Maintenance preparation support for Indonesia’s Banjarsari power plant with CNEEC
Bukit Asam’s Banjarsari power plant
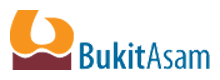
PT Bukit Asam (PTBA) is an Indonesian state-owned coal mining company, partly listed on the Indonesian stock exchange. The second largest coal producer in Indonesia, with mineable reserves of approximately 7.3 billion tons (17% of the total coal reserves in Indonesia), PTBA strives to become a competitive energy company. This vision has been manifested by the establishment of PT Bukit Pembangkit Innovatif (BPI), a sister company of PTBA, to operate the Banjarsari mine-mouth coal-fired steam power plant.
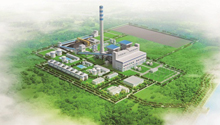
The 2x135MW power plant, a total investment of 240M USD, is located in South Sumatra province. China National Electric Equipment Corporation (CNEEC) was selected as the EPC contractor for this project. Construction started in April 2012 and the plant was handed over to client at the end of 2015, after which the warranty period started.
The challenge: meeting the owner’s expectations for plant documentation
Chinese engineering and construction companies traditionally emphasize cost control during construction, with progressive adjustments and modifications of the design as the project moves ahead. While the resulting speed and construction cost advantages have proven critical to support the development needs of many countries such as Indonesia, it often comes at the expense of maintenance preparation: Chinese EPCs face difficulties to provide complete as-built drawings or preventive maintenance instructions.
On the other hand, plant owners or operators in overseas markets have certain expectations in terms of the documentation to be handed over to the maintenance team, often as part of the Computerized Maintenance Management System (CMMS) delivery. For the Banjarsari power plant, PTBA required the plant technical database to be loaded in a Computerized Maintenance Management System (CMMS), to be delivered turn-key by the EPC.
CNEEC selected Siveco China for this project. Based on a long experience of greenfield infrastructure projects all over the world, Siveco has developed a specific expertise working alongside EPC companies and their equipment suppliers during the construction phase, ensuring smooth transfer of technical documentation to the plant owner, supporting plant commissioning and start-up with an accurate technical database and enforcing good maintenance practice from day one. Siveco was awarded the contract in March 2013.
The project: preparing maintenance during the construction stage
The main objective of the project was to build up the plant database in a CMMS for hand-over to operations before startup, in order for all the plant to be accurately documented in the system and for maintenance teams to use the system to support their daily work from day one.
The figure below summarizes the Siveco approach for maintenance preparation during a construction project based on the utilization of the CMMS:
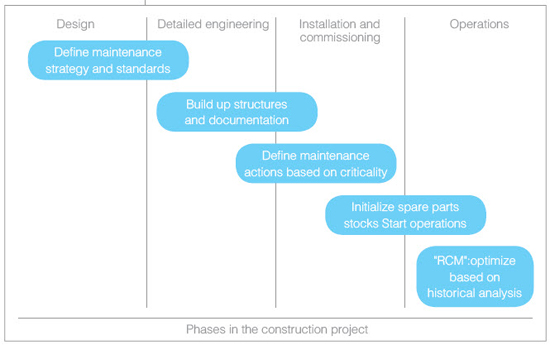
The Banjarsari project was split into three main phases:
1. Data preparation
2. CMMS configuration and factory-testing
3. Onsite delivery
2. CMMS configuration and factory-testing
3. Onsite delivery
The first two phases were mostly performed in China, working closely with CNEEC and subcontractors. Phase 3 was performed at the plant in Indonesia starting in the last quarter of 2015.
Siveco appointed a project manager for the entire project, a senior maintenance consultant with experience in similar power plant projects. Siveco China’s main resource center in Shanghai provides personnel for phases 1 and 2. All Siveco engineers are bilingual Chinese-English and have experience working in an international environment.
Phase 1 – Building a detailed, accurate and easily accessible technical documentation
The plant’s technical documentation consists of plant structures, equipment data, specifications, contracts, spare-parts, preventive maintenance instructions and inspection routines, technical documents etc. It can be entirely delivered in the CMMS and its associated Document Management System.
