A catalyst for maintenance improvement at leading chemical group
This story has won the 2010 Motorola Enterprise Mobility Solutions Industrial Applications Grand Prix.
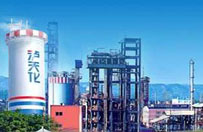
Sichuan Lutianhua Company Limited
Sichuan Lutianhua Company Limited (www.sclth.com) is engaged in the production and sale of fertilizers and chemical bulks. The Company primarily offers urea under the brand name of Gongnong and synthesis ammonia, with an annual production capacity of one million metric tons of synthesis ammonia and 1.6 million metric tons of urea at its Luzhou, Sichuan, production base.
During the year ended December 31, 2009, the Company produced 810,000 metric tons of synthesis ammonia, 1.23 million tons of urea, 60,000 metric tons of thick nitric acid, 50,000 metric tons of carbinol, 40,000 metric tons of nitro phosphor complex and 40,000 metric tons of ammonium nitrate. The Company primarily distributes its products in domestic markets.
Optimizing the inspection process – a key requirement in the chemical industry
Sichuan Lutianhua manages complex chemical production units, operating around the clock, with strong safety requirement and environmental regulations: the company is highly dependent on its maintenance organization to ensure availability, reliability and safety. In the chemical industry, maintenance can be considered the core business of the company and one of keys to its success.
Sichuan Lutianhua has over the years established a good maintenance practice, based on the know-how accumulated by its technicians, with a focus on preventive maintenance. Inspections and measurements play a major role in the company’s preventive maintenance program, as a means to detect early signs of failures.
In 2009, Sichuan Lutianhua invested in a state-of-the-art “Enterprise Asset Management” (EAM) solution, which is currently still in improvement phase.
Sichuan Lutianhua’s management team, always on the lookout for improvement opportunities and rich of this first experience using IT systems, decided to launch a project to support the inspection and measurement rounds. The utilization of mobile devices was imagined to be the ideal solution to support field technicians. The project team reviewed various hardware and software vendors before meeting with Siveco, the largest maintenance consultancy in China, a company uniquely positioned in using high-technologies to solve real-life maintenance problems.
The two companies quickly reached an understanding and the project was started in August 2010 with the following objectives:
– Standardization and planning of inspections (routine maintenance and measurements)
– Ensuring jobs are actually performed, through mandatory scanning of asset tags
– Diagnosis aid for technicians based on reported symptoms and access to know-how base
– Analysis of measurement trends, operation and management reports and optimization of plans over time
– Standardization and planning of inspections (routine maintenance and measurements)
– Ensuring jobs are actually performed, through mandatory scanning of asset tags
– Diagnosis aid for technicians based on reported symptoms and access to know-how base
– Analysis of measurement trends, operation and management reports and optimization of plans over time
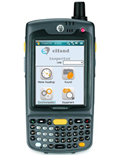
The project
Motorola handheld device were selected, equipped with 2D imagers for asset identification (see box), to run the Siveco bluebee® Inspector solution. Siveco provided the complete turnkey solution including consulting services, software, hardware (mobile devices, server and barcode printer) as well as equipment labels (stainless steel plates).
Two Siveco project managers were appointed, one focused on overall project management and maintenance improvement, the other on the delivery of the system. The Siveco back-office team located in Shanghai, with three people dedicated full-time on the project, provided support for the entire project.
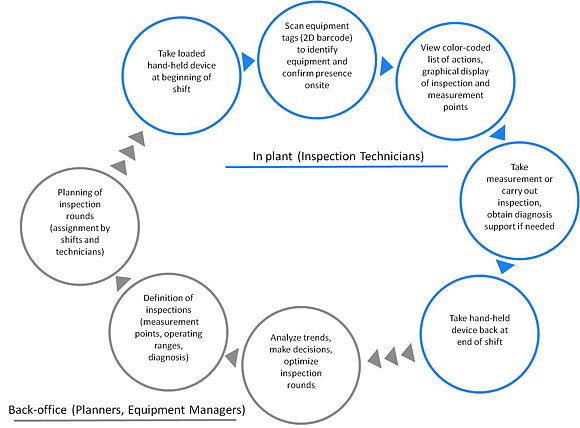

Immediate benefits
Such a project is characterized by immediate benefits experienced during implementation itself:
• Motivate the maintenance team and increase awareness: high-tech acts as a catalyst for maintenance improvement.
• Initiate a continuous improvement process based on predictive maintenance: strong linkage is created between field inspections and back-office analysis.
• “Clean up” of the CMMS database: especially more detailed equipment structures, down to specific inspection or measurement points.
• Motivate the maintenance team and increase awareness: high-tech acts as a catalyst for maintenance improvement.
• Initiate a continuous improvement process based on predictive maintenance: strong linkage is created between field inspections and back-office analysis.
• “Clean up” of the CMMS database: especially more detailed equipment structures, down to specific inspection or measurement points.
The second series of benefits happened from the very first days of utilization:
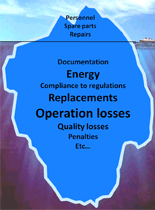
• Ensure inspections are done: records cannot be saved without scanning of equipment tag (two-dimensional barcode on stainless steel tags), ensuring technicians have actually been there. Highly visual color-codes indicate unfinished actions. Management staffs receive completion reports to track job done.
