Leading automotive supplier demonstrates ROI in less than a year with Siveco’ SaaS solution

Brose Wuhan
Brose (www.brose-group.net) is a partner to the international automobile industry and delivers mechatronic systems and electric drives to more than 40 automakers as well as suppliers. More than 16,000 employees work for Brose at 46 locations in 21 countries on all major automotive markets worldwide. With a turnover of 2.6 billion euros in the 2009 business year, Brose is the fifth-largest family-owned company among the top 100 automotive suppliers worldwide.
In Wuhan, located in Hubei Province in central China, Brose opened a manufacturing plant for window regulators and seat systems in 2008. Among its customers are Shanghai General Motors, Donfeng Peugeot Citroen Automobile, Geely and Chery. The range of products made in Wuhan is currently being extended and the operation is set to grow significantly in the next few years as long-term contracts have already been secured, with a plan to build a new facility.
The project
Brose hired Siveco in July 2009 for a project aimed at establishing strong maintenance fundamentals at its Wuhan plant. With production volume and complexity on the increase, and new product lines being introduced, maintenance was becoming a priority for Brose in order to guarantee the reliability of its manufacturing process.
The joint Brose and Siveco team started to use Siveco’s maintenance system COSWIN on a Software-as-a-Service (SaaS*) basis as a support tool to organize the plant’s technical know-how and to systematically analyze failures. The project was incorporated into Brose’s TPM practice, with a strong Visual Management aspect.
Based on similar projects in the automotive industry, ROI was expected within one year.
* In the Software-as-a-Service (SaaS) model, software is rented, as part of a service contract, rather than purchased. The application can still be installed locally, but it is ideally suited for cloud computing on the Internet, i.e. hosted at Siveco’s datacenter. Involving no capital expenditure, the SaaS model also presents obvious advantages in terms of IT administration. Apart from Brose, other examples of this approach among Siveco China customers include CCPG and BYJC-Fabricom.
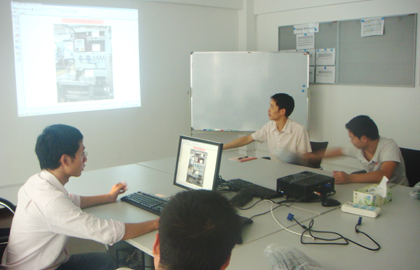
Joint breakdown analysis session with Siveco at Brose Wuhan
The results
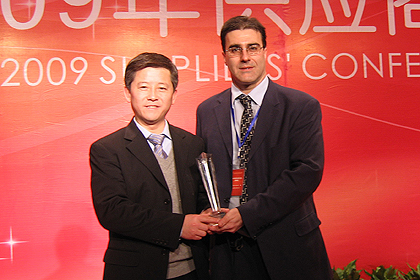
Qiang Chen, Head of Sales Brose South China (left) and Marc Bourgeois, General Manager of Brose Wuhan picked up the “Special Contribution Award” at the supplier conference held by Dongfeng Peugeot Citroen Automobile Company Ltd. on the behalf of all the employees at the Brose plant in Wuhan.
Marc Bourgeois, General Manager of Brose Wuhan, was interviewed by Shanghai Business Review for an article on Lean Manufacturing. This is what he had to say about the maintenance improvement project:
“As our future growth plan is very aggressive, one of the fundamentals that Siveco has helped us with is establishing is a structured maintenance system from an early stage, before our operation gets on such a large scale that implementing systems become more difficult. The project included not only a maintenance software, but also Siveco’s experience and expert advice. Here are some specific examples of improvements brought by the project.”
Structure and discipline:
“The system brings the necessary structure and organization to our maintenance department. It not only helps with the planning and execution of the various tasks, but more importantly ensures a systematic and disciplined approach to maintenance.”
Ease of use and flexibility:
“The system itself is very user friendly; its layout is extremely practical and our Brose team shows a very good understanding of it. It is also compatible with other systems that our company uses, such as SAP. With the Software-as-a-Service approach, IT issues are kept out of the way.”
KPIs (Key Performance Indicators):
“Structured data make analysis and management reporting very easy, with both standard KPIs and customized reports. Based on the weekly and monthly reports, important improvements have already been achieved in key areas.”
Return on Investment:
“Based on calculations by our finance department, which I believe to be on the conservative side, we can say with confidence that the ROI target of one year has been realized. As the project is still at an early stage and our activities are ever increasing, future savings will be even more important.”
The figures below show a sharp decrease in downtime and energy consumption at Brose Wuhan, two essential components of the savings realized under the project.
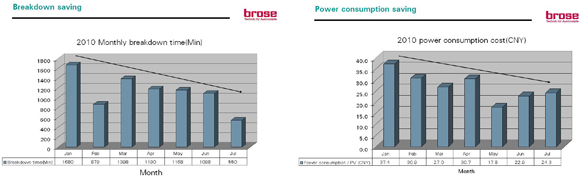
Siveco in the automotive industry:
With over 40 customers in China, Siveco is the country’s largest maintenance consultancy. Automotive customers in China include Advanced Comfort Systems, Allevard-Rejna, BYJC-Fabricom, ZF Lemforder and ZF Steering Systems, all recent additions to Siveco’s prestigious list of global automotive accounts such as Daewoo Motors, Daimler Chrysler, Delphi, Denso, Faurecia, Federal Mogul, Fiat, Iveco, Magna, Magnetti Marelli, Maragoni Tyres, Mercedes-Benz, PSA, Renault, Treves, Volvo Trucks etc.