While this is ideally launched before contracts with the major equipment suppliers are signed, in order to ensure that the data collection requirements are incorporated into those suppliers contract with a clear delivery schedule, it is often not possible, as was the case for the Banjarsari project… Instead, Siveco held a kick-off meeting in April 2013 with CNEEC and key subcontractors to review the project schedule, explain the plant owner’s requirements and define the data collection process, activities and milestones, as well as applicable standards (IEC61346, IEC PAS 62400 and ISO/TS 16952-10 RDS-PP also known as the “new KKS”).
Siveco engineers created the overall plant structure and are supervising the entire data collection project, checking the quality of data provided on a monthly basis, ensuring consistency and compliance with standards, proposing alternative solutions when data is not readily available. The data collection phase will continue until the end of the construction, at which point the final data will be delivered in the CMMS database. It runs parallel with phase 2 (CMMS configuration).
Phase 2 – Preparing the CMMS before onsite delivery
In July 2013, a week-long “Implementation Study” workshop was conducted by Siveco experts with Banjarsari power plant’s top managers in Shanghai (at this stage of the project, it is normal that the maintenance team is not yet in place). The main purpose of the Implementation Study is to ensure that the CMMS supports the plant’s maintenance strategy and deliver the expected functionality and benefits.
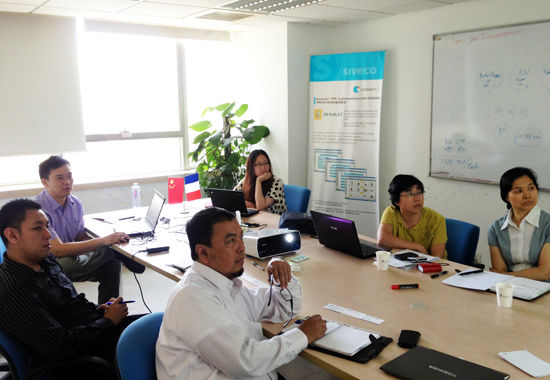
Implementation Study with Banjarsari Power Plant leaders and Siveco team
Drawing on Siveco’s long experience with similar projects all over the world, the Implementation Study resulted in a “Core Model” document (sometimes known as “CMMS blueprint”), defining the way the CMMS will be used in the plant. The Core Model describes the overall maintenance strategy, the CMMS data structures, all the plant’s maintenance management business processes (including spare parts management). The document also defines Key Performance Indicators (KPIs) and management reports, based on the EN 15341 Maintenance Key Performance Indicators standard.
The Banjarsari CMMS Core Model was finalized and approved in September 2013, after which the CMMS configuration activities started at Siveco office.
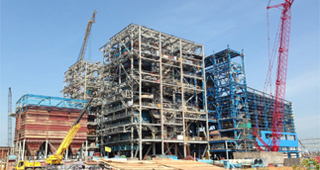
On August 27, 2013, the power plant’s number 1 boiler underwent successful water pressure test.
Based on the Core Model, the CMMS was configured at Siveco Shanghai office. Already prepared plant data were uploaded for Factory Acceptance Testing (FAT) in Q1 2014. Data collection continued until final delivery onsite.
Phase 3 – Onsite delivery
Onsite delivery started during Q4 2015. The Siveco project team conducted end-users training and babysitting activities in Indonesia for several weeks. At the end of 2015, BPI purchased a total of 10 Coswin 8i concurrent user licenses for the Banjarsari power plant. Coswin 8i has become the main operation and maintenance management system for the plant, covering the following main processes:
- Plant data management: keeping up-to-date of equipment structure and equipment-related information
- Preventive maintenance planning: standard work instructions and the entire planning process
- Work management: scheduling, execution and reporting all maintenance activities
- Stock management: maintain item register, stock receipt, stock issue, stock transfer, stock adjustment, stock count and repairable management process
- Purchasing management: purchase request, quotation, purchase order
- Management and analysis reports and KPIs
- Preventive maintenance planning: standard work instructions and the entire planning process
- Work management: scheduling, execution and reporting all maintenance activities
- Stock management: maintain item register, stock receipt, stock issue, stock transfer, stock adjustment, stock count and repairable management process
- Purchasing management: purchase request, quotation, purchase order
- Management and analysis reports and KPIs
Additional coaching services are provided during 2016, as part of the warranty period.