bluebee® cloud: Control & monitoring integration
Siveco and its partner PcVue (featured in this Partner article of our newsletter) have designed a two-way integration toolkit between Siveco’s bluebee® facility management and maintenance system and PcVue Solutions’ HMI and SCADA system. The joint solution demonstrates the openness of both systems and brings unique benefits to owners/operators of automated facilities.
For an overview of the bluebee® solution, see this article.

At the heart of the bluebee® solution, bluebee® cloud acts as a gateway to other software systems such as the BMS or SCADA. The integration is based on a Service-Oriented Architecture (SOA) toolbox including web services, OPC connectors and more traditional ODBC connectors – allowing great flexibility in communicating with various systems.
Unlike traditional interfaces, which feature a transfer of data to trigger work orders in the maintenance (often without practical application other than replacing the phone), the bluebee® cloud – PcVue integration toolkit ensure a tight integration between the two subsystems, bringing value-added to both automation and maintenance users.
HMI integration
With the bluebee® cloud – PcVue integration toolkit, both systems HMI can be integrated, meaning that operators can view bluebee® cloud data and access its functionalities from the SCADA HMI, while maintenance users can call up screens from the monitoring system (assuming permission is granted to them). This seemingly simple feature provides unheard-of support for work productivity improvement, fault diagnosis, safety management and decision-making.
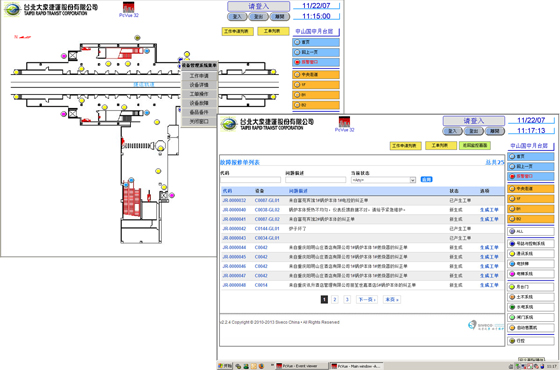
Data exchange
Alarms, measurements and meters are automatically transferred to bluebee® cloud after processing by the operator or directly for further processing in bluebee®. Unlike traditional maintenance systems that can only receive data, but are not able to treat them apart from automatically launching a work order, bluebee® cloud is able to forecast the next maintenance date, based on historical records and to already plan the work order. bluebee® cloud provides integrated reporting tools to graphically display and analyse data coming from both operation and maintenance, helping for example to optimize preventive maintenance plans for energy optimization.
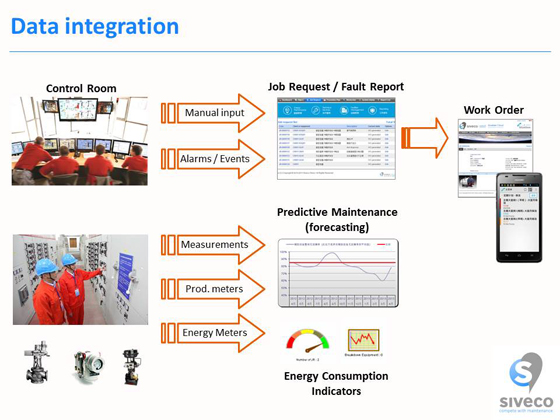
Standardization
While it is always possible to interface different systems, through specific software development work, we believe that using standard off-the-shelf components increases the reliability of the data transfer and considerably reduce Total Cost of Ownership (maintenance, upgrades, and modifications). It is especially critical that new tags can easily be added, equipment structures synchronized, etc.
Other features
Among issues that are often overlooked when interfacing systems, we could mention access control (combined login for both bluebee® and PcVue), the sharing of basic data (equipment, measurement points, etc.) and synchronization of databases (structures), e.g. what happens when a tag is modified in the bluebee® and PcVue? Finally the security of the automation system must be ensured, i.e. the management system should never disrupt operations: bluebee® cloud and PcVue standard integration tools ensure a fail-safe design.
From control room to field workers
The mobile component of bluebee® plays a major role in facilities management: field workers are equipped with phones or tablets running the bluebee® apps. Thanks to the bluebee®-PcVue integration, critical operation data from the BMS / SCADA, once limited to operators in the control room, finds its way to field workers in charge of daily maintenance. Conversely, for the first time, control room operators obtain direct access in their HMI to valuable facilities information from the field.
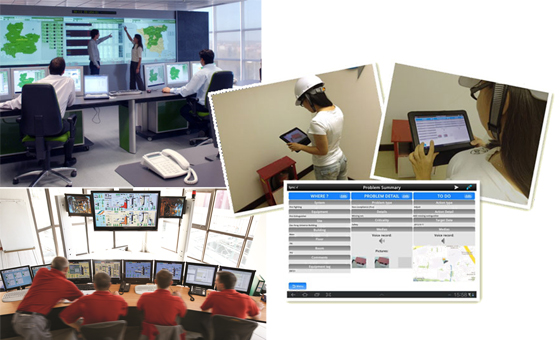