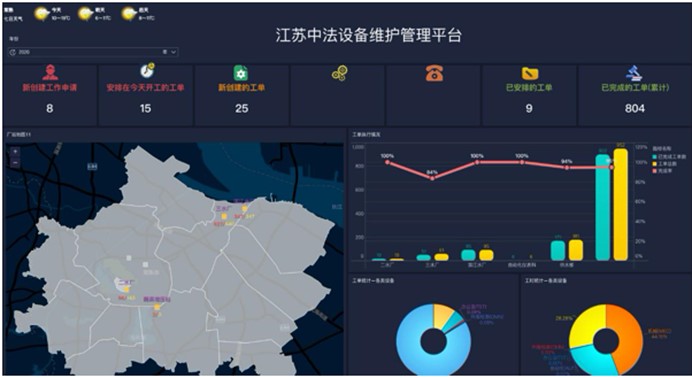
At present, the wastewater company has used the Smart Operation & Maintenance + bluebee® mobile inspection system to carry out their daily maintenance management, effectively integrating data through Information Technology, building a data platform, which will provide a huge boost to the company’s cost-effectiveness.