喜科助力天津南港油库实现持续维护改进
项目背景
荷兰皇家壳牌集团是全球领先的国际能源公司之一,业务遍布全球70多个国家和地区。2018年营业收入达3,884亿美元,世界500强排名第五位。壳牌华北石油集团由壳牌集团及天津食品集团共同出资成立,在南港工业区运营着一座一期6万立方米罐容的成品油油库,年周转油品68万吨,二期建成后年周转油品可达300万吨,项目总投资约5.5亿元。
天津壳牌石油储运有限公司(以下简称“南港油库”)为壳牌华北石油集团的全资子公司。南港油库作为接收、储存和发送汽柴油的区域,存储的油品具有易燃易爆的特点,一旦发生火灾或爆炸等事故,将造成严重的人员伤亡、设备损毁、环境污染及企业财产损失,影响范围极大。早在项目建设阶段,壳牌(中国)及南港油库管理团队意识到亟需落实一套系统帮助其增强油库的维护维修能力,并在正式投产后落实油库的资产管理工作。得益于壳牌在中国丰富的项目经验,其专家团队迅速意识到需要一套相较于传统大型企业管理系统更为灵活的解决方案,将供应商的维护实践经验与项目充分融会贯通,且通过强有力的本地技术支持助力持续的维护改进。
喜科作为拥有大型化工制造业项目实施经验的供应商,有能力在工厂建设期和试运营期介入和实施CMMS系统。南港油库基于这一首要的安全运营需求开始了选型工作并与喜科取得了联系,双方就项目范围进行了充分的前期讨论。2014年12月,喜科团队赴南岗油库项目现场进行调研评估。在调研初期,喜科团队就如何收集设备基础数据及确保数据的完整性、准确性和结构完备性向南港油库提供实用建议。数据准备作为搭建CMMS系统的第一步,将为日后的维护巡检工作打下坚实的基础。在南港团队多次实地拜访喜科位于天津的客户现场后,喜科顺利通过正式招标流程,成为本次南港油库项目的系统供应商。
项目实施