• Immediate increase in accuracy of records (temperature, vibration): instant warning for out-of-range data.
• Onsite inspection results without the need to return to office: technician gets immediate warning when measurements are outside of safe range or into danger range and get access to diagnosis information, with easy contact with the back-office team if needed.
• Enable analysis based on trends: performed by the back-office team (equipment managers), they allow for true predictive maintenance and long-term optimization of the maintenance strategy.
• Immediate increase in accuracy of records (temperature, vibration): instant warning for out-of-range data.
• Onsite inspection results without the need to return to office: technician gets immediate warning when measurements are outside of safe range or into danger range and get access to diagnosis information, with easy contact with the back-office team if needed.
• Enable analysis based on trends: performed by the back-office team (equipment managers), they allow for true predictive maintenance and long-term optimization of the maintenance strategy.
Long-term benefits from the project will derive from the implementation of predictive maintenance that bluebee® enables. Rapid improvements are expected in terms of downtime reduction and the indirect cost of maintenance.
bluebee® – not the same old mobile solution!
The traditional mobile solutions provided by CMMS/EAM vendors are usually smaller-screen versions of the main product, presented as an option to the main system but almost never implemented. Hardware resellers can also develop custom applications with no industrial value-added. Siveco’s bluebee® suite, on the other hand, consists in standard off-the-shelf applications designed by maintenance engineers for maintenance engineers. Based on very intuitive user-interface requiring little or no training, bluebee® allows for the direct creation of, and access to, know-how by technicians in the field.
The integrated system will provide a technical knowledge base for the plant, to support the inspection work and to provide a decision support system for the maintenance team. By enforcing systematic recording of failures and work done, a historical database of inspection will be built up, thus enabling technical-financial analysis.
This principle is shown in the figure below:
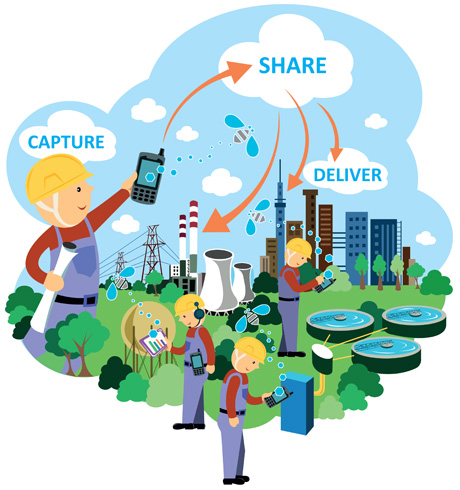
Key functionalities are:
• Intuitive user-interface requiring very little or even no training.
• Access to the central knowledge-base with three main points of entry: diagnosis (fault), equipment and inspection work orders.
• Report of measured values (meters and measurements) to the central database, with support to identify abnormal values and consult historical data.
• Report of failures, with selection of faults and access to diagnosis support information.
• Access to inspection WO lists and possibility to report on the work orders.
• Synchronization with the back office system.
• Possibility to barcode (2D barcodes) equipments and inspection points, for quicker and more accurate input and for verification purposes (“is this the right inspection point?”, “has the technician actually been there?”).
• Intuitive user-interface requiring very little or even no training.
• Access to the central knowledge-base with three main points of entry: diagnosis (fault), equipment and inspection work orders.
• Report of measured values (meters and measurements) to the central database, with support to identify abnormal values and consult historical data.
• Report of failures, with selection of faults and access to diagnosis support information.
• Access to inspection WO lists and possibility to report on the work orders.
• Synchronization with the back office system.
• Possibility to barcode (2D barcodes) equipments and inspection points, for quicker and more accurate input and for verification purposes (“is this the right inspection point?”, “has the technician actually been there?”).
The mobile solution can be integrated with any back office system (SAP PM, Maximo, Datastream, Coswin etc.) through a robust synchronization platform that takes care of data exchanges as well as optimizing telecommunications and the management of devices (software updates, security…). The platform is highly scalable, from a few devices to hundreds of mobile workers (for example for large facility management service suppliers). Siveco China’s mobile R&D team, located in Shanghai, can further customize the standard modules to cater to specific customers requirements.
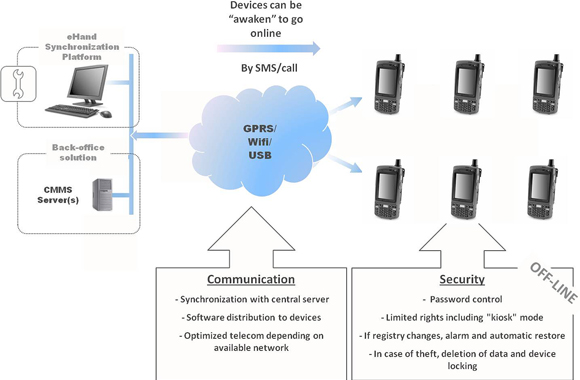
Click here to see how Motorola’s handheld devices support all bluebee®‘s features.