避免TPM项目中的陷阱
作为生产、维护改进战略之一,企业在实施TPM项目时会遇到诸多挑战。虽然所聘请的专家顾问都来自于TPM的发源地,如日本或其他西方国家,但国内的实施情况却与国外不同。
TPM项目的基本原则是主张“自主维护”,即由操作人员进行维护工作,或是由生产人员直接参与到维护改进项目中。成功实施TPM项目的益处之一就是能让操作人员从执行简单的工作开始,如日常清洁工作、定期润滑、加固螺栓以及其他检查等,慢慢地承担起更多的岗位职责。在做好日常维护工作的基础上,可以继续增加更为复杂的工作,如操作人员在检查到自己的设备有故障时,利用标签进行标注——这是一种非常行之有效的方法,能够让全厂的员工都了解到工厂现在的维护状况。而TPM项目所能获得的收益,就是在实施TPM的后期,企业生产团队也能融入到分析和改进决策中。
基于喜科丰富的项目经验,本文将着眼于中国TPM项目的独特性,从而帮助企业管理层避免实施TPM时的未知陷阱。
人力资源的局限性
“自主维护”的关键词应该是:参与、职责和主观能动性,而多数企业的人力资源部门可能并不这么认为。不单单在中国,改变陈旧工作习惯是人们一直面临的首要问题。然而,生产人员自身能力的局限性限制了他们的工作表现,例如,与他人分享对于设备的操作经验和技能。往往在中国,操作人员固然具有一定的工科理论基础,但由于较高的人员流动率和缺乏多学科学术背景,导致他们对于设备的认知和了解其实并不高。
虽没有办法马上解决这个难题,但可以:制定降低人员流动率并改进操作技能水平的工作计划。无论所制定的维护改进计划是否是基于TPM理论,都将有效地解决人力资源局限性这个问题(参照“换个角度看维护”一文)。而在开展TPM项目时,也应考虑到这点。
在开展TPM项目前降低故障率
在开展“自主维护”项目前,应该尽可能地降低设备故障率。试问生产操作人员怎能具备正确维修经常发生故障设备的能力呢?我们时常可以见到,维护技术人员像“消防员”一样,成天都在生产一线进行紧急维修工作。请时刻谨记,在这样的情况下是无法进行“自主维修”项目的。
反之,我们应该在开展纠正性维修工作的同时,积极开展预防性维护工作,关注如何降低设备的故障率(范围还包括设备改进),并让生产部门参与到改进项目中。由此而见,TPM项目实则更适合新建工厂的生产改进。
首先实施工作反馈管理系统
当将维护工作转移给生产部门时,时常会发生数据丢失的情况:因为在交接前,维护部门是整个工厂少数储存这些维护知识数据的地方,而现在,这些数据需要完整地与其他部门进行分享。此时,拥有一套集中化存储基于工作反馈数据的管理系统就显得非常重要,从而避免因数据缺失导致的维护部门与生产部门沟通不畅的情况。从一方面看,一套综合性的维护数据管理系统是进行设备故障分析的重要工具(详见下文)。而另一方面,工作反馈则有助于让维护人员了解操作人员的快速解决方案,从而进行有针对性的维修工作。
我们推荐通过“工单管理”(或称为“工作请求”)功能来获得重要的数据信息。通过预先定义的检查列表可大大简化数据收集流程:症状、故障类型、故障时间(一般不需要精确时间,用户可以自行选择,如5分钟、30分钟、2小时、4小时、8小时以上等)。通过喜科移动解决方案bluebee®,现场操作人员使用智能手机不但能轻松获取有效数据,更能添加故障图片并从中央数据库中直接、快速检索故障排除信息。
包括TPM在内的任何维护改进项目良好的收益即是基于系统化的历史数据分析。经验证明,实施CMMS系统能有效地进行这项工作:纸面工作和基于Excel的系统则无法进行复杂的运算和分析。而基于历史数据的工作改进决策可获得真实且可衡量的收益。
获取维护改进
通常,只有当维护团队摆脱繁重的维修工作(将一线维修工作转移给了操作人员)时,他们才有时间全身心地投入到工作改进项目中。也就是说,技术人员如果不承担起他们应尽的岗位职责,TPM项目根本无法进行。
今时不同往日,维护人员不能游手好闲地等待故障发生才开始工作。现在,有必要让他们了解到他们的参与和工作表现对可靠性改进有着重要的影响。
首先,维护团队对于这样的变化要做好准备。因为他们需要运用到一些新的方法和工具来辅助其新职能:如,根本原因分析、预防性维护工作的规划和实施,以及制作基本报表和KPI指标等(详见“COSWIN使用技巧:Coswin中的OEE指标”)。
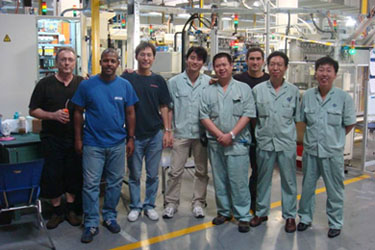
喜科联合团队为上海采埃孚提供维护支持服务
结论:实施TPM的先决条件
总之,实施TPM必须符合:
- 低故障率
- 拥有工单管理系统
- 维护团队准备接受新职能角色,并致力于实施改进工作
虽然TPM在某些工业发达国家被证明是非常行之有效的生产改进方法(工程师拥有专业的维护方法论背景),但在中国则遇到了诸多挑战。经验告诉我们,TPM项目成功的主要元素包括:组织架构、方法和工具。在中国,实施CMMS系统是创建可持续发展组织架构的有效的方法。而我们建议在开展TPM项目前,就有必要率先实施CMMS系统。更多内容,欢迎参阅“换个角度看维护”一文。