在壳牌南港油库正式选择喜科进行项目合作后,南港项目步入了试运行阶段。喜科立即组织核心项目团队开展实施工作,并致力于通过依托成熟的Coswin 8i管理工具,融汇国际先进的管理理念,为南港油库建立起一个全面的CMMS平台。通过本次合作,喜科帮助南港油库建立起一套完备的运维管理平台,并对以下工作提供技术与管理支持:
●
工厂基础技术数据与技术文档管理体系的构建
●
维护标准和安全运营体系的构建
●
可供技术分析及诊断使用的维护历史知识库
●
整厂预防性维护工作的建立和执行
项目伊始,双方团队便对数据收集工作在系统建设中的重要性表示了极大关注。由传统IT供应商引导的数据收集方式仅仅是向用户提供标准的数据收集模板(如:excel表格)并由用户自行收集数据。由于用户从未参与过数据收集,且不了解数据将如何应用于CMMS系统中,最终导致维护团队更为繁重的工作任务,且收集的数据无用。与之不同的是,喜科通过维护管理咨询与指导服务,为南港油库制定了详尽的数据收集计划,并与工程师共同对数据收集过程进行优化。
如何科学地划分设备关键度是南港油库团队面临的一大挑战。喜科建议通过以下三个方面确定设备的关键度:第一是设备对于安全和环境的影响程度;第二是设备对于生产的冲击;第三是设备发生问题的可能性。除关键度的划分外,基于区域、流程、设备、组件之间的多种结构关系也同时建立。南港团队根据喜科的建议将设施划分了16个系统区域,例如:汽油罐区、汽油泵区、添加剂区和应急发电机房等。
为了使维修人员快速找到故障设备,喜科建议南港油库在CMMS系统中使用图形化导航以直观地定位设备,继而查看设备历史问题、检查过往的预防性工作记录,并分析设备症状及故障原因等。所有关键设备的预防性工作指导建议都由计划员和维护主管制作并导入系统,系统将在条件满足的情况下自动释放工单。在系统首页的仪表盘中可清晰体现所有人员的工作情况,如:未分派的工单、过期未完成的预防性计划等。
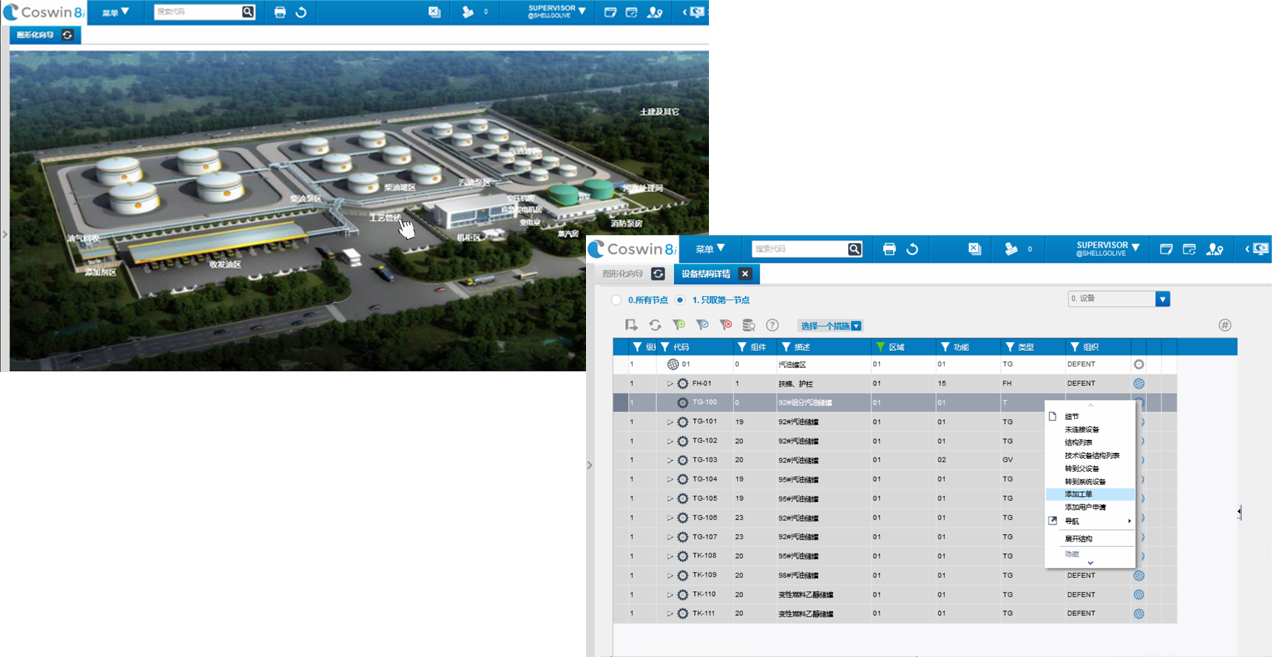
南港油库系统仪表盘展现了在喜科所有系统中通用的图形化导航功能。除精美的展示外,图形化导航允许用户直接钻取选择相应设施、打开相关报表并执行工作。
此外,南港团队将全部设备备件录入系统并设定了安全库存。一旦备件实际库存数量低于安全值,系统的安全库存指示器将会提醒仓库管理员采购。维护主管也可通过报表工具将未来一个月的预计备件消耗和现有库存量做比较,以决定是否提前采购备件。
项目收益
喜科为南港油库实施的智慧运维项目已步入了第五个年头。南港油库维护团队充分利用了项目投产前建立起的维护管理系统,坚持每月末通过喜科定义的标准报表分析当月的工作情况,进行维修维护总结。包括:工单完成率、前五故障原因、前五大维修措施在内的多个数据指标已成为检验维护团队工作的主要参照,实实在在地帮助南港团队持续改进维护工作。
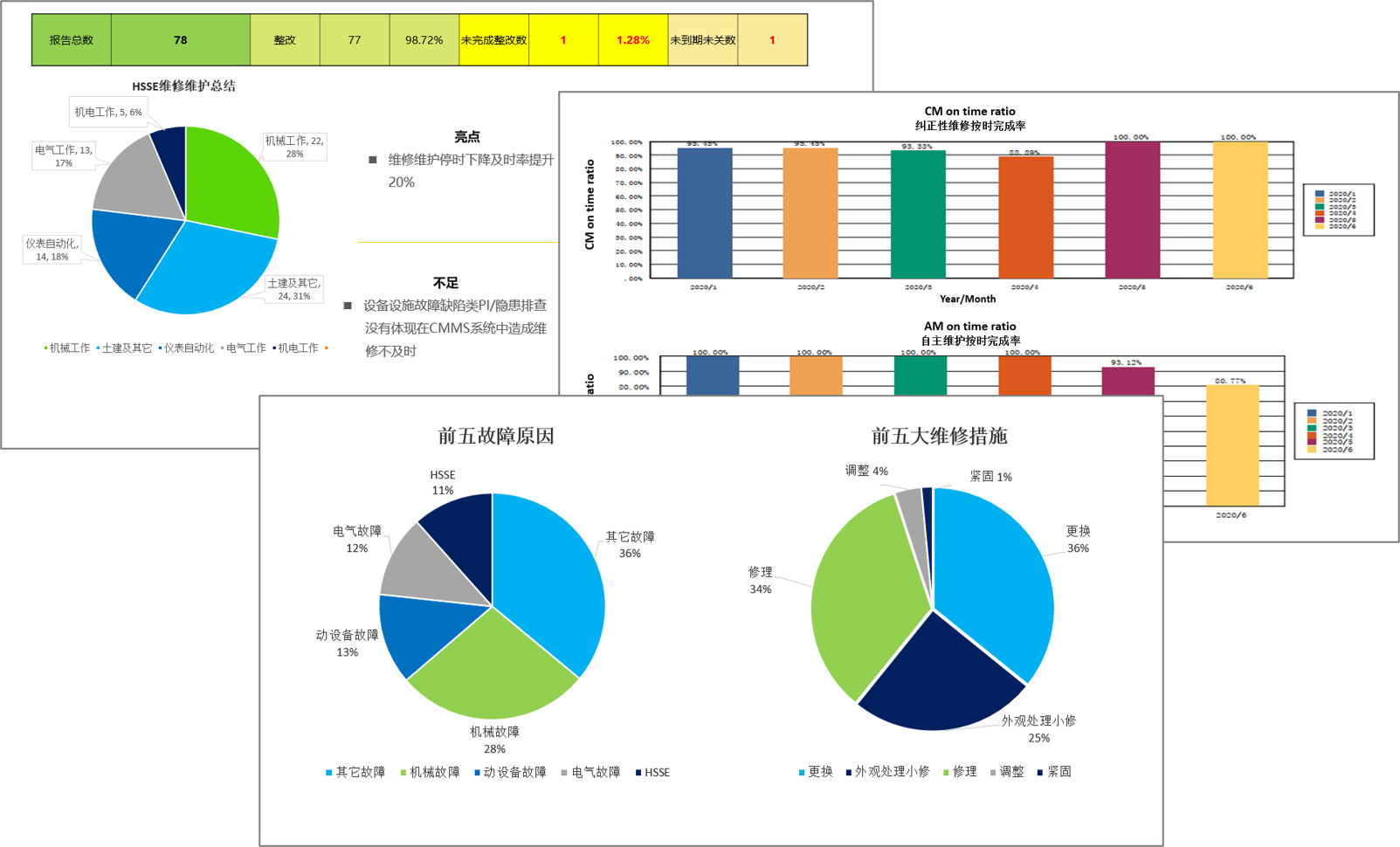
此外根据年度累计停机时间跟踪显示,南港油库停机时间呈明显下降趋势,证明维护团队在严格按照定义的维护策略执行工作的情况下,可有效降低停机时间,保障企业正常运营。
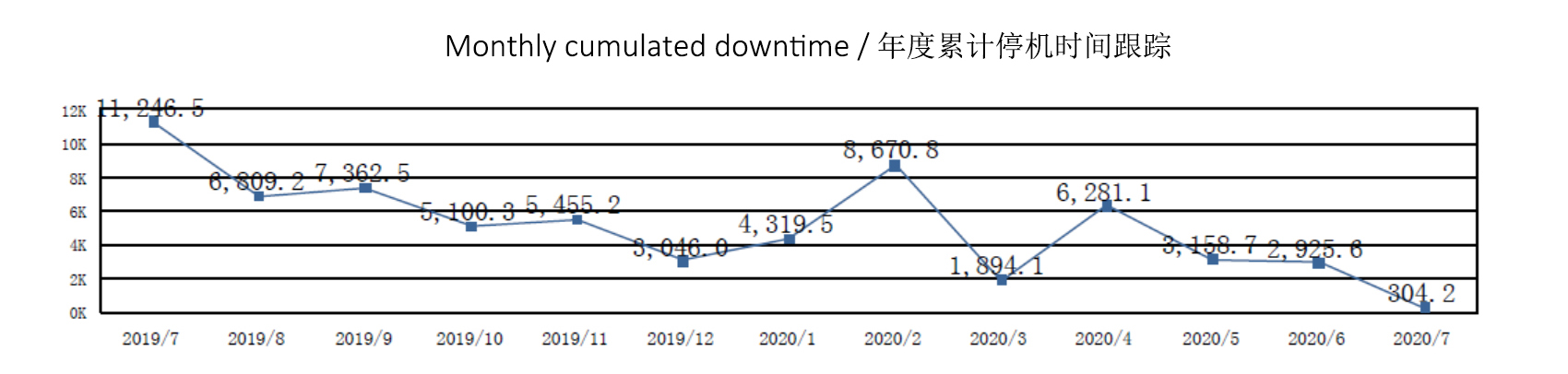
(备注:2月因疫情影响无法及时关闭工单导致停机时间记录上升)
南港油库生产工艺经理说:“与喜科多年的合作帮助我们建立了一套完善的设备管理体系,我们将Coswin充分应用到每天的日常维护工作中。随着时间积累,我们已建立起完善的技术数据库,设备情况一清二楚。在双方的共同努力下,南港油库维护管理获得了持续改进